A3 Problem Solving Using A3 Report Templates
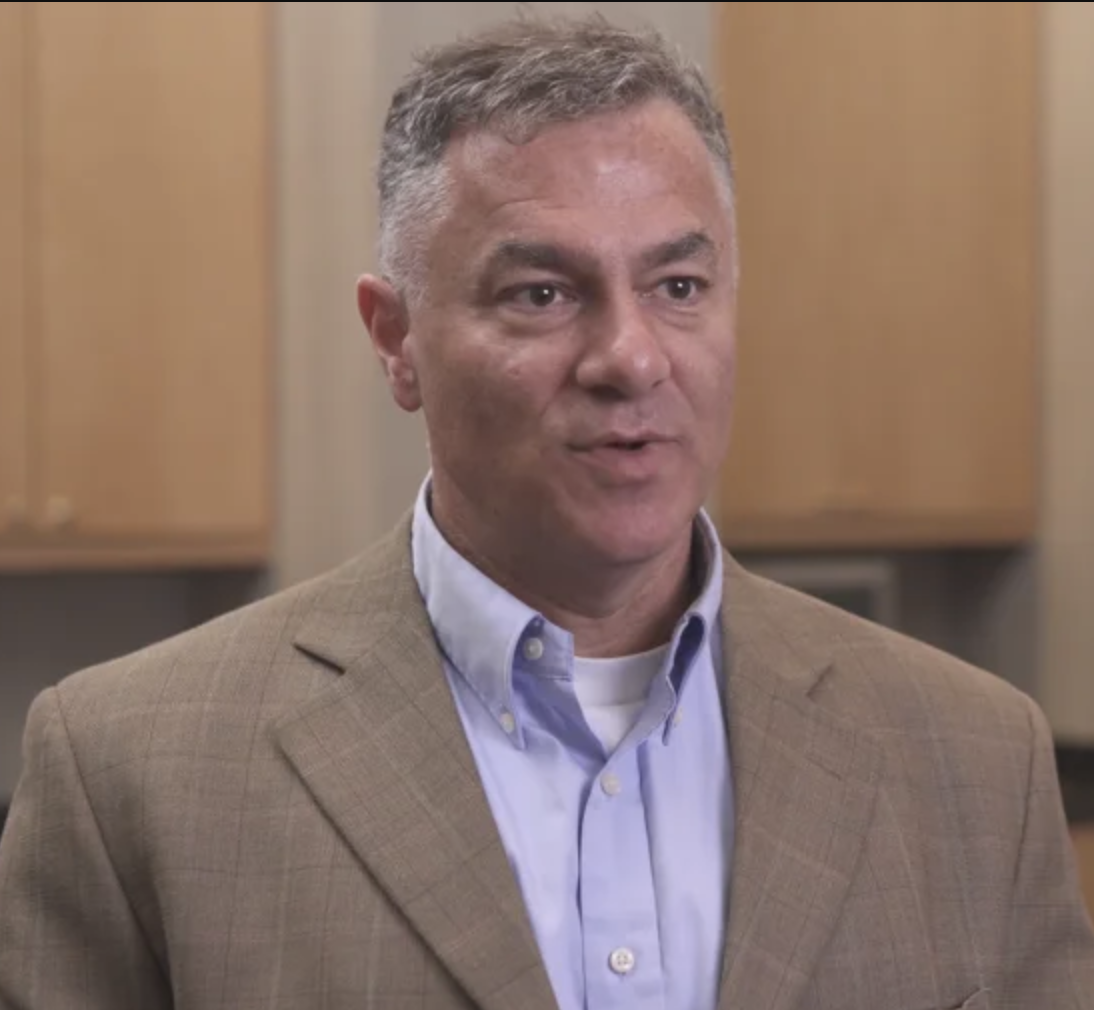
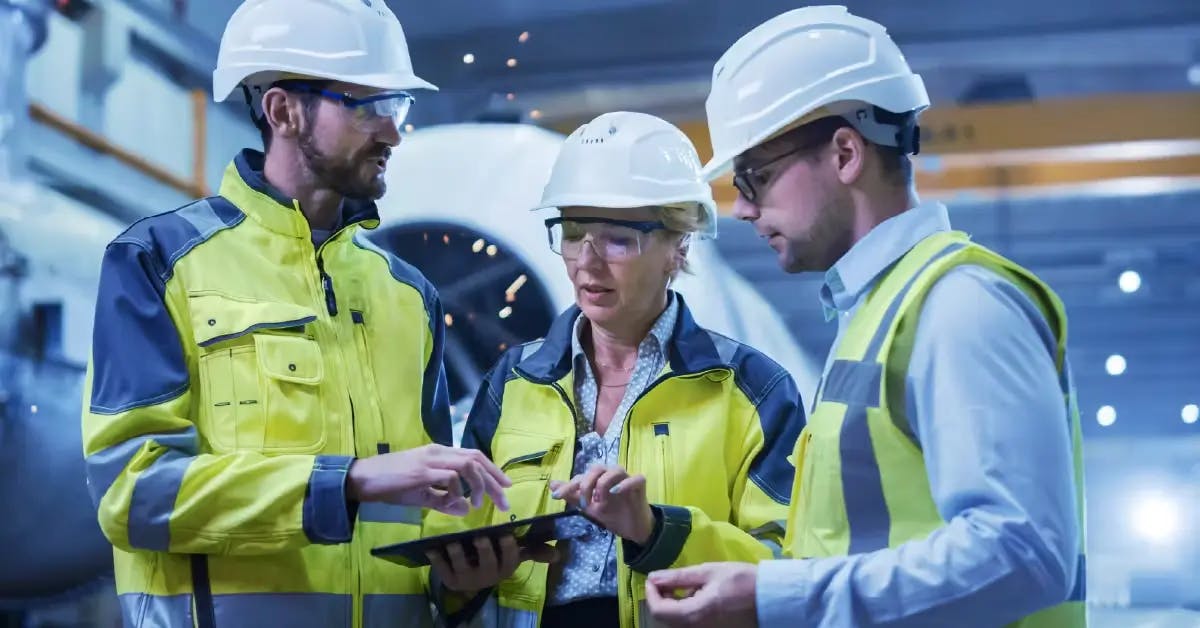
A3 reports are prevalent in many manufacturing organizations, giving teams a way to quickly understand the nature and current status of problems affecting their plant.
