Real-Life Layered Process Audit Results
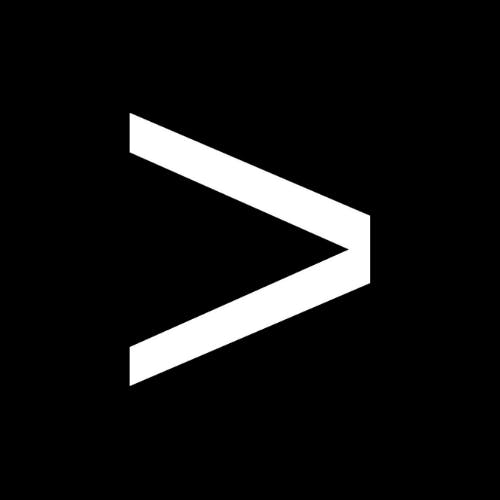
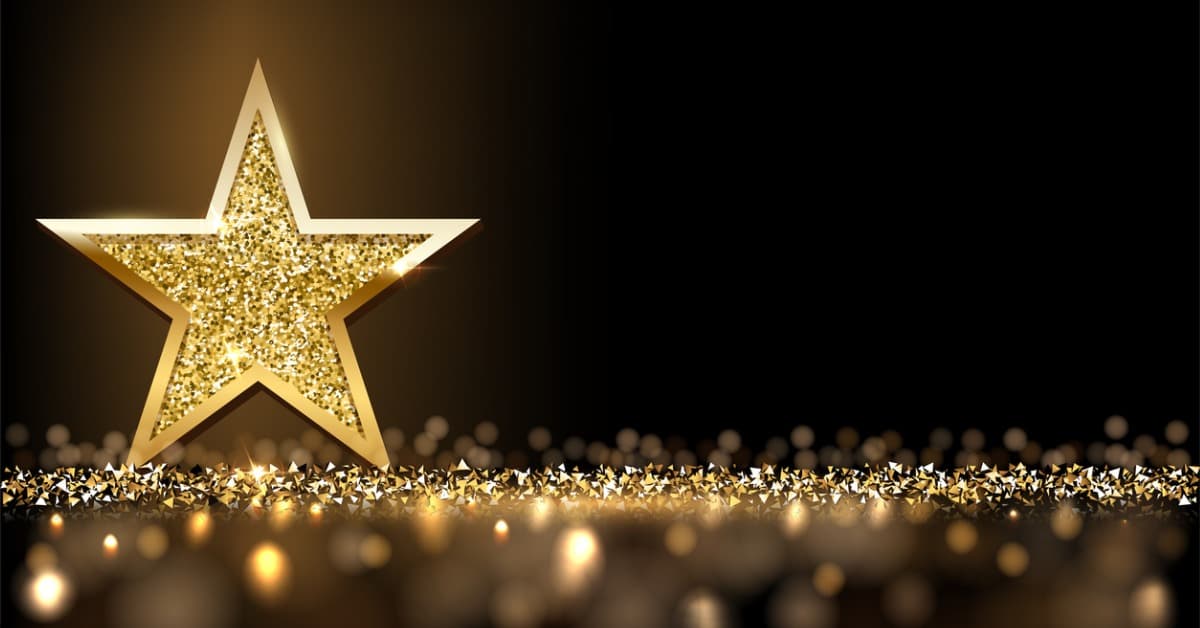
Implementing a layered process audit (LPA) program takes effort and adequate resources to manage, report on, and address audit findings.
The question for many plants before embarking on such an initiative: is it worth it?
The answer is yes if you put in the work to build a robust LPA program. To illustrate the power of LPAs, this article explores real-life examples of LPA results, including how LPA software can be a catalyst for success.
Download your free Ultimate Guide to Layered Process Audits for LPA best practices and tips for writing questions
Valeo Plant Reduces Quality Costs 50%
Valeo is a Fortune 500 automotive supplier with 184 production facilities in 31 countries. One Valeo plant was facing complaints over defective pivot tubes and had added a step to the assembly process to correct the issue.
LPAs were critical to ensuring operators followed the new process, but manual Excel tracking and basic audit software made follow-up and reporting difficult.
