Finding Systemic Quality Issues: One Customer’s LPA Innovation
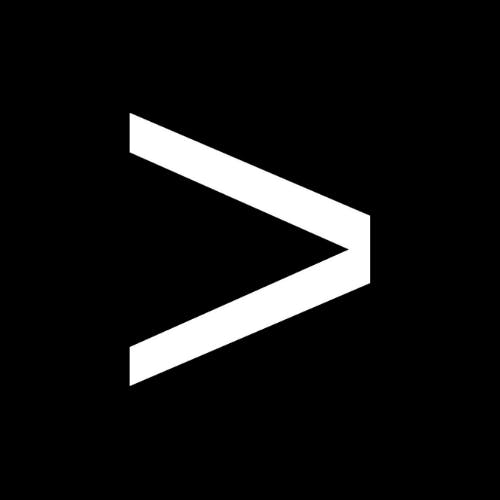
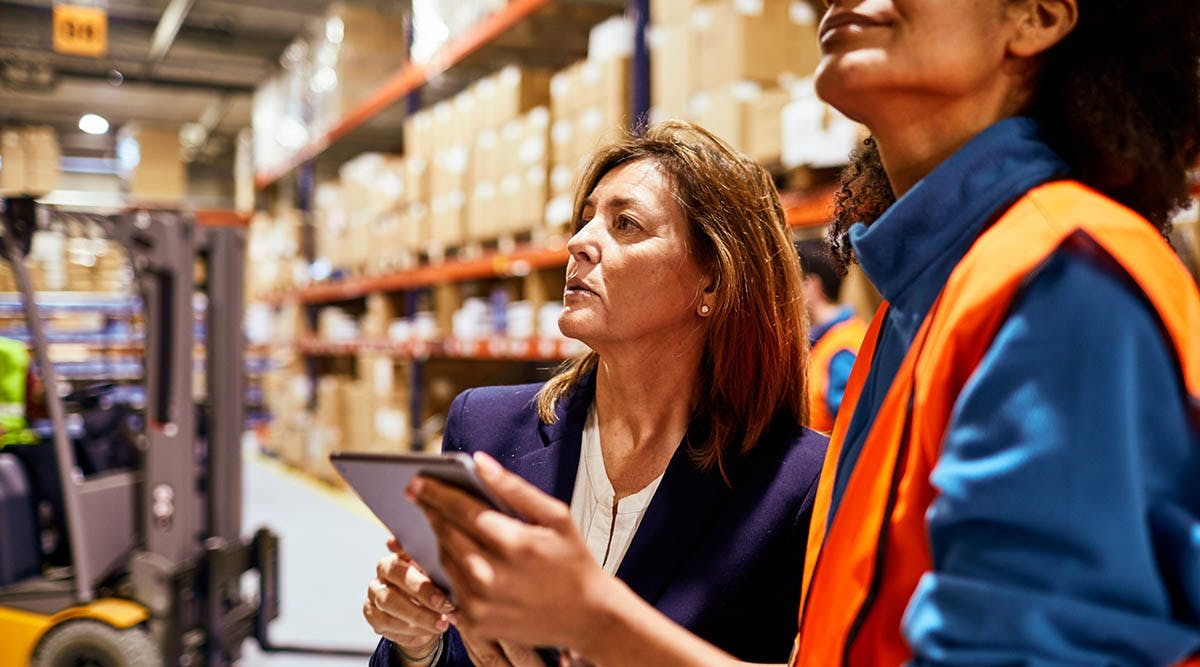
There’s a specific reason why automakers like Fiat Chrysler and General Motors (GM) require suppliers to conduct layered process audits (LPAs).
It’s because these quick daily checks ensure multiple layers of verification on high-risk process inputs, preventing defects at their source. But while many suppliers simply conduct them as a matter of compliance, the truth is they can drive far bigger results than just satisfying a customer requirement.
