How Many Layered Process Audits Should You Be Doing
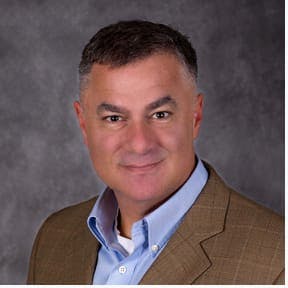
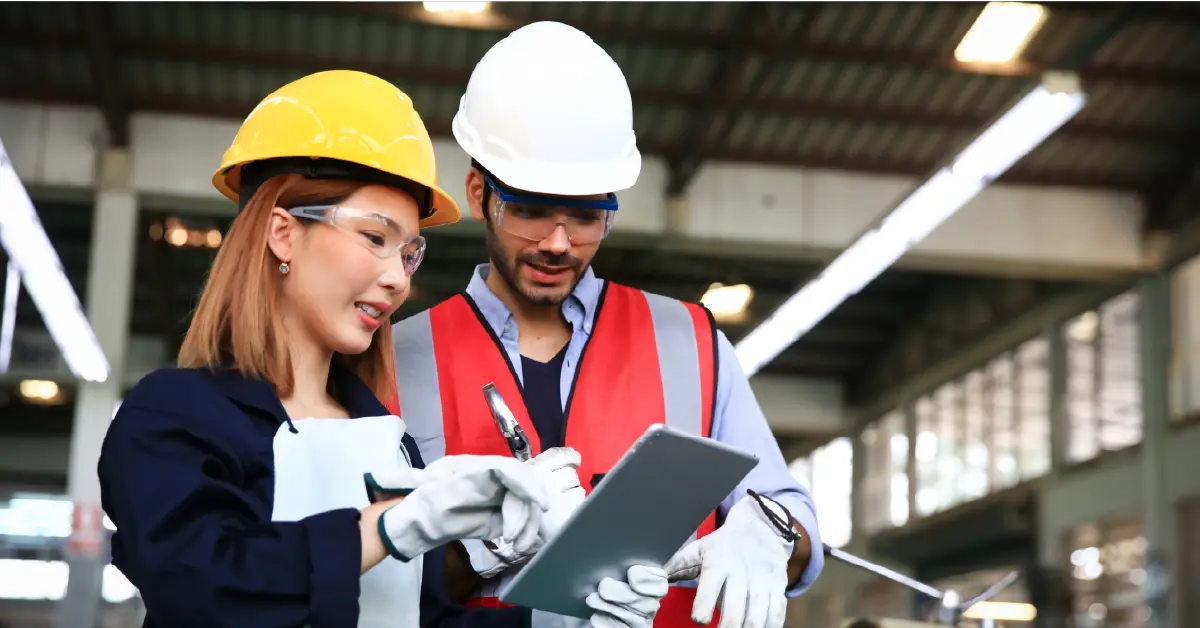
Layered process audits are fast, frequent checks of process inputs that identify deviation from the established standards to reduce product variation and improve customer satisfaction. The key element here is frequency, providing more data, more visibility into risk and the ability to step in quickly before non-conforming products are made.
The challenge is that frequency can mean different things at different plants. Some plants conduct hundreds (or even thousands) of checks each year, while others conduct many less.
In this article, we look at some considerations for determining the right audit frequency in your plant. We also present a new way of thinking about audit frequency to make your LPA system more effective and a driver of improvement.
Download your free Ultimate Guide to Layered Process Audits for more LPA question best practices, examples and tips
Basic Expectations
The layers in layered process audits refer to the different levels of management participation in the audit program. From a best practices approach, we at The Luminous Group recommend plants aim for the following three layers:
- Layer 1 supervisors and team leaders should conduct at least one audit every shift they work
- Layer 2 engineers and employees from other departments should conduct at least one audit weekly
- Layer 3 managers should conduct at least one audit monthly
The idea is that layer 1 supervisors should catch most issues, since they are closest to the process. Layers 2 and 3 help verify that layer 1 isn’t missing problems and complies with scheduled audits. It’s also worth noting that layer 2 often created and troubleshoots the process, while layer 3 adds to a culture of communication and feedback.
Plant size will affect what this looks like in practical terms. For instance, if you have design engineering staff onsite, you will have more people available to conduct layer 2 audits. Conversely, if you have a large plant with only 50 support people among 400 employees, achieving a high number of layer 2 audits will be more of a challenge.
Keeping Audits Short
Being able to complete a higher number of audits relies on people being able to perform them quickly. Audits should take roughly 10 minutes, no more than 15 minutes max, to complete. Short audits can focus on what’s most critical and are less likely to be postponed or ignored.
If they’re taking longer than 15 minutes, that means you need to review your questions and audit structure to reduce the load on employees. Questions should be concise and have clear evidence so people can answer them easily.
Aim for Broad Coverage
Let’s say a supervisor in your plant is responsible for 10 work cells. It’s not practical to have them spend over 90 minutes a day auditing, but it’s also critical not to skip work cells.
Rather than thinking about how frequently people are conducting audits, you should think about how frequently each work cell is audited. For example, instead of asking 10 questions at one work cell each day, it would be better to ask one question daily or even two questions every other day at each work cell. Again, focus on the few things that are more critical, or most likely to be nonconforming or out of place.
The reason is that if you’re only checking a given cell once every 10 days, you lose the value of LPAs detecting change quickly. That’s when problems can slip by, leading to defects and complaints. So while rotating audits among work cells may seem logical, it ultimately defeats the purpose of LPAs.
The same applies when considering layer 2 engineers who conduct audits once a week. You don’t want to cover just one work cell and not get to the tenth location for three months. What you want to ensure is that people get to every work cell often, making problems more visible so you can catch problems faster.
Rotating and Randomizing Questions
Many plants we work with start by using a fixed set of questions, meaning many cells get skipped when the questions don’t apply. Using LPA software like EASE can help avoid this problem by letting you tag questions by work cell and randomize them within the audit.
This approach ensures each checklist is specific to the work area so questions don’t get skipped. It also lets you keep audits short so you can cover more work cells more frequently.
Ultimately, the biggest thing to remember is that frequency is relative. Just because a supervisor does an audit every day doesn’t mean that each work cell is audited frequently. For LPAs to achieve their purpose, teams must orient their thinking towards the coverage each cell gets, rather than how often people conduct audits.
Ask yourself how would you feel if your manager only came to see you every 10 weeks and then took up a lot of your time when you were busy. Wouldn’t it be easier if he stopped by often to see how you were doing, listened to your job concerns and only took a few minutes of your time? He would know right away if you had a problem and could start helping you with it.
Don’t let your auditors be the first type of manager. Get them to every work cell, even if only for a short visit each time. That’s how you keep your finger on the pulse of the plant and drive value from your LPA system.