Implementing EASE helped them eliminate hours of manual data input, with real-time access to LPA metrics and dashboards to stay on top of issues and trends. They also added photos to mobile checklists clearly showing the correct crimping, helping eliminate recurrence of the issue altogether.
Key results:
- 50% reduction in customer complaints and quality costs
- 98% on-time audit completion rate
- Completing nearly 500 audits monthly
Read the full case study
Global Aerospace Supplier Reduces Customer Defects by Half
A top aerospace supplier implemented EASE to address shortcomings in its paper and Excel-based LPA program. Plants were struggling with low audit completion rates due to the hours required for manual scheduling, tracking and data entry.
With EASE, the supplier automated scheduling, reminders, and reporting, scaling from seven audits per year to over 100 each month in the process. With auditing metrics strongly correlated with quality, LPAs have also equipped the plant with leading indicators for proactively preventing defects and complaints.
Key results:
- 53% reduction in customer defects
- Went from 7 to 100 audits monthly
- Rolled out digital LPAs to 21 plants in 6 countries
Read the full case study
Top 50 Automotive Supplier Reduces PPM 73%
A Fortune 500 supplier with dozens of plants was struggling to get results with its paper-based LPA program that required a full-time employee to manage. Audit completion rates were only about 50%, meaning they weren’t getting the data needed to effectively manage process risks.
Automated notifications and real-time reporting with EASE helped significantly increase audit completion rates, also helping pinpoint specific lines, shifts or processes with issues. The result was a sharp reduction in internal PPM and overdue corrective action requests, leading to a rollout of EASE to more than 30 sites.
Key results:
- 73% reduction in internal PPM, plus reduced scrap costs
- 94% fewer overdue corrective action requests
- 85% or more audit completion rate at all plants
- Highest ever customer quality ratings from OEMs
Read the full case study
Jacobs Boosts Audit Completion Rates 40%
Jacobs Vehicle Systems initially used a Kamishibai system to structure its audit process, which required logging results on a dry erase board and spreadsheets. Due to difficulties with scheduling audits, following up on issues, and ensuring adequate audit coverage, they decided to implement EASE.
Using the digital LPA platform, one plant increased audit completion rate more than 40%, while ensuring even distribution of audits and more effective mitigation of quality issues. As a result, the company has implemented EASE in additional plants, also expanding its use for safety and 5S audits.
Key results:
- Audit completion rate increase of 40%
- Monthly audits increased 300%
- 10 findings resolved weekly, with average closure rate of 2 weeks
Read the full case study
Global Tire Manufacturer Innovates LPA Strategy to Uncover Systemic Issues
A large global tire manufacturer implemented EASE to streamline its manual LPA system, which had failed to deliver results after six months. The company deployed EASE because of how it simplified scheduling, data collection, and reporting, ultimately using the platform to innovate its own method for identifying systemic quality issues.
Their strategy was built around EASE’s dynamic question library, allowing them to add a temporary tag to questions when a nonconformance occurs. Then they add that question to audits on related equipment for several weeks, so they can quickly see whether the nonconformance is an isolated or systemic issue.
Key results:
- Over 200 audits completed weekly
- Faster mitigation of quality issues
- Developed quick-look strategy to identify when multiple work areas are at risk of process failure
Read the full case study
Eissmann Group Automotive Improves Audit Engagement, Reporting and Visibility
Eissmann Group Automotive is a top supplier of vehicle interiors with plants on several continents. A plant in the Czech Republic was having trouble with the overwhelming number of documents that needed updating anytime they wanted to update LPA checklists.
After testing multiple LPA applications, they selected EASE due to its flexibility and language options. The rollout has led to a jump in user engagement, improved reporting, and better visibility into quality plantwide.
Key results:
- 98% audit completion rate
- Streamlined external audits
- Ability to quickly adjust questions and checklists
Read the full case study
LPAs are a powerful strategy for reducing defects and complaints quickly, especially with software like EASE to help streamline these complex audits. With the right tools, plants struggling with quality can achieve their continuous improvement goals with a modest investment of time and resources.