5 Non-Audit Quality and Safety Findings You Should Be Tracking
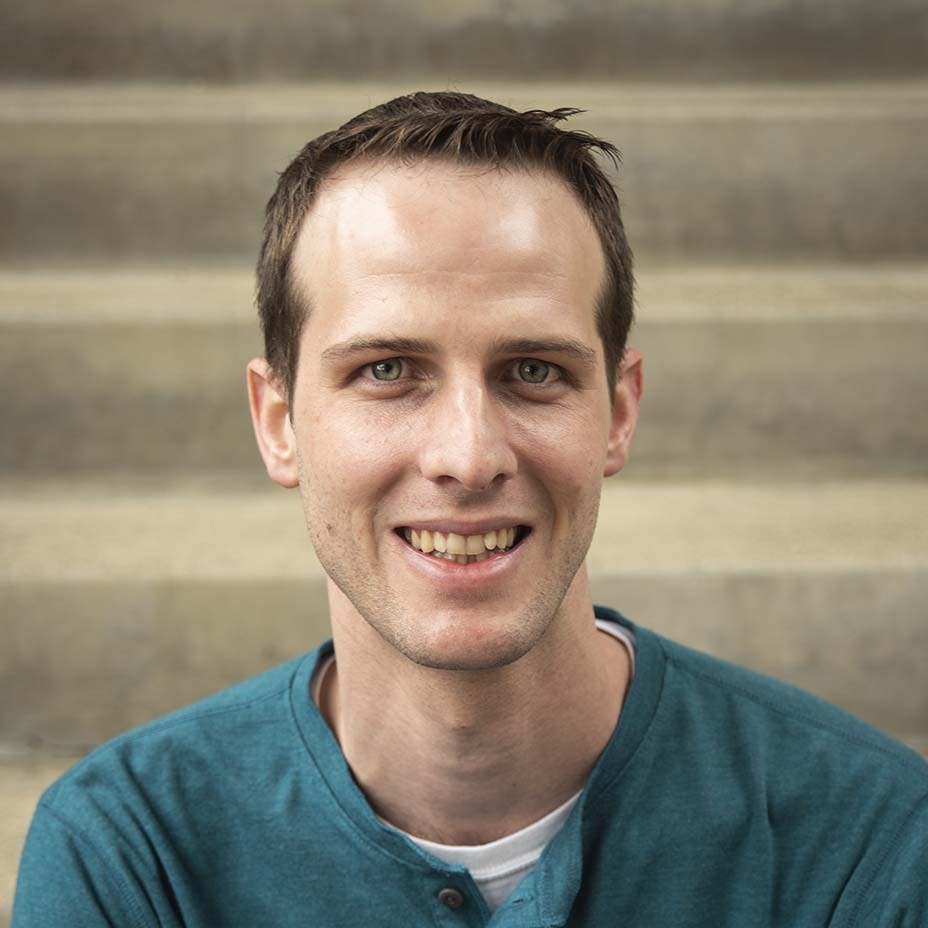
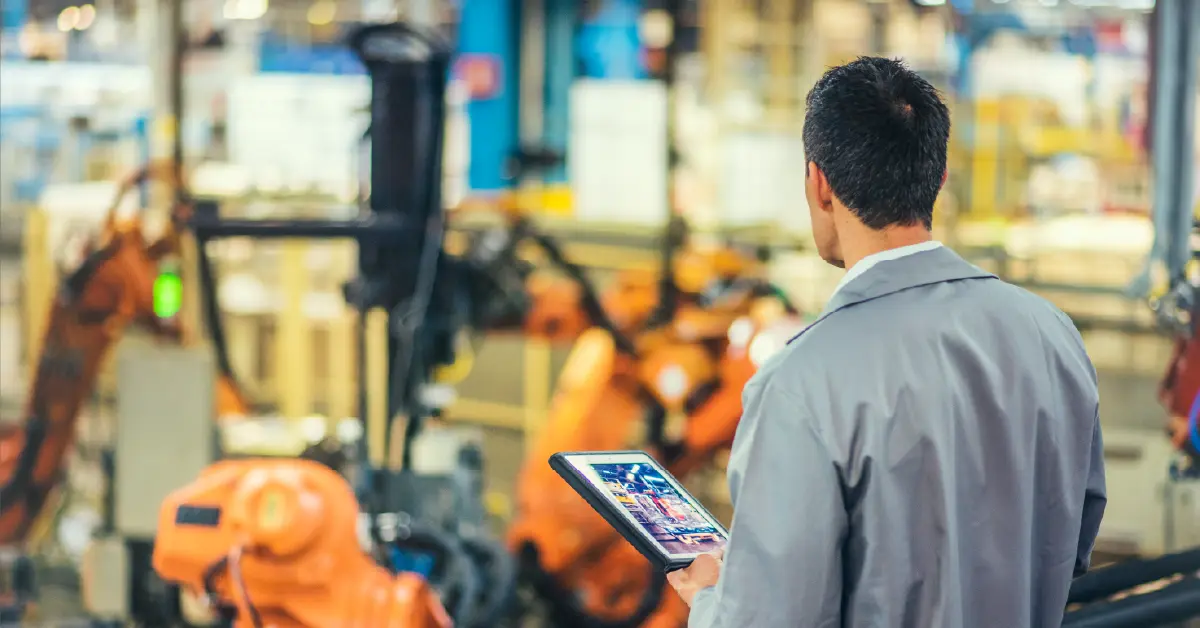
Capturing non-conformances in audits like layered process audits or 5S audits is critical to preventing process issues that cause defects.
