User Summit Notes: Layered Process Audit Tips from Leading Companies
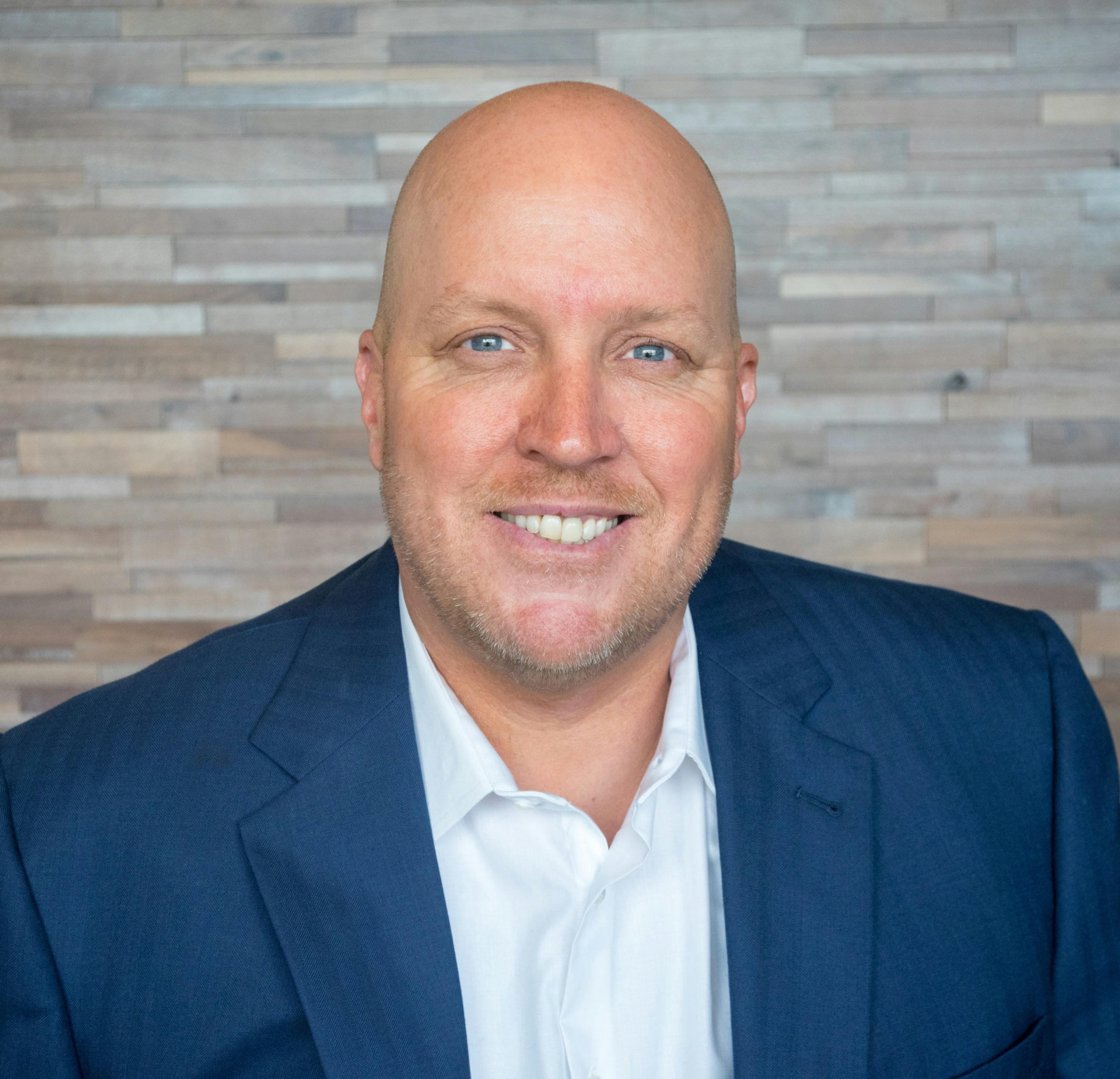
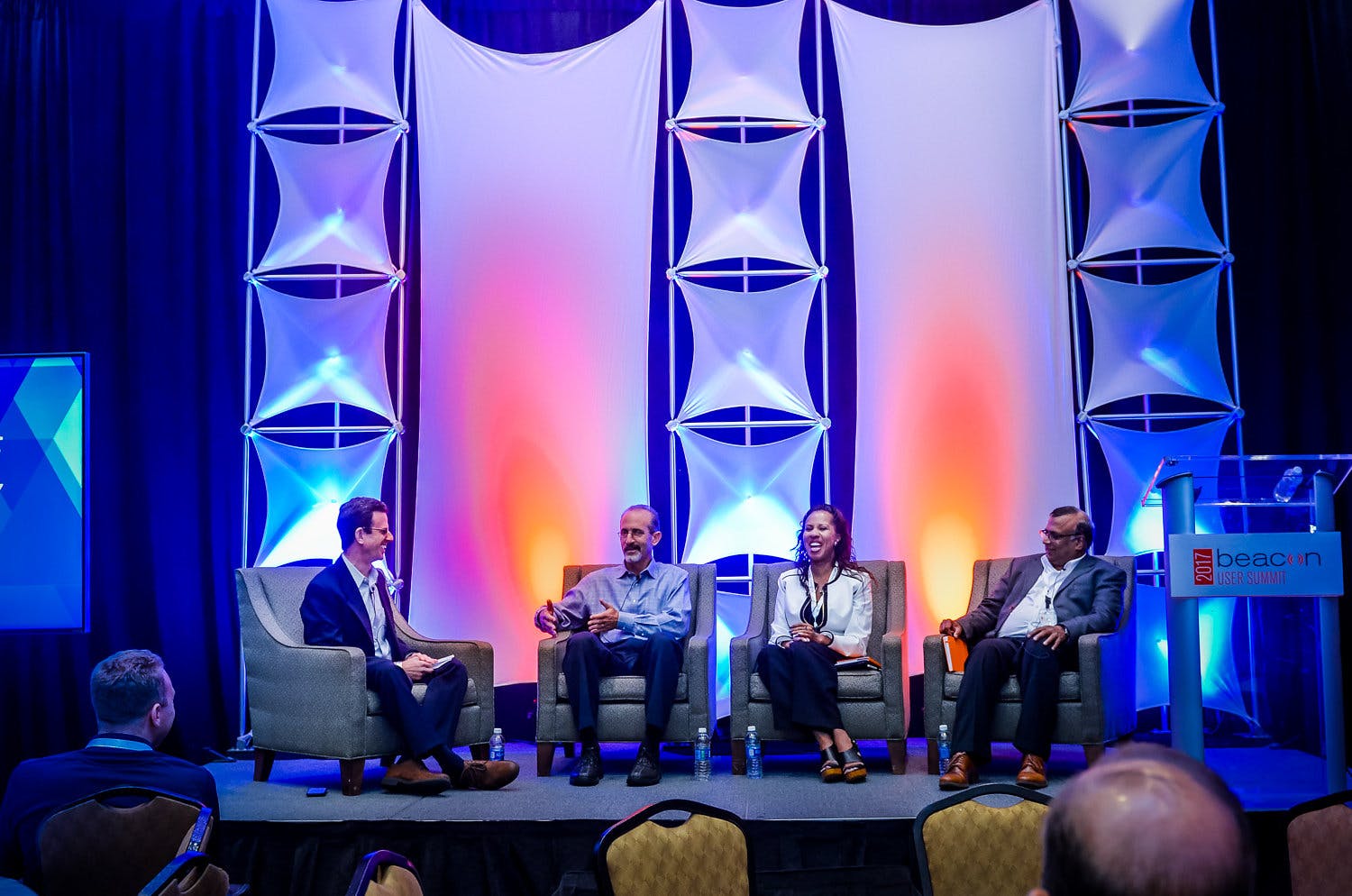
The 2017 Beacon User Summit convened auto and aerospace manufacturers looking to trade strategies on creating a culture of quality and using layered process audit (LPA) software.
