How Tier 1 Automotive Suppliers Can Use 5S Audits
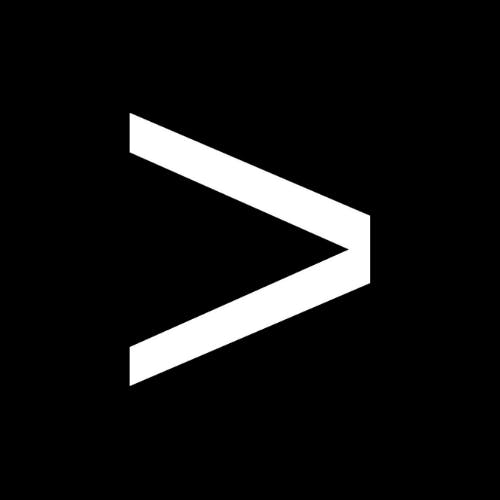
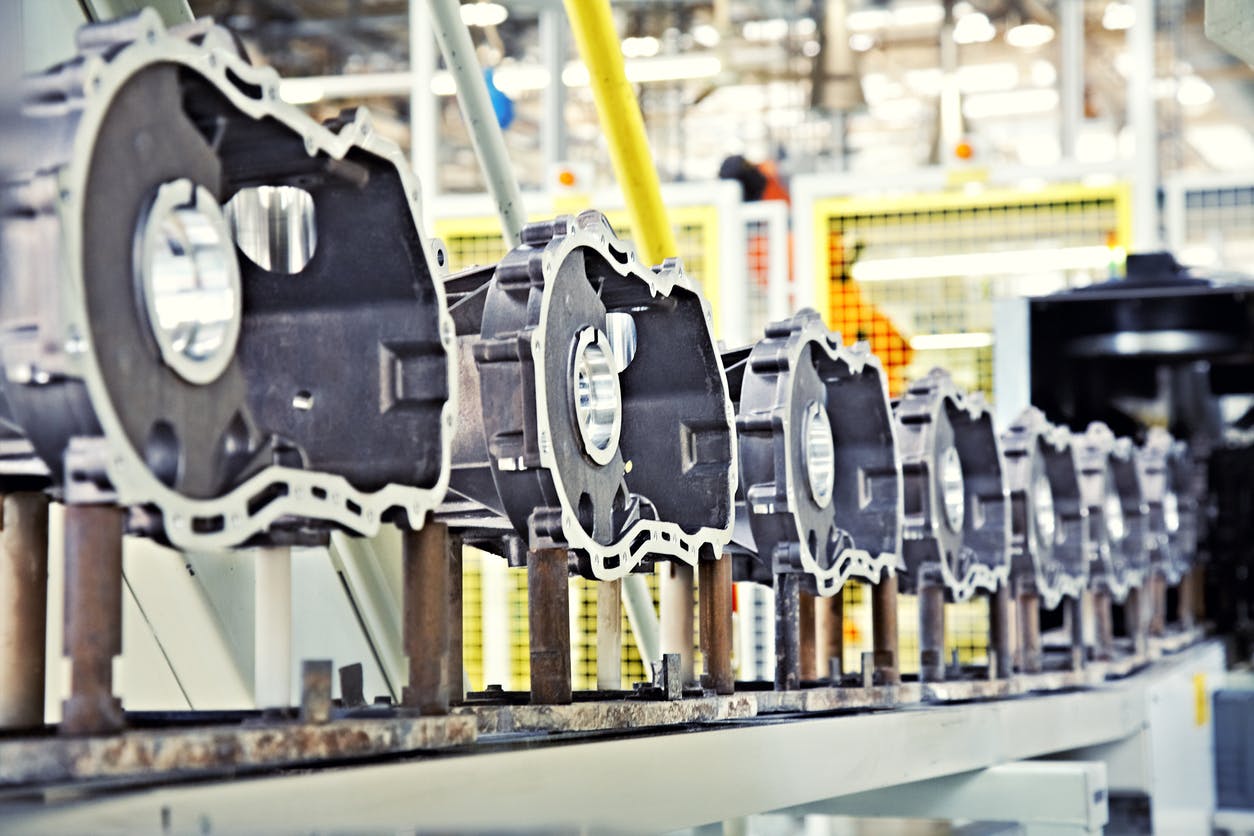
Who doesn’t like a clean workspace?