But how do these reports work, and what do teams need to know to get the most from them?
In this article, we explore the basics of A3 report templates, including how they’re structured, pitfalls to avoid and key ingredients for success.
What Is an A3 Report?
An A3 report is a Toyota Production System tool for communicating the results of the problem-solving process. Named for the A3 size paper used in this process, A3 reports are a way to document Plan-Do-Check-Act (PDCA) thinking on a single page of paper.
Download Our A3 Report Template
A3 Report Template Structure
The A3 report has a structure similar to 8D problem-solving or DMAIC (define, measure, analyze, improve, control) tools. Diagrams, pictures and process flow maps are heavily emphasized in A3 reports, for example before and after photos of a blemished vs. clean part surface.
While A3 report templates vary from one organization to the next, common sections may include:
- Theme or problem description: What is the problem you’re trying to solve? The A3 report should succinctly describe the problem in one or two sentences.
- Background: This section should include the context and significance of the problem, for example, any relevant customer complaints or photos of defective parts.
- Current state: Here you want to describe the current condition and how it’s contributing to the problem. Value-stream maps or process flow maps are often used to describe the current state, as well as any relevant quantitative data.
- Analysis and root cause identification: This section records the results of the root cause analysis process, for example including a Fishbone diagram or 5 Whys exercise.
- Target state: What is the goal of the problem-solving process? You should include quantitative goals where possible, as well as any relevant diagrams or photos of the desired condition.
- Action plan: This section documents proposed countermeasures and the implementation plan for achieving the target state. A proposed timeline is also essential for this section. It may also identify where else the action should be applied to leverage the learning throughout the organization.
- Follow-up actions: Here you want to document any follow-up actions needed such as process audits to verify conformance with new procedures. Also document any countermeasures not completed within the proposed timeline, as well as any problems identified during implementation. Finally, this section should record any results that have been achieved.
Using A3 Reports to Communicate Problem-Solving Efforts
At The Luminous Group, we emphasize that A3 reports aren’t a problem-solving tool in and of themselves. Rather, they help teams document the thinking process behind problem-solving. More importantly, the real power of an A3 lies in its power to communicate the status of problem-solving efforts—and any bottlenecks in the process.
One of the common uses of A3 reports in fast-response meetings for tracking problems at a plant. Teams may post A3s on flip charts or using a projector. Each team would come up to speak briefly on the status of individual problems currently being addressed and the progress they are making.
For instance, let’s say there’s an A3 team for broken tools. During the meeting, the team lead would point to how they’ve defined the problem including quantifying the problem’s effect on the plant on the A3. They would then go on to explain the solution that was jointly developed with the tool shop to build a thicker tool holder.
The next A3 might deal with paint contamination from fibre in the air. The A3 would document that a new guarding piece is being added to reduce the likelihood of the problem occurring again.
To extend the communication to the frontline workers, some facilities may also post the A3 in specific work areas so teams know what’s happening with a recent problem and what they should be paying attention to.
Pitfalls and Success Factors
In order for A3 reports to provide real value to the organization, two factors must be in place: regular updating and management involvement.
Teams must regularly review A3s and update them with any new information to keep them relevant. An obsolete or out-of-date A3 will only confuse people, which is why it’s important to look at every step in the process to determine if new information should be added.
Management must also be involved in the process of evaluating and communicating results. If an engineer fills out an A3 and nobody pays attention to it, you won’t get the desired input or result.
For instance, let’s say an A3 report identifies a moulding defect on the left bezel of a part. During the fast-response meeting, management should also ask whether the stock has been checked to see if the defect also exists on the right bezel. Determining where else the problem might occur is vital to leveraging the value of problem-solving and preventive action.
Finally, leadership plays a vital role in keeping the process on track, helping identify and resolve any bottlenecks slowing down the process. For example, the team may need support from subject matter experts (SMEs), more resources to collect data or cross-functional participation of the A3 team.
Using Plant Floor Audits to Support the A3 Process
Plant floor audits such as layered process audits (LPAs) support A3 reporting in several ways. (Read LPA best practices here)
For example, plant floor audit data can reveal background information on the frequency and location of process failures that cause defects. This information can drive the creation of an A3 team to address the root cause of the issue.
Plant floor audits are also essential for verifying countermeasures and recording follow-up. For instance, an A3 may result in a new LPA question to check that operators are following a new process to ensure finished part surfaces are clean and unblemished. An LPA platform like EASE can streamline this process, helping maximize the value provided by A3 reports. Furthermore, it provides documentation to customers on the effectiveness of the A3, building confidence and trust.
A3 reports communicate problem-solving at a glance, offering a structured format for describing the problem, its root cause, target state and action plans. However, organizations must realize that success or failure hinges on the A3 teams regularly updating the form, as well as management asking insightful questions and keeping action plans moving forward.
Plant floor audits, particularly LPAs, complement the A3 process by providing valuable background data, verifying countermeasures and ensuring effective follow-up. This synergy between plant floor audits and A3 reports ensures that companies can get the maximum value for the effort invested in A3 reports.