Are Layered Process Audits Getting in the Way of Quality?
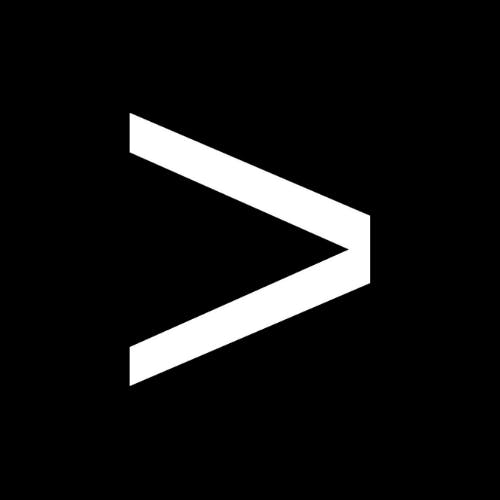
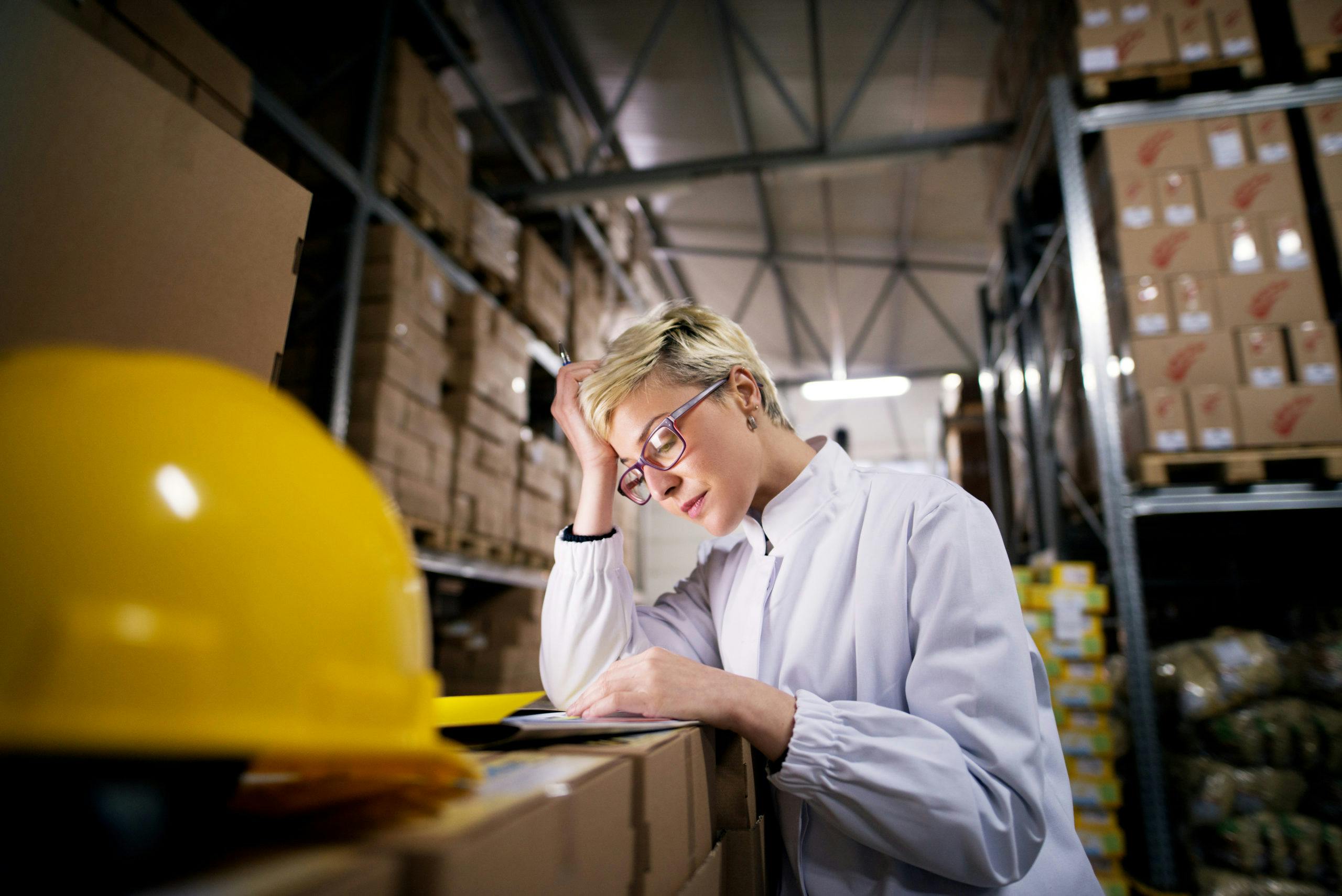
According to the Deloitte Automotive Quality 2020 report, auto manufacturers spend an average of 116 days annually on quality management system (QMS) compliance.
