Profiles in Quality: W. Edwards Deming
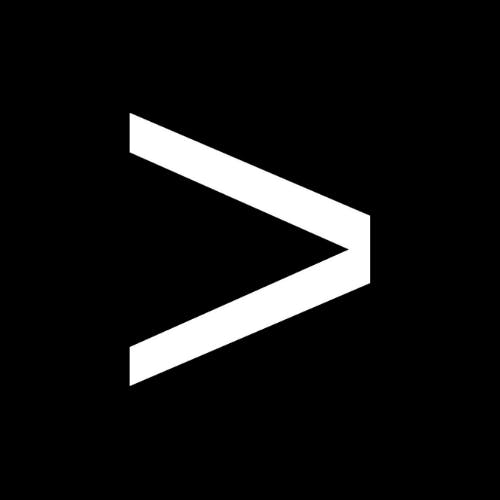
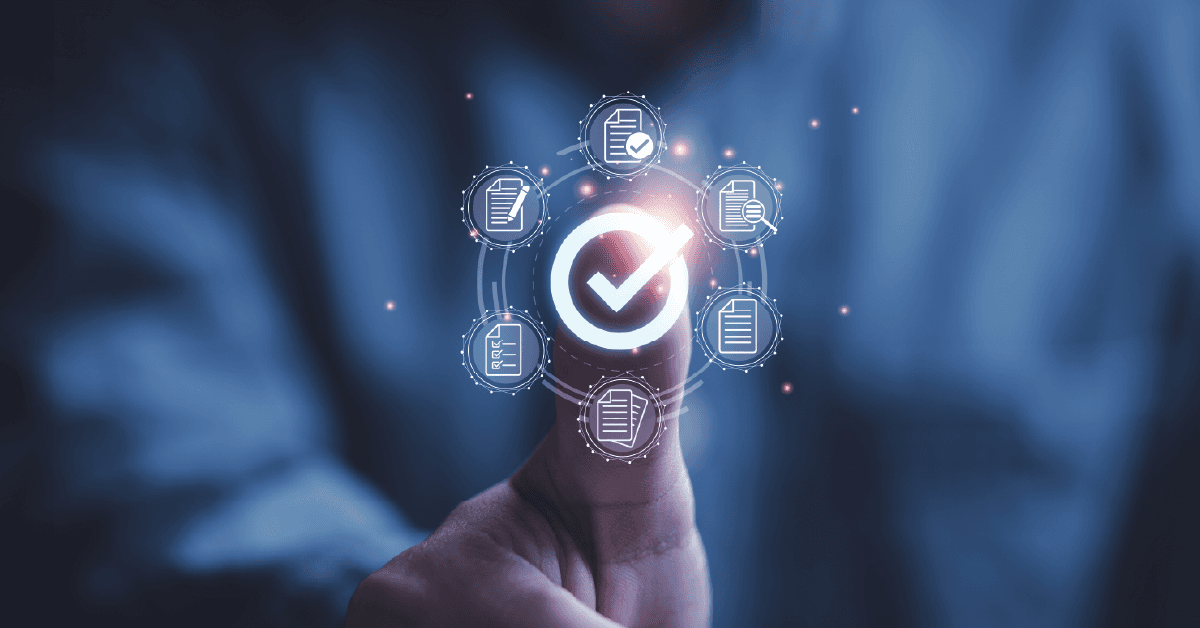
In the field of quality management, few historical figures command the stature of W. Edwards Deming.
Considered by many to be the founding father of quality management, Deming came from humble beginnings, establishing a philosophy unique to the time that would revolutionize the post-World War II manufacturing world.
Today’s article, the first in a series of profiles on quality leaders, explores the background and philosophy of Deming, and how his work still resonates in manufacturing today.
