4 Practical Ways to Maximize Your Layered Process Audits
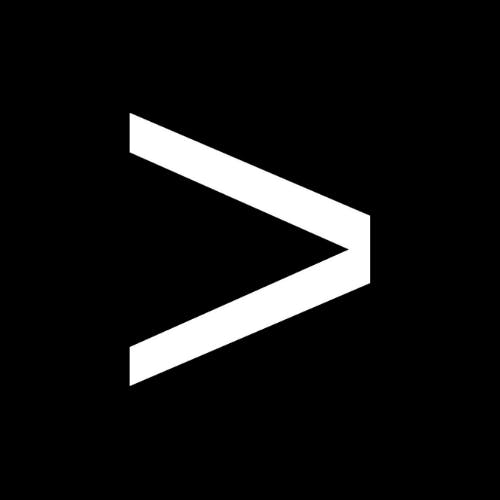
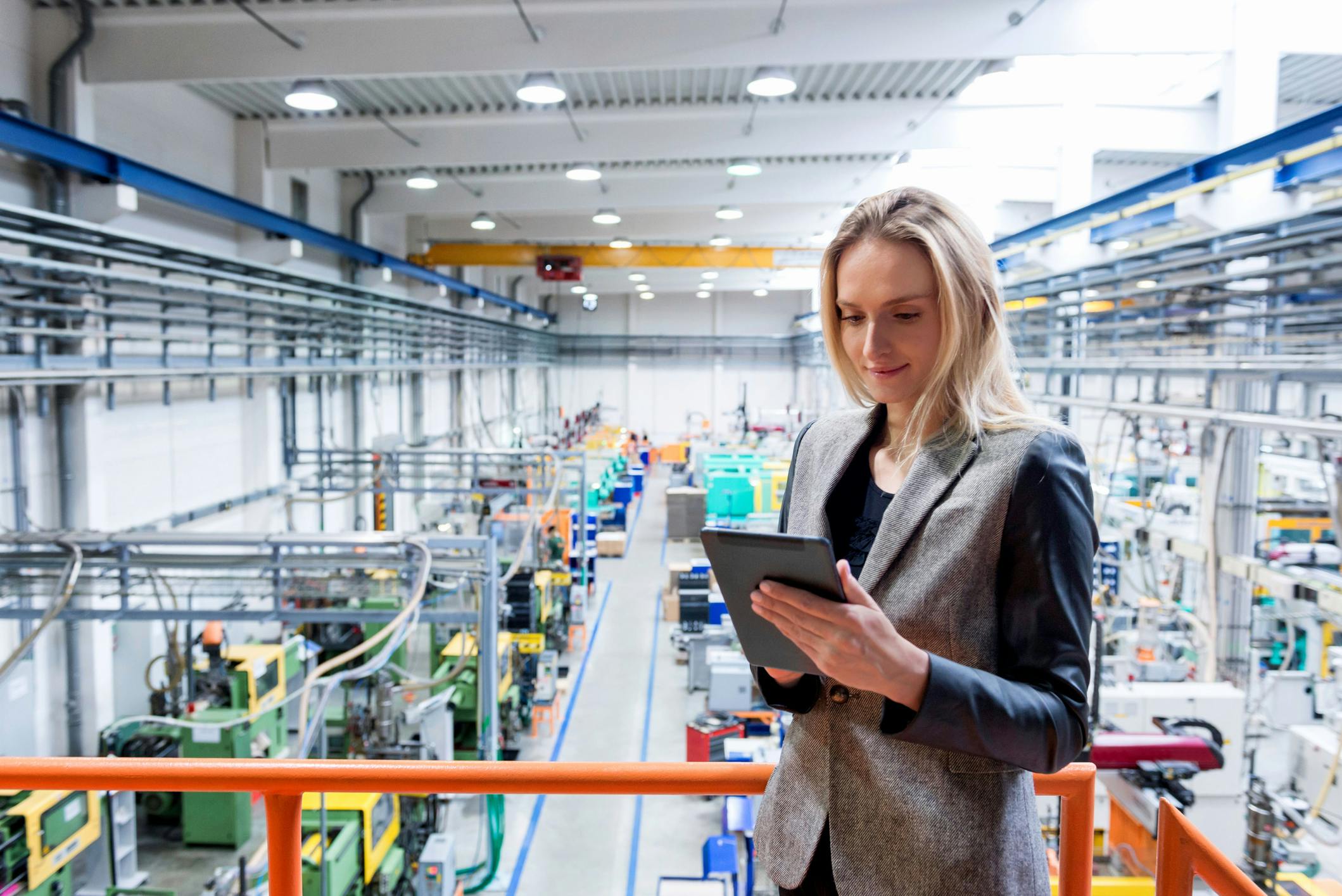
Understanding and applying key components of an LPA program are critical to success, but to maximize the short- and long-term effectiveness of an LPA, Ease has found that manufacturers should also integrate the following four key practices.
