How Connected Worker Platforms Create Engaged Employees
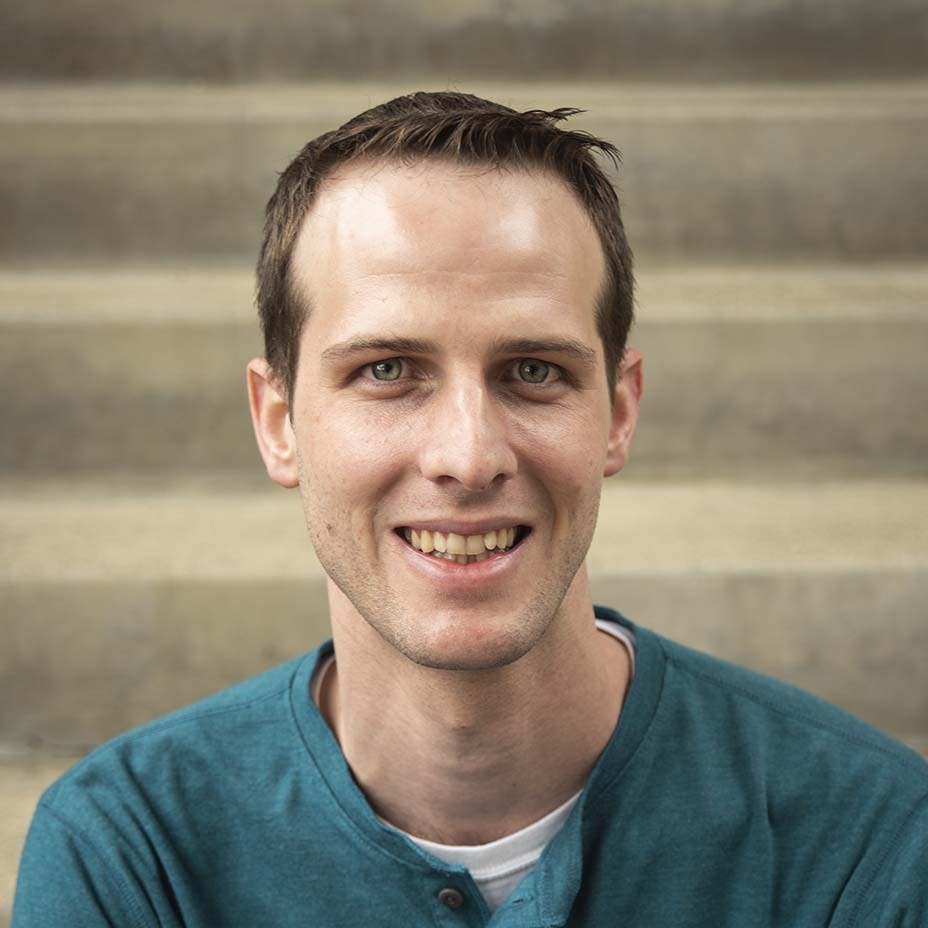
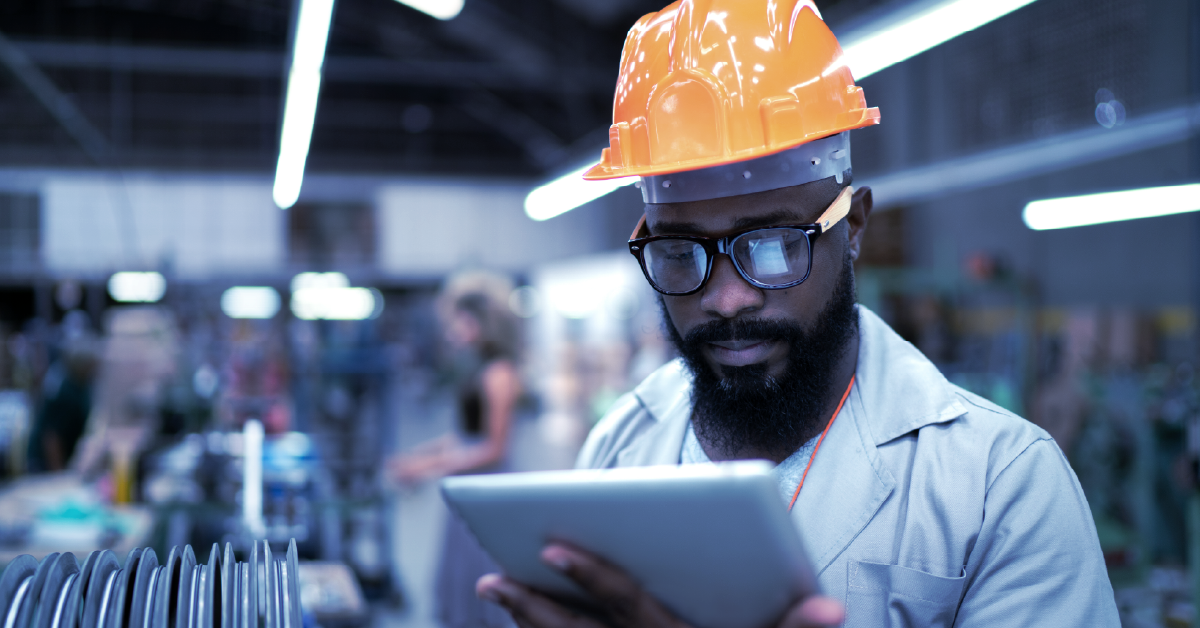
Employee engagement is a growing problem for companies today, with Gallup research showing the ratio of engaged to actively disengaged employees is at its lowest point in a decade.
