Gemba Audit: Taking the Step from Gemba Walks to Layered Process Audits
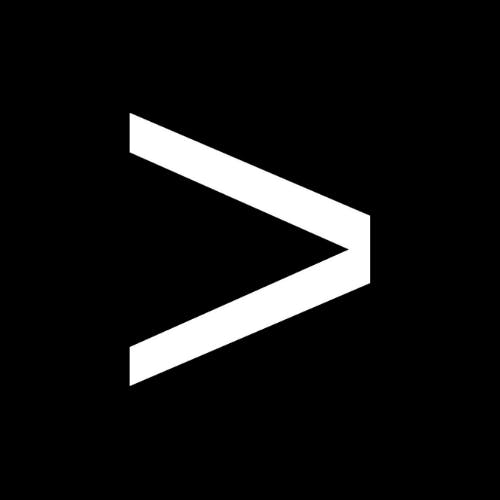
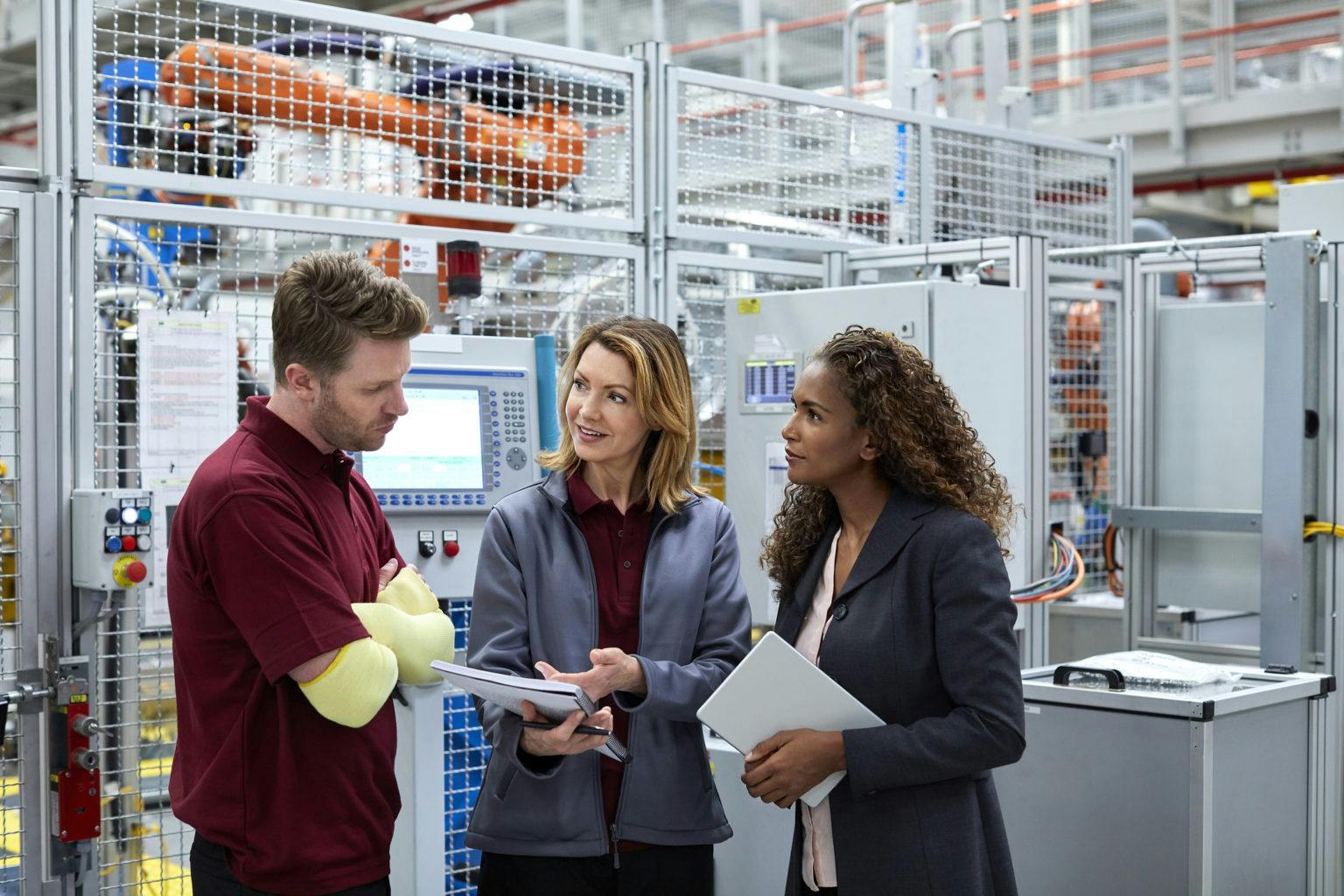
Reading the Automotive Industry Action Group’s CQI-8 Layered Process Audit Guideline, you might notice a line saying LPAs are “completed on-site ‘where the work is done.’”
