How Mobile Audit Tools Accelerate AIAG's Quality Road Map
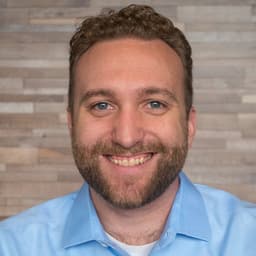
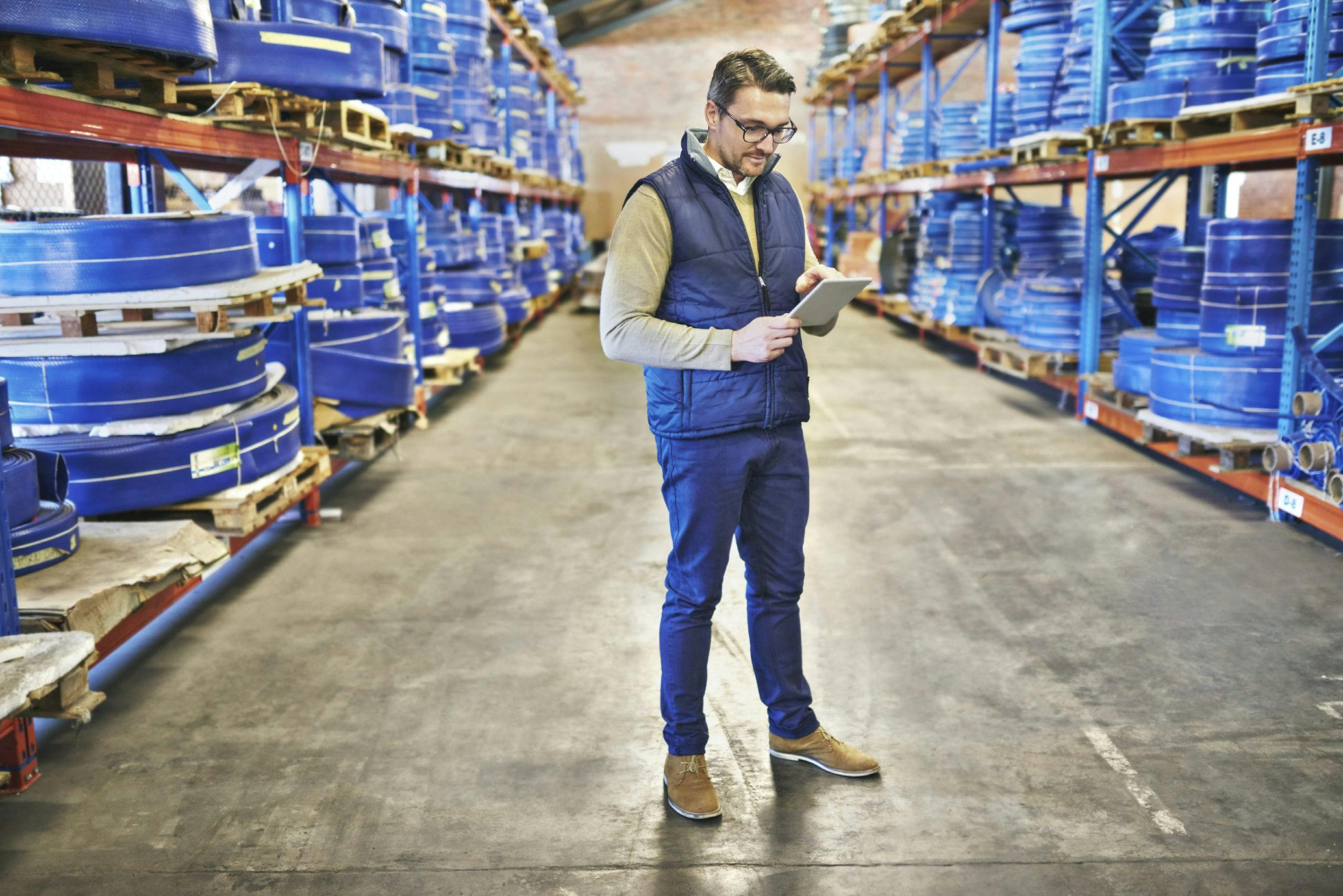
The Automotive Industry Action Group (AIAG) has many resources for companies focused on continuous improvement, represented as a set of key checkpoints on its Road Map to Quality Success.
