How to Use FMEA for Root Cause Analysis
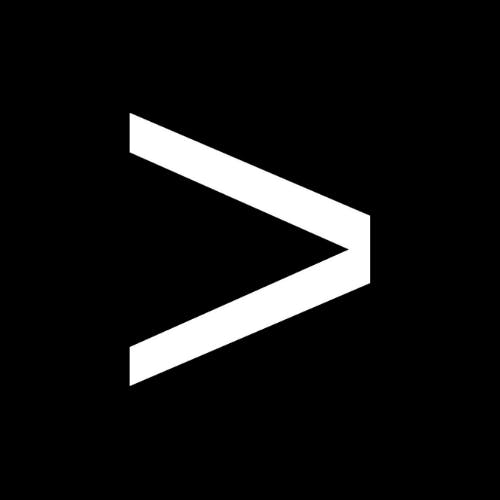
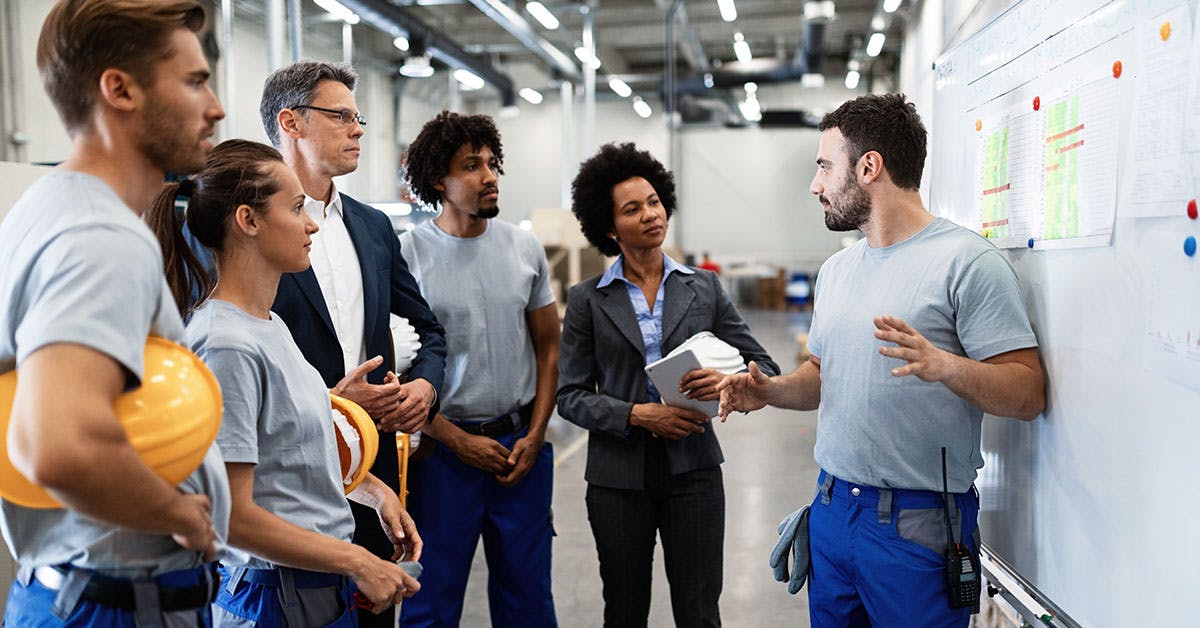
Most people use the fundamentals of a failure mode and effects analysis (FMEA) on a daily basis without even realizing it.
On a basic level, this root cause analysis tool is about thinking through everything that could go wrong, the impact on customers and what steps can prevent failures.
Let’s look at the basics of creating an FMEA, including how to set one up and a real-life example of how to use it.
What is FMEA?
FMEA is a structured, empirical approach to understanding the potential impact of something going wrong in a process. Each individual opportunity to go wrong is called a failure mode.
Each failure mode is assessed for three factors: severity (S), occurrence (O), and detection (D). These scores combine to produce a Risk Priority Number (RPN), and that score is the ranking system that you use to determine which problems to focus on first.
Find out how to reduce defects and quality costs with our Ultimate Guide to Layered Process Audits
How to Set Up an FMEA: Current State
An FMEA has two sections. The first focuses on creating a scorecard for the current state, including potential causes and existing controls, and the second part focuses on corrections.
In the first part, each failure mode goes on its own line. Severity (S), occurrence (O), and detection (D) are scored on a scale from 1 to 10 based on the team’s judgement. For each score, 1 would be the best–case scenario and 10 is the worst.
- Severity represents how bad the impact of a failure would be, ranging from no impact to catastrophic
- Occurrence represents how often the failure occurs, ranging from extremely unlikely to inevitable
- Detection represents how likely you are to catch the failure
How to Set Up an FMEA: Corrections
The second half of the FMEA is used to assign necessary corrective actions to the appropriate people to prevent problems identified in the first section.
Know that not all problems have obvious solutions. Sometimes the action is simply to determine next steps.
An FMEA Example
FMEAs are used before things go wrong to prevent quality failures. In this example, we apply the FMEA process to a drive into work.
The first step is breaking down the process into smaller bites (although some teams may prefer to do this as they go). What are some sub-processes of driving into work?
- Backing out of the driveway
- Driving through town
- Merging onto a highway
- Passing through a toll bridge
- Navigating traffic jams
- Parking at the office
Each one of these sub-processes has their own failure modes. What can go wrong when backing out of the driveway? What can go wrong when merging onto the freeway? These are the questions that you ask yourself every day, consciously or not.
Failure Modes
An FMEA allows you to dig into each item in great detail. What can go wrong when backing out of a driveway?
- Hitting another car
- Running over a toy
- Hitting a person
- Being hit by another car
Populating the FMEA
From here, choose one failure mode and drill down. If you hit another car, what is the effect? How severe will it be? What might have caused it? How often might you hit another car? What could you do to prevent it? How likely are you to notice?
Those questions lead through the full FMEA and end with calculating the RPN. Once you have scored everything, multiply the three numbers together to get the RPN. This overall score lets you rank potential problems.
Assessing FMEA Results
Now that the first half is done, it’s time to evaluate and correct. With such a high RPN, it’s important to contain this problem. The goal is to implement controls that will bring down any of these scores.
What action can you take to reduce the severity of hitting another car? Sometimes, you can’t do anything about severity. What can you do about occurrence? Can you reduce the likelihood that you will hit another car?
Perhaps training could help. Increased awareness and diligence could go a long way. Every control you add will help bring down the RPN. What could you do to increase detection? How could you help yourself know when there is another car behind you?
Corrections
At this point, an action can be assigned to a responsible person. From here, the responsible person should pick up the project, make their changes, and update that information on the FMEA itself.
To create a closed-loop corrective action process, you’ll need to check back to verify the correction was implemented and held in place. This means updating plant floor audit checklists, either on paper or in your audit software.
FMEAs can seem complicated at first, but as you use them, they become second nature. The objective is to reduce overall RPN scores as far as possible by implementing controls that reduce the severity and occurrence, or that increase the detection of a potential failure. Referring to our driveway example, something as simple as parking in the driveway backwards could help prevent hitting another car.
Not only does this process help you develop solutions, it also provides empirical data to support your decisions.