4 Ways Layered Process Audits Foster a Culture of Quality
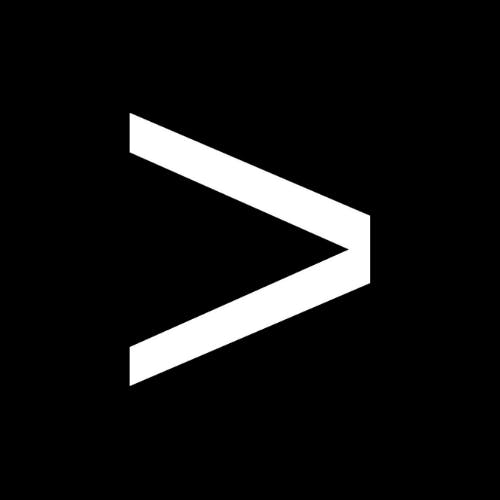
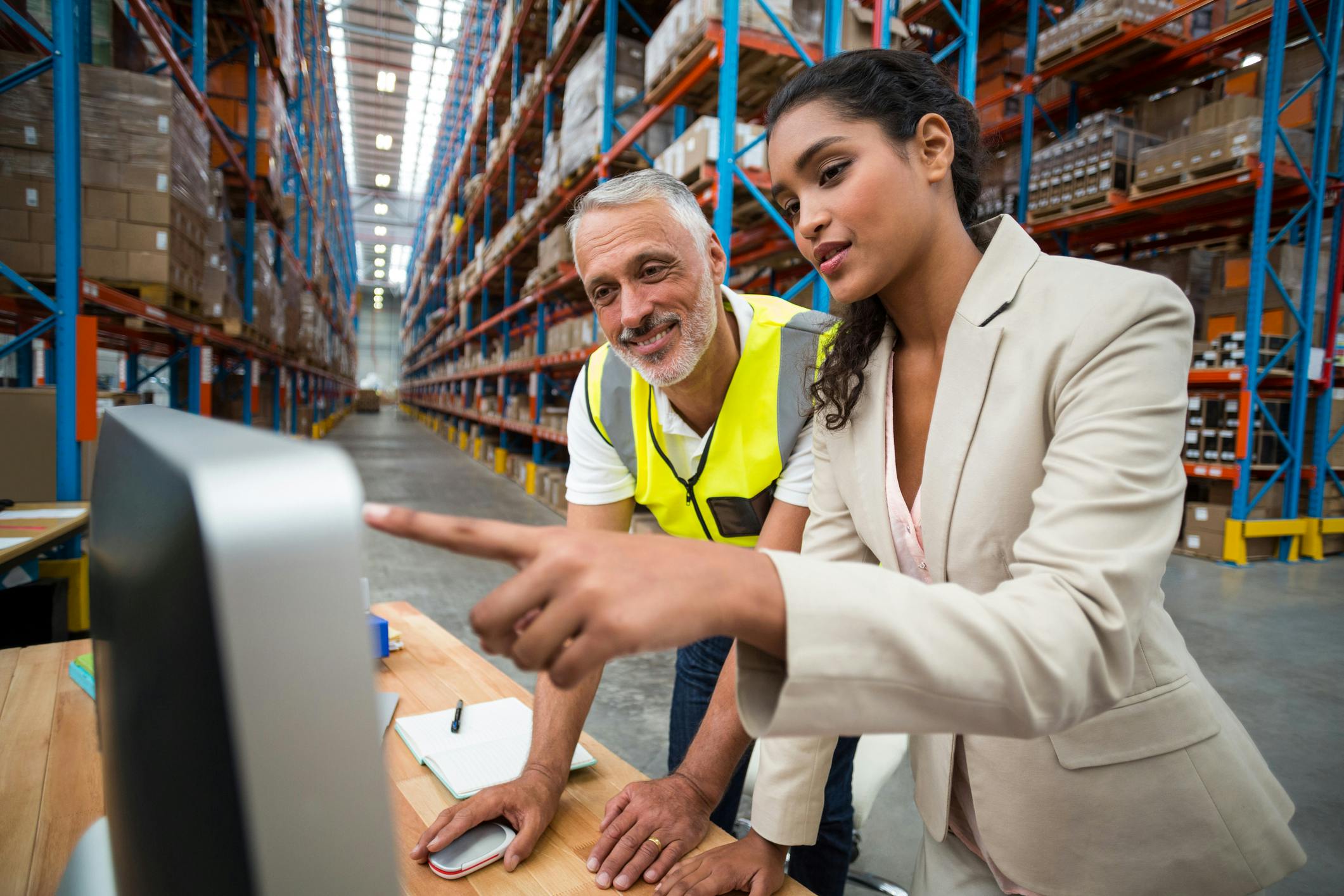
Companies with a robust culture of quality save an average of $350 million annually compared to low-performing companies, according to a survey by CEB. While the benefits are clear, getting there is no simple task. In fact, 6 in 10 companies struggle to create a culture where quality is a personal priority to employees, instead of just a management requirement.
