Continuous Improvement in Manufacturing: Process Excellence Frameworks
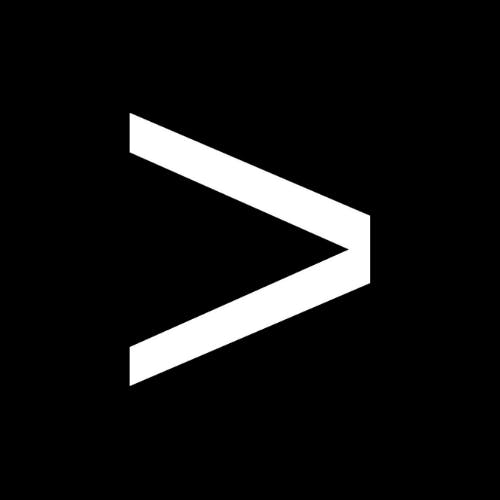
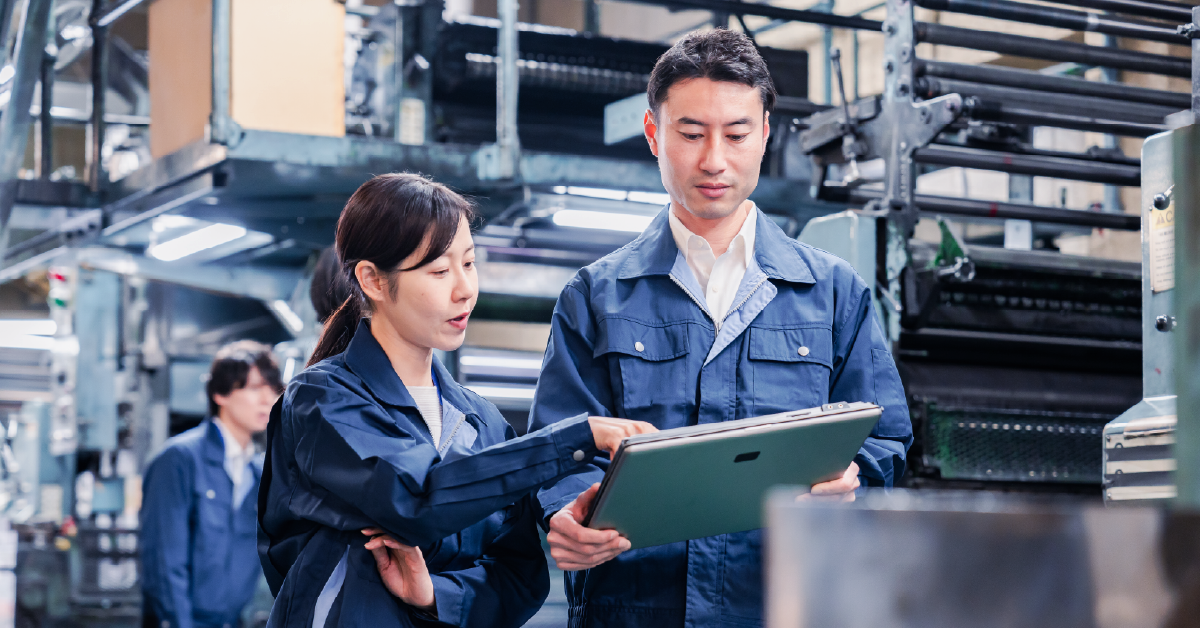
“Plan your work, work your plan.” It’s a core mantra in continuous improvement that requires forethought and planning, as well as a commitment to executing your process.
In this article, we explore some of the top frameworks for continuous improvement in manufacturing, including:
- Lean Manufacturing
- Six Sigma
- Total Quality Management (TQM)
- Theory of Constraints
Download your free Root Cause Analysis 101 Guidebook for an overview of common root cause analysis tools plus tips and tricks for making them more effective
Read how digital transformation helps to continuously improve manufacturing
Lean Manufacturing
Lean manufacturing or simply “Lean” describes a collection of tools originating from the Toyota Production System (TPS) in post-WWII Japan. The core aim of Lean is to eliminate waste, focusing on three categories of waste or the 3Ms:
- Muda: Activities that don’t create value for the end product or customer
- Muri: Unevenness in production levels
- Mura: Overburden of workers and processes
Lean Tools
Lean encompasses a wide variety of tools to reduce waste while improving efficiency, including:
- Just-in-Time production: One of the core pillars of the TPS, this principle is about making products as needed to minimize inventory and related costs
- Jidoka: The second core pillar of TPS involves giving machines and workers the ability to detect when abnormalities occur and stopping work immediately.
- Kaizen: Kaizen is a quality philosophy that promotes continuous improvement using small, incremental changes made by all employees that add up over time
- 5S: Part of the Kaizen philosophy, 5S is a workplace organization tool comprised of 5 steps: sort (seiri), set in order (seiton), shine (seiso), standardize (seiketsu) and sustain (shitsuke)
- Value stream mapping: This is a tool for visualizing processes to identify value-added and non-value-added activities to help with streamlining processes.
