Reverse FMEA Basics for Manufacturers
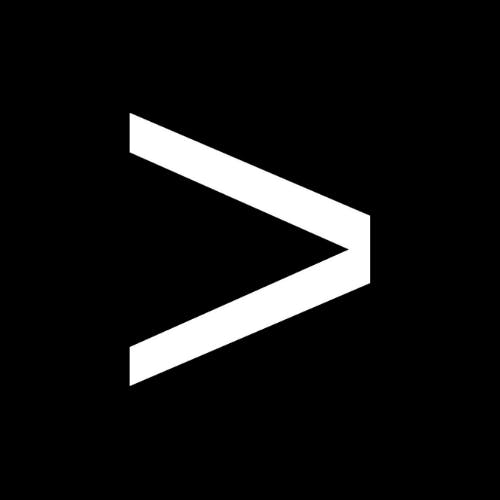
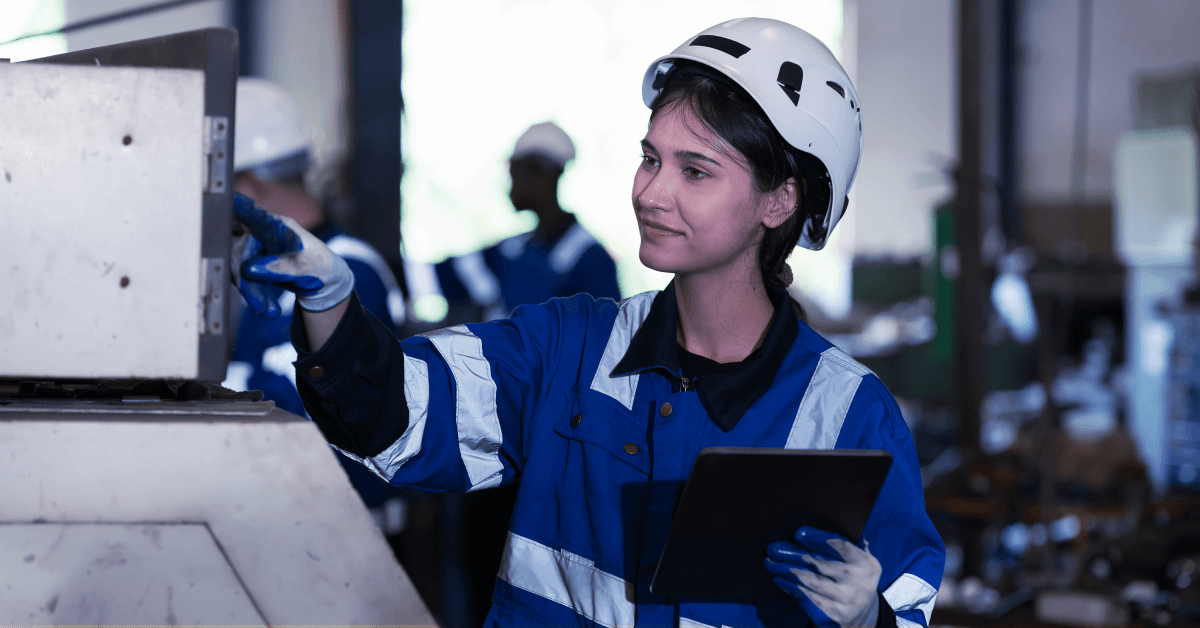
Suppliers to Ford are required under the automaker’s customer-specific requirements to perform a reverse failure mode and effects analysis (FMEA) on all new equipment launches.
This requirement begs the question—should manufacturers be conducting reverse FMEAs as a routine practice? If so, what do they need to know to get the most from this process?
Here we dig into these and other questions, exploring best practices for conducting a reverse FMEA and mistakes to avoid in the process.
Download a free eBook on Root Cause Analysis 101 Guidebook to learn more about FMEA and other root cause analysis tools
What Is an FMEA?
An FMEA is a tool used in manufacturing to reduce risk at the product or process design phase. An FMEA first defines all the ways a product or process could fail to meet the customer’s requirements, which are called failure modes. From there, the FMEA looks at:
- What are all of the potential causes for each failure mode
- How the cause can be prevented with prevention controls
- How the cause or failure mode can be detected with detection controls
What Is a Reverse FMEA?
A reverse FMEA can be applied to a process FMEA (PFMEA) to validate each of the above elements against real-world conditions on the plant floor to assess whether:
- All failure modes have been identified
- All possible causes have been documented
- All prevention and detection controls have been implemented and are operating properly
Reverse FMEA Steps
A reverse FMEA is essentially an audit of the completeness and effectiveness of a PFMEA. The first step in conducting a reverse FMEA is to go through all of the prevention and detection controls in the PFMEA to make sure they are in place and functioning as expected.
For example, let’s say the process in question has a poka-yoke in place to prevent a part from being loaded upside down. A reverse FMEA would then involve going out to the machine to confirm the effectiveness of the poka-yoke. If testing reveals that by pushing the part around, it will still load upside down, that’s a gap in your prevention controls that must be addressed.
The second step in a reverse FMEA is to determine if all possible failure modes have been identified. Cross-checks here include:
- Reviewing problem-solving and corrective actions
- Looking at other similar processes and what failures they have had (for example, as indicated by scrap)
- Having a cross-functional team review FMEAs on an ongoing basis
The third step in a reverse FMEA is to determine if all potential causes have been identified, both for existing failure modes as well as any new ones identified in step two. One way to facilitate this is by having a cross-functional team use a Fishbone diagram to analyze failure modes.
One Pitfall to Avoid with Reverse FMEAs
The most common mistake plants make with reverse FMEAs relates to identifying causes of problems. As a best practice, teams should evaluate the full range of potential causes in a Fishbone diagram, also called the 6Ms of process control:
- Man (operator)
- Machine
- Method
- Mother nature (environment)
- Material
- Measurement
Too often, plants become overly focused on just one leg of the Fishbone diagram, for instance just looking for operator mistakes or machine issues.
One plant, for example, was investigating a laser weld failure mode of seam split. The team jumped to the conclusion that more heat was needed to improve the weld strength, so they slowed the machine down to add more heat. This, in turn, created a different failure mode of burn through.
In fact, the real cause of the weld failure was not the machine—it was a defect in incoming material. The operation that cut the blank was leaving a burr on the blank, preventing it from being properly located in the laser weld machine. What the team needed to look at was how the material was presented to the weld cell, not just how the weld cell operated.
Do Plants Really Need Reverse FMEAs?
According to manufacturing consultants at The Luminous Group, what many call a reverse FMEA has always been part of the advanced product quality planning (APQP) process.
“At best, a reverse FMEA is a documentation of existing practices,” says senior consultant Richard Nave. “At worst, it’s just a band-aid fix when a plant isn’t doing what it should be in APQP.”
He also mentions layered process audits as a key tool for verifying FMEA controls on a frequent basis, rather than performing the occasional reverse FMEA exercise.
“If you’re doing layered process audits, you’re already checking process and detection controls,” he says. “If you used FMEA during APQP to develop machine processes, you wouldn’t need to do a reverse FMEA.”
Ultimately, says Nave, the concept of a reverse FMEA is a cross-check that all plants should be using as part of layered process audit and APQP processes that are operating effectively. Layered process audit software like EASE can help improve effectiveness, so plants can get to the heart of what reverse FMEAs are all about: verifying controls and preventing process failures.