Core Lean Manufacturing Principles for Aerospace Manufacturers
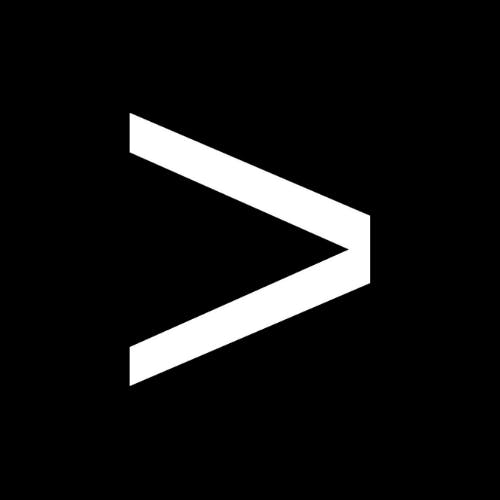
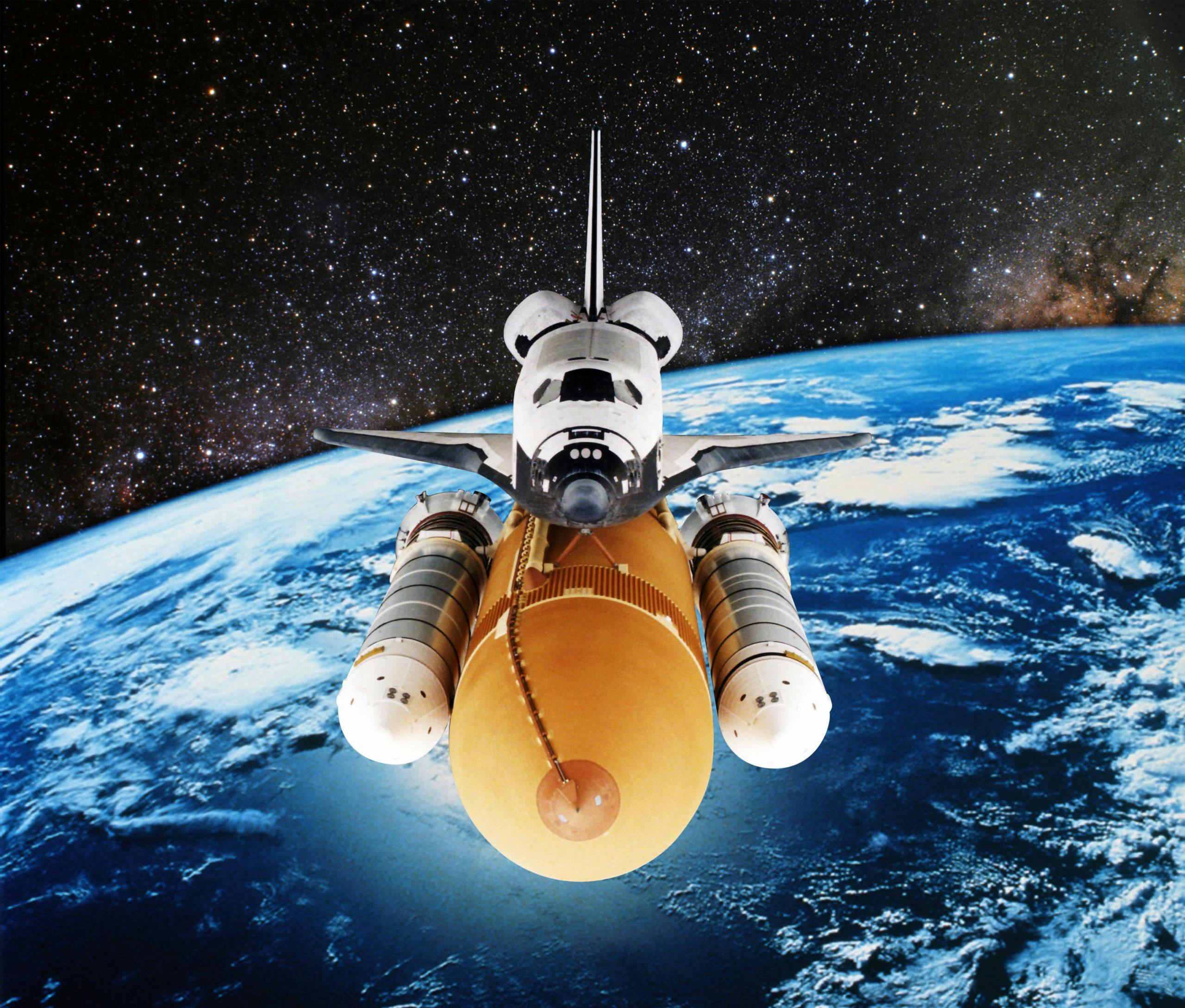
Quality guru Shigeo Shingo once said, “Improvement usually means doing something that we have never done before.” For many in the aerospace industry, the exploration of lean manufacturing principles would qualify not only as something new, but also as something that merits consideration.
Lean manufacturing is a methodology for improving processes with continuous improvement (kaizen) and eliminating waste in the workplace. Many think of lean manufacturing as North America’s answer to the Toyota Production System (TPS), which enabled Toyota to deliver a wider variety of products more efficiently than the traditional mass production techniques of the era.
In the past, there may have been a perception that lean manufacturing was best suited for the automotive industry and was perhaps too challenging to transfer to other sectors, especially when there were major differences between the sectors. Yet, lean principles have been widely implemented since the 1990s, in a wide variety of industries, and countless companies have achieved notable results. Lean manufacturing is a viable strategy not only within the automotive industry, but also in nearly every sector, including the high-precision aerospace industry.
Lean Manufacturing Principles
Lean manufacturing is centered on five tenets:
- Identifying what creates value from your customers’ perspective
- Specifying every step in your processes
- Ensuring that those processes flow
- Producing only what customers request
- Striving for perfection by continually removing wastes
These lean manufacturing principles incorporate a range of techniques including just-in-time inventory systems to identify and reduce waste in processes and to satisfy customers’ requests. A just-in-time system not only provides internal and external customers what they want, but also when they want it and at the lowest possible cost.
Two of these lean tenets—specifying process steps and ensuring that processes flow—can be supported with the use of layered process audits (LPAs). These audits differ from generic process audits as they involve multiple people, including management, in conducting an ongoing chain of basic verification checks to ensure that a defined process is followed correctly. When implemented properly, LPAs are a powerful audit management tool that can promote quality and deliver cost savings by boosting problem-solving systems and making continuous improvement nearly routine.
Lean manufacturing in the aerospace industry is a bit different than in other manufacturing areas such as automotive; here are two examples why:
- The aerospace industry has myriad government regulations with which it must comply.
- Aerospace parts and services often require greater attention to detail and precision than other manufactured items. In some respects, the aerospace industry is comparable to healthcare in that “close enough quality” is simply not acceptable. Read lesson to learn from Boeing 737 Max 9 Issue.
Reducing Waste in Processes
Whether used in the aerospace, automotive, or another manufacturing sector, according to the American Society for Quality there are seven types of wastes associated with lean:
- Transportation
- Inventory
- Motion
- Waiting
- Overprocessing
- Overproduction
- Defects
The end goal is to create work processes in which all production time adds value to a part or product. For the aerospace industry, two of the wastes—transportation and motion—are prime targets for initiatives that can lower operating costs and improve productivity.
What wastes are found in your organization? What new quality methodologies could you embrace that might lead to breakthrough improvement?