3 Strategies for Writing Better Layered Process Audit Questions
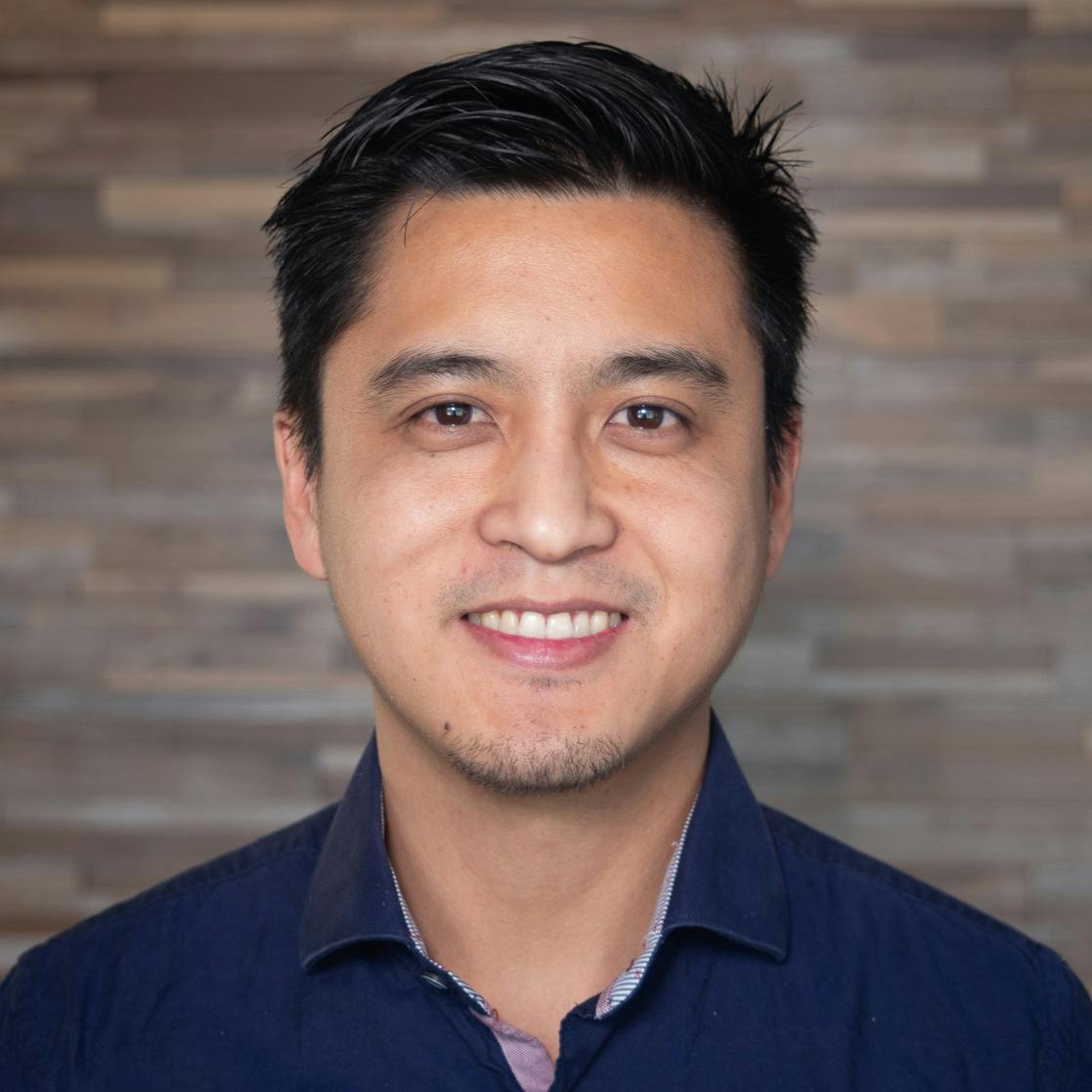
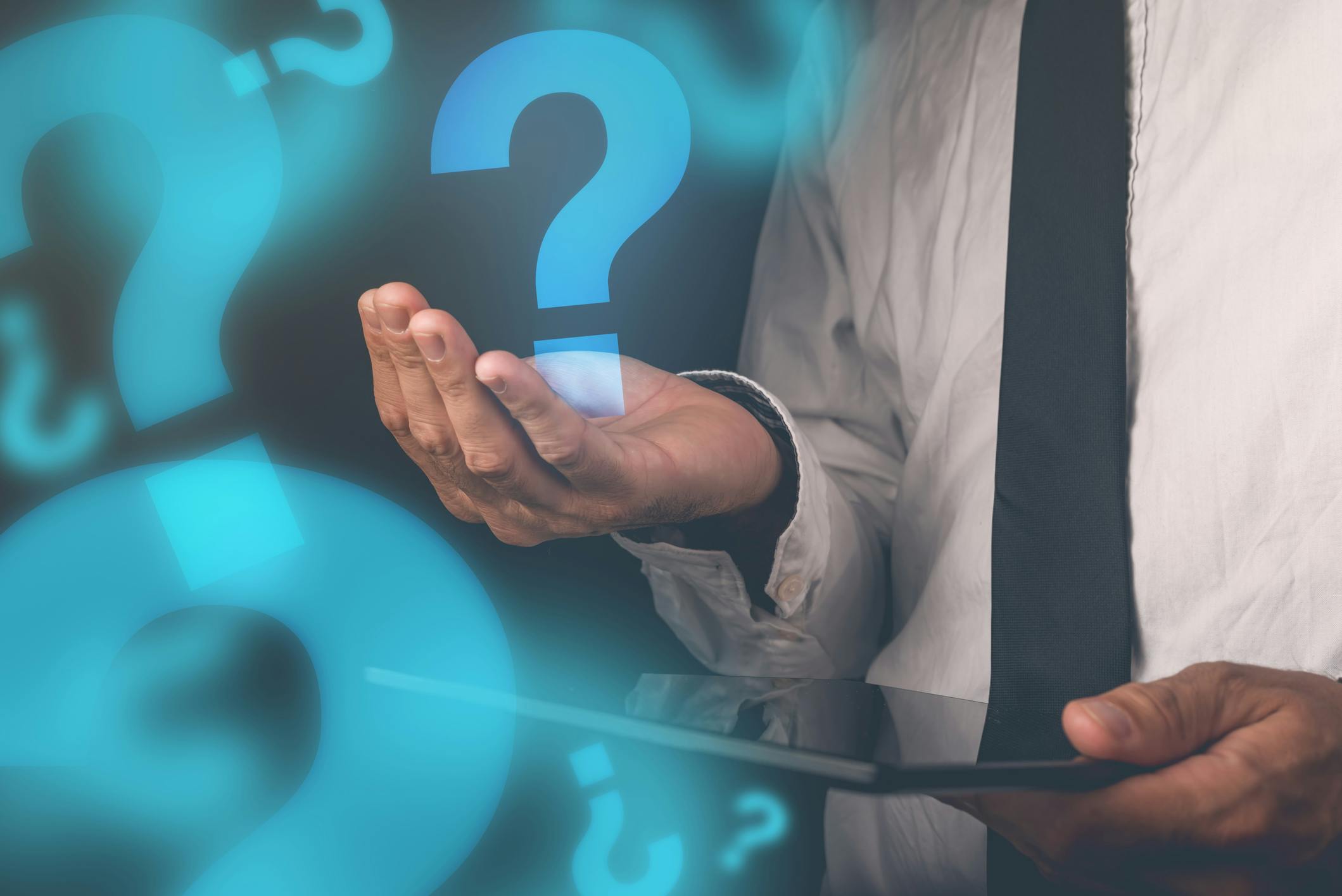
Providing daily checks of high-risk processes, layered process audits (LPAs) act as a finely woven net for catching defects upstream before they impact the customer.
While you may conduct thousands of audits throughout the year, what you actually catch with that net is directly proportional to the quality of your questions. Poorly designed questions leave room for error and make it hard to detect the right problems. But knowing where to find good questions, keeping them simple and updating them regularly can help you build a more robust and effective LPA program.
1. Find Good Sources of LPA Questions
A key strategy in improving the quality of LPA questions is addressing the right questions to begin with. LPA questions should focus on areas that pose the biggest risks to product quality, safety and organizational performance.
If you want to know whether previous problems have truly been corrected, you need to pay close attention to those problem areas moving forward. Some examples of places to find ideas for LPA questions include:
- High-risk operational and process areas such as fabrication, setups and changeovers
- Process failure modes and effects analysis (PFMEA) results
- Previous problems such as customer complaints, defects or safety incidents
- Reports on scrap and similar issues
- Equipment reliability indicators such as proper temperature settings, pressure settings or specific gauge calibration values
- Quality system audit findings and non-compliances (e.g., ISO 9001, IATF 16949 or AS 9100)
- Root cause investigation results and previous corrective actions
2. Design Simple, Straightforward Questions
Another strategy for writing better LPA questions is improving how you construct checklists and questions themselves. LPA checklists should be short and sweet, taking under 15 minutes to complete and consisting 10 or fewer questions.
Well-written LPA questions are:
- Objective: Questions should be yes or no, and they should be easy to answer when comparing the process against the stated criteria.
- Specific: Instead of using vague words like “proper” or “appropriate,” LPA questions should state the exact specifications or tolerances for a given setting.
