How to Use Custom Tags to Make Layered Process Audits More Effective
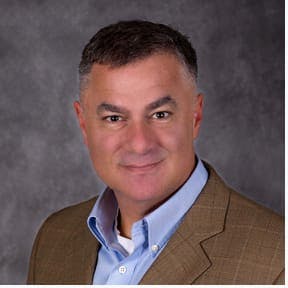
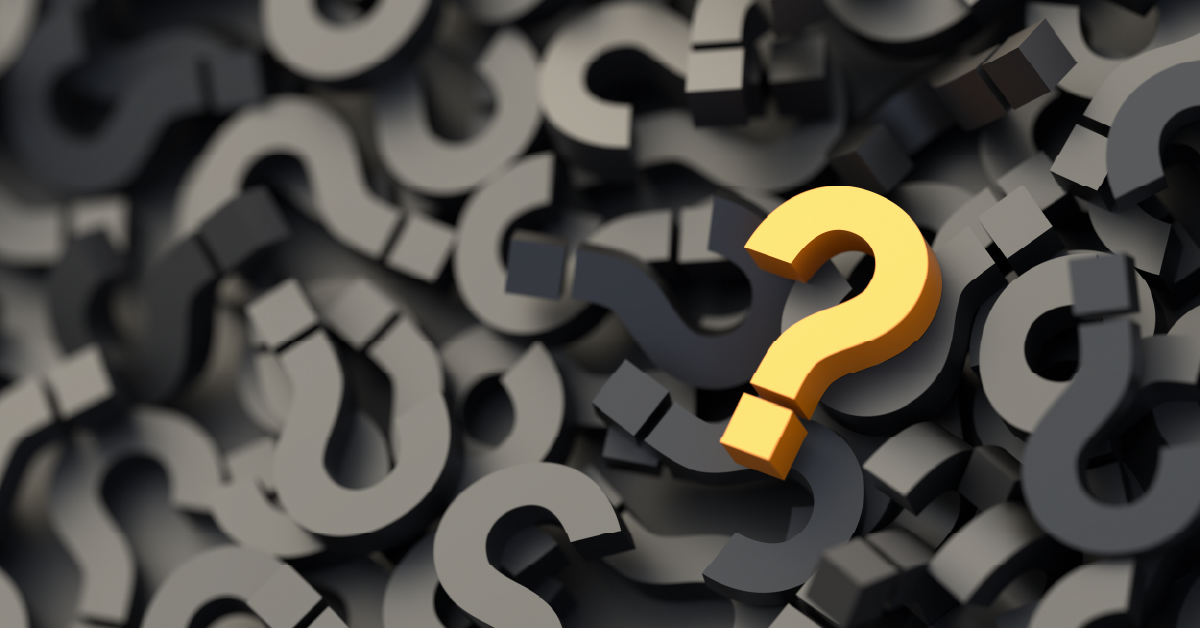
The cardinal rule of layered process audits is that they should be short and fast, lasting roughly 10 minutes. The problem is, that only leaves room for about 7-10 questions per audit—not much time to cover everything from customer complaints to safety to process-specific standards.
How can plants cover more ground in less time while also getting detailed data on process-specific risks? The answer is with custom question tags.
For companies using layered process audit (LPA) software like EASE, we at The Luminous Group recommend using custom tags on questions that are then rotated within checklists. The rotation of many questions ensures ongoing verification to identify non-conformances that cause defects, resulting in broader coverage of standards without overloading auditors.
Today we’re looking at the advantages of using this strategy, common tags we recommend using, and how to distribute checklist questions among those tags.
Download your free Ultimate Guide to Layered Process Audits for more LPA question best practices, examples and tips
Advantages of Using Custom Tags for Layered Process Audit Questions
Creating custom tags for grouping your LPA questions provides several advantages compared with using a single pool of uncategorized questions. These include:
- Reducing N/A responses: Generic checklists often have questions that are not applicable (N/A) to the process area, which are essentially wasted questions.
- Improving coverage of audits: Using custom tags helps you cover a larger spectrum of manufacturing process elements that cause variation.
- Reporting by tag: Using custom tags lets you see, for example, if you have systemic issues related to one of the 6Ms. This allows you put in place corrective actions for the specific process and then leverage corrective action to address systemic issues across the plant.
Which Custom Tags Should You Use for Layered Process Audit Questions?
Using tags with your LPA questions requires some basic planning. They can’t just be random, where people keep throwing more tags on the system, without it becoming chaotic.
We recommend manufacturers focus on the following key places to group tags together:
- Process: Here you would include different process areas in your plant, such as molding, stamping, plating or assembly.
- Safety: For companies that incorporate safety questions into LPAs, you can include process-specific safety questions here.
- 6Ms: We recommend plants use inputs from the 6Ms of process improvement as a centerpiece of their LPA questions.
- Customer Complaints: Here you would include questions specific to corrective actions or customer complaints to ensure improvements are being held in place.
- 5S: Many plants incorporate 5S into LPAs to ensure that work spaces are clean, organized and labeled properly.
- Low-frequency questions: Having a pool of low-frequency questions is useful for those items that only need an occasional check.
If you’re using LPA software, adding multiple tags to questions helps improve specificity to avoid N/A responses. For example, you could have a question tagged safety and stamping to ask if the operator knows how to operate the emergency shutdown on the stamping press.
This strategy also helps spot important trends, such as if you have multiple questions fail that are tagged both injection molding and man (6Ms). Seeing this might indicate operators need more training or recertification. Conversely, if you had multiple findings in molding related to material (6Ms), the problem might be poor labeling on bins rather than a training issue.
Rotating Questions in Your Layered Process Audit Checklists
Rotating the questions used on your checklists instead of using a fixed set of questions is essential to covering a broad set of standards. It also helps prevent pencil-whipping, keeping auditors engaged so they can’t just rush through questions.
When using software like EASE to put together checklists, you might distribute the different tags like so:
- Question 1: Safety
- Questions 2-4: Process + 6Ms
- Question 5: Continuous improvement
- Question 6: 5S
- Questions 7-9: Random
- Question 10: Low-frequency questions
Structuring your checklist this way means you’re much less likely to get N/A responses. For instance, you won’t be asking questions about plating in an injection molding area. You also know you’re getting broad coverage of standards to cover all aspects of the specific process. The result is maximum visibility from each audit, all in just 10 questions so you can achieve a high frequency of audits.
Using custom tags for your LPA questions is an effective strategy for improving visibility of problems and insights into where to target corrective actions from these high frequency audits. The important thing is to keep it simple, creating a set of tags such as safety, process, 6Ms, corrective actions and 5S. This strategy will help you cover a wide range of standards in a short 10-minute audit, so you can complete more audits in less time with better data for driving improvement.