Case Study Video: Aston Martin Relies on Ease Manufacturing Software
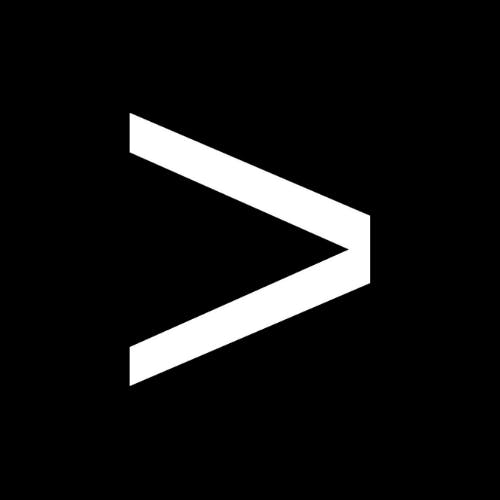
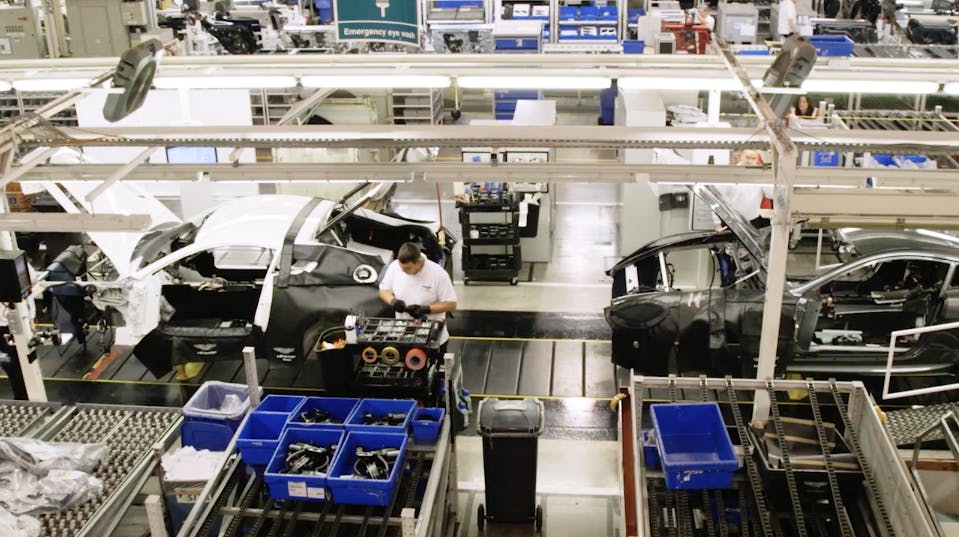
Founded more than 100 years ago, Aston Martin has built a global brand known for producing exceptionally designed, high-quality cars through handcrafted production methods.
After more than a century of excellence, few can understand better that delivering market defining quality and craftsmanship requires superior tools, techniques, and technology. As Aston Martin looked to increase production levels and launch new models, they quickly realized many of their traditional manufacturing processes would limit growth and competitiveness. Aston Martin needed an innovative solution that would create new manufacturing efficiencies without compromising their ability to deliver a truly bespoke product to their customers, built to the highest quality standards.
To achieve these goals, Aston Martin turned to Ease. Founded in 1986, Ease has been built on the premise that quality processes translate into higher output and superior end-products.
After implementing Ease, processes such as passing folders with printed technical documents between stations was eliminated. Time lost from technicians paging through binders to find the correct process for a specific configuration was recaptured through a single touch-screen with only the most current and relevant information needed by the technician for that specific order. Quality audits previously done on a clipboard are now done via tablet and include real time reporting.
With help from Ease, Aston Martin is making better cars, more efficiently.
Aston Martin and Ease Video
Ease is excited to release this video about its partnership with Aston Martin. This case study video provides a closer look at how Ease helps Aston Martin achieve new efficiencies and higher quality that’s consistent with their manufacturing and design philosophy of Power, Beauty and Soul.
Transcript of the Video
Aston Martin was founded just over 100 years ago by Lionel Martin and Robert Bamford. If you said “Aston Martin,” 90% of people would say “James Bond,” wouldn’t they? Probably more.
A lot of work goes into the interiors of the car and the paint finish. It’s all about the finer details. The whole philosophy of the company is about the power, the beauty, and the soul. We believe that it is our responsibility to create beautiful cars built to the highest quality standards, giving customers the opportunity to create a truly bespoke vehicle.
