How Layered Process Audits Support Toyota Production System Principles
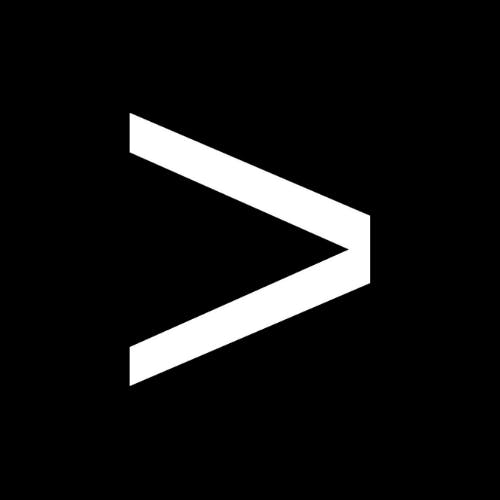
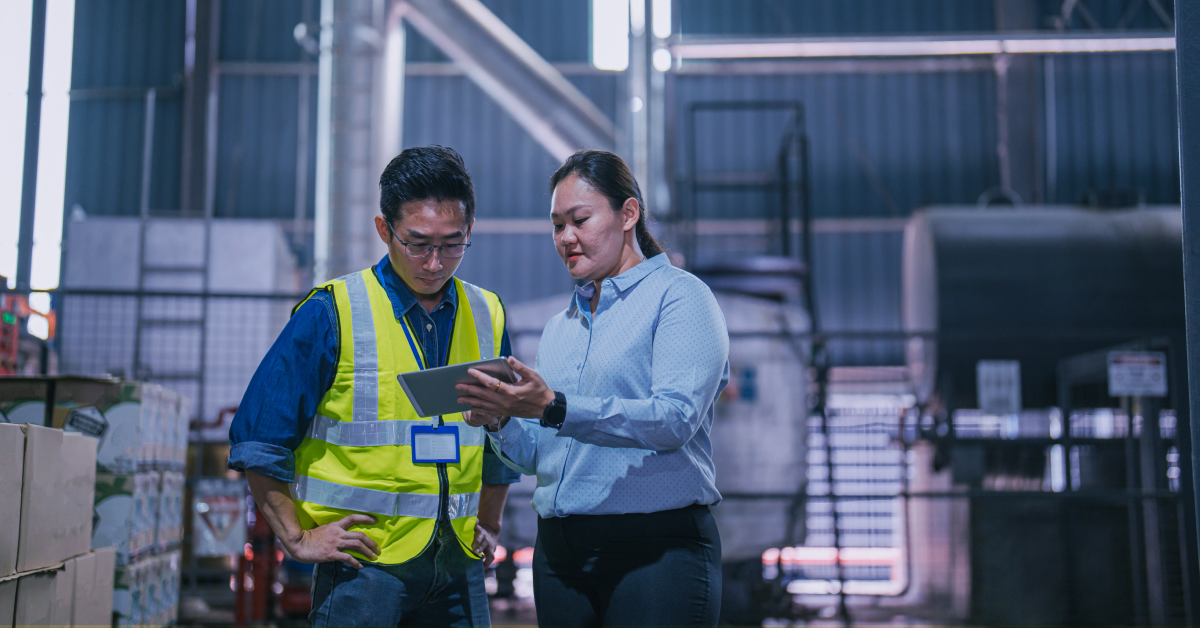
In “The Toyota Way,” author Jeffrey K. Liker outlines the principles of the Toyota Production System (TPS), largely credited with making the company a leading competitor in the global automotive industry.
The book has sold more than a million copies and has been translated into 26 languages since its publication in 2004. Today, it remains as relevant as ever for manufacturers looking to minimize defects and maximize productivity.
Let’s take a look at how layered process audits (LPAs) support the principles of TPS, aligning with the Toyota philosophy to help achieve some of its most important goals.
Download our Ultimate Guide to Layered Process Audits for 93 pages of LPA tips, tricks and strategies
What Is the Toyota Production System (TPS)?
