5 Strategies for Your Layered Process Audit Rollout
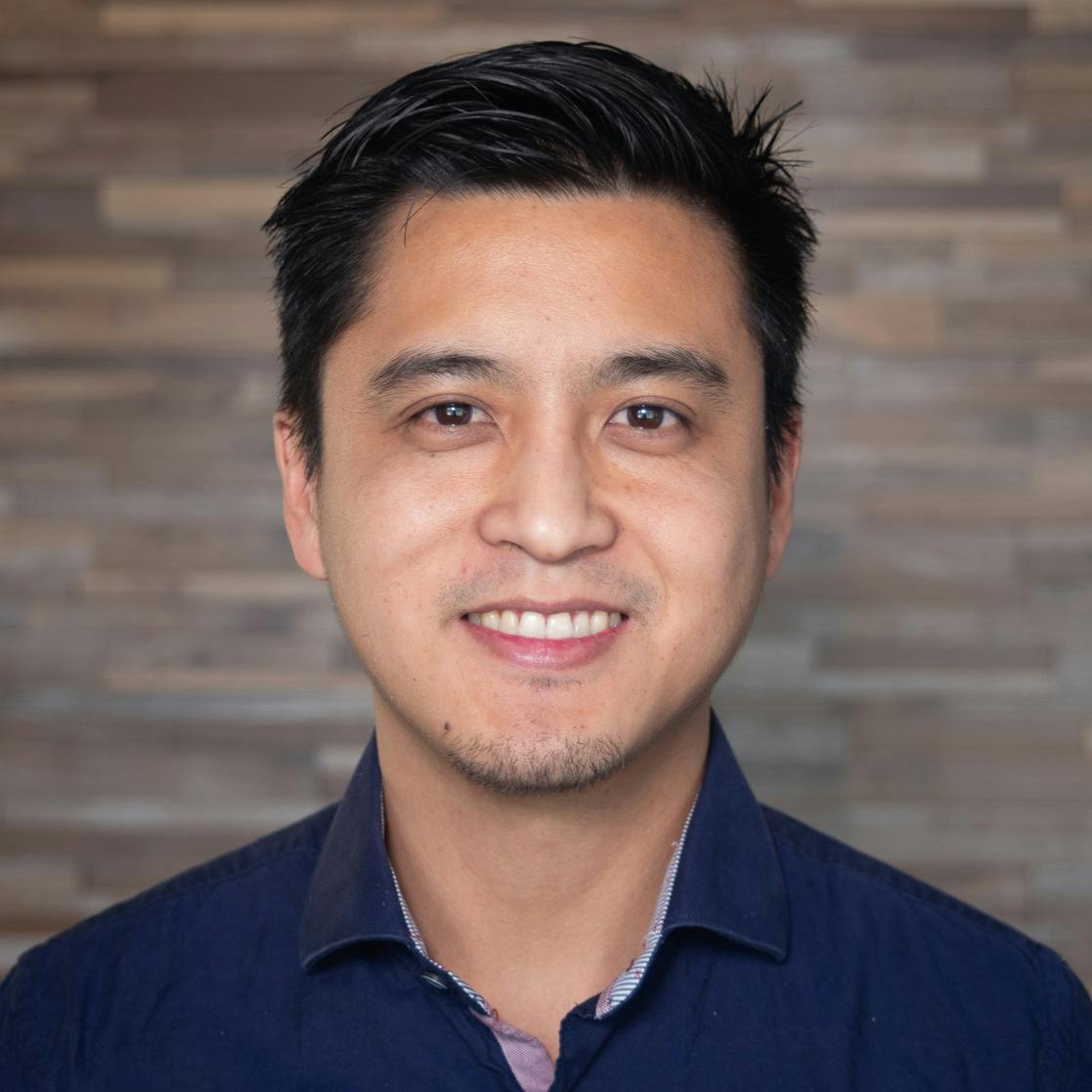
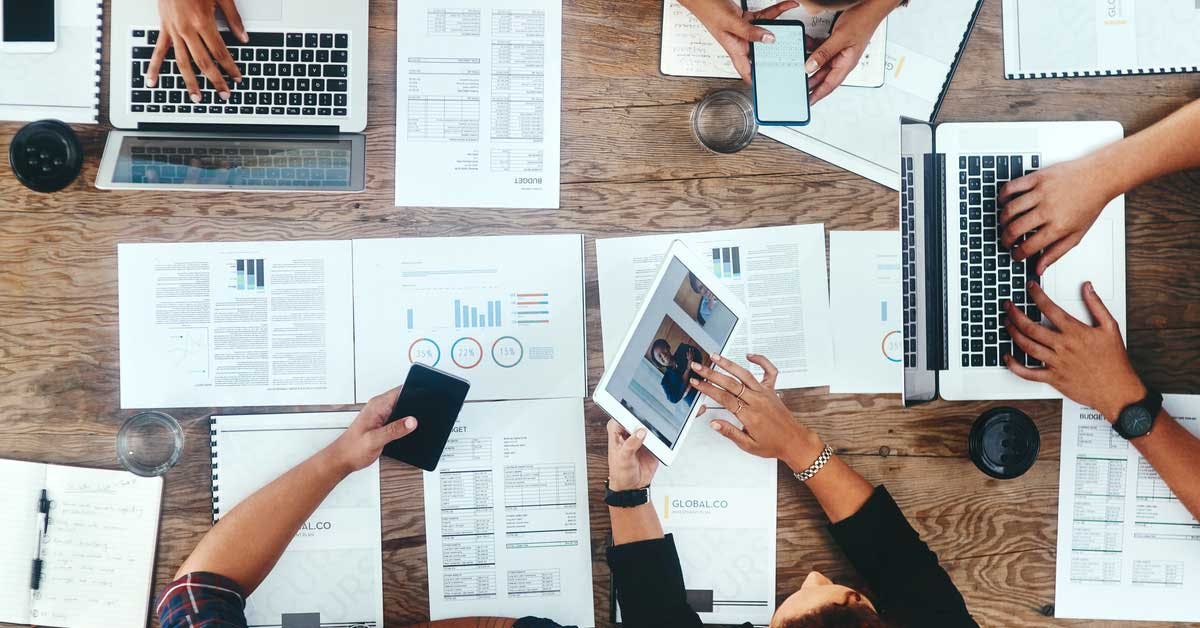
Quality management legend W. Edwards Deming famously compared management to looking at results to driving a car by looking in the rearview mirror.