Download a Root Cause Analysis 101 Guidebook for a breakdown of the 5 most common root cause analysis tools
The Seeds of Change
Deming was born in 1900 in Sioux City, Iowa, spending several years of his childhood living on farms in Iowa and Wyoming. His humble beginnings undoubtedly shaped his views on quality, particularly through the lens of eliminating waste.
In 1921, Deming received a bachelor’s degree in electrical engineering from the University of Wyoming before earning a master’s in mathematics and physics from the University of Colorado. From there, he went to Yale, where he earned a doctorate in mathematical physics in 1928.
What first set him on the course of transforming manufacturing were the summers he spent in 1925-1926 working at the Western Electric Hawthorne Plant in Chicago. It was there he became aware of the need for uniformity in telephone equipment, and where he first learned of Walter Shewhart of Bell Laboratories. At the time, Shewhart was exploring the use of statistics to control process variation—a concept that would later become central to Deming’s quality approach.
Applying Statistics to Quality Control
After his doctorate, Deming spent 12 years with the U.S. Department of Agriculture (USDA) as a mathematical physicist. While there, he invited Shewhart to deliver a series of lectures to the USDA graduate school. Deming then joined the U.S. Census Bureau in 1939, first applying statistical sampling techniques during the 1940 census to identify census workers needing more training.
In 1942, he joined the World War II war effort in conducting a series of courses in applied statistics at Stanford. This resulted in significant reductions in scrap and rework for wartime manufacturing, with Shewhart’s Plan-Do-Check-Act cycle and statistical process control charts playing a key role.
Taught to thousands of people, these courses laid the foundation of the quality control movement in the United States.
Impact on Japanese Industry
After World War II, the U.S. War Department sent Deming to Japan to help with a census aimed at understanding reconstruction needs in the war-ravaged country. It was there he first connected with Japanese culture and developed contacts with Japanese statisticians.
At the time, Japanese products were considered inferior compared with the rest of the world, and the country could ill afford to waste raw materials as a result of poor quality. These problems led the Union of Japanese Scientists and Engineers (JUSE) to invite Deming in 1951 to deliver a series of lectures on applying statistics to quality control.
Meanwhile, in the United States, the use of statistical process control had virtually vanished after the war, making Japan the ideal place to put his ideas into action.
Deming’s lectures were a resounding success, delivered to standing room only audiences hungry for a solution to rebuilding industry. The real turning point, however, was when JUSE president Ichiro Ishikawa introduced Deming to 21 of the country’s top business leaders.
What Deming recognized even then was that management buy-in was vital to success. He told leaders that if they followed his process, Japan would rise to the top of international manufacturing within five years. In fact, they did it in just four.
Deming’s 14 Points and Lasting Legacy
It was decades before U.S. manufacturing leaders recognized the value of Deming’s teachings, during which time he worked as a consultant and published a number of academic papers.
In 1982, Deming published Out of the Crisis, which outlined his now-famous 14 points:
- Establish constancy of purpose in improving products to stay competitive
- Adopt the new philosophy and take ownership of change
- Stop depending on inspection for quality, instead relying on built-in quality
- Stop awarding business to suppliers based on cost alone
- Strive for continuous improvement of products and processes
- Implement on-the-job training
- Establish better leadership and supervision of not just operators, but management itself
- Eliminate fear
- Break down departmental silos
- Get rid of slogans like zero defects, recognizing that poor quality is a problem with the system itself
- Substitute leadership for quotas and targets
- Eliminate barriers that rob people of their pride in workmanship
- Implement education programs
- Put the entire organization to work in driving the transformation
The fact that these 14 points seem commonsense today is a testament to how his ideas have fundamentally shaped the field of quality management. Universally recognized as one of the founding fathers of Total Quality Management, Deming is also credited for Japan’s economic miracle of the 1970s and 1980s.
In the end, his legacy goes beyond statistics with a philosophy that focuses as much on people as on numbers. Moreover, his ideas came not just from business theory, but from observing people, showing respect for their experience and identifying what they needed to do their best work.