One EASE customer has developed an innovative approach to using LPAs to uncover and correct systemic quality issues faster, reducing quality escapes while driving continuous improvement.
While the example here is focused on identifying systemic quality issues, the same methodology could equally be applied to identifying systemic safety issues.
Here’s how they do it:
By using dynamic question banks, the team can immediately check all machines when an audit finding occurs, allowing them to pinpoint repeat issues and solve them quickly. Let’s look at how they set up these question banks, and the one crucial element you must have for this approach to work.
- Learn how to cut defects and costs while creating a culture of quality with our free 93-page eBook: The Ultimate Guide to Layered Process Audits
Step 1: Create Question Tags
The first step of this strategy starts with building your question library. As you create questions based on things like customer requirements, work instructions and previous problems, you’ll want to assign each one a tag or category such as:
- Equipment
- Process
- Material
- Quality
- Project sustainment
A final category tagged as Focus questions will also be used later—but not until you start conducting your audits.
Step 2: Conduct Layered Process Audits
This step involves conducting audits as usual, rotating and randomizing questions from the categories you established in the first step.
Using question banks in this way is simpler when using an automated LPA platform like EASE, since it allows you to quickly generate checklists that draw from multiple question tags. You’ll want to make sure checklists are specific to the process, machine or work area, rather than using generic checklists across the plant.
Step 3: Launch Focus Questions
Whenever a question on one piece of equipment fails, next steps are to:
- Temporarily change the question’s tag to a Focus question
- Add that Focus question to all LPAs for the same equipment type for the next four weeks
- Ask the Focus question on every audit and shift and piece of equipment
What that means in practical terms:
If you identify a finding on Monday at third shift, by the first shift on Tuesday you’re looking across all similar machines to see if the problem is happening elsewhere.
The result is you’ll be able to quickly see whether the nonconformance is an isolated incident or systemic problem. Instead of just hopping from finding to finding, correcting one-off problems, your focus will be on widespread issues that add up to a bigger impact on quality. This allows you to find and fix problems that could cause large quality escapes.
Again, mobile audit software is a key enabler of this approach, giving companies the ability to make custom changes to audit checklists immediately, rather than having to recall, rewrite and redistribute paper checklists.
Step 4: Focus on the Vital Few
It’s critical to note that the total number of focus questions must be small for this strategy to work. For instance, while the EASE customer that developed this method may have 15 questions in each standard question category, they don’t have more than two focus questions at a time.
The Pareto principle or the 80/20 rule tells us that 80% of outputs are the result of 20% of inputs. It’s why Lean and other process excellence methodologies emphasize the concept of focusing on the “vital few,” rather than getting distracted by the “trivial many.”
In this context, an oversized list of Focus questions is going to either make audits too long or prevent you from verifying critical-to-quality items from other question tags. Restricting Focus questions to the vital few ensures you can achieve both a large volume of audits and broad coverage of key standards.
Other Benefits of Dynamic Question Banks
Using dynamic question banks in this way has helped the customer achieve several other benefits in addition to correcting systemic issues faster. These include:
- Helping with root cause analysis: Flipping on Focus questions related to known problem causes can help quickly get to the root of issues by providing insight into what’s actually happening on the plant floor.
- Improving documentation: Focus questions can help highlight when systemic problems are related to documentation issues, for example if work instructions need updating.
- Communicating about quality: Focus questions help quickly raise awareness about quality issues that all operators needs to be aware of. The customer also achieves this by launching all new LPA questions as Focus questions.
Getting maximum return for the time and effort involved in LPAs requires a strategy that looks at the bigger picture—not just fixing individual problems that pop up. Using audit findings as opportunities to find bigger problems is the key to continuous improvement, preventing defects from reaching customers while promoting quality culture in your organization.
- Whether you’re new to quality or are a quality industry veteran, our free 93-page eBook will help you level up on your LPAs and plant floor quality: The Ultimate Guide to Layered Process Audits