3 Key Investments to Increase Quality and Reduce Production Costs
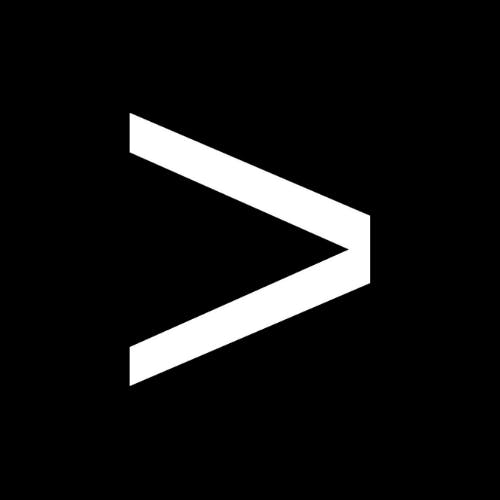
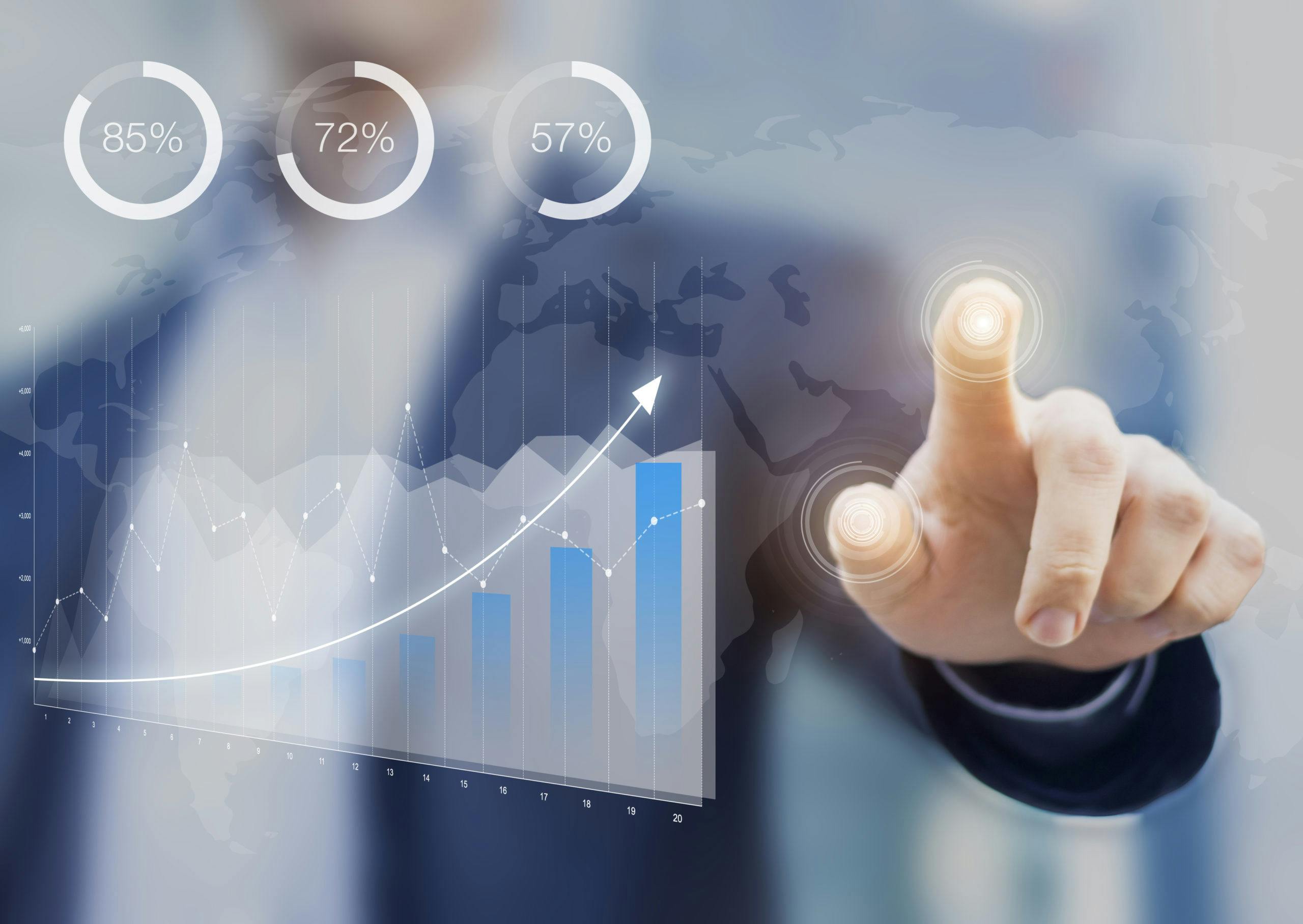
In today’s competitive environment, manufacturers are more focused than ever on delivering high-quality products while reducing costs. Unfortunately, too often efforts are driven by a skewed perception of how best to achieve this goal. This is because many manufacturers pay greater attention to the cost of poor quality (CoPQ), comprising internal and external failure costs, over the cost of good quality (CoGQ), comprising proactive prevention and appraisal costs. As a result, they make reactive investments that yield less return and later prove to be insufficient.
