How Layered Process Audits Support the APQP Process
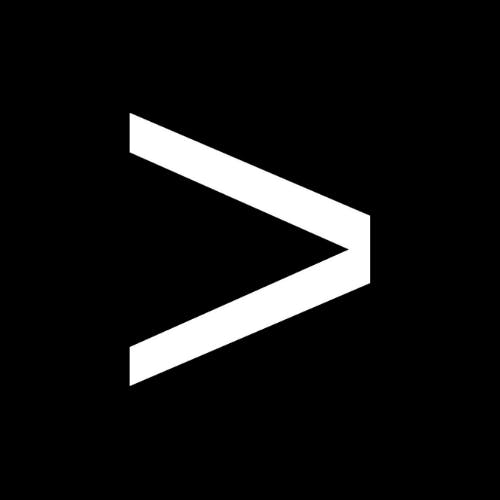
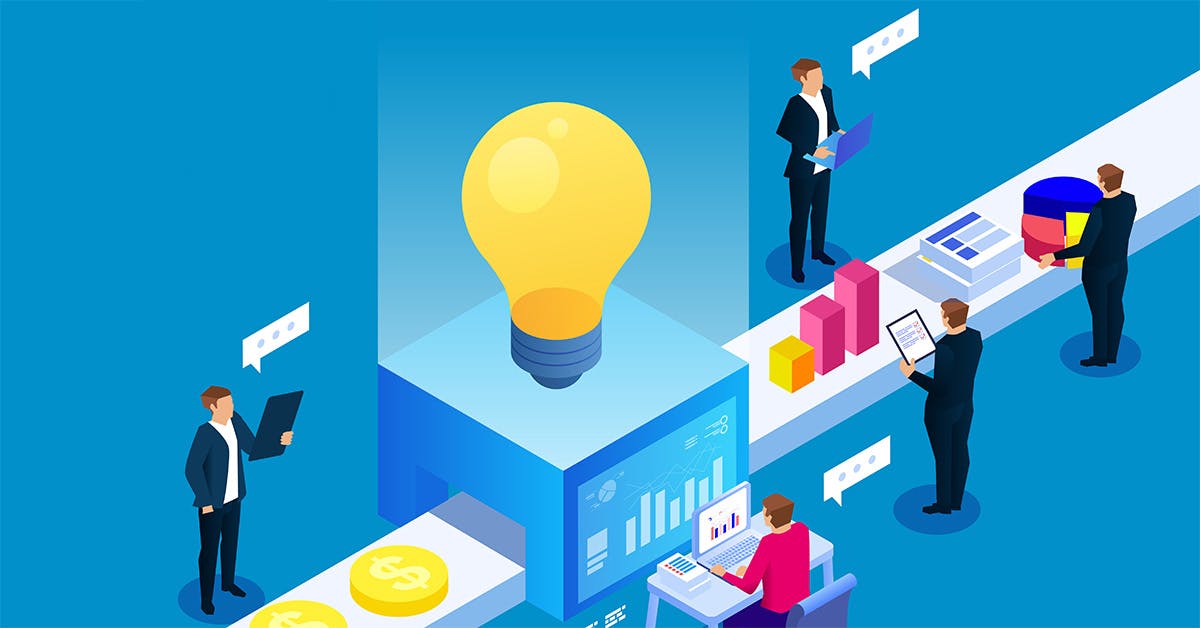
Most people think of layered process audits (LPAs) in terms of preventing production defects through daily checks of plant floor processes.
However, manufacturers can use LPAs to verify a wide range of quality processes, including advanced product quality planning (APQP).
To learn more, we spoke with Ali Rizwan, Director of Quality at Continental. Rizwan recommends developing a checklist of questions from each phase of the APQP process, then cross-checking the questions with an LPA to identify and prevent potential quality problems.
Below you’ll find ideas and starter questions to ask across every stage of the APQP process, from pre-planning through production and continuous improvement.
Find out how reduce costs and complaints using LPAs with our free Ultimate Guide to Layered Process Audits
What is APQP?