In manufacturing, the employee engagement crisis has significant implications for quality, productivity, and safety—not to mention the bottom line. It’s one reason why connected worker solutions having been deployed by more than 25% of manufacturers (and growing), according to LNS Research.
A connected worker platform offers multiple avenues for boosting engagement, making workers feel valued while empowering them with greater control over quality and safety.
With that in mind, today we’re exploring the importance of employee engagement in manufacturing and how connected workforce solutions can help.
Learn about more Manufacturing Quality Trends to Watch in 2023
Employee Engagement and the Manufacturing Skills Shortage
National Association of Manufacturers survey data shows that attracting and retaining quality workers is a mission-critical priority for more than 75% of manufacturers today. The industry has over 780,000 open manufacturing jobs to fill, many of which are for frontline workers.
Organizations must also cope with the loss of institutional knowledge due to the Great Resignation and the fact that 2.6 million baby boomers will retire over the next decade.
Combined with falling engagement, having fewer skilled workers and more unfilled positions presents several risks to manufacturers:
- Productivity: When plants are short-staffed, it makes it harder to fill orders, ramp up production, and pursue new product development opportunities
- Quality: With manufacturing teams stretched thin—and pressured more than ever to meet production goals—people are more likely to cut corners, skip process steps, and miss key quality requirements.
- Safety: Having a larger proportion of newer workers means a greater risk of safety incidents, with new workers accounting for 35% of workplace injuries.
Problems with quality and safety also create a negative feedback loop that can further impact engagement and retention. Ongoing quality issues mean lower job satisfaction, while those who feel unsafe at work are more likely to leave. The result is increased employee turnover and costs and, not surprisingly, lower morale and engagement.
The Emergence of the Connected Worker
Connected worker technology presents a significant opportunity for employers to improve employee engagement while ensuring quality and safety. Connected worker platforms provide operators with digital tools to access key information, communicate with the team, and collaborate to solve problems more effectively.
Connected worker platforms encompass tools such as:
- Digital forms and checklists like mobile plant floor audit and inspection apps
- Guided procedure checklists and training programs tailored to each worker’s individual level of training
- Live engineering support for troubleshooting equipment issues or getting more resources at the workstation as needed
- Internet of Things (IoT) sensors and edge computing that provide real-time guidance to address and resolve machine issues
Benefits for Employee Engagement
For many manufacturers, implementing a connected worker platform is aimed at creating a more responsive manufacturing process that ensures quality and safety. A connected workforce is also by definition a more engaged workforce, which manufacturers are seeing play out in several ways.
First, it makes training an interactive experience, rather than one comprised of reviewing documents or computer modules. Procedure checklists can be targeted to the employee’s experience, for example providing a 10-step checklist for new workers versus a simple quality check for fully certified operators. Skills matrix tracking helps show who needs what training, offering employees opportunities to build new skills and move up in their careers.
Second, connected workforce solutions create a culture of engagement and accountability. What does this look like in practical terms?
- Showing employees they’re valued: Operators can communicate directly to raise issues, for instance if they need additional components or need an immediate answer about a machine issue. This makes employees feel heard and shows them management genuinely cares about them.
- Accountability: Automated notifications, reminders, and progress tracking help close the loop on issues. Workers are more likely to take ownership of problems they see when they know management won’t ignore them.
- Collaboration: Connected workforce tools help everyone work together on problems more efficiently and effectively. Frontline workers have access to remote experts, leadership, and others, enhancing their contribution to quality and safety.
- Employee buy-in: Improved accountability and follow-through shows management commitment to following standards. This in turn fosters greater respect for following standards among the entire team.
Engaging Workers with Digital Tools
More and more, digital transformation is becoming an important driver for meeting the challenges of the manufacturing worker shortage. The next generation of frontline workers, which represent the majority of unfilled positions, are digital natives. That means they grew up with technology and see it as a basic expectation in any place they work.
Technology also helps support older workers, giving them targeted support for greater flexibility in staffing different workstations and processes. Critical to success are using intuitive tools that actually make people’s jobs easier and putting in the work on the planning side to ensure a streamlined deployment.
Ultimately, a connected workforce helps move beyond a siloed approach in manufacturing. When people are engaged in what they are doing—and with each other—you build a greater sense of teamwork in creating a culture of excellence together.