- Poka-yoke: Error-proofing devices or techniques help prevent defects or make them immediately detectable.
- Visual management: Visual management tools use charts, displays or other visual cues such as Andon lights to communicate key information about processes.
When fully adopted by an organization, Lean becomes more than a set of tools or a manufacturing discipline. Rather, it becomes a unifying philosophy driving how the company operates and addresses problems, helping establish a culture of quality.
Six Sigma
Six Sigma is a data-driven methodology focused on minimizing defects and variation. This approach to continuous improvement in manufacturing centers on applying data and statistical analysis to process control. The Six Sigma methodology was developed by Motorola engineer Bill Smith in 1986, and has since been adopted by leading companies such as GE, Ford and Honeywell.
Six Sigma refers to the number of standard deviations or sigma around the mean under a normal distribution (bell curve). Achieving Six Sigma quality equates to a defect rate of 3.4 parts per million, or nearly defect-free processes.
DMAIC Cycle
Six Sigma is built around the DMAIC cycle, which stands for define, measure, analyze, improve and control:
- Define: In this phase, the problem itself is clearly delineated, as are project goals, stakeholders, customer requirements and the process needing improvement.
- Measure: The measure phase involves collecting data on current process performance, helping establish a baseline for assessing improvement.
- Analyze: In this phase, teams analyze the data for process variation and perform root cause analysis. Here statistical analysis is central to pinpointing factors impacting quality.
- Improve: The improve phase is where solutions are developed and tested, with the goal of directly addressing the root causes identified in the previous step.
- Control: Here the focus is sustaining improvements over time. This requires process monitoring and implementing controls to maintain Six Sigma quality levels.
The DMAIC process largely mirrors and is an extension of the Plan-Do-Check-Act framework, which we discuss below.
Total Quality Management (TQM)
Total quality management (TQM) is a comprehensive framework for continuous improvement in manufacturing originally developed by W. Edwards Deming, one of the founding fathers of quality management. TQM focuses on statistical process control, data-driven decision-making and organization-wide participation in quality.
TQM is centered on the Plan-Do-Check-Act (PDCA) process approach, also called the Deming Cycle:
- Plan: Setting objectives, defining and documenting processes and standards
- Do: Implementing processes, conducting employee training, executing projects
- Check: Collecting data to measure performance against objectives to identify trends and evaluate effectiveness, such as with layered process audits
- Act: Taking action based on data collected in the check phase, including adjusting processes and implementing corrective action
TQM Tools
TQM utilizes a range of tools and techniques that overlap with other continuous improvement frameworks. These include:
- Process mapping to visualize processes and opportunities for improvement
- Statistical process control (SPC) to monitor processes and reduce variation
- Fishbone (Ishikawa) diagrams to brainstorm potential causes of problems
- 5 Whys analysis for digging into successive layers of a problem during root cause analysis
- Employee participation to involve people at all levels in the organization in quality efforts and building a culture of quality
Theory of Constraints
The Theory of Constraints is a management philosophy aimed at improving efficiency by eliminating constraints that stand in the way of continuous improvement in manufacturing. Emerging as a response to the limitations of traditional management techniques, the Theory of Constraints takes a more holistic approach to improving system-wide effectiveness, focusing on the most critical bottlenecks.
The Theory of Constraints was first presented by physicist and management expert Eliyahu M. Goldratt in 1984, and has since been widely adopted by many manufacturing organizations.
Theory of Constraints Tools
The Theory of Constraints incorporates multiple strategies and tools aimed at identifying and managing constraints, such as:
- Concentrating efforts: The Theory of Constraints emphasizes concentrating the organization’s efforts and resources on addressing the most critical constraints hampering performance.
- Prerequisite tree: This tool helps organizations identify constraints by mapping process prerequisites.
- Five focusing steps: The problem-solving process includes five steps aimed at continuous improvement. These are: identifying the constraint, exploiting it, subordinating all else to the constraint, elevating the constraint and going back to step one to identify new constraints.
- Buffer management: The concept here is to create buffers or controlled inventories so that variations can be absorbed without risk to quality, also reducing the risk of bottlenecks.
- Drum-buffer-rope (DBR): The DBR system ensures production rates are set according to the capacity of the constraint, smoothing out the process while preventing overproduction or underproduction. The drum is the pace-setter or constraint, the buffer is the controlled inventory that protects against disruption and the rope is what allows communication between the constraint and upstream processes.
Continuous improvement in manufacturing is a journey, not a destination. Each of the frameworks discussed here provides a roadmap for the journey, helping improve processes, remove bottlenecks and improve quality. Plan your work, work your plan and be ready to adapt along the way.