Your job is to deliver the correct parts to the correct place at the correct time—efficiently and consistently.
Cleaning, organizing and standardizing your plant and office helps you accomplish this because a clean, organized and standardized workplace builds efficiency and consistency. Picture in your mind the difference between a clean and a messy work place and you know what we mean.
Implementing 5S will improve your workplace and your profits. 5S stands for:
- Sort
- Straighten
- Shine
- Standardize
- Sustain
Since 5S auditing was invented, people have added three more “S’s”: Safety, Security, and Satisfaction. Safety is always a top priority; nothing lowers moral like an injury on the job. Concerns about security have increased exponentially since the inception of 5S auditing in the 1940’s. And satisfaction is multi-tiered: satisfaction for plant owners, stakeholders, business partners, customers, and employees.
But the basic 5S audits remain the same. Best results occur if you perform these steps in order.
Sort
In this basic first step we separate the necessary from the unnecessary. The members of an automotive shipping or packaging area determine as a team what objects they are going to remove, retain, or store to make the area more efficient. Team members “red tag” items as they sort through them so they can discuss each item’s fate. In the plant, this means junk, refuse, broken equipment, and prototypes. In the office, it means out-dated computer hardware, broken furniture and old documentation. If the team is unsure of what to do with any items, place them in a special area for later consideration.
Sorting is not limited to objects. It also means improving safety and efficiency. Are work instructions available and up-to-date? The team can identify broken safety devices and remedy them, repair non- or poorly-operating electrical and mechanical devices, and remove clutter.
While the team is sorting, it may come up with new proposals to improve their areas. Great—document these ideas for further discussion within the team.
Straighten
It is essential, especially in the plant, that work areas are arranged for top efficiency. Place the parts, tools, and packaging materials team members use the most in prominent areas and reserve space farther away for those the team uses less frequently. Organize areas so that tasks flow following the easiest routes. Organize the team members themselves in the station for the most efficient movements and logical coordination.
Use correctly sized Kanban containers for parts and tools, the correct equipment for the workstation’s job, and quick-change handles when appropriate. Employ shadow boards for tool and equipment storage.
Shine/Scrub
Clean and organize work areas so they are not just clean but shining for maximum performance and usability. Sweep and clean floors. Degrease and polish surfaces. Repair leaks. Paint surfaces and equipment where needed using light-colored paint so any leaks are obvious and so they can be repaired sooner. Install improved lighting and replace burned out light bulbs. Update warnings and postings so team members have the most current safety and job information. Put desks, storage units, and work benches on casters for easiest moving and cleaning. Retractable hoses and electrical cables make the area look neat.
In the office, vacuum the carpet; dust and clean all surfaces. Replace worn carpeting.
Standardize
The workstation looks and feels great if the equipment is standard within the station and with the other stations in the facility. Use the same style lighting, storage units, workbenches, shadow boards, desks and chairs. Arrange furniture and equipment in offices and workstations similarly, if practical and possible.
Sustain
The plant and offices operate best when it is always orderly and clean—not just on Fridays or on inspection days. The team can assign each office or work area member a specific responsibility and make sure him or her remains accountable for that job. The team can also appoint a member to conduct audits after the initial organizing, cleaning, and arranging so that the momentum continues. Make sure the auditor documents the 5S audit so members can monitor the process easily with charts and graphs as well as statistics. Publish results, making them visible and available to the team, perhaps posting them in workstations and break areas and certainly including the results and talking about the benefits at team meetings.
Efforts towards implementing 5S auditing improve over time. Key obstacles to effective implementation include too little standardization (the fourth “S”), management resistance to actual 5S auditing even though management is receptive to the concept, not enough time spent in training for an effective 5S audit, and lack of effective benchmarking.
Tier 1 automotive suppliers can benefit in many ways from the correct implementation of a 5S audit. This includes improved efficiency, faster and more accurate order filling, better packaging, and ultimately a more successful and profitable company.
The best part might just be that most components of the 5S audit are simple, common sense, and do not cost much. The second-best part is that the audit just might make everyone feel better.