4 Ways to Use Audit Photos to Improve Quality
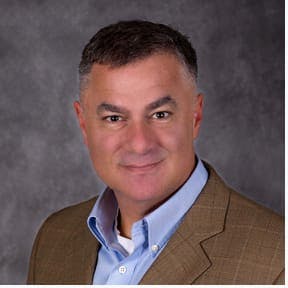
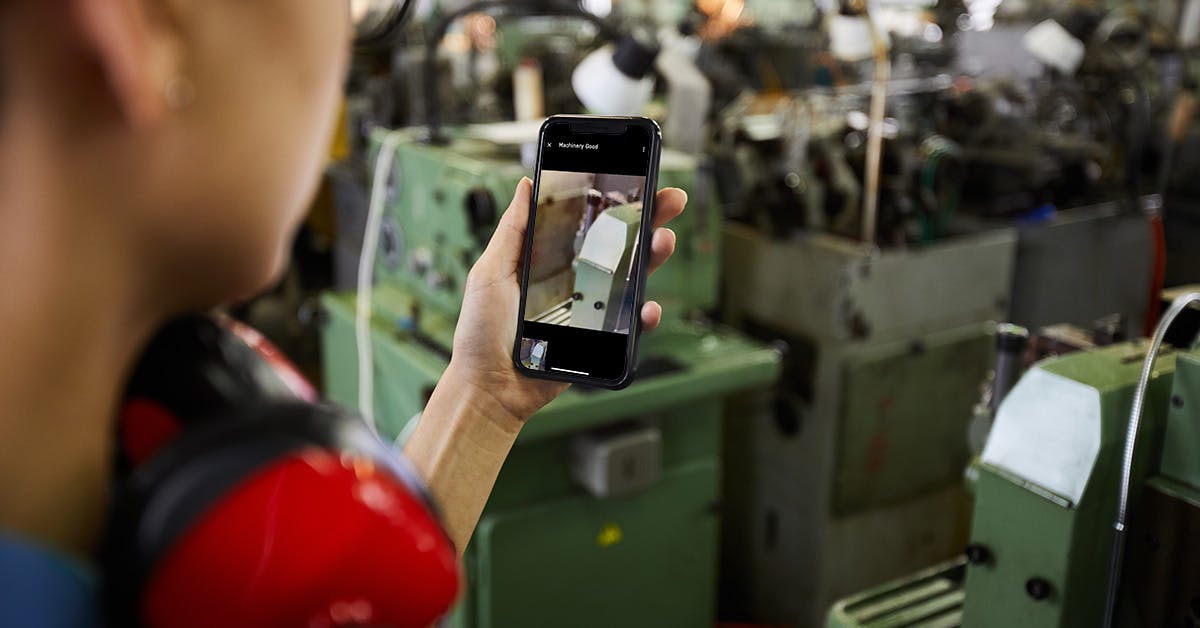
If you already use EASE for plant floor audits, you know how powerful it is for boosting visibility and reducing defects.
One tool built into the Ease software that can increase the success of audits is photo uploads. Photos leverage the “a picture is worth a thousand words” philosophy to make questions simpler, increase the reliability of data collected and provide more information about findings to facilitate root cause analysis.
At The Luminous Group, we recommend that 70-80% of questions have a photo associated with them. In other words, attaching photos to audit questions should be the rule, not the exception. In addition, we like to require a photo when there is a finding during an audit.
Let’s look at a few ways audit photos can help do this, including clarifying questions, improving audit compliance and boosting root cause analysis.
Download our free Ultimate Guide to Layered Process Audits for 93 pages of strategies, best practices and expert tips for getting more from LPAs.
1. Showing Auditors Where to Look
One place audit photos are useful is by showing auditors where to look. This is especially important with layered process audits (LPAs), which are short, fast checks of process inputs that take place on every shift and often involve auditing a workstation that may be unfamiliar to the auditor.
LPA auditors come from all over the organization, which is great for getting fresh eyes on processes. On the flipside, it means auditors may not be familiar with those processes. Having photos of where to look is key to keeping LPAs short. Photos are the enabler to getting more LPAs done and collecting more data for improving quality.
For example, imagine an LPA question that requires checking a machine’s water temperature. Will every auditor know where to look? Could an auditor look at the wrong gage?
Including a photo of the machine with an arrow pointing to the gauge location means the auditor won’t need help finding it and will check the correct process input every time.
The result: a question that might have taken minutes to answer can be accurately completed in seconds.
2. Showing Good vs. Bad Conditions
Audit photos can help auditors see which conditions are acceptable and which aren’t. It’s a critical piece of knowing when to pass or fail an audit question, which can mean the difference between a customer complaint and preventing a quality escape. In addition, it improves the consistency of your data and helps to direct action to the most critical areas.
Here’s an example:
Let’s say an LPA question asks whether a machine’s filter element is fully loaded. If the auditor isn’t an expert on this process, they may have no idea what fully loaded means.
Instead of expecting them to figure it out or take time to get an explanation, you could instead include two photos. The first would show a filter element in the fully loaded position, while the second shows a filter element sticking out half an inch. Again, you’d want to add green and red circles or arrows to the photo for clarity (most people use PowerPoint or a paint program).
3. Verifying an Audit Took Place
Using audit photos to verify people are actually doing audits on the plant floor is something we don’t see companies using enough.
As many already know, audit completion is one of the biggest challenges with LPAs. The high frequency and volume of the audits means people may be tempted to pencil-whip them. Some “other people” at “other companies” will even complete checklists without ever leaving their desks (we know this would never happen at your company!).
Requiring at least one photo with every audit can help avoid this problem.
For instance, let’s imagine an audit that requires the auditor to visit a weld cell. People might avoid going there, especially in summer when it’s 30 degrees hotter than the rest of the plant.
To make sure the audit takes place, you can simply require a photo on a question asking whether the cell is clean of weld spatter.
4. Improving Root Cause Analysis
Using audit photos to document failures can help with problem solving and root cause analysis, especially where the problem is corrected on the spot.
If you don’t take a photo in these cases, a manager may visit the plant floor to investigate the problem and it looks fixed. A photo helps clarify the conditions at the time of the audit, which can help address underlying issues.
One example we saw recently is where an LPA question asked if there were any trip hazards in the work cell. The auditor identified an extension cord hanging across the work cell. By taking a photo, the team recognized that the operator was using a corded drill rather than a battery-powered drill.
Digging deeper, they realized the operator preferred the corded drill because it was lighter. The solution they came up with was to add an overhead balancer, taking the weight of the battery-powered drill so it was easier for the operator to use.
Had they just moved the extension cord without taking a photo, they would never have discovered the true root cause of the trip hazard. It’s a perfect example of how to use LPAs to drive a culture where we provide the tools our operators need to work safely and efficiently.
Ultimately, that’s where a platform like EASE can really help people get more value from LPAs. Showing where to look, clarifying standards, verifying audits and documenting failure conditions all help move beyond just checking the box to an LPA program that actually impacts quality metrics.