Nick Lines, Head of Manufacturing, Aston Martin:
When I first came here, the production methods were very much, craft hand production methods, but also had craft-type levels of control in terms of processes.
Leon Hand, Manufacturing Manager, Aston Martin:
Place an order into Excel, print it into hard copies and put in a folder on the station.
Nick:
For every single step of the production process, we had a document that outlined, on a series of pieces of paper with photographs and instructions, how to do the job.
Scott Ward, Trim & Assembly General Manager, Aston Martin:
Department to department would have to pass those documents on. And in passing those documents on, errors are often made.
Leon:
We knew we had to go out and do something different.
Nick:
And so we went out and looked at the broader marketplace. And then we came across Ease.
Eric Stoop, CEO, Ease Inc.:
Ease was founded in 1986. We are a company focused on improving our customers’ quality, reducing our customers’ wastes and costs, and overall improving efficiency with Labor Standards, Work Instructions, Process Audits, and Work Measurement software.
Mark Whitworth, COO, Ease Inc.:
Ease has, to date, really been focused on the operators, or associates, at the manufacturers or at the service companies to make sure they’re performing their tasks correctly, time and time again.
Paul Foster, Requirements Analyst, Ease Inc.:
We want to help make it easy for them to use all of the great new technologies that are becoming available with the Internet and computing power.
Mark:
Aston Martin had three goals of increasing quality, efficiency, and output.
Eric:
They’re bringing four different models down two lines and you have completely different configurations. It’s a very customized vehicle.
Mark:
So they are really in a situation where if you want to produce more vehicles, if you want to produce different types of vehicles, you have to bring efficiencies to the table.
Leon:
Ease is on all manufacturing areas now. Every part of the factory from the very beginning shutters and railway past the sales point has got an Ease station on there.
Nick:
We use Ease to communicate to the production areas precisely the specification the customer wants, precisely how that car is to be built.
Scott:
We’ve introduced more and more control through Ease. Parts verification is the big thing whereby now, as we build the car, the technicians scan through these terminals to verify what parts have been fitted to what vehicle.
Nick:
The Ease system communicates with the PLCs [programmable logic controllers] and the systems that run the production conveyors that actually stop or start the production conveyors dependent on this issue whereby the production technician confirms that the quality is good.
Leon:
We have less rework now, in terms of when the cars come off. Because we know that the car leaving the station is correct.
Mark:
One of the challenges that organizations face is this handling of change requests and the ability to make sure that that gets raised to the appropriate parties and gets properly dispositioned.
Nick:
With the Ease system, the production technicians can make a request of the engineering team to say that they need to have something changed.
Leon:
If they see something wrong with it, process documentation, they have direct access to be able to tell the manufacturing engineers that something’s wrong.
Scott:
We’re constantly improving the process through that format.
Mark:
Even though they have these electronic instructions and the operators are doing things well, there are other things that can break down the process.
Eric:
This audit and compliance piece is the foundation for manufacturers because it’s the best way to determine whether you’re actually improving.
Nick:
By using a tablet or using a smartphone, we can conduct audits. We pull the information and they send it out to the people who are responsible for the areas that we’ve reviewed.
Paul:
The prime example of how that would work is an auditor is assigned to do an audit. They pull it up on a tablet and then they can start wandering the factory floor where there may not even be Internet connectivity. And conduct work and then go back online and then everything syncs up seamlessly.
Scott:
The processes that are at-fault, straightaway link-in through the tablet and then we can correct things.
Leon:
And they are all done on a regular schedule as well. So you can say you need to repeat these audits every two weeks and it will just schedule it.
Scott:
It’s basically the toolbox people need to be able to achieve the standard.
Nick:
The future of Aston Martin is to continue to create beautiful cars and sell them all around the world.
Scott:
To be the best and match the best, you’ve got to have the best tools and techniques at your hands.
Paul:
Whether you’re looking for quality standards, you’re looking for customer satisfaction, almost any industry or company could use Ease.
Mark:
Really, Ease’s products help make sure that everyone has the right information and that they’re doing things in the right way.
Eric:
We say “Process Performance Solutions” because that’s what we do. We come in and really give our customers a tool that really makes a difference.
Scott:
If someone came to me and asked, “what’s the best tool to use to achieve the right process,” then I would say “Ease” without any shadow of a doubt.