One of the most interesting sessions was a customer panel discussion on how companies are leveraging LPAs to improve quality. To help you learn from their expertise, we’ve distilled the discussion into the top best practices for companies looking to implement LPAs.
Implement Audits for the Right Reasons
According to panelists, getting real value from your LPA program starts with the right motivation.
With LPAs, all layers of management participate in checking high-risk processes on a daily, weekly, monthly and quarterly basis. This requires long-term discipline, making internal motivation essential to success.
Think of it like the classroom: intrinsically motivated learners study because they are genuinely interested in the subject. Extrinsically motivated learners study because their parents will punish them if they flunk, or because they want to get into grad school. While rewards and punishments may work in the short term, research shows they are ineffective in the long term.
The same goes for LPAs. Are you implementing them because you truly want to improve quality, or just to satisfy a customer requirement? As with many business problems, a basic compliance approach won’t take you far.
Drive Culture Change from the Top
Creating a culture of quality is a primary goal for many companies using LPAs. Panel experts insist that culture change starts at the top, with leadership setting the tone and expectations around quality.
It’s one of the advantages of LPAs. By definition, they involve upper layers of management. When front-line employees see leaders on the floor, they know your commitment to quality actually means something.
This mindset shift makes people more likely to:
- Identify and fix problems on their own. One panelist noted LPAs have made the maintenance team more proactive, so they no longer miss scheduled activities.
- Share observations with leadership. When people see problems fixed quickly, they’re motivated to share their own ideas for improvements.
- Complete scheduled audits. Knowing higher layers of management will see if they missed a problem is a powerful motivator.
Involve the Entire Organization
Beyond just quality leaders, organizations are seeing results by requiring LPA participation from all departments, including engineering, human resources (HR), finance and administration.
Why is this important? Several reasons:
- It takes quality out of a single department. Many companies treat quality as an administrative function, when it actually affects every business area. Only when everyone is accountable for quality will you see meaningful improvement.
- Fresh eyes lead to fresh observations. Non-experts typically follow audit instructions to the letter, rather than making assumptions. One example discussed was how certain auditors simply assumed operators were following work instructions, automatically checking off the item. It took an HR auditor to notice that some stations didn’t even have instructions posted.
- It makes quality personal. Cross-functional collaboration opens people up to how quality affects them personally. For instance, finance people might resist participating until they see a costly oil leak firsthand.
Make Quality Visible
Panel experts insist that companies need to make quality more visible. It’s an important driver of cultural change, helping dispel the idea that only the quality department is responsible for quality.
Examples discussed include strategies such as:
- Having auditors wear high-visibility vests with “LPA” printed on the back, which reminds employees to pay close attention to quality
- Activating an audible and/or visible alarm when a defect is found, aiming to raise awareness rather than point fingers
- Being disciplined about updating quality metric boards, so everyone can see that leaders are engaged
Take Ownership of Quality
More than just scheduling and completing audits for the sake of doing them, companies have to own the entire process. As one panelist put it, “Why should customers have to tell you that your product is falling short? You should be identifying the problems yourself.”
Key elements of quality ownership include:
- Closing the loop with corrective action. If you find a lot of issues without resolving them, people will see the audits are worthless and stop engaging. It also significantly increases your risk of a quality escape.
- Analyzing data as soon as possible. Companies using paper-based tracking methods waste a lot of time manually entering data. By the time they analyze their data, they’ve missed important opportunities to prevent defects.
- Developing leading indicators. Effectively leveraging data means developing leading indicators around your audit programs. Metrics like audit completion rates and time to closure often directly correlate with quality.
- Updating audit checklists. Audits should reflect current problems, so you should continually refine your questions according to defects, returns and other issues. You should also eliminate questions that never record a failure.
Ultimately, panelists agreed that automation streamlines the process and accelerates results. Those results include moving from 20 annual audits to 200 monthly, driving a 50% reduction in defects and quality escapes. It may sound difficult if you’re just starting with LPAs, but anyone can get there with the right approach.