How Layered Process Audits Ensure Quality and Safety During a Crisis
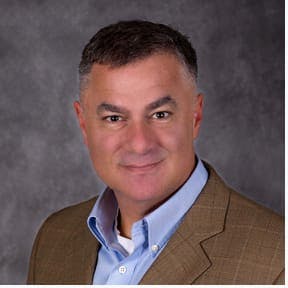
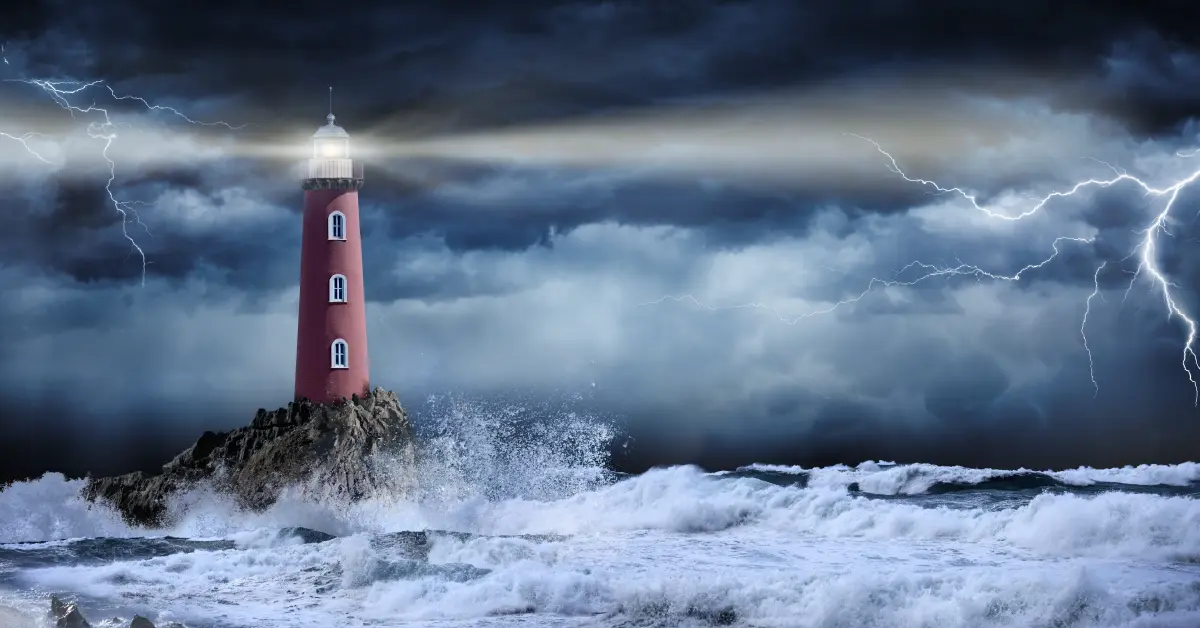
The past two years have been a roller coaster for manufacturers, who have met challenges including production shutdowns, staffing shortages and supply chain bottlenecks.
When faced with a crisis, the ensuing time crunch tempts many people to take process shortcuts to meet production deadlines. The result, however, is increased quality and safety risk—with the potential to make a difficult situation worse.
The most effective way that we know of to maintain process discipline is to conduct layered process audits, which provide frequent checks and added layers of verification to detect and prevent quality and safety issues.
Here we explore how layered process audits (LPAs) help ensure quality and safety during a crisis, and why second- and third-level audits are paramount.
Get our free Ultimate Guide to Layered Process Audits for top tips and best practices for getting the most from your LPA program
The Paradox of Crisis Management
Here at The Luminous Group, we find that anytime a plant is behind on delivery, a quality problem is likely to follow. Whether it’s a machine down, a parts shortage or even a scheduling error, it’s human nature to cut corners when trying to get a shipment out without missing a deadline.
So what’s the solution to prevent these problems? It’s quite simple. In these situations, you need to pay more attention to quality, not less, using LPAs to add layers of verification and identify where people aren’t following the process.
If you don’t, the result could be bigger problems than a late shipment. Consider, for example, the outcome of shipping non-conforming parts to a key customer in the rush to meet delivery deadlines. For automotive suppliers, the cost can run as much as $10,000 per minute should the problem cause a production shutdown at the vehicle manufacturer’s assembly plant.
The lesson here is that you need to slow down to hurry up. The Navy SEALS have a saying, “slow is smooth, and smooth is fast.” During critical missions, rushing and missing something can cost lives. While it may sound counter-intuitive, being extra careful during a crisis is what will allow you to come out the other side unscathed.
Why Layers 2 and 3 Are Critical
During a crisis, layer 2 and layer 3 LPAs become more important than ever. Layer 1 auditors are usually the first line of defense against quality issues, but during a crisis, these supervisors tend to sub-optimize their priorities and skip their verifications.
Normally, they would have multiple priorities, including safety, delivery, quality and cost. In a crisis, delivery becomes the only priority, with cost, quality and safety no longer optimized.
That’s where plants get into trouble. When it happens, someone can get hurt, you may produce bad parts and spend way more money to do it. If you are relying on a dock audit to find defective parts, it’s too late. Instead, you need to audit the process to identify problems upstream—at the source of the problem.
Getting Leadership Involved
When you find yourself in a time crunch, we recommend having upper management conduct some ad-hoc audits in addition to any regularly scheduled audits. If it’s a big enough crisis, you’ll likely have people from corporate onsite, and these audits can give them something to do to help. Their audits reinforce that even when resources vary, it’s important to follow all standards, settings and process requirements.
If you’re using an automated LPA platform like EASE, you can easily create an ad-hoc audit that’s not on the schedule. You might also look to use tags to rotate in questions focused on key process steps, previously identified quality issues and machine settings.
It’s important to note that LPAs aren’t just for identifying defects, but to find any situation where the process isn’t being followed to the stated requirement. An example would be if an operator increases the plating thickness on a part in an effort to avoid quality problems amid a delivery crisis. Depending on the metal used, this situation could send costs soaring, highlighting the need for extra eyes on the process.
LPAs are a key tool for holding standards in place when a crisis hits and you’re rushing to meet delivery timelines. Upper management has a crucial role to play, providing additional layers of verification at a time when quality is most likely to falter. Companies that can steer the ship safely will find not just lower quality costs, but also the confidence to weather any storm.