The Toyota Production System (TPS) is a management system that focuses on the elimination of waste. A forerunner of Lean Manufacturing, TPS was developed by company president Eiji Toyoda and engineer Taiichi Ohno during Japan’s post-World War II quality revolution. The philosophy is based on founder Kiichiro Toyoda’s earlier principle of just-in-time production.
Core Toyota Production Principles
TPS is centered on the principles of jidoka and just-in-time production. Loosely translated as automation with human intelligence, jidoka refers to manually built processes that stop automatically when an abnormality is found.
Just-in-time production evolved as a concept for eliminating waste and delivering vehicles as quickly as possible while holding minimal inventory. Reducing waste and inefficiency focuses on eliminating the 3Ms:
- Mura (unevenness): When workloads aren’t level, you’ll have overproduction or waiting.
- Muri (overburden): When employees or equipment are subject to unreasonable requirements, problems occur.
- Muda (waste): Muda is itself a result of Mura and Muri, and consists of seven categories.
Muda covers seven categories of non-value added activities that include:
- Excess transport of product
- Wasted goods and materials
- Excess movement, whether of machines or people
- Waiting
- Overproduction
- Over-processing
- Defects
How LPAs Support Jidoka
At the heart of jidoka is creating processes that automatically stop when an abnormality is detected. This helps reduce waste and downstream defects, while also reducing risks to people and machines and allowing for better problem-solving.
LPAs support the concept of jidoka by providing a mechanism for finding those abnormalities. Whether an issue with a process nonconformance or a machine with the wrong settings, LPAs give you the chance to find issues and intervene before they result in production defects.
Key areas of focus here include using LPA questions to verify:
- Error-proofing devices
- Equipment settings
- Compliance with standardized work
Continuous improvement of processes is essential to achieving jidoka, another area where LPAs provide value. By identifying issues and process nonconformances, LPAs promote continuous improvement and allow processes to run more reliably.
How LPAs Support Just-in-Time Production
Toyota refers to just-in-time production as “making only what is needed, when it is needed, and in the amount needed.” By bringing quality leaders to the plant floor to observe processes, LPAs help highlight areas where Mura, Muri or Muda may be creating waste or inefficiency.
For example, a plant manager conducting an LPA might identify a bottleneck in the process resulting in one workstation waiting and one continuously running behind, an example of Mura. LPAs also make it easier to see when people or machines are overtaxed (Muda), which can result in injuries or equipment downtime. One-on-one conversations with operators can help identify problems, which is one reason why LPAs should include open-ended questions that solicit feedback from employees.
LPAs are known for reducing production defects by identifying process noncompliances. However, questions can be targeted to all of the seven wastes, and it should be clear to all participants that the purpose of LPAs is to improve processes overall.
Equipment reliability is also a huge part of just-in-time production. LPAs help minimize downtime with questions targeted at machine settings, condition and verification of operator-based maintenance tasks.
Using LPAs in the Context of TPS Tools
LPAs support a wide variety of other TPS tools and principles, including methods such as:
- Kaizen or incremental improvement: LPAs help identify small changes that add up to continuous improvement, both in terms of process standardization and getting insights from front-line employees.
- Genchi genbutsu or going to see: LPAs get people to the gemba, which translates to where the work is done. Seeing processes in person is essential to the TPS approach, and LPAs support this by having people observe processes on the plant floor.
- 5S: LPAs can be used to verify elements of 5S checklists, helping ensure the workplace is designed to promote quality.
- Poka-yoke or error-proofing: Verification of error-proofing devices is an important part of LPAs. Using LPA questions to see whether poka-yoke devices correctly identify a red rabbit provides confidence that the system isn’t letting abnormalities slip through.
For companies that aspire to Toyota’s reputation for efficiency and quality, LPAs are a useful tool to verify that the principles are being followed on the plant floor. Digital LPA software like EASE helps by putting audit results front and center, making it easy to spot areas that could be contributing to waste and poor quality.
At the end of the day, TPS is more than just a set of tools or strategies. It’s a philosophy based on respect for people and their work, a guiding principle of LPAs that’s also foundational to creating a culture of quality.