5 Surprising Insights Hiding in Your Plant Floor Audit Data
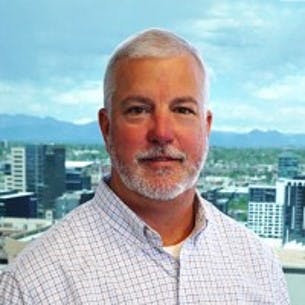
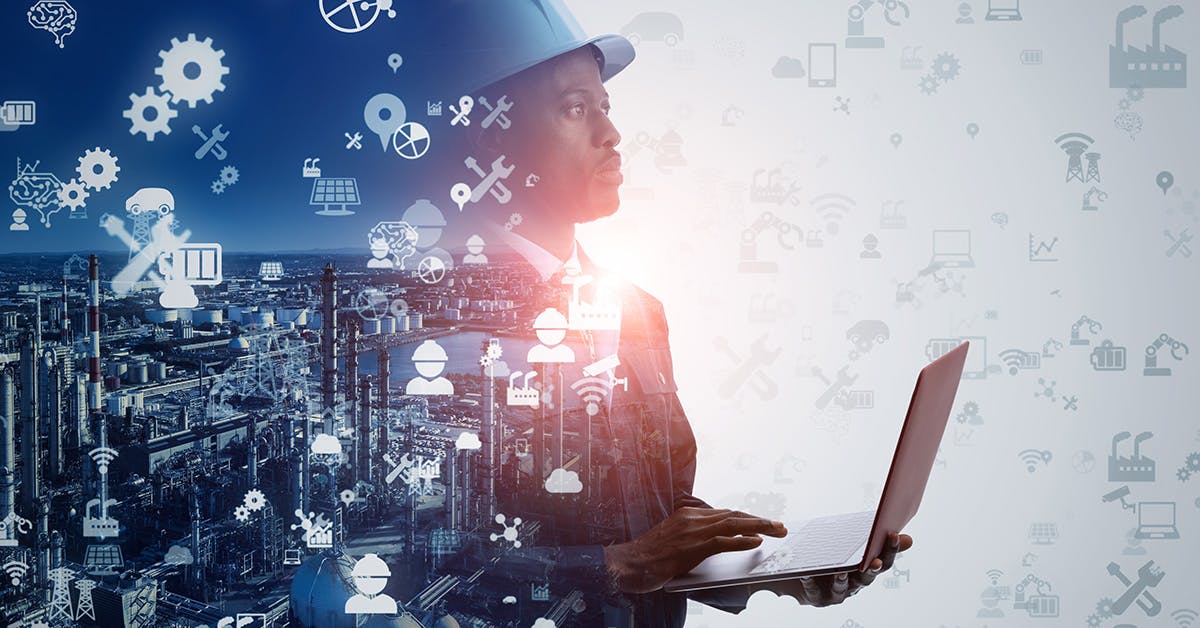
If your company conducts plant floor audits such as layered process audits (LPAs), you probably already track metrics like audit completion rate and audit pass rate.
What might not be so obvious, however, are the deeper insights hidden in your data—many of them available without advanced analytics.
Today we’re looking at five surprising insights hiding in your plant floor audit data that can help you address several root causes of quality and safety problems.
What do meaningful LPA results look like? 3 quality leaders discuss management’s role in a successful LPA program
Audit Checklists and Questions Need Updating
While your inspection pass rate is an important metric to track, it’s also worth looking at question pass rates. In this context, a question having a 90% or 100% isn’t necessarily a good thing. In fact, it may indicate that the question needs updating.
High-frequency auditing techniques such as layered process audits (LPAs) should only last about ten minutes, so every question should deliver value. If the question passes every time, think about rotating it out for a new one, or randomizing the question so it still shows up on audit checklists periodically. LPA software makes it simple to do this, so you can easily cover a wider range of risks with your audits.
It’s also worth considering whether auditors are simply skipping the question because it’s too confusing or complex and needs revision. If you’re using mobile audit software to manage checklists, you can update the existing question (rather than creating a new one) to retain the compliance history of that question.
Operators Don’t Have What They Need
One surprising insight you can get from plant floor audit data is when operators don’t have everything they need to do their jobs safely. For example, let’s say you conduct an audit and discover an extension cord from a drill that’s a trip hazard in the work cell.
Requiring a photo of the audit finding could reveal that the operator was using the corded drill because it was lighter than the correct tool, a battery drill. Understanding the true root cause leads to a permanent fix—adding an overhead balancer to take the weight of the battery drill—rather than just fixing the trip hazard.
Using mobile audit software to capture audit photos can lead to many deeper insights. This function allows you to do things like:
- Investigate audit findings
- Show what good vs. bad looks like
- Document mitigations or corrections
- Capture proof that an audit took place
Systemic Quality and Safety Issues
Fixing one-off audit findings is beneficial, but using audits to identify systemic quality issues is where companies can really make huge quality improvements. One manufacturer has successfully used mobile audit software to do this, using an innovative process centered on dynamic question banks.
The process involves:
- Building a library of questions tagged by categories such as equipment, process, and materials
- Conducting audits with the above questions rotated throughout the checklists
- When a question fails on one machine, changing the tag to label it as a focus question
- Adding the focus question to all audits where the issue could occur (e.g., similar process or equipment), limiting focus questions to just one or two per audit
This strategy allows you to do a fast look across the plant to identify whether an audit finding is a one-off failure or a systemic issue affecting multiple work cells.
Gaps in Employee Training
Demonstrating training effectiveness is a requirement for external audits such as ISO 9001 and IATF 16949 audits. Plant floor audit data can help assess hidden gaps in employee training, also helping document verification of training effectiveness.
One way to do this is to develop questions from employee training that get rotated into mobile audit checklists. When you review data monthly or quarterly, you can assess whether a high fail rate indicates areas of training that need improvement.
People Are Pencil-Whipping Audits
Using your plant floor audit data to identify when people are pencil-whipping their checklists can help ensure you’re getting reliable data from your audits. There are a few strategies manufacturers use to do this:
- Include a dummy question that should trigger a ‘no’ answer on the audit, like whether Mickey Mouse is a cat.
- Look at audit duration to see where people may be rushing through audits or just completing them from their desks
- Require a photo to be uploaded to every audit to verify the auditor visited the plant floor
Plant floor audit data can hold important insights into the state of quality in your organization. Mobile audit software like EASE streamlines the process of collecting plant floor audit data, allowing manufacturers to capture photos, create dynamic checklists and question libraries, and verify audit compliance.