5 Tips for Managing Repeat Audit Findings
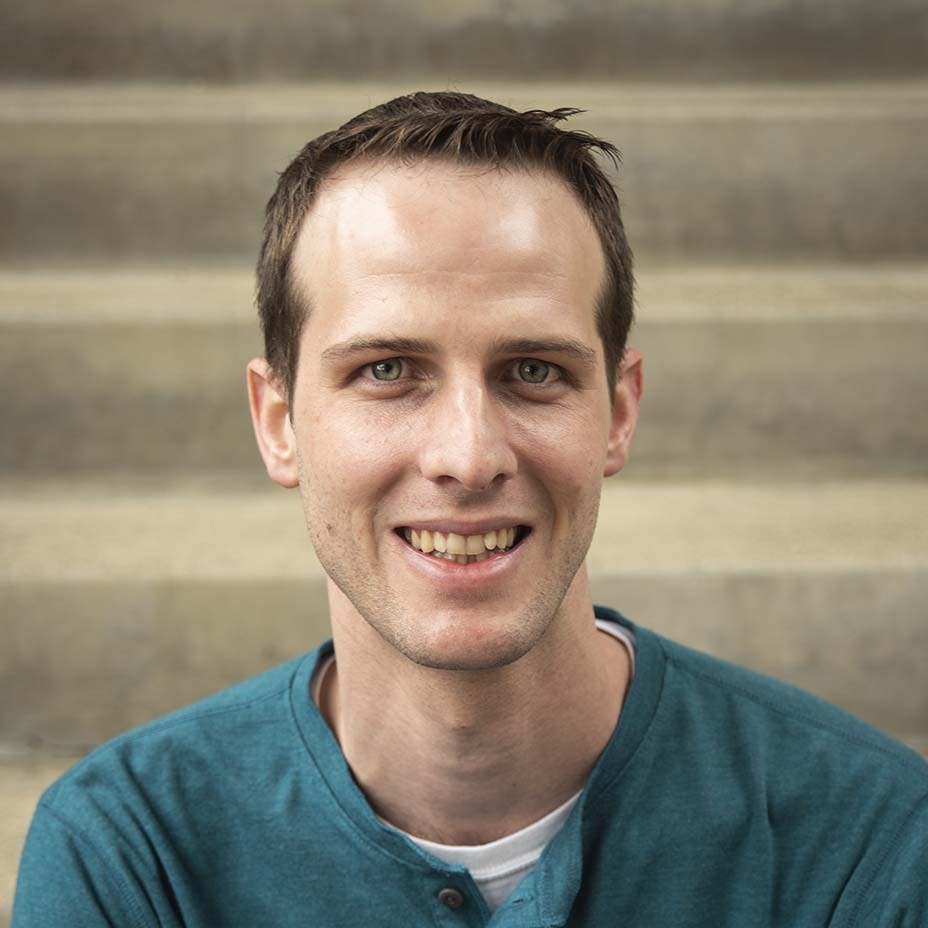
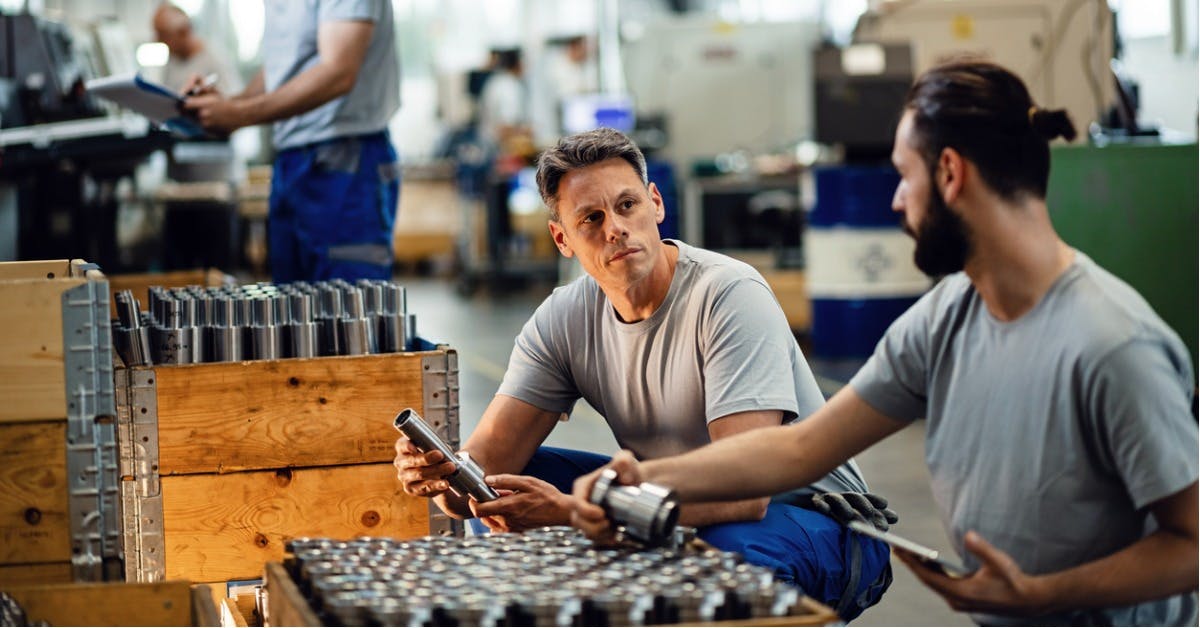
Plants that do layered process audits (LPAs) often perform hundreds of checks per month, providing important insights into process nonconformances that lead to product defects.
