Boeing 737 Max 9 Issue Reveals Important Lessons on Quality Management
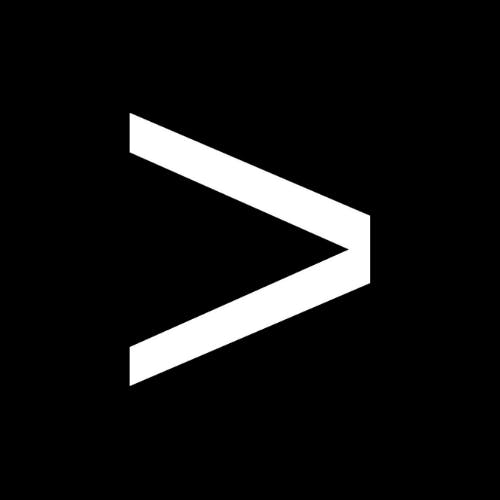
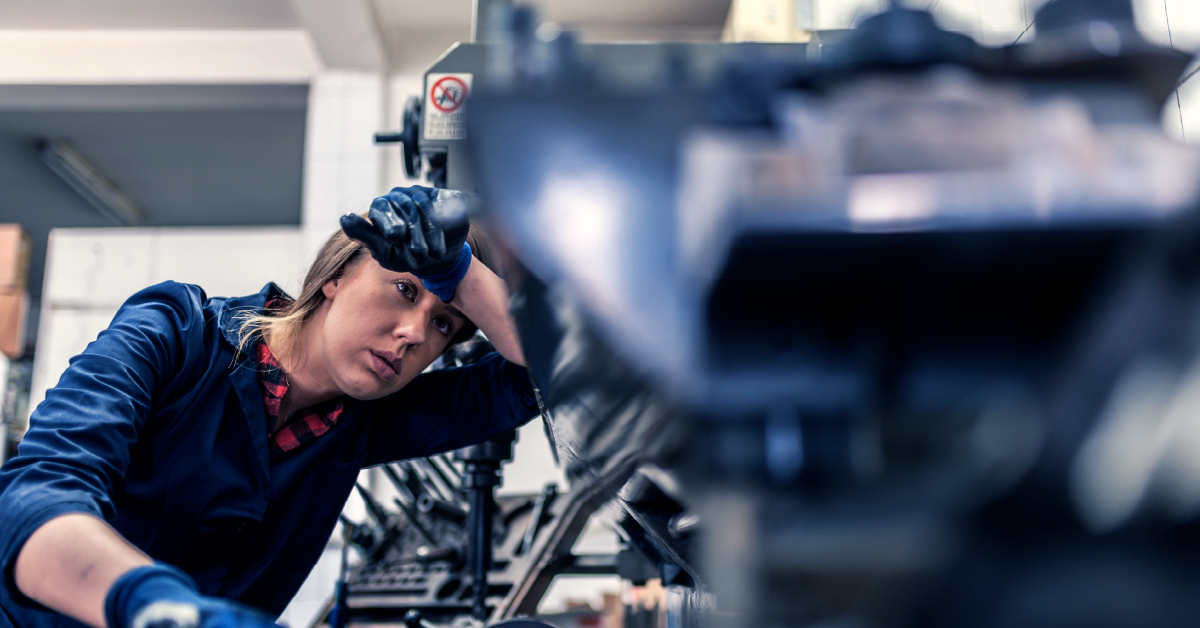
When a door plug blew off an Alaska Airlines 737 Max 9 in mid-flight in early January, the questions started flowing in.
How could this have happened? More importantly, what could have been done to prevent it?
The door plug in question is a piece of fuselage with a window affixed where an exit door might otherwise be on different configurations of the aircraft. Since the incident, United Airlines has identified several instances of 737 Max 9 door plugs with loose bolts.
While investigation into the incident is still ongoing, numerous issues with the 737 Max 9 underscore the importance of verification, both at the point of manufacture as well as design.
Download your free Root Cause Analysis 101 Guidebook to learn about when and how to use common root cause analysis tools
What We Know So Far
In the aftermath of the Alaska Airlines incident, the Federal Aviation Administration (FAA) grounded 171 other 737 Max 9s and has initiated an audit of the aircraft’s production line. The FAA has also signaled it will increase oversight of the manufacturer’s operations, potentially to include third-party quality inspections.
Boeing has announced it will deploy a team to the supplier that makes and installs the aircraft’s door plugs to investigate the problem, as well as check 50 additional points in the supplier’s production process. New checks are also being added to Boeing production lines, and the manufacturer announced it will open its facilities for customer inspection.
In a letter to employees, Boeing CEO Stan Deal said “These checks will provide one more layer of scrutiny on top of the thousands of inspections performed today across each 737 airplane, and build on the reviews we have implemented to catch potential non-conformances.”
Layer is the key word here—and a critical concept for truly reducing risk in the manufacturing process, as we’ll see.
The Importance of Layered Process Audits
The root cause of the Alaska Airlines incident and the loose bolts on other 737 Max door plugs has yet to be determined. Even so, the current nature of the investigation suggests this is something that could have potentially been caught at the point of manufacture.
“If bolts were missing or loose, that should have been controlled for,” says Murray Sittsamer, President of The Luminous Group, a manufacturing consulting and quality auditing firm.
He points to the importance of layered process audits (LPAs) in providing multiple layers of checks during production. For instance, in this case LPAs would involve multiple people in verifying key elements of the process, such as:
- Whether all bolts were present
- Whether bolts were torqued to the appropriate threshold
- Whether bolts were affixed correctly, and not cross-threaded
“The goal here is to prevent problems by removing opportunities for human error, such as someone omitting steps or not fastening bolts correctly,” he says.
He notes that while inspections and other detection activities are essential for identifying nonconformances, they also require additional layers of verification.
“If they were using a torque gun to verify the correct torque, for instance, how do you know that it’s calibrated correctly?” he says. Again, it’s an area where LPAs provide a critical backstop by ensuring the detection process itself is working.
“If anything is at risk, LPA is your safety net,” says Sittsamer.
Verification in the Design Process
Beyond just making sure parts are manufactured and assembled correctly, Sittsamer says that verification is also vital at the design stage. He points specifically to activities like design risk assessment and design failure mode and effects analysis (DFMEA), both of which help identify and control risk during design.
“These are engineering activities that can be done well, done poorly or skipped altogether,” says Sittsamer. He adds that having a separate set of eyes on the process is essential to verifying that they are performed correctly.
“Was a design risk analysis done? Were the right people on the team? Did they project all the failure modes, and therefore will the resulting design decrease risk?”
An Ounce of Prevention
According to Sittsamer, there are many factors that can contribute to problems like those Boeing is experiencing, for instance:
- Not having a verification strategy in place, including at the design stage
- Not conducting LPAs effectively, especially when relying on manual or pen-and-paper tracking systems
- Lack of leadership support for LPAs due to competing priorities
Whether or not these factors had anything to do with the 737 Max failures remains to be seen. One thing that’s clear, however, is that Boeing will have to throw a lot of money at the issue with new inspectors and verifications, while also facing added scrutiny from regulators.
The key takeaway for manufacturers: an ounce of prevention is worth a pound of cure.
Upfront investments in quality, for instance auditing your design processes or implementing digital LPA systems, pays dividends in the long run. In the end, your company’s future and reputation may depend on it.