Rethinking Quality: A Systems Perspective Inspired by Mechatronics
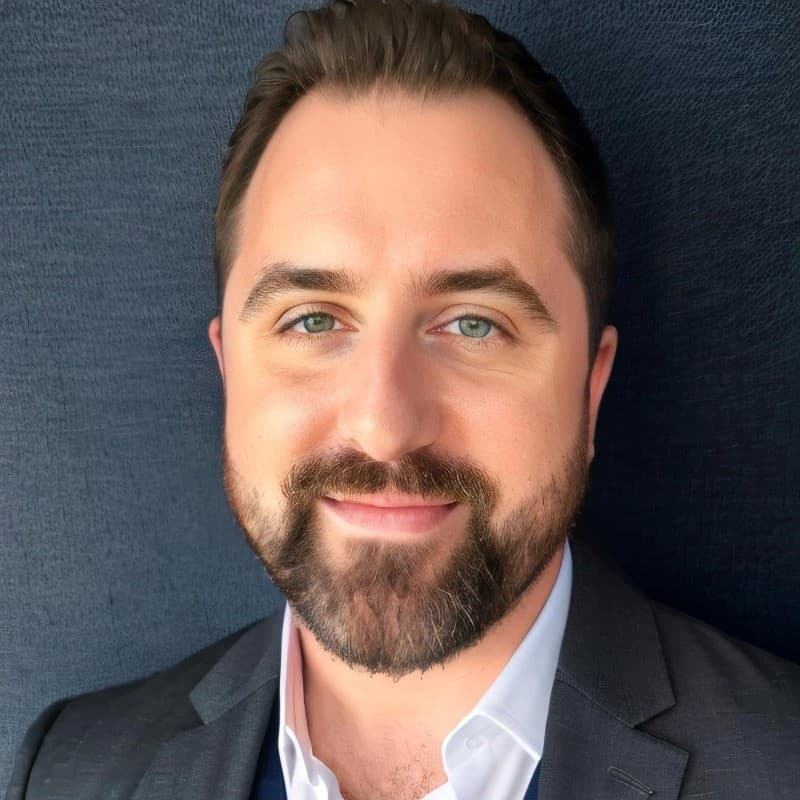
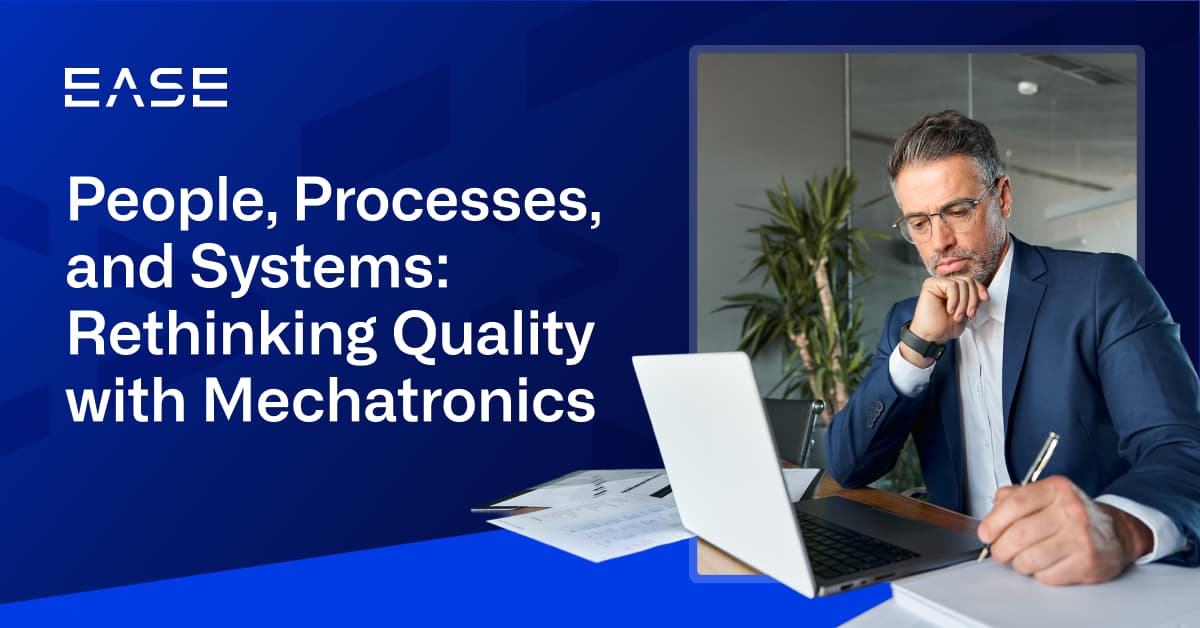
You fix a quality issue. It works for three weeks. Then it’s back.
Different shifts, same process, different results. Your audit completion rates are inconsistent, and leadership is asking why the same problems keep surfacing.
I recently sat down with Daniel Castilla, a mechatronics engineer and quality management consultant with 20+ years of experience, on an episode of the Shop Floor, Top Floor Talk Show. His perspective goes against traditional thinking about why quality problems persist and what manufacturing leaders can do differently.
We surveyed 1,000 manufacturing professionals to better understand how quality is perceived. See the results in our research report: Are Leaders and Frontline Teams Aligned?
The Systems Thinking Revelation
Everything is Connected
Daniel’s insight hit me immediately when he shared his cake analogy: “It doesn’t matter which ingredient is wrong. You just need one to be wrong, and then everything is wrong. You cannot just say, ‘I only care about the water because that’s my responsibility.'”
