5 Questions that Reveal Whether Your Plant Has a Culture of Safety
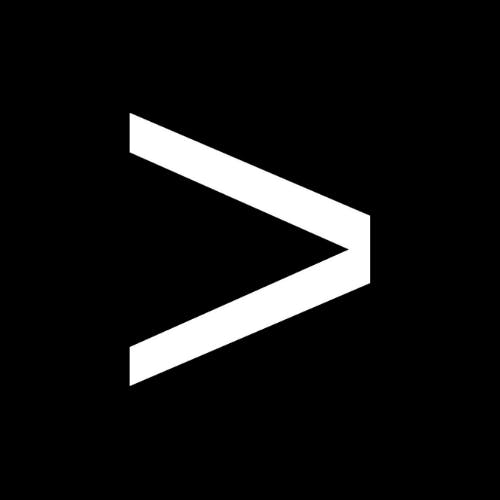
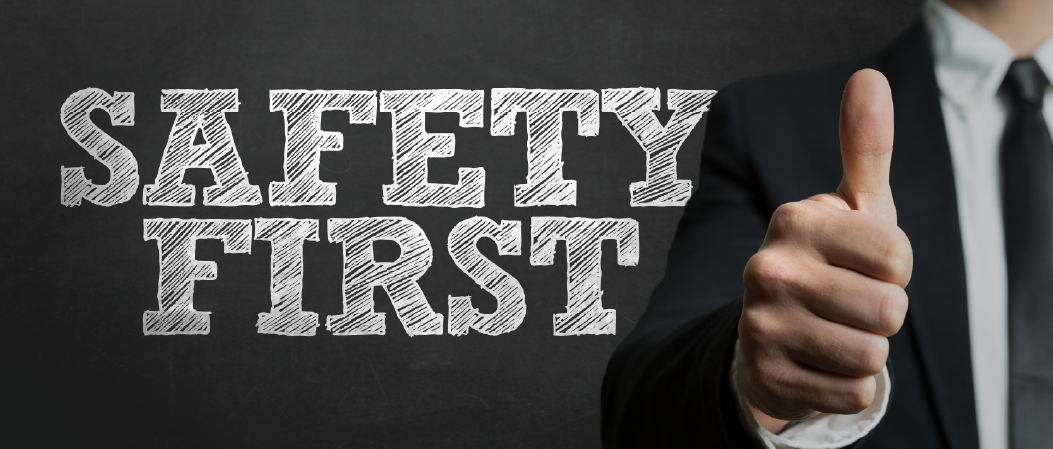
According to the National Safety Council, the average cost of a medically consulted injury is $42,000.
However, the true cost is far higher when considering the impact on employee satisfaction, turnover and morale.
Fostering a culture of safety should be a top goal for every manufacturing plant, helping protect your most valuable resource as well as company profits.
So how do you know if you have a culture of safety?
In today’s post, we take a look at five questions that can point you to the answer—and where you might need to make improvements.
- Learn how digital safety inspections can help make your plants safer
1. Do People Take Ownership of Safety?
People taking personal ownership of safety is one of the most important parts of safety culture. Discussions of safety culture focus heavily on leadership’s vision and commitment, but those don’t matter if people on the front lines don’t care about safety.
So what does it mean when employees take ownership of safety? It means that safety is personally important to them, so that they:
- Notice hazards rather than just ignoring them
- Share safety observations with management
- Take action to eliminate hazards
- Step in when they see someone doing something unsafe
2. Are Near-Misses Reported?
When an accident almost happens but doesn’t, how do people respond? While relief is a natural reaction, the truth is that near-misses are a leading indicator that provide helpful information on where safety incidents are likely to occur in the future.
For simple proof of this, think of how many times after an accident you’ve heard someone say, “I knew that was going to happen.”
So while you might be tempted to just be thankful that nobody got hurt, it’s critical to realize that near-misses actually are safety incidents and should be reported as such.
3. Is Management Present on the Plant Floor?
Management is a key driver of company culture, and it’s also true when it comes to safety. More than any jazzy slogans or vision statements, however, true management commitment is about being a visible presence on the plant floor.
To understand why, put yourself in an operator’s shoes. What’s going to make you feel like your boss actually cares about you—yet another “Safety First” banner, or your manager asking you face-to-face about whether you have the tools to do your job safely? Clearly, it’s the latter.
Incorporating safety questions into layered process audits or conducting regular safety inspections is one way to make sure these conversations take place.
4. Do You Prioritize Safety Over Production?
People often treat safety as an obstacle to productivity, but it should never come second to getting orders out the door. If it comes down to doing something fast or doing something right, doing it right should always take precedence.
Some additional questions to ask to determine whether safety is truly a priority in your plant include:
- Do workers take shortcuts, or do they follow work instructions and job safety analysis (JSA) procedures?
- Do people feel comfortable stopping production if they notice something unsafe?
- Do employees seem hesitant when pointing out safety problems?
5. Are Safety Issues Corrected Quickly?
Whether and how quickly hazards are addressed is a telling indicator of the state of safety in your plant.
If you have a large backlog of safety-related corrective actions, you’re obviously leaving the door open to injuries. Just as important, however, is the message that this sends to your workforce.
The reality is that people pay more attention to what you do than what you say. You may have well-developed safety objectives and training programs, but if you don’t quickly deal with reported hazards, your credibility is shot.
Think of it from the operator’s perspective. How serious would you think management is about safety if a broken machine guard goes unfixed for three months?
Again, this is an area where daily safety inspections can make a big difference, providing opportunities to identify problems and for operators to share feedback about unsafe conditions. Mobile audit and inspection software like EASE also gives you an advantage in terms of closing the loop on problems identified during inspections, so they don’t lead to safety incidents.
Discussions of safety culture often focus on vision and management commitment. And while these are important parts of creating a culture of safety, what’s actually happening on the plant floor can tell you so much more. The questions here can help you look deeper, going beyond the surface to see how your plant’s safety culture truly measures up.