- Concise: Just like the checklist itself, LPA questions should be short and to the point. Make them clear enough that someone who is unfamiliar with the process could perform the audit, providing additional context if necessary.
Let’s look at a couple of examples:
Weak: Is the operator wearing the correct PPE?
Strong: Is the operator wearing a hard hat and safety glasses?
Weak: Are defective parts disposed of properly?
Strong: Are all defective parts tagged and set aside in a container clearly marked with red tape?
3. Refresh Questions Regularly
IATF 16949 and auto manufacturers require more than just a paper trail showing you’ve checked off a set of generic LPA questions. The entire purpose of LPA requirements is to engage in continuous improvement activities that ultimately push defect rates lower and lower.
To do that, your LPA checklists must constantly evolve to reflect new information and learnings, whether it’s a recent corrective action or updated requirement. LPA questions also need regular changes to keep participants engaged. Otherwise, as with any other repetitive process, auditors are more likely to end up on autopilot and miss problems.
Situations that call for updating checklists include:
- Changes in customer requirements
- Process or equipment changes
- Corrective action, audit and investigation findings
- Any time business objectives change
Layer Process Audit software like Beacon keeps questions fresh by randomizing checklists based on a custom pool of potential audit questions. Switching up questions helps prevent pencil-whipped data that results when auditors just pass everything automatically. It also provides better coverage across a wider range of issues, from materials and motions to workstation design, documentation and follow-up.
As a bonus, these systems also support images and documents to further clarify right from wrong, and the ability to take and attach photos during the audit process serving as evidence or proof of performance.
Continued checklist optimization and photo support represent two of the biggest advantages of an automated LPA system over a paper-based or spreadsheet-based system. It drives engagement and accountability, ensuring you’re in a position to make—and hold—greater gains than would otherwise be possible.