So how do you achieve cultural change, an element that is both intangible and reliant on human behavior? Auto and aerospace suppliers are finding that layered process audits (LPAs), in addition to reducing defects, foster quality culture in several important ways.
In this post, we’ll look at how LPAs promote a culture of quality through standardization, leadership engagement, communication and customer satisfaction.
1. Process Standardization
LPAs involve multiple layers of management who conduct frequent, short audits of critical processes. One of the main objectives is standardization, which drives the consistency of quality needed to meet customer expectations. LPAs promote process standardization through:
- Concentrated focus on high-risk or error-prone processes identified in process failure modes and effects analysis (PFMEA) and customer complaints
- Ongoing checks to verify that operators are following standard quality and safety procedures
- Proactive identification of process issues before they cause product defects, a hallmark of quality culture
2. Leadership Engagement
Lean and other methodologies like ISO 9001 underscore leadership engagement as a core principle. And yet, one of the main problems companies face—roughly half of them, according to the CEB study—is insufficient leadership emphasis on quality. It’s understandable, given the many pressures leaders face daily, but this lack of involvement sends the wrong message to employees.
LPAs provide a structure for engaging leaders in a meaningful, authentic way. With supervisors conducting audits as often as each shift, operators get face time with leaders daily. What’s more, the audits aren’t part of the quality department—the LPAs belong to the department where the audits take place.
This level of presence and involvement sends a subtle but important signal that company leaders are genuinely invested in quality. And when supervisors and managers step up to the plate, employees are more motivated to do the same.
3. Open Communication
Correcting problems is painful in many organizations. Some leaders aren’t good at giving feedback, resorting to anger and punishment when they find problems. Employees, too, often struggle with accepting constructive feedback.
LPAs enable a culture of quality by creating opportunities for operators and leaders at all levels to improve their communication and feedback skills. As people get used to having these conversations, everyone becomes more comfortable sharing concerns and problems.
The types of insight you can gain are limitless when you experience shop floor conditions up close. You might find an operator doesn’t have time to repair a critical tool, a manager needs additional coaching or that a long-held assumption is incorrect.
4. Meeting Customer Expectations
The central goal of quality management is to satisfy customers, and yet many companies lack the data they need to keep customers happy. In particular, customers with mature supplier quality management (SQM) processes often have more information on a supplier’s performance than the supplier itself. In these situations, customers discover quality problems before the supplier does, driving up scrap, rework and quality costs.
LPAs lift the lid on the hidden factory controlling quality, helping you see areas that need improvement before product ever leaves your facility. Collecting this data is difficult without full-time employees for scheduling and managing the hundreds of audits that must take place annually.
The alternative is using LPA software, which can reduce administrative overhead by as much as 85 percent. Key capabilities to look for in these systems include:
- Automated scheduling that accounts for time off and non-working days
- Notifications to remind you when to execute the audit, as well as to escalate overdue audits to supervisors
- Centralized checklist repository with question randomization to prevent pencil-whipping or automatically passing all items without question
- Mobile audit capabilities that allow you to use a tablet or smartphone rather than a paper checklist
- User-friendly analytics that give instant insight into LPA results
Conducting LPAs alone isn’t enough to create a culture of quality. If you’re only doing it to satisfy a customer or regulatory requirement, you can’t expect to achieve the results discussed here.
Instead, you need to have the internal motivation to improve your products and processes. With that key element in place, you’ll be in a position to use LPAs as a tool for building and reinforcing your culture of quality.
Learn more about layered process audits with our free white paper on Optimized Process Audits.