For Lean manufacturing experts, this specific quote might bring to mind Gemba walks, a method where leaders observe and solve problems on the shop floor. In Japanese, Gemba means “the real place,” or in manufacturing, where the work is done. Here are some Gemba walk examples.
Whether the reference is intentional or not, layered process audits (LPAs) and Gemba walks share clear similarities. Could it be why companies doing Gemba walks have an easier time with LPA programs, despite their complexity? This post compares Gemba walks with LPAs, exploring how to tell if you’re ready for LPAs and how to prepare.
Comparing Gemba Walks to Layered Process Audits
Gemba walks are an essential strategy for getting managers out of the office to experience shop floor processes up close. In this sense, they’re similar to LPAs, where frequent checks of critical processes give managers fresh perspective (and maybe even challenge some assumptions).
Other similarities between Gemba walks and LPAs include:
- Focus: Any Gemba walk or LPA has a specific focus, whether it’s a high-risk procedure or one where bottlenecks tend to occur.
- Layers: Both practices involve multiple layers of management who participate at different frequencies.
- Communication: Gemba walks and LPAs open the door to conversation and coaching, rather than focusing on punishing mistakes.
- Visibility: The presence and involvement of leadership on the plant floor makes quality visible, elevating it as a priority for everyone.
Taking Gemba Walks to the Next Level
On their own, Gemba walks are a valuable tool for uncovering inefficiencies in an organization’s processes. LPAs complement Gemba walks by providing:
- More structure: LPAs are more structured, consisting of a set of up to 10 questions focusing on specific areas critical to quality and/or safety.
- Robust data: LPAs can generate a large data set of quality insights, helping you develop leading indicators that show you where you’re headed.
- Nonconformance management: LPAs let you correct problems and log corrective measures on the spot, so you only have to send larger issues to the corrective action system. By uncovering issues internally before they become a customer problem, suppliers can expect as much as a 50 percent reduction in returns.
Are You Ready for Layered Process Audits?
While organizations with mature Lean programs are primed for LPAs, the most important ingredient for success is a genuine commitment to improving quality. Any expert will tell you that doing LPAs just to check a box will never give you the same results as when you believe in their ability to truly improve quality.
So what does that kind of commitment look like?
- Taking the time to analyze data while they are still actionable, rather than letting the results sit in a spreadsheet or file cabinet
- Investing in training and resources to help your team be successful
- Structuring audits and follow-up activities in a way that prevents pencil-whipping
- Not allowing leaders to delegate audit responsibilities
- Sticking to your audit schedule, instead of just accepting that you will only complete a portion of them (a major problem in many organizations)
Laying the Foundation
Final thoughts on Gemba audit
For many companies, making these audits work requires an automated LPA system to handle scheduling, data analysis and checklist management. Many aerospace suppliers see the benefits of LPA in the auto industry, but they are reluctant to do it because of the administrative overhead.
Automation slashes the resources required, allowing some manufacturing sites to reallocate up to 2 full-time employees focused on audit scheduling and management. An automated LPA platform makes it simple to:
- Schedule an entire year’s worth of audits, accounting for shifts, days off and time away from work
- Send email notifications with links to checklists, also escalating overdue audits as needed
- Use mobile audits to eliminate paper checklist management
- Update audit checklists as needed to account for key changes or newly identified risks
- Pinpoint trends driving quality with user-friendly graphs and key performance indicator (KPI) tracking
What you decide to do with these insights is where the real work starts. Knowledge is power, but only if you’re ready to take responsibility for what you find in your data.