But the truth is, audit non-conformances aren’t the only issues you should be tracking to prevent problems. Using a digital audit platform can also help you capture other findings to proactively identify risks and opportunities while fostering quality and safety culture.
In this article, we take a look at five types of quality and safety findings to track, and how to build your workflow to ensure a closed-loop process.
Download our free white paper on Digital Safety Inspections for more best practices and tips for working safer
1. Safety Observations
Recording safety observations is essential for companies that use behavior-based safety approaches. Centered on observation and feedback, behavior-based safety relies on documenting hazards and unsafe actions as well as recognizing safe behavior.
If you’re using mobile audit software to record your safety observations, you should look for the ability to create your own categories for classifying observations, such as unsafe procedures or hazardous conditions. This can help you identify if there are systemic safety issues present at your plant.
2. Incident Reports
Safety incidents cover a range of events companies can document with audit software. Incidents can include:
- Lost time accidents
- Minor injuries
- Medically consulted injuries
- Near-misses
Manufacturers may also categorize unsafe acts and jobs well done as incidents to capture in the audit system. In fact, recognizing a job well done is one of the most common incidents reported in manufacturing environments.
3. Near-Misses
Many companies don’t effectively record near-miss incidents as part of their safety process. While most people are likely to feel relief after a close call, the reality is that it’s one of the greatest predictors of future safety incidents.
Capturing and investigating near-misses in your audit system is crucial to investigating the incident and preventing it in the future. Consider, for example, a machine guarding issue where an operator narrowly avoids injury. If supervisors aren’t aware of the problem and don’t investigate, that increases the likelihood that it will happen again. Only this time, the operator might not be so lucky.
You first must train employees that near-misses are taken just as seriously as accidents and injuries. As such, near-misses should be defined as incidents to be recorded and investigated.
4. Operator Recommendations
Plant floor checks like layered process audits aren’t all about finding non-conformances. Experts also recommend manufacturers use layered process audits to capture operator feedback.
Why is this important?
For starters, operators have firsthand knowledge of potential issues that others aren’t aware of. Second, soliciting ideas and feedback from operators is also a fundamental component of quality and safety culture. When you take time to ask for ideas—and then take action—it shows genuine commitment to quality and safety. The result is greater ownership over quality and safety, and a belief that leadership takes employee concerns seriously.
Even if your layered process audit checklists aren’t set up to solicit operator feedback, mobile audit software with support for non-audit findings can help you capture and analyze these valuable insights as you walk the plant floor.
5. Improvement Opportunities
In addition to operator feedback, audit software can help you capture other opportunities to improve quality and safety. One example is around repeat findings.
Let’s say you’re conducting an audit and a question fails. Ordinarily, you might just record the failed question. What’s more helpful, however, is getting a notification that the question failed multiple times over the past 30 days. In this case, you could log an observation to suggest a corrective action around the recurring failure.
Another situation would be if, during an audit, the auditor notices a way to improve the process or increase efficiency. Having a place to log these ideas makes them more visible so that people can take action towards continuous improvement, in the process reducing “hidden factory” situations that cost manufacturers so much in the long run.
Building Your Workflow
If you’re using automated software like EASE to capture audit and non-audit findings, you’ll need to consider the necessary elements of your workflow to ensure proper follow-up. Common steps to incorporate into your workflow are:
- Categorization: Set up high-level categories to capture including observations, incidents and hazards.
- Sub-classification: Determine subcategories for each high-level category, such as lost time accident, minor injury, near-miss, unsafe act or job well done.
- Mitigations: Identify containment, investigation and follow-up action items.
- Photo evidence: Determine whether you will require a photo of the non-conformance or correction.
- Responsible party: Assign mitigations to one or multiple individuals.
- Urgency and approvals: Decide how you want to assign urgency to any mitigations created outside of audits and consider whether an approving party needs to review that the issue was addressed.
If an on-the-spot correction takes place, it’s still worth documenting that in the system to create a record of the issue and the correction. This creates a complete record of compliance that also makes it easier to identify repeat issues.
Capturing non-audit findings such as observations and feedback is essential to quality and safety culture. Empowering people to share their input makes them feel heard, increasing visibility into risks while showing management values their perspective. In the end, this drives greater investment and ownership on the individual level to drive a cultural shift overall.