Q&A: Casper Zublin Talks Industry 4.0 and Creating a Culture of Quality
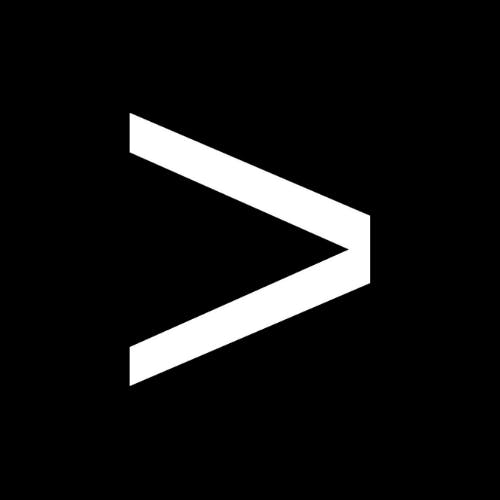
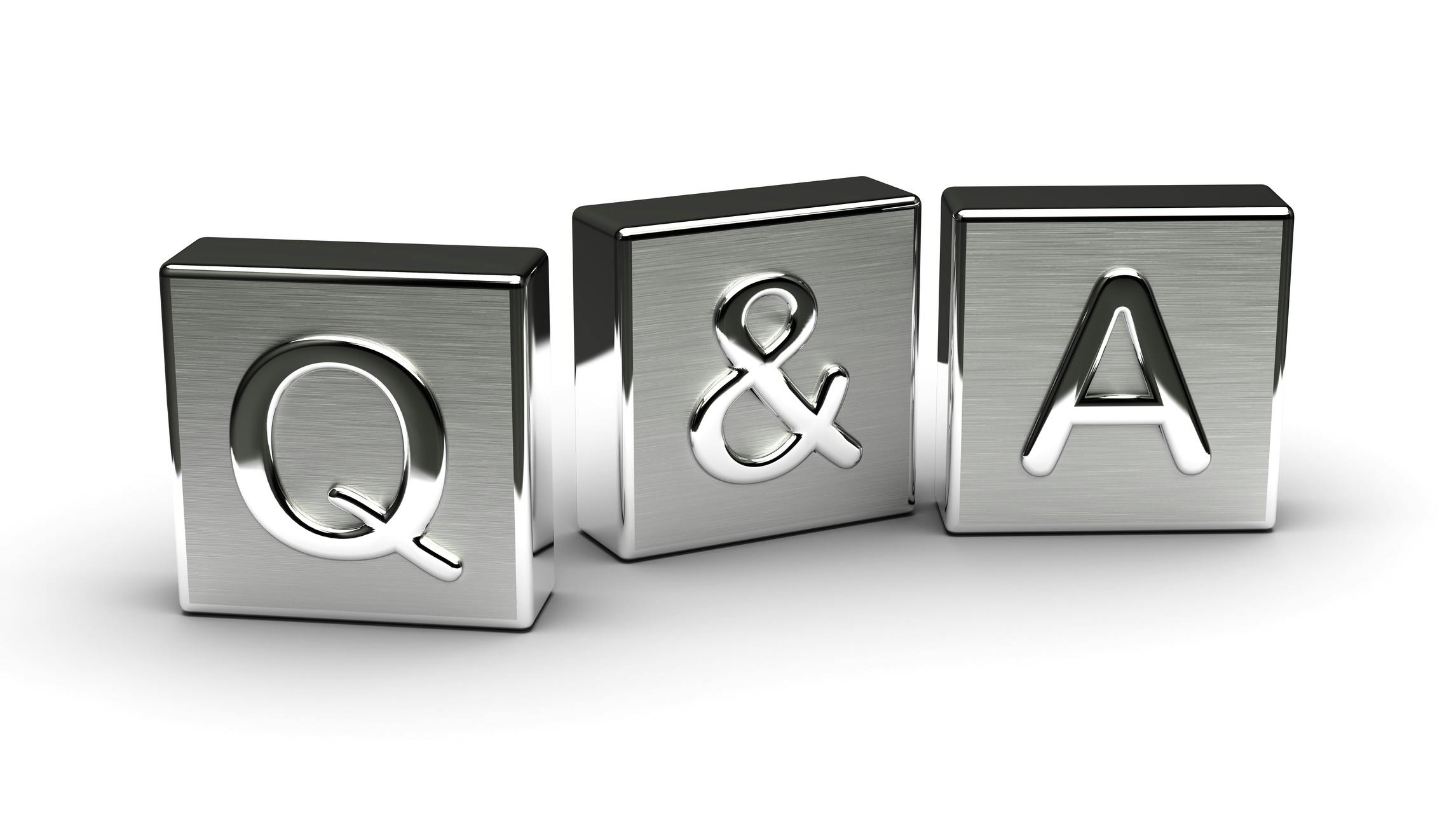
In our new Q&A column, we’re interviewing top manufacturing experts about industry trends and solutions to common quality challenges.