While it looks like a simple set of steps, the path isn’t necessarily straightforward. Each step is a process in and of itself, but there is one common tool that will help you get from point A to point B: audits.
Today we’re looking at how audits, and specifically mobile audit tools, can help accelerate your progress towards quality goals.
Core Tools
AIAG’s Core Tools are the first step on the road to quality. These tools include many famous quality acronyms:
- Advanced product quality planning (APQP)
- Statistical process control (SPC)
- Production part approval process (PPAP)
- Failure modes and effects analysis (FMEA)
- Measurement systems analysis (MSA)
Audits provide a key support for these tools in areas such as:
- Generating data for failure mode analysis
- Verification and control of high-risk processes
- Understanding sources of variation when investigating SPC issues
Mobile audit tools provide an especially useful snapshot of plant floor processes related to these areas, compared with trying to analyze details recorded later from a desk.
Layered Process Audits
Layered process audits (LPAs) are a core requirement for suppliers to General Motors (GM) and Fiat Chrysler, and are also a recommendation for Ford suppliers. LPAs check high-risk processes multiple times daily, with different layers of the organization participating based on their level in the company.
Obviously, the paperwork associated with multiple daily audits across various work areas can add up. Companies using paper-based audits often have a huge backlog of checklist data and outdated checklists. In most cases, they also rely on overly generic checklists.
Mobile audit tools improve the efficiency and effectiveness of LPAs by allowing you to:
- Reduce administrative burden of LPAs by up to 85%
- Rotate and randomize questions to check specific problems or work areas
- Time audits and verify audit location to protect audit data
- Analyze real-time audit data to identify sources of variation and areas for improvement
Problem-Solving and Corrective Action
AIAG promotes corrective action via the 8D problem-solving method, an 8-step approach that includes planning and analysis, containment actions, corrective and preventive action.
Where can mobile audit tools accelerate problem-solving? Let’s look at several specific steps:
- Defining the problem: When you find a problem during an audit, you can upload a photo to the audit record rather than having to describe it in words. This is more effective at helping the person who reviews it understand the problem right away.
- Implementing corrective actions: A robust mobile auditing tool will allow you to link non-conformances to mitigations or corrective actions. In addition to assigning follow-up, you’ll have a clear paper trail for tracking corrective actions.
- Validating corrective and preventive actions: Once you’ve implemented corrective action, you can add new audit questions to verify it worked and that you’re holding the gain.
16949 Certification
IATF 16949:2016 expands requirements around internal audits and supplier audits. Certification now requires manufacturers to demonstrate compliance with customer-specific requirements, which include layered audits for several automakers.
What this effectively means is that, for most suppliers, LPAs are more than just an AIAG best practice—you’ll actually need to do them to maintain certification.
Mobile auditing tools can help you accelerate your IATF certification by helping you:
- Implement and track results of LPAs
- Boost completion rates to avoid non-conformance findings
- Document that you’re using audit results as intended
Special Process Assessments
AIAG publishes guidance documents for special process assessments to help develop management systems for:
- Heat treating
- Plating
- Coating
- Welding
- Soldering
- Molding
- Casting
These guidance documents provide a detailed approach for systematically assessing critical processes to reduce defects. Using mobile audit tools, you can create questions for key elements like high-risk process steps or verification of previously failed items.
All in all, this means you’ll get more value from special process assessments, helping you make quantifiable improvements rather than just completing a single assessment.
Change Management
Effective change management is a hallmark of operational excellence. That’s why AIAG provides specific guidance for streamlining changes to products and processes.
Mobile audit tools are particularly helpful in helping validate that key process changes are in place and working correctly. You can easily add questions for any department or work area with updated processes, so you can get first-hand feedback on how changes are working.
Managing Warranty Claims
The final step on AIAG’s Road Map to Quality Success is warranty management. Like many of the steps, this one is aimed at reducing defects while improving customer satisfaction.
One way to get more from your warranty management processes is to use mobile audits to close the loop on customer complaints, newly identified failure modes and internally identified defects.
What makes a mobile audit platform especially powerful is that you can take critical elements from each phase discussed here and make them part of ongoing, daily checks.
And that’s the real power of mobile audits: integrating quality goals into a daily routine that becomes embedded in your organization’s culture as a whole. When you’ve done that, you can be sure you’re on the road to quality.