How LPAs Help Manufacturers Ace External Audits
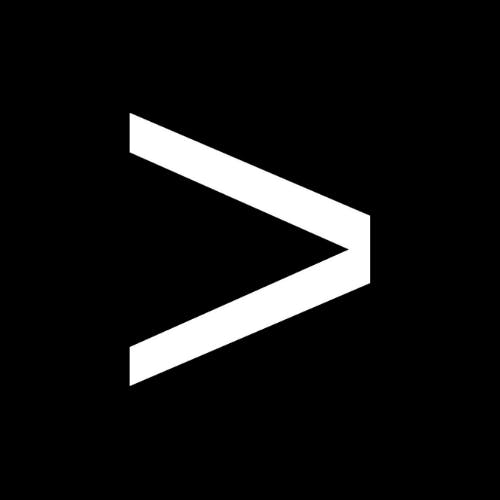
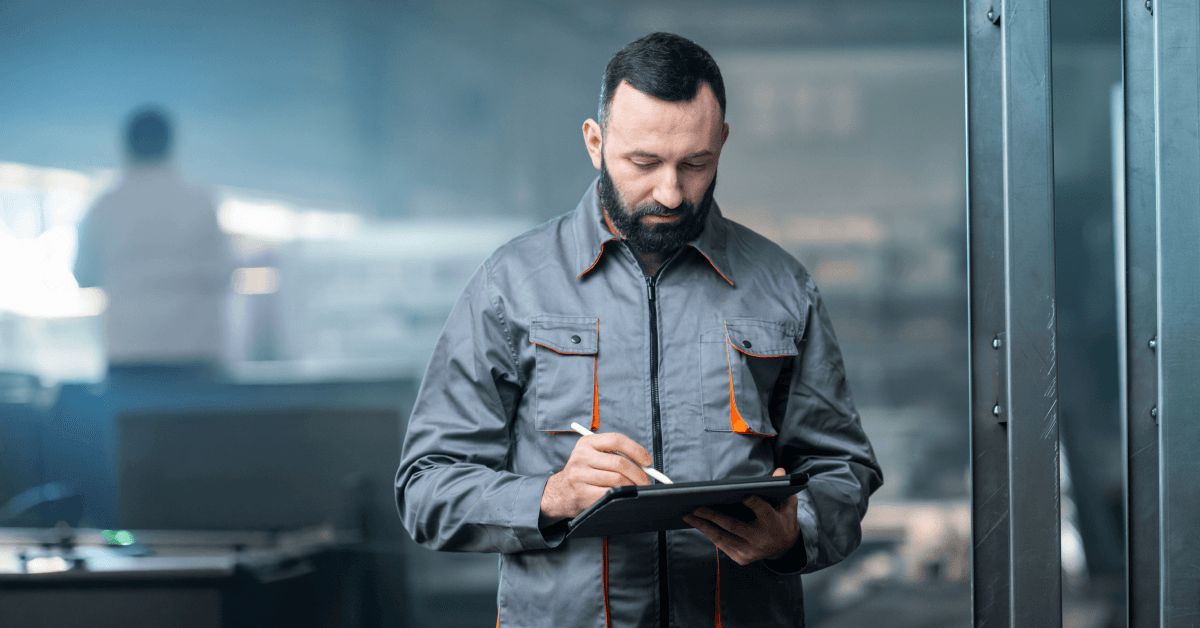
Manufacturers face a complex web of regulations, standards, and certification requirements, and external audits are essential for ensuring compliance. While plant floor audits serve as the foundation for ongoing operational excellence, they also help make sure you’re ready for external audits in manufacturing.
Here, we explore how plant floor audits prepare you for external ones, and why they’re necessary for maintaining robust quality management and regulatory compliance in manufacturing.
External Audits vs Plant Floor Audits in Manufacturing
External audits in manufacturing are formal evaluations conducted by independent third parties to verify compliance with specific standards or regulations. Common ones include:
- ISO 9001 certification audits, which assess a company’s overall quality management system including process control, customer satisfaction, leadership commitment, and continuous improvement practices. These audits verify that manufacturers have systematic approaches to maintaining quality across all operations.
- In automotive manufacturing, IATF 16949 certification requires regular external audits of quality management systems to maintain certification.
- Aerospace manufacturers must undergo AS9100 audits, which examine areas like product safety, reliability, counterfeit part prevention, and design controls that are critical in aerospace manufacturing.
In an external audit, the third-party auditor follows a structured process that includes collecting facts and evidence through document reviews, employee interviews, and direct observation of processes and facilities.