We recently talked with Casper Zublin, president of International Rubber Products (IRP), about rising quality expectations, Industry 4.0 and how to build a culture of quality. IRP’s three divisions manufacture liquid silicone rubber for medical device components (IRP Medical), precision rubber rollers (ABBA Roller) and elastomer components for aerospace and defense (MikronPMP Aerospace).
Q: What are the biggest challenges to manufacturing quality today?
Zublin: Every manufacturer would probably answer that a little differently. In my industry, there’s a rising degree of complexity. There’s also a rising degree of expectation from customers. Between the two, the demand to be better has never felt so urgent.
And I would tell you it’s not just critical devices anymore. I’d say the general expectation is 100% on-time and 100% perfect. It’s an enormously difficult task.
It’s not hard to make a few perfect parts. It’s not hard to ship a few parts on time. But when you start dealing with large assemblies, multiple supply chains and a cascading series of dependencies, there are so many steps that you have to become great at process. The challenge is that there are very few people in most organizations that understand the whole process.
Q: What’s your advice for companies that want to harness Industry 4.0 technologies but are overwhelmed about where to start?
Zublin: You just dive in. It’s definitely a jump into the deep end, but that’s how you learn. You can spend a lot of time strategizing where and how, but the important thing is just to start, because you’ll adjust.
What you have to do is commit to putting a stake in the ground and go from there. I don’t know if I’ve seen a process digitalization project go right the first time. We’re always adjusting and learning from that first effort.
Q: What kinds of obstacles have you run into, and how can companies overcome them?
Zublin: The obstacles aren’t so much physical in terms of a piece of software or equipment. It’s more overcoming the mindset of not wanting to make an investment that becomes a boat anchor in the plant.
You have to be willing to try and even fail, and then keep going. You have to be willing to say, “Let’s try this. What can we learn from it? How can we adjust?”
Q: I know that you’re a proponent of leveraging consultants to help with important initiatives, like when your organization partnered with the Toyota Production Systems Support Center [TSSC]. How do organizations know when it’s time to work with consultants?
Zublin: You call in experts when you’ve concluded that others are doing something better than you are, you need to change and you don’t know how to get there. The challenge is, it’s really easy to call in the wrong people.
As for how you bring in the right consultants, I have a mastermind group of other manufacturing CEOs that I meet with on a quarterly basis. Hearing how they solved their problems, what worked and what didn’t has been really helpful. That’s how we found TSSC.
Q: How can organizations balance the need to both improve quality while meeting rising production demands?
Zublin: I don’t think it’s a balance. I think it’s a choice. Either you say you’re going to be a zero-defect organization and you live it, or you say you’re going to be production-focused and there’s a certain level of bad quality you’re willing to live with.
If you’re serving a market that doesn’t tolerate bad quality, you have to create a process that yields great quality. And that means if you have to stop production, you stop production. You make the commitment to process improvement and uncovering the root cause of problems. Culturally, everybody knows that’s where we stand and that’s how we fight.
Q: How can leadership influence quality culture?
Zublin: Ultimately it doesn’t matter what the executive suite says, and you have to recognize that the business isn’t in spreadsheets or the enterprise resource planning (ERP) system. There’s only one truth, and that truth is what’s happening on the plant floor.
To influence quality culture, you have to stay connected with the plant floor. You have to observe and make sure, from a policy and process perspective, that you are dealing with plant floor truth.