The Evolution of Cost of Quality Investments
The traditional cost-related goal in manufacturing has been to reduce CoPQ, namely failure costs related to rework, scrap, returned materials, schedule disruptions, equipment downtime, and poor quality resolution.
On the surface, this viewpoint seems logical. Failure stands out—in production and on the market. As supply chains extend, CoPQ becomes a major concern because failure costs hurt not only revenues, but also morale, productivity, efficiency, and brand image.
To reduce visible failure, most manufacturers began by hiring more QA staff. These workers then needed modern tools, which later required software investments. This software was initially general business management solutions, such as Enterprise Resource Planning (ERP) systems used to collect, manage, and store data. However, they were designed to cover a broad range of applications and thus are too general in their use in a manufacturing setting.
The introduction of manufacturing-centric Quality Management Systems (QMS) was an improvement on ERP systems, providing the procedures, processes, structure, and resources necessary to streamline operations and manage cost of quality. Yet, they too present drawbacks.
For example, most QMS are designed by quality engineers for one industry—rather than for common issues across industries. Also, they struggle with information silos (like any enterprise system), and they do not track historical data, limiting the system’s usefulness in detecting and correcting quality issues. Finally, most data in QMS is focused on failure detection and compliance appraisal—not failure prevention, where small investments can yield much greater results.
The ultimate goal should be to prevent failures by positioning workers to do the right things, at the right times, for the right reasons. The following three investments aim to achieve this goal.
Investment 1: Layered Process Audits
In a classic audit, supervisors account for their staff’s output and use of resources, then test the data to identify potential issues. This approach falls short, as it fails to account for the potential of human relationships, whether tense or cordial, to create grey-area issues.
For example, let’s say Steve is a quality checker and Jack is a production line worker. Steve and Jack eat lunch together every day and have become close pals. Steve learns on an audit that Jack’s waste of materials is increasing. Since they’re friends, Steve lets Jack slide even though the waste has approached unacceptable levels.
Meanwhile, Jim, another production line worker, is also wasting materials, though to a lesser degree than Jack. Jim has always had an attitude with Steve, so Steve is overly critical of Jim’s performance. Regardless of whether Steve’s bias is unconscious or conscious, both situations, independently and in combination, diminish quality standards over time.
To address the human element of evaluation and cut degradation of quality standards, layered process audits (LPA) need rotating audit supervisors and resource assignments. And since all auditors aren’t necessarily qualified to audit all things, managers can set audit and auditor levels.
Layered process audits are also unique in that they involve all levels of management, formalizing the notion of continuous improvement throughout the company. They also emphasize operational excellence, since they require manufacturers to review metrics of the audit and create an action plan for improvement.
By investing in layered process audits, most manufacturers find that they reduce CoPQ, including:
- Build variations due to work standardization
- Defects due to increased compliance and errors caught before product shipping
- Operator injuries due to better safety monitoring
Investment 2: Data Collection and Management
To ensure easy retrieval and control of data related to LPAs and other manufacturing information, manufacturers should also consider investment in software that scans quality data during in-process checks. This allows you to store historical information and use it to identify difficult-to-spot issues.
For example, Ease worked with Cummins Inc., which had discovered that some of its engines were failing prematurely. Cummins produces large, specialized engines for vehicles such as trucks, tractors, and ships, so addressing this issue was as complicated as identifying it. In addition to a tremendous brand risk, the failed engines presented what could have been a logistics nightmare for recalling, transporting, and servicing.
Cummins had invested in advanced data collection systems that scan quality data during in-process checks, so by analyzing systemized historical information, Cummins was able to identify that the problem engines had indeed passed quality checks. However, within each engine, several parts were only borderline in-specification; cumulatively, the engine had drifted into risk of failure.
Cummins was able to rectify an otherwise perplexing issue—and reduce CoPQ in the process—thanks to proactive data management. By investing in a system that scans, tracks, and displays information by asset, process, or department, most manufacturers enjoy similar results as Cummins, including:
- Less variation and rework due to up-to-date information being available through a single point of entry, display, and control throughout the company
- Easier identification of issues through revision control and tracking of the change history of documents
Investment 3: Electronic Work Instructions
Just as the need for quality assessments has grown, so has the need for immediate access to real-time work instructions. Extending supply chains and rapid upgrade cycles have presented major challenges with version control, as there are now more items to check and near-constant revisions to work instructions.
For instance, in the auto industry 10 years ago, the same product manufactured 90 days apart would have differed in only a handful of parts. Today, the same experiment would result in well over 100 different parts.
By having up-to-date, revisable work instructions displayed and managed electronically, workers can focus more on production and less on looking for documents or waiting for corrections or repair instructions. Also, the effectiveness of the instructions can be increased by incorporating video, graphics, digital photographs, and scanned images.
By investing in electronic work instructions, most manufacturers find that they reduce CoPQ, including:
- Scrap due to automated work instruction processes freeing up engineers to focus more on improving processes and quality
- Rework and defects due to operators being able to confirm, acknowledge, measure, and record data during in-process checks and audits
- Planning time due to engineers being able to generate work instructions faster and more accurately respond to changes
The Power of Combined CoGQ Investments
While each of these CoGQ investments can serve as a self-standing solution, the best return will be experienced when combining all three for end-to-end results. This is because systemized layered process audits, data collection and management, and electronic work instructions cumulatively close the quality loop and curtail the quality vs. production conflict.