Information Overload: What Do Operators Really Need?
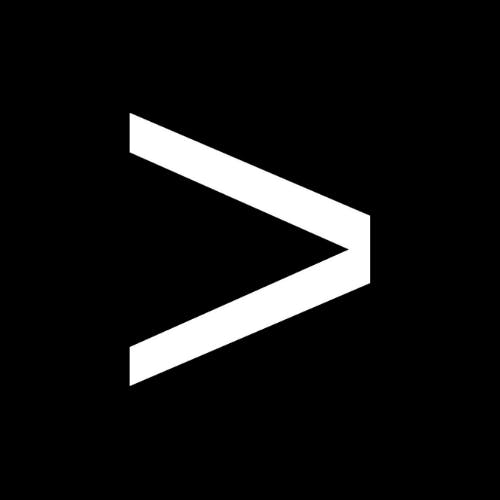
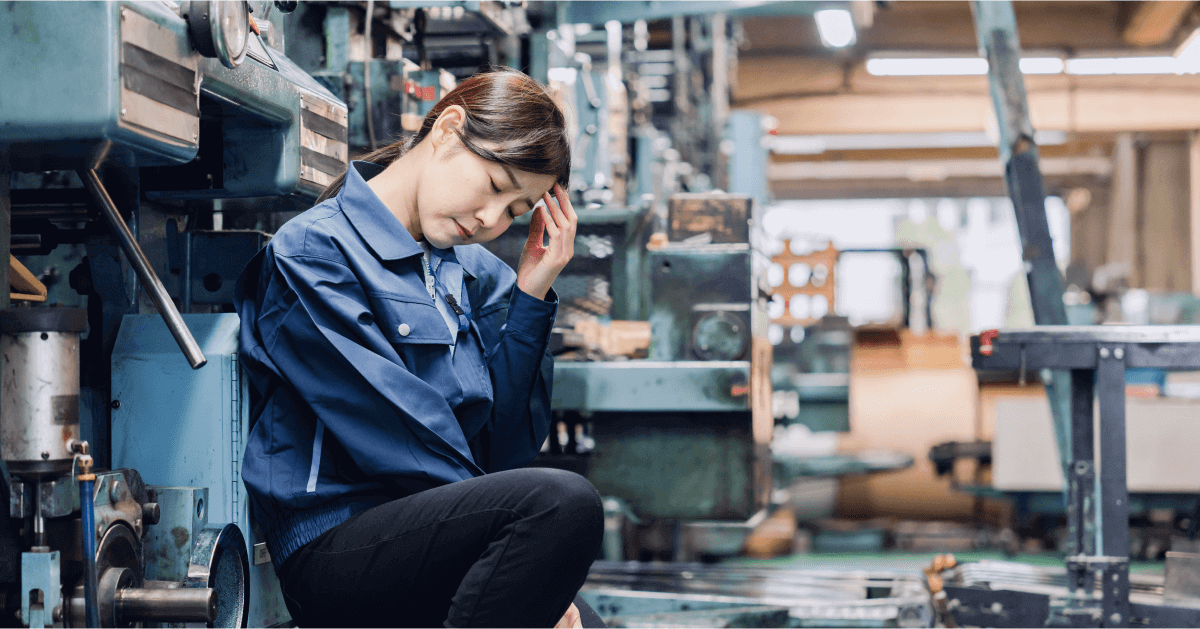
The likelihood of important information getting lost in your inbox is directly proportional to the overall number of messages received.
The same is true for operators on the plant floor faced with a constant stream of information, resulting in cognitive overload and missed opportunities for improvement.
If you’re an operator, your job is to build things right, not wade through a sea of documents, alerts, and training modules that teach you what you already know. The unfortunate reality is that this onslaught of information — which is meant to help — only ends up burying critical information under a pile of noise.
As for how manufacturers can cut through the clutter, it all comes down to asking one question: What information actually helps operators perform at their best?
Learn how to improve efficiency on the plant floor with our free eBook on The 5S of Lean Manufacturing Principles
Information Overload on the Plant Floor
Management often assumes that more information equals better performance. Ask operators, however, and they’ll tell you they’re drowning in information, most of which is redundant.
Examples include:
- Flashing the same quality alert on a screen every time a product comes into the workstation
- Mandating computer-based refresher training for skills already mastered
- Requiring the operator to check off the same 10 process steps on a connected worker platform to move a part that hasn’t changed in months
Imagine the perspective of the operator in that last example above. At the beginning of the shift, seeing each step on the screen can provide a helpful reminder. By the second hour of the shift, however, the operator is advancing through all 10 screens at once without reading them.
At that point, the information becomes less than useless; it actually becomes a risk because the operator isn’t paying attention to it at all. This is what’s most dangerous about information overload: It makes people tune out, and the information they truly need to know is lost in the clutter.
Think Quality, not Quantity
Operators don’t need more information. What they need is the right information, delivered at the right time. Let’s look at a few examples to illustrate what this looks like in practice.
Quality Alerts
Instead of blasting the same quality alert all shift long, try requiring a single confirmation at the start of the shift.
You can reinforce the message with a simple one-point lesson or quick huddle at the beginning of the shift, rather than posting information that will quickly get ignored.
Connected Worker Systems
Not all tasks need detailed instructions every time, so consider adjusting on-screen guidance based on task frequency and operator experience. Whereas low-frequency tasks may require detailed instructions, high-frequency tasks may only require a reminder of critical steps or a final quality check.
If the operator really needs to know something, consider requiring verification in terms of a measurement or photo to actually prove that the operator executed the task correctly.
Let’s say, for instance, the operator is supposed to affix three screws to a torque of 12 in order to attach a wire harness correctly during an assembly process. If it’s that important, the system shouldn’t advance to the next screen until the operator records the torque measurement.
Digital Process Verification
Implementing a system of quick, frequent process checks such as layered process audits provides targeted reinforcement of vital information. The result is less variation in the process, fewer defects, and higher productivity overall.
Digital audit tools make it easy to identify skills gaps, standardize procedures, and boost accountability — without the paperwork.
On-the-job Training Support
While traditional employee training via learning management system (LMS) has its place, it’s not where learning sticks. It’s one reason why it’s so common for manufacturers to identify training gaps as the root cause of problems.
Digital on-the-job training tools can help improve retention by providing targeted information where operators need it most: at the point of work.
This can be as simple as a quick video of a procedure, a one-point lesson, or a more detailed review of key standard operating procedures (SOPs) with an assessment at the end. In addition to reinforcing key information, this approach creates a closed-loop system that links training-related audit findings to corrective actions (and the documentation to back it up).
More information doesn’t drive better performance. In many cases, it only breeds disengagement and undermines quality. If your digital tools aren’t helping operators cut through the clutter, they’re working against you.
The solution is less noise and more signal. Focus on delivering timely, relevant, and actionable information, so operators can focus on what matters most: doing the job right the first time.