Repeat audit findings in particular are important to identify and monitor given that they represent unmanaged risks likely to affect the customer.
The silver lining, however, is that you can use repeat findings as an opportunity to drive continuous improvement and prevent complaints. Within this context, here are five tips for managing repeat LPA findings to reduce risks and accelerate the resolution of systemic issues.
Learn the 5 ways LPA programs most often fail in our FMEA of LPAs webinar
1. Treat Repeat Findings as Strategic Opportunities
While it’s hard to imagine repeat findings as a good thing, the truth is that they represent a unique opportunity for manufacturers. That’s because real improvements aren’t driven by one-time actions—they’re driven by addressing systemic issues, which repeat findings are evidence of.
It all goes back to the Pareto Principle, also known as the 80/20 rule. This rule states that 20% of inputs drive 80% of your results. Identifying and tracking repeat findings places the focus on the 20% of inputs that cause 80% of your quality problems.
One global tire manufacturer frames it this way: if you’re just hopping from one corrective action to the next, you’re less likely to recognize the full value of LPAs. The real win is identifying repeat findings and correcting systemic problems.
2. Track and Analyze Your LPA Metrics
Tracking and analyzing LPA metrics is an important place to start when looking at how to manage repeat findings. This includes looking at trends in not only findings but metrics related to the overall health of your LPA system as well.
For example, when you look at LPA questions that fail repeatedly, are they clustered around one process or production line? What about a certain shift or time of day? If you have 10 repeat findings and 8 of them are in injection molding, you have a better idea of where you need to focus your efforts. Asking these types of questions can help identify the root cause of an issue, such as if a standard isn’t stable or operators aren’t being trained correctly.
It’s also worth looking at which auditors are logging findings. Are the repeat findings coming from layer 1 auditors, or are they only being caught by layer 2 auditors? If it’s the latter, you may have a problem with layer 1 pencil-whipping their audits, since they are the front line who should be catching these issues most often.
3. Flag Repeat Findings During Audits
Identifying repeat findings doesn’t necessarily have to be limited to reviewing LPA data after audits take place. In fact, being able to flag them during the audits themselves can help accelerate resolution and shine a spotlight on unresolved issues.
Within the EASE LPA platform, for example, auditors are notified if a failed question with a finding assigned also failed at that same location in the past 30 days, providing insight into:
- How many times the question has failed recently
- The status of any related findings
- The auditor who previously reported the issue
This capability can help plants uncover recurring issues faster, also showing leadership where more formal corrective actions may be necessary.
4. Examine Your LPA Questions
In some cases, repeat findings can be a symptom of problems within your LPA questions. Bad questions mean bad responses, and ultimately more repeat findings.
Common problems that can cause LPA questions to fail repeatedly include:
- Not involving operators in evaluating questions
- Confusing or ambiguous wording
- Questions that are based on unstable standards
One approach to improving your LPA question library is to hold a Kaizen event with individuals such as process engineers, quality engineers, operators, and a black belt facilitator. From there you’ll want to bring in control plans, standards, and work instructions to ensure questions reference standards. This can also help you shore up standards themselves so that questions and processes aren’t based on tribal knowledge.
5. Use a Dynamic LPA Question Library
If you’re using an LPA solution like EASE, one powerful strategy for managing repeat findings is using question tags or categories to identify systemic issues. For example, the same global tire manufacturer uses a special tag for failed questions called focus questions. When a question fails, they change its tag to focus question and then that question is dynamically pulled into all audits on similar equipment for several weeks. This approach enables them to quickly separate one-off findings from repeat issues, allowing them to prioritize actions to address their biggest risks.
At the end of the day, managing repeat audit findings effectively requires a systematic approach to identifying and tracking them. A digital audit and inspection app provides this framework, uncovering actionable insights in real time while eliminating hours of audit management and data analysis.