Advanced product quality planning (APQP) is a systematic approach to ensuring manufacturing quality from start to finish. APQP covers six distinct phases:
- Phase 0: Pre-Planning
- Phase 1: Planning
- Phase 2: Product design and development
- Phase 3: Process design and development
- Phase 4: Product and process validation
- Phase 5: Production and continuous improvement
Phase 0: Pre-Planning
Developing LPA checklists from the APQP process should start with items such as the request for quotation (RFQ), customer contract and voice of the customer (VOC).
“It’s like when you buy a house and you sign the papers without reading all 500 pages,” says Rizwan. “In manufacturing, if you don’t read paperwork carefully, the customer may come back to you with penalties for not meeting customer-specific requirements in areas like safety, engineering, design quality flaws and on-time delivery.”
LPA questions you might ask here include:
- Have you reviewed VOC information such as customer expectations and preferences?
- Have you checked your database of previous quality issues?
- Have you benchmarked your competition?
- If your price is higher, what makes your product unique to justify it?
Phase 1: Planning
Rizwan says LPA questions from phase 1 of the APQP process should focus on areas such as suppliers, materials, building your team and product reliability.
“If your product isn’t reliable, you end up with recalls and lose money,” he says. “People don’t typically think about all of this up front.”
Here you’ll want to consider creating LPA questions such as:
- Are you using the right drawings?
- Does your product meet reliability standards?
- Do you have all the right suppliers and materials?
- Do your interview questions ensure you have the right team?
Phase 2: Product Design and Development
Phase 2 of the APQP process is about ensuring you consider all aspects of product design. Here you’ll want to develop LPA questions from planning tools such as Failure mode and effects analysis (FMEA) and design failure mode and effects analysis (DFMEA).
“If you have the right DFMEA, assembly will be right,” says Rizwan. “If you have the wrong design, your assembly and process will have a problem.”
Examples of LPA questions to use in this phase include:
- Have you identified failures that could happen, and are controls in place to prevent them?
- Have you considered more than one vendor in case your primary supplier can’t deliver?
- Has the product design been translated into a standardized process?
- Do you have the right tooling for the process?
- Has the customer portal been checked daily for any design changes from the customer?
- Do material specifications match customer requirements?
Phase 3: Process Design and Development
This phase leverages tools such as process failure mode and effects analysis (PFMEA), focusing on quality system checks. Rizwan uses the example of a new customer visiting your plant.
“If you’re doing a presentation, you need to make sure you’ve done an LPA on that presentation, because whatever you’re telling them has to match what they see on the tour,” he says. “Otherwise, your integrity is shot.”
Here you might ask LPA questions such as:
- Is the layout of the plant represented correctly?
- Does your PFMEA incorporate critical-to-quality product characteristics?
- Have you done an LPA on packaging standards?
- Have you done a dry run to test your processes prior to validation?
- Have regulatory requirements been incorporated into your system?
Phase 4: Product and Process Validation
Rizwan emphasizes that at this phase, companies should be doing an LPA on every significant product run.
“If the truck is waiting at 3:30 to pick up 100 pieces, you’d better be ready,” he says. “If you only make 80, that means flying the other 20 to the customer. That’s how you lose money.”
LPA questions to consider creating from this phase include:
- Is your process under control?
- Do you have an LPA for process capability?
- Is the process validation done right?
- Have you met all customer-specific requirements?
Phase 5: Production and Continuous Improvement
According to Rizwan, this phase is all about asking whether your process went as expected and applying lessons learned.
Questions to cross-check here should include items such as:
- Did you experience any unexpected variation in the APQP process?
- Did the material arrive in time from the supplier?
- Did you have any problems with specific processes, such as maintenance or packaging?
In the end, says Rizwan, conducting an LPA on your APQP process is all about implementing checks and balances in order to keep customers happy and streamline production.
“Are you checking all the requirements? How do you know it’s been checked,” he says manufacturers must ask themselves. “This is how you avoid delays common in APQP.”