The Mechatronics Mindset Shift
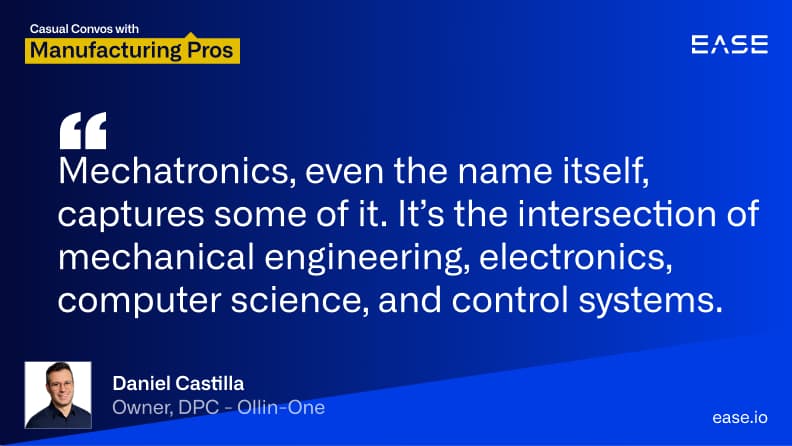
Understanding those interdependencies is just the first step. Daniel’s background in mechatronics, an engineering discipline that integrates mechanical, electrical, and software systems, pushes this thinking further. This interdisciplinary approach, increasingly common in both engineering curricula and manufacturing environments, naturally views operations as interconnected systems rather than isolated components, showing how to design quality into the entire system from the start.
“Quality management is nothing else than systems thinking. A company is running as a whole – human element, infrastructure, environment, machines, product – but everything is part of one thing,” he said. In other words:
- Traditional approach: Fix what’s broken and hope it stays fixed.
- Systems approach: Design quality into the entire system from the beginning.
Instead of chasing problems after they happen, design systems where quality emerges naturally. It’s the difference between reacting to emergencies and designing systems that avoid them in the first place.
Three Critical System Elements
1. People as System Assets
Daniel challenges a common misconception about human variation in manufacturing: “Human variation is sometimes misunderstood as noise, but in reality, that human variation many times is the success factor because it compensates for deficiencies in our machines and products.”
Think about the operator who “just knows” how to make difficult equipment work. These operators compensate for design flaws in equipment or processes.
Instead of eliminating variation, capture and systematize this expertise.
2. Process Interconnections
Most quality leaders face a complex reality: Marketing connects to design, which connects to purchasing, manufacturing, and logistics—suddenly, you realize you have around 50 interconnected processes.
Your work relies on processes that come before you, and other processes downstream depend on what you deliver. A delay or inefficiency in one area ripples through the entire operation.
3. Technology Integration
Simplicity is key. Handle complexity without overwhelming people. Technology should support systems thinking by creating seamless information flow that supports decision-making rather than creating more data to manage.
When you optimize people, processes, and technology as interconnected components, you create a system that prevents problems instead of just detecting them.
Common System Failures
The Quality Paradox
Daniel described a frustrating cycle many quality professionals face: “There’s a saying among quality professionals that we work to lose our jobs. We try to get things to work smoothly, but then organizations say, ‘Why do we need you?’ and reduce quality focus.”
The cycle repeats: problems vanish, investment drops, and then problems reappear. Effective quality systems raise questions about their necessity, but removing them causes quality issues to return.
Breaking Down Silos
Departmental boundaries create artificial ownership lines. People become protective of their metrics and processes, losing sight of how their decisions impact other areas.
When departments focus only on their metrics without considering system-wide impacts, they optimize locally while damaging globally.
Communication and Complexity
Quality professionals often face pressure to oversimplify complex realities for leadership presentations. But ignoring complexity doesn’t make it disappear; it just pushes problems elsewhere in the system.
The solution: Manage complexity in ways that keep operations simple for frontline workers, rather than oversimplification.
Speaking Business Language
We’ve established that quality professionals struggle with communication complexity. But how do you actually bridge that gap? The key is learning to speak each stakeholder’s language while maintaining your systems thinking method.
The same quality improvement can be positioned differently depending on your audience:
- Operations: Focus on efficiency and capability gains. Discuss reducing downtime, fewer disruptions, and smoother processes.
- Finance: Emphasize ROI and capacity implications.
- HR: Frame improvements around employee engagement, safety, and skill development.
- Leadership: Connect quality directly to business growth.
The methodology avoids manipulation or overselling, instead helping each part of the organization understand how quality improvements support their specific objectives while advancing the overall system.
The Bottom Line
Daniel’s systems thinking approach transforms quality from firefighting to systematic prevention. His key insight: “Quality is just an attribute of the output. If your machine is well-oiled and all things are happening as they’re supposed to happen, the output should be good.”
Instead of asking “How do we catch more problems?” we ask “How do we design systems where problems don’t occur?”
Start Here
- Map your process interconnections to see how department delays ripple through your operation.
- Apply the cake analogy to look beyond symptoms and find the real system issue.
- Translate quality improvements into language that resonates with each stakeholder.
- Design for simplicity by handling complexity without overwhelming frontline workers.
When you think like a mechatronics engineer, you see the factory as everything working together by design.
Listen to the full episode of the Shop Floor, Top Floor Talk Show for deeper insights into how mechatronics engineering principles can revolutionize your quality approach. It includes real examples of companies that successfully shifted from reactive quality management to prevention-focused systems. Listen to the full episode here.