Critical Strategies for Improving Supplier Quality Management
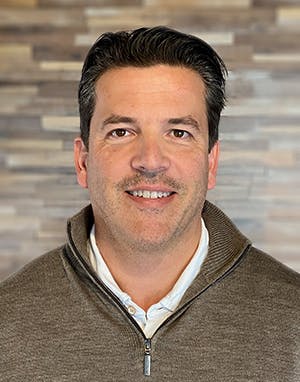
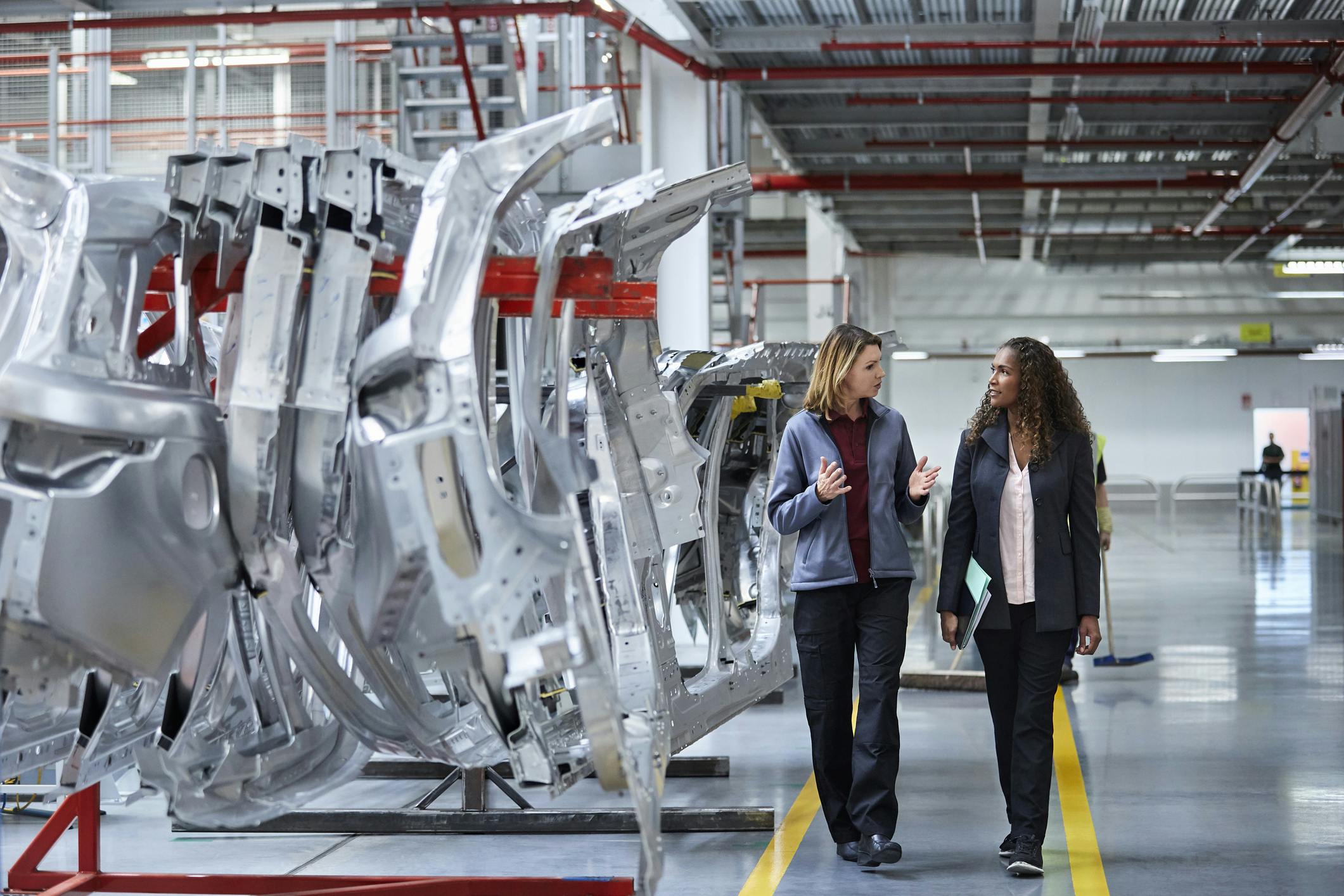
During the past 30 years, global manufacturing has evolved into a fast-growing network of overlapping supply chains, ever-changing regulatory requirements and complex operational demands. Consider that many automotive and aerospace manufacturers can have thousands of suppliers and other third-parties in their supply chain for any given product. As such, these and similar organizations are becoming more and more strained in managing and overseeing the quality, cost and timely delivery of raw materials and parts. It’s more critical than ever to have the right tools and systems in place to support those many different aspects.
What is Supplier Quality Management?
Supplier Quality Management (SQM) represents a critical business activity that focuses on monitoring, managing and responding to the dynamic nature of supplier quality. That includes factors like regulatory compliance, production quality and delivery performance. Ineffective SQM can be catastrophic to your business, negatively impacting your brand name and reputation, and creating legal and financial impacts that cannot be fully passed through to the partner at fault.
Strategies for Improving Supplier Quality Management
Manufacturers often spend so much time determining how they’re going to identify issues, which includes conducting spot checks and creating reports, that they miss problems until it is much too late. So what are some strategies to help? First and foremost, a robust supplier management system can help reduce the non-value-add distraction associated with operating the monitoring and reporting process. It also allows for a clearer focus on identifying issues and opportunities— and acting on them. Leveraging a system that supports layered process audits (LPA) can provide additional benefits by automating all quality and other audits via layered assessments that feature cross-functional reviews by several levels of managers for added assurance.
Here are some more specific strategies to consider:
- Measure and Track COPQ
There are many ways to measure and track supplier quality, but every one should include metrics that track scrap, rework, sorting and processing, warranty expenses caused by poor quality, and even product recall expenses.
2. Implement a Cost Recovery Process
The cost recovery process ensures partners can be held accountable for poor quality, and gives the company the ability to manage and minimize quality risks from suppliers.
3. Standardize Supplier Audits
A well-organized supplier quality management system rates suppliers on performance by way of audit scorecards that provide for benchmarking amongst “similar suppliers.” These scorecards measure the cost of quality, overall equipment effectiveness, percentage of production in compliance, on-time and complete shipments, and new products introduction.
By auditing the supplier on processes such as non-conformances in manufacturing, shipment, engineering change, invoicing, and quality, the companies can jointly identify corrective actions that will reduce supplier quality risks, and prevent them from reoccurring in the future. These corrective actions serve to remedy problems that stem from product deviations, nonconformance, out of specifications, quality incidents or customer complaints. Additionally, scorecards provide short- and long-term guidance that assist in the overall supplier relationship.
4. Utilize Closed Loop Corrective Actions
A closed loop corrective action properly identifies the root cause of the problem and ensures that problems get tracked and fixed in a methodical fashion that is auditable from end to end.
Where does Ease fit in?
Ease is a leading provider of process management software including Beacon, a powerful, yet easy-to-use cloud-based assessment platform, that can help organizations establish a robust SQM program and achieve operational excellence.