Plant floor audits, which are conducted internally, are exactly that: Inspections developed and implemented by manufacturers themselves. Within operations and production specifically, many plant floor audits focus on making sure specific standards are met and processes are followed. This is critical for obvious reasons — to ensure quality and safety, but also to optimize productivity, reduce waste, and increase customer satisfaction.
Layered process audits (LPAs) are a particularly effective type of plant floor audit. LPAs distinguish themselves by creating multiple verification layers with high-frequency checks. This approach ensures repeated and comprehensive process verification, from frontline operators to top management, providing a more detailed, accurate view of compliance and performance.
Learn more about layered process audits with our free LPAs 101 eBook
How Plant Floor Audits Prepare Organizations for External Auditing Success
Given the rigor and systematic nature of external audits, manufacturers need a robust internal program to ensure they’re consistently ready for third-party evaluation. Plant floor audits, particularly LPAs, ensure documentation is well-organized, help teams become comfortable with the audit process, and create a clear trail of monitoring and improvement activities that external auditors can easily follow.
Finding and Correcting Issues Early
Plant floor audits create a systematic approach to identifying and addressing nonconformities, including before external auditors arrive. LPAs are especially effective here, as their high frequency and multi-level verification process helps catch issues quickly. For example, while an operator’s daily LPA might identify a process deviation, a team lead’s weekly audit could verify that corrective actions are being properly implemented. This proactive, multi-level approach reduces the risk of an external auditor finding the deviation, or that the corrective action had failure points.
Team Training and Collaboration
High-frequency plant floor audits, like LPAs, familiarize both operators and management with general audit processes and requirements. When team members regularly participate in them, they become more comfortable discussing processes, showing documentation, and explaining procedures to the person performing the audit. This experience proves invaluable during external audits, where confidence and clear communication are essential.
Documentation Management
One of the most important aspects of external audit success is having well-organized, up-to-date documentation. LPAs and other types of plant floor audits help ensure that standard operating procedures (SOPs), training records, and other critical documents are:
- Current and accurate
- Easily accessible
- Consistently followed
- Properly maintained
- Regularly reviewed and updated
Data-driven Insights
Plant floor audits generate valuable data that provides context for external auditors. The frequent cadence of LPAs generates particularly rich data sets that can reveal trends over time. LPAs can capture the full story of issues identified and corrective actions taken by the company: the who, what, when, where, why, how, and more. As highlighted in the ISO 9001 principles, evidence-based decision-making is crucial for effective quality management. Internal audit data supports this approach by providing concrete evidence of monitoring and improvement activities.
Building a Culture of Excellence
Perhaps most importantly, regular plant floor audits help create a culture of quality and continuous improvement. LPAs strengthen this culture by engaging everyone from operators to executives in the audit process. When team members at all levels regularly participate in these layered checks, quality becomes everyone’s responsibility rather than simply a departmental function.
Rather than treating audits as periodic events to “pass,” organizations with robust audit programs make quality, safety, and compliance part of their daily operations. This aligns nicely with modern standards like ISO 45001, which emphasizes the integration of occupational health safety management systems into everyday processes, rather than treating it as a separate function.
The Digital Advantage in Audit Management
Digital tools have transformed how companies manage both internal and external audits in manufacturing. Gone are the days of shuffling through paper files and Excel spreadsheets — digital platforms have streamlined the entire audit process, making it more efficient and effective than ever before.
For example, when external auditors request records or other documentation, teams can quickly retrieve the needed information with just a few clicks. This eliminates the traditional scramble through filing cabinets and reduces the stress and time traditionally associated with audit preparation.
Other benefits of having a digital solution include:
Real-time Monitoring
Real-time monitoring capabilities also have transformed how manufacturers track and manage audit findings. Quality teams can now track issues and corrective actions as they happen, ensuring nothing falls through the cracks. This immediate visibility not only helps teams address issues more quickly, but also provides clear evidence of follow-through when external auditors come calling.
Advanced Analytics
Advanced analytics have added another dimension to audit management. Manufacturers can now easily identify trends and patterns in their audit data, allowing them to focus on improving areas that will have the most impact. This data-driven approach helps quality teams demonstrate the effectiveness of programs and provides valuable context for external auditors about ongoing improvement initiatives.
Improved Collaboration and Visibility
With mobile-friendly digital tools, team members can now conduct audits where the work happens, documenting findings and observations in real-time. This increased accessibility has led to more consistent audits and better participation across all levels of the organization, creating a more robust quality management system overall.
Ultimately, a robust plant floor audit program, supported by digital tools, does more than just prepare for external audits in manufacturing. It drives continuous improvement, enhances operational efficiency, and helps build a sustainable culture of quality and safety. By investing in internal audit processes and supporting technologies, manufacturers can turn what might otherwise be a stressful compliance exercise into a valuable tool for operational excellence.