Layered process audits, which can number more than a thousand audits per year, can take up many of those hours for companies that perform these short, frequent checks.
Executed correctly, layered process audits (LPAs) can help sharply reduce defects and quality costs relatively quickly, but these high-frequency audits can also bury companies in administrative work if they’re not prepared.
This post examines classic problems standing in the way of quality, and how to fix them to make bigger and faster improvements.
Download our free case study to learn how one automotive manufacturer reduced internal PPM 73% with LPAs
Scheduling Inefficiencies
Making and sticking to a schedule is fundamental to LPA success, but the reality of scheduling daily, shift-level audits of critical to quality processes can quickly become overwhelming. Scheduling around paid time off and planned downtime is more complex and time-consuming, as is notifying auditors of their responsibilities.
An automated LPA platform provides an advantage for companies that opt for automation, allowing them to create an annual audit schedule integrated with Outlook in a matter of minutes.
Low Audit Compliance
Low audit completion rates are a thorny problem for many companies, preventing quality improvement by:
- Allowing problems to slip through the cracks
- Limiting the amount of data companies collect
- Sending the message that LPAs don’t matter
Adding alerts to calendar invites can help remind people not to skip audits, but low audit completion rates often represent an accountability problem. If skipping audits is standard practice, why should anyone participate? The fix is simple—people should have to answer to management for missed audits. And if management won’t hold them accountable, you’ll need to go back and get leadership buy-in for LPAs.
Poor Data Quality
Data quality is another common challenge for companies that conduct LPAs. The two main problems are pencil-whipping and questions that don’t add value.
Pencil-whipping occurs when people just check the box to complete audits quickly. One way to identify when this is by timing audits. If someone completes audits in under a minute, it’s unlikely they were looking very closely.
The other problem gets back to LPA questions themselves. Many companies rely on generic questions used plant-wide, but getting quality data requires questions specific to the process or work area.
Lack of Coaching and Feedback
Using audits to cast blame means missing critical opportunities for coaching and feedback. One manufacturer we heard from even suggested calling LPAs layered process coaching, given the kinds of interactions they facilitate.
At their core, audits bring leaders face-to-face with plant floor issues, also giving operators the chance to be heard. To get these benefits, you have to show respect by:
- Making eye contact with the person you’re auditing
- Demonstrating genuine interest in understanding the process
- Soliciting feedback and suggestions
- Asking why rather than criticizing workers when you find a nonconformance
- Giving praise when people do things right
Not Addressing Nonconformances
If you don’t have a closed-loop process for following up on nonconformances, your audit program is dead in the water. Not only are you risking quality escapes, you’re inadvertently telling your team you don’t really care about audit findings—which means you can never build a culture of quality.
Fixing this problem requires a standardized process to:
- Notify supervisors of nonconformances requiring corrective action
- Create a corrective action plan outlining responsible parties and timelines
- Circle back on problems to hold people accountable for action items
- Regularly review audit results with management and address overdue items
An automated audit platform streamlines this process, especially when it’s linked into corrective action tracking.
Reporting Lag Time
Reporting is another crucial area where an inefficient process can get in the way of results. It’s particularly difficult when manufacturers rely on manual or spreadsheet-based tracking, which creates a delay between when audits are conducted and findings are analyzed. Someone has to input the data and analyze it by hand, a process that uses valuable time while problems continue unabated.
Automation can be a driver of change here, allowing companies to identify problems in real-time, so they can take action immediately to head off potential quality issues. Freeing up this time also means people can focus on strategic quality projects in place of data entry.
Lack of Verification
The final piece of ensuring that your audit process isn’t blocking quality is verification of corrective actions and revisiting missed audit items.
For many organizations, it’s hard enough dealing with the backlog of corrective actions, let alone going back to see whether they’re actually working. Getting it right can be as simple as adding a new question to LPAs that gets randomly rotated in, allowing you to make sure you’re holding the gains.
The traditional approach to LPAs involving paper checklists and Excel spreadsheets data entry creates inefficiencies that ultimately get away from quality. LPA automation can address these inefficiencies and take the focus off of administrative work so teams can focus on their true job—improving quality and keeping customers happy.