Layered process audit (LPA) programs change that dynamic, helping manufacturers look ahead to where problems might occur so they can avoid them. These fast, frequent spot checks are conducted by team members from different layers of responsibility within a facility to shine a spotlight on critical processes and problem areas.
As for whether the audits achieve their intended result, a good start can go a long way toward getting you on the right track.
This post covers 5 strategies for your layered process audit rollout, including how to involve the right people, where to start and how digital LPAs can boost results.
Get more strategies and tips on LPA implementation with our Ultimate Guide to Layered Process Audits
1. Make Management Participation a Priority
The management team is crucial to a successful LPA implementation. That’s because having buy-in at the top increases awareness of defect-causing operations across the entire plant.
Here’s how it works:
With more people looking at critical processes, it’s only natural that operators will take steps to ensure compliance with standards. Furthermore, seeing various levels of management involved also shows operators that leadership is truly committed to preventing defects.
In other words, with extra attention comes extra diligence—and the understanding that quality is a core value across all layers of management.
2. Start with a Pilot Program
Choosing the first area to attack using LPAs can be tricky. Rather than rolling them out to the whole plant, some organizations have found it better to start with a smaller pilot program.
So where should you start with your pilot program? Ideas include starting with an area where people are ready and eager to try something new, or an area in need of improvement that can deliver early wins and momentum.
Once you have the process down, the LPA team can continue the rollout through other parts of the facility. Having the first group train the next can help, giving people the chance to learn from their peers rather than a traditional top-down training approach.
3. Use a Kaizen Event to Kickoff LPAs
A Kaizen event is a team-based approach to honing in on a problem and driving rapid improvement. Assembling a group of team members to brainstorm and implement solutions can be a shot in the arm for long-standing problems in a facility, and is also a great way to start your LPA implementation.
The standard steps of a Kaizen event usually include:
- Assembling a cross-functional team of stakeholders
- Holding a brief training event introducing LPAs to the team
- Development of LPA questions
- Development of targets and KPIs
Each of these steps is crucial to implementing LPAs in your facility. By introducing LPAs to your cross-functional team through training, you force everyone to be on the same page. Since auditors conduct these checks independently, it’s important that everyone understands the objectives ahead of time.
4. Go Digital to Boost Audit Completion Rates
Sometimes it can be difficult to get people to complete their assigned LPAs. Leadership participation can go a long way towards preventing this problem, but you may have to try other solutions if it persists.
An automated mobile audit platform like EASE can help improve audit completion rates and simplify follow-up by:
- Sending email notifications to auditors when it’s time to do their LPA
- Making it simple to complete the audit on a mobile device, rather than having to input findings on a paper checklist or spreadsheet
- Escalating missed audits to managers who can investigate further
- Providing data on audit duration to identify pencil-whipping
- Allowing you to link audit findings to corrective actions to ensure problems don’t fall through the cracks
5. Communicate with Your Team
Communication is an essential part of any new initiative. Communicating with your team during an LPA rollout should include:
- Notifying operators that they will be audited, being sure to reinforce that the purpose is not about blaming but improving processes
- Training auditors to catch people doing things right, and to make audits a genuine conversation that includes operator suggestions and feedback
- Conducting management review of LPA data to proactively identify problems and trends
- Sharing successes and highlighting problems solved to boost engagement
More than just identifying process non-conformances, LPAs are a tool for communicating what people should be paying attention to. By engaging more people in a specific problem, the problem has higher visibility. Visibility means attention and attention means more compliance with standards, promoting process standardization and, in turn, improved quality.