The ROI of Digital Collaboration in Root Cause Analysis
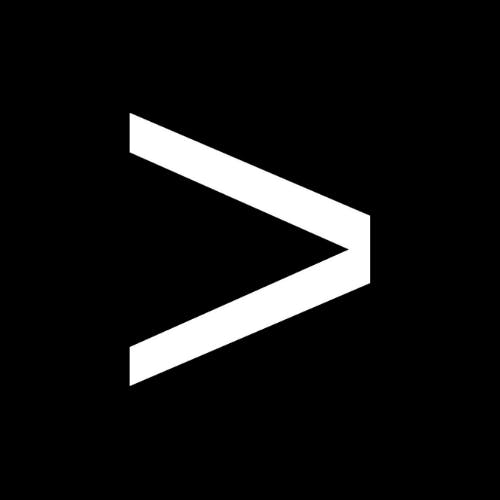

In manufacturing, efficient problem-solving and root cause analysis are vital to quality, on-time delivery and customer satisfaction.
Historically, manual processes have meant extended problem-solving timelines, allowing issues to snowball into systemic problems with downstream impacts on quality and company reputation.
The advent of Industry 4.0, however, has changed the equation, opening up new avenues for streamlining root cause analysis and problem-solving.
Below we explore the complexities of these processes, how traditional manufacturing problem-solving creates challenges and the financial impact of using digital tools to improve collaboration.
Download your free Root Cause Analysis 101 Guidebook to learn about the five most common root cause analysis tools
The Complexity of Root Cause Analysis and Problem-Solving in Manufacturing
When investigating problems like quality or maintenance issues, the problem-solving process requires multiple steps and handoffs. For example, 8D problem-solving, a common approach to addressing complex or recurring issues in manufacturing, involves eight steps:
- D0: Plan
- D1: Form a team
- D2: Define and describe the problem
- D3: Implement interim containment actions
- D4: Analyze the root cause
- D5: Formulate and select corrective actions
- D6: Implement and validate corrective actions
- D7: Identify and implement preventive actions
- D8: Recognize the team and individuals
Root cause analysis is a critical part of this process, often using methods such as the 5 Whys or creating a Fishbone diagram. These methods typically require gathering data, process observation and collaboration among departments like quality, engineering and operations to understand the problem.
Manual Processes Drive Long Problem-Solving Timelines
One major challenge in manufacturing problem-solving is reliance on manual processes. Using paper-based methods, simply bringing together essential team members and gathering the right data can take weeks. Then there’s the time it takes to formulate, implement and validate corrective actions, extending problem-solving timelines even further.
The result is extended lead times—in some cases, upwards of 90 days—to fully resolve issues.
One major concern is that these delays leave room for problems to escalate, impacting quality and customer satisfaction. It’s one reason why an extensive backlog of open corrective actions can be such a problem for manufacturers during third-party or customer audits.
Streamlining Collaboration with Technology
Digital collaboration is key to overcoming the limitations of manual root cause analysis and problem-solving, with digital tools providing advantages such as:
- Easy access to relevant data: Digital tools allow enable plants to more easily access historical data, including data on similar issues that have occurred in the past. This saves time by allowing teams to leverage insights from previous root cause analysis exercises, accelerating the path to identifying effective solutions.
- Visual documentation: The ability to upload photos on the plant floor, such as with mobile audit software, helps clarify problems and provides crucial context for root cause analysis.
- Automated issue management: Digital collaboration tools like mobile audit software and connected worker platforms streamline issue management by automatically routing nonconformances for review, investigation, and correction. This minimizes waiting time associated with manual handoffs, improving problem-solving efficiency.
- Real-time equipment insights: Manufacturers can utilize data from the Internet of Things (IoT) sensors to get better insights into the root cause of equipment issues. Real-time data enables more proactive problem-solving on the plant floor, reducing downtime while increasing overall equipment effectiveness (OEE).
- Streamlined communication: Tools like connected worker platforms facilitate real-time communication among teams, so that all relevant parties can stay updated on the current status of issues. This helps identify and minimize bottlenecks that can hold up the process.
The ROI of Digital Collaboration
According to analysis by McKinsey, digital collaboration applied to root cause analysis has the potential to add tens of millions of dollars to a manufacturer’s bottom line. These financial benefits come primarily from two sources: improved service and reduced quality costs.
Their firm looked at a hypothetical manufacturer with $10 billion in revenue, noting that digital collaboration in problem-solving could increase service level by 1% and reduce downtime by 1%. The result in this hypothetical scenario is a 0.2% increase in revenue, totaling $20 million.
McKinsey also estimates that digital problem-solving tools could reduce scrap as much as 25%, adding 0.5% or $50 million in revenue to their hypothetical manufacturer’s annual revenue.
Relying on traditional problem-solving methods can lead to delays in resolving issues, which can ultimately impact quality, efficiency and customer satisfaction. Digital collaboration tools have emerged as a game-changer in terms of providing better visibility and communication, accelerating problem-solving for fewer defects and more satisfied customers overall.