1. Empower Auditors
While rotating audit supervisors by management level ensures that every process is viewed from different perspectives, the benefit of these perspectives is greatly negated when auditors don’t have the authority to make corrective actions. By empowering the managers conducting LPAs to take action, issues can be addressed and remedied sooner, thereby reducing potential failure costs.
However, do note that there must be balance when empowering auditors, as too much authority may yield conflicts of interest within certain teams and functions.
2. Integrate and Automate
Integrating the LPA tool with your organization’s other systems, such as document collection and management and electronic work instructions, can further reduce variations, communication delays, and failures later in the manufacturing process.
For instance, in plants with manual change request processes, many requests take months to get reviewed. Even worse, many change requests get lost or never processed or enacted. The resulting cost and quality consequences can be severe, amplified by today’s short product cycles. By integrating the change request process with an LPA, the benefit of issue identification is immediately realized, since issues are automatically converted to a change request.
In addition, automation helps ensure proper scheduling and rotation of auditors by reducing the potential for human error or misunderstanding. In Ease’s experience, often auditors are not aware of the rotation requirement or the importance of audit frequency.
3. Foster Participation with Incentives and Competition
Many employees view LPAs as just another task: something implemented to satisfy a customer or company directive. Therefore, to help drive LPA enthusiasm, ownership, and cultural change throughout your organization, Ease has found it useful to tie incentives to LPA participation and results. Then, if an issue is identified during an LPA and a resulting change is implemented, we recommend aligning compensation with the success of the change in reducing variation and failure.
According to recent Miami University and University of Nebraska studies, financial and non-financial incentive systems can have a significant impact on participation levels, performance, and overall program success. Notably, studies have also found that financial incentives are effective even when modest.
To further enhance the impact of employee incentives, Ease has found that internal competition between teams or sites helps to increase employee eagerness and buy-in for the LPA tool. For optimal results, include internal competitions as part of the initial LPA implementation and align them to specific aspects of LPA participation and results. Finally, emphasize the benefits of the competition process, not just the results, in order to fully establish LPAs as part of a culture of continual improvement.
4. Educate Workers
Finally, Ease highly recommends providing ongoing education and mentorship regarding not only the LPA process and methodology, but also the benefits of LPAs to the organization and themselves.
When implemented properly, LPAs can have a real, substantial impact on quality, cost, delivery, morale, and safety—areas of interest for every employee. Reductions in rework, scrap, and customer rejections lead to improved company financial performance and the job security and potential job growth that come with it. Further, improved communication tools, such as the immediate report and acknowledgement of a nonconformance by a supervisor, reduces build variations and line worker confusion and frustration.
Education is critical, as LPAs often fall short due to a lack of employee understanding and subsequent engagement. In fact, a recent Harvard Business Review study found that the second most important driver of employee engagement is having a clear understanding of how your job/task contributes to the company strategy/goals. (The top driver is recognition given for high performance; e.g., employee incentives noted above.)
The more familiar employees are with LPAs, their purpose, and their impact, the more effective they will be in enacting change. Also, a better understanding of LPAs and their relationship to the organization will enable employees to be more knowledgeable of the overall company, which improves job performance and satisfaction.