Reporting Near Misses and Good Catches: 6 Best Practices
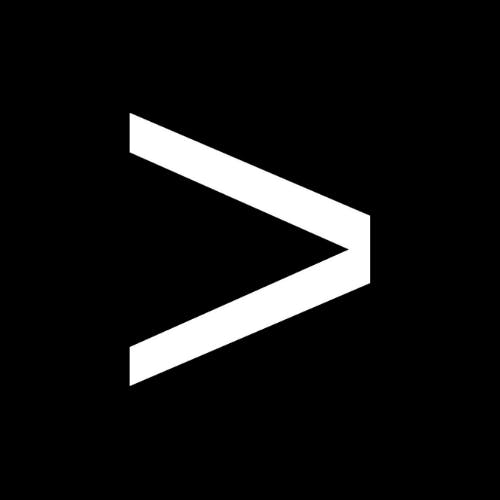
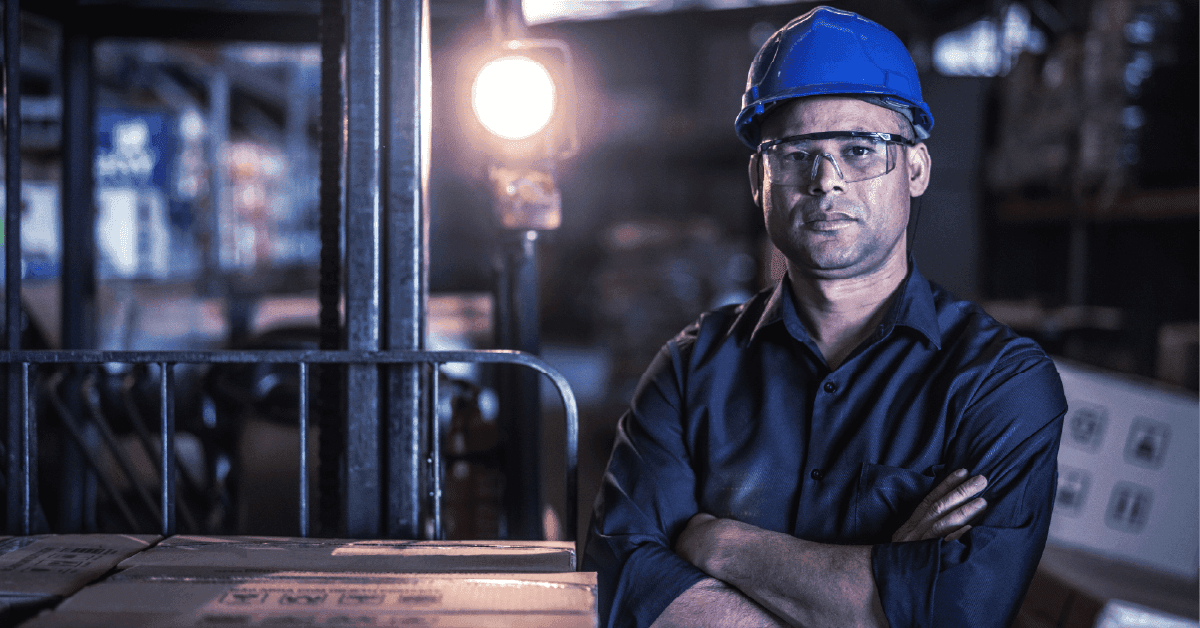
Imagine an employee slips and falls on a wet surface but is lucky enough to walk away uninjured.
Whether the person reports the incident could make the difference in whether another worker is actually injured, for example if the water continues to drip from a leaking roof.
In that case, you’d likely hear: “we knew this was going to happen.”
The key to preventing these avoidable injuries is getting people to report near misses and good catches so you can use these incidents as opportunities to reduce risk.
Here we discuss how and why to do it, and how plant floor software can help capture more and better incident data.
Download a free white paper to learn Why and How Digital Safety Inspections Help Manufacturers Work Safer
1. Defining Near Misses and Good Catches as Incidents
Since near misses and good catches don’t count as OSHA recordable incidents, there’s a temptation to not report them. However, from an internal reporting standpoint, these events provide important clues on hazards and risks on the plant floor.
Defining near misses and good catches as incidents for internal reporting allows you to capture more information about the conditions surrounding the event. This helps plants:
- Identify previously unknown areas of risk
- Develop effective corrective actions to prevent an actual incident
- Share lessons learned with other areas of the plant to prevent a similar incident elsewhere
2. Educating Your Workforce on the Importance of Reporting
If you haven’t already been documenting near misses, you’ll need to educate your workforce on:
- Why it’s important
- What qualifies as a near miss or a good catch
- How to report a near miss
- What details to capture
This sort of training doesn’t need to be complicated, and can even be incorporated into pre-shift or safety meetings.
3. Eliminating Blame and Shame to Encourage Reporting
Getting people to report near misses requires a fundamental shift in how you respond to safety incidents. If the typical reaction is finger-pointing, blame or punishment, people won’t speak up when an accident is narrowly avoided.
Instead, management needs to communicate that the goal is to use these incidents to prevent future harm to other workers. Workers need to know they won’t be retaliated against, and instead will be recognized for their proactive reporting of potential hazards.
Over time, avoiding any type of blame for incidents—including near-misses as well as actual accidents—will foster a culture of openness that allows you to identify and learn from more hazards.
4. Reporting Near-Misses and Good Catches
When reporting near-misses and good catches, it’s critical to capture certain details to ensure thorough documentation and investigation. When setting up reporting forms, you’ll want to consider including details such as:
- Date and time
- Location in the plant
- Incident description, including any resulting injury or damage
- Contributing factors such as equipment malfunction
- Witnesses present in case additional details are needed
- Initial response and follow-up action items
Plant floor audit software or connected worker platforms can be helpful in capturing this data on the spot. Waiting to record incidents on paper later, when they aren’t as fresh, can mean missing important details. Mobile reporting makes it easier for people to log observations, near misses and good catches, and initiate the necessary follow-up for closing the loop on prevention.
5. Closing the Loop on Near-Misses
Crucial to reporting on near misses is following through on them to make sure issues are addressed in a timely manner. If you don’t, people will quickly decide there’s no point in reporting them.
Essential steps here are:
- Flagging the incident for management review
- Launching root cause analysis if needed
- Implementing corrective actions
- Verifying corrective actions with plant floor checks
Preventive action also goes one step further, checking where similar issues could occur and proactively adding controls to prevent recurrence.
6. Using Software to Capture Near Miss Data
Automated plant floor audit software and connected worker solutions improve the reporting process in several ways:
- Workers can easily document near misses on mobile devices, even capturing and attaching photo evidence, increasing the likelihood and quality of reporting
- Plants can customize reporting fields to capture relevant details, track action items and notify leaders
- Streamlined reporting allows you to spot trends by work area or time period
- New audit questions can be added to verify corrective actions, or to check elsewhere in the plant for similar problems
While near misses and good catches are often met with relief, your team needs to know it doesn’t stop there. Capturing details surrounding these incidents is what allows you to prevent them in the future, keeping workers safe while helping build a culture of safety and quality.