How to Improve Hazard Identification with Layered Safety Audits
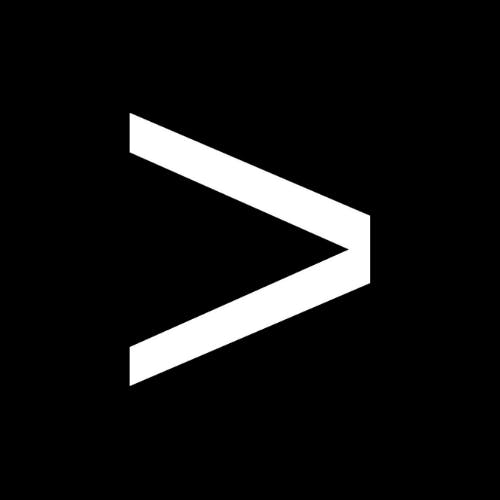
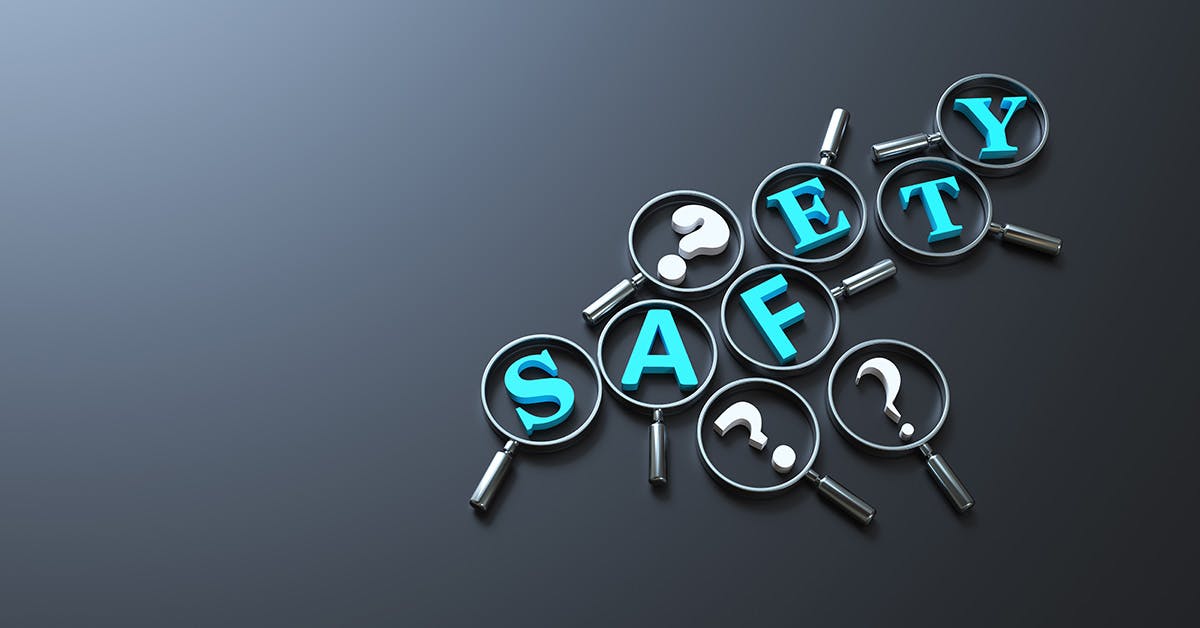
According to the National Safety Council, the average cost of a medically consulted workplace injury totals $42,000 in lost wages, medical and administrative costs.
More than just dollars and cents, however, safety incidents can change a person’s life forever, while some workers never make it home at all.
The biggest tragedy of all is that every single workplace injury is entirely preventable.
That is, if you recognize the hazards and take appropriate action to eliminate or mitigate them.
Layered safety audits are one way that manufacturers are taking a more proactive approach to hazard identification, which is central to risk management, behavior-based safety and more.
Below we examine the importance of hazard identification in safety management, what makes layered safety audits unique and how do they align with regulatory guidance for safety programs?
Get free ideas for behavior-based safety questions
What Are Layered Safety Audits?
Layered safety audits or inspections are high-frequency safety checks that involve multiple levels of the organization in hazard identification. Layered safety audits promote a culture of safety through management participation and frequent face-to-face discussions about safety.
Compared with annual safety audits or even targeted semi-annual checks, layered safety audits are much more frequent, with some companies verifying safety items on a daily basis.
Layered safety audits or inspections can focus exclusively on safety, or they can be incorporated into daily quality checks of plant floor processes. Some companies may include one to three safety-related questions in layered process audits.
How Layered Safety Audits Promote Hazard Identification
Layered safety audits provide daily opportunities to identify hazards on the plant floor. Using an automated platform to conduct layered safety audits makes hazard identification more effective, making it easier for teams to:
- Document, track and eliminate safety risks by putting more eyes on the process
- Analyze trend data to find patterns in location or type of hazard, as well as changes over time
- Mitigate similar hazards in other areas of the plant or organization
- Implement corrective actions that reduce risks to workers
- Ensure compliance with safety regulations and standards
Hazard identification is critical to creating a culture of safety where everyone is aware of safety issues and takes ownership of problems they see. That could mean moving an electrical cord that someone could trip on, alerting a supervisor to a machine guarding issue that needs attention from maintenance, or otherwise taking action on unsafe situations that are observed.
Getting workers to be proactive in this way only happens when identifying hazards is a daily habit—something that layered safety audits encourage. What’s more, they ensure management is visibly involved with safety, which is another crucial element of building a culture of safety.
They also demonstrate the genuine commitment to employee safety needed to build a culture of safety
How Layered Safety Audits Support OSHA Hazard Identification Recommendations
Hazard identification is a central component of U.S. Occupational Safety and Health Administration (OSHA) recommendations for safety programs. Layered safety audits support all the core elements of OSHA’s Recommended Practices for Safety and Health Programs, including:
- Management leadership: By definition, layered safety audits involve leaders in verifying plant floor safety measures.
- Worker participation: These checks focus on one-on-one conversations with operators, soliciting feedback and encouraging them to take ownership of safety.
- Hazard identification and assessment: Layered safety checks put more eyes on the process, catching more compliance issues and hazards that can lead to incidents.
- Hazard prevention and control: Layered safety audit questions can include verification of previous corrective actions to ensure change is sustained and people aren’t falling back on old habits.
- Education and training: More frequent checks and conversations about plant floor safety keep hazard recognition front and center for operators and other employees.
- Program evaluation and improvement: Using a digital platform like EASE to manage layered safety audits provides data for tracking safety performance over time.
- Communication with contractors: Temporary workers can introduce significant risk into a plant. Layered safety checks allow you to more closely monitor whether they follow safe practices.
At the end of the day, the value of hazard identification goes beyond saving money on workers’ comp claims and lost productivity. Instead, it’s about protecting the people who rely on you. Taking a proactive approach involving multiple layers of verification makes it harder for problems to go unnoticed, helping prevent injuries while fostering a culture of safety.