How to Use PFMEA to Jump-Start the Layered Process Audit Process
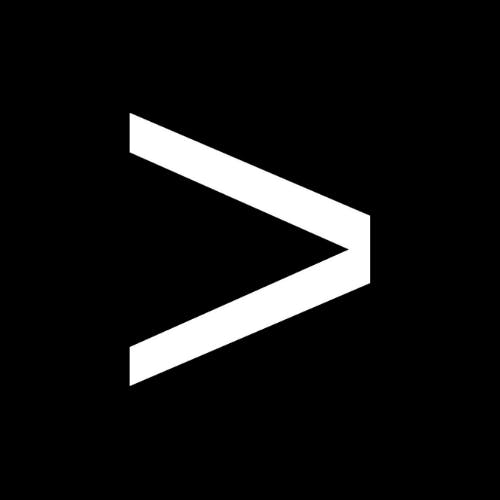
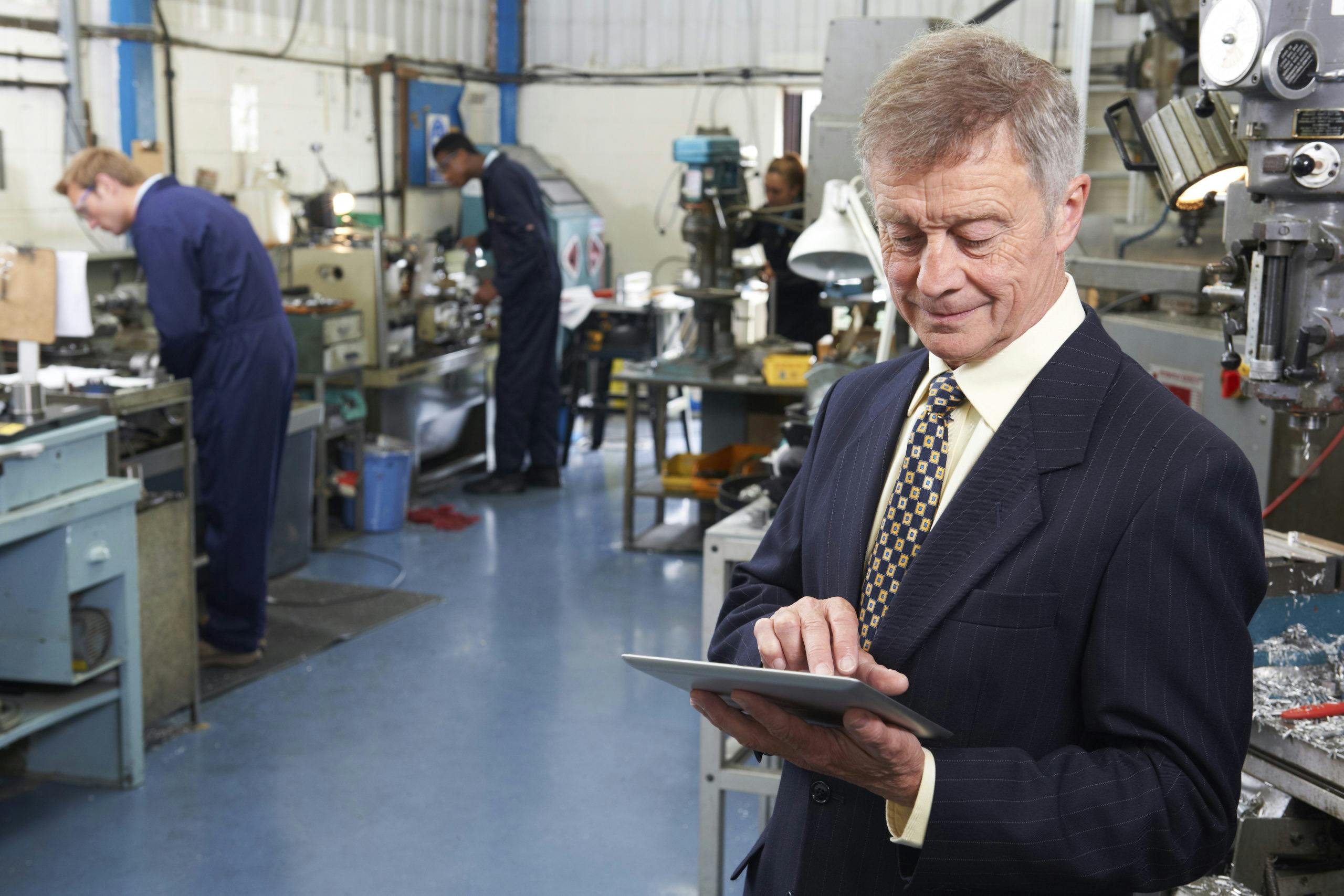
In a manufacturing environment, it’s common for teams to run into Murphy’s Law – the notion that “anything that can go wrong, will.” A simple day that starts with an employee calling in sick, can escalate through other events such as a workstation running out of parts, a machine shutting down for unknown reasons, or similar issues which result in missing production targets for the week.
In order to minimize risks, plants should use a Layered Process Audit (LPA) program to ensure that the most important controls to prevent defects and waste are in place. But with so many things that can go wrong, where do you start?
One great tool to consider is Process-FMEA (Failure Mode and Effects Analysis). Teams that are looking to start a Layered Process Audit (LPA) program often have a long standing practice of doing PFMEA to determine their areas of high risk and frequent failures. Teams can use the Risk Priority Number (RPN) calculated from PFMEA as the basis for focus areas to prioritize when developing LPA questions.
PFMEA and Risk Priority Number
PFMEA works to determine operational risks and helps to calculate a RPN score to rank potential failures. Typically, teams calculate an RPN for each PFMEA by using a similar formula and chart as shown below, and then, prioritize mitigation activities in decreasing order of RPN value starting with the largest RPN.
S x O x D (Severity X Occurrence X Detection) = RPN
Division |
Potential Failure Number |
Definition |
Severity – How much will this failure negatively affect operations? | 1 to 10 | 1 represents the least concern regarding safety; 10 represents the most concern |
Occurrence – How often could this failure occur? | 1 to 10 | 1 represents the least likelihood of the event to occur; 10 represents the most likelihood of the event occurring |
Detection – How difficult is it to catch this failure? | 1 to 10 | 1 represents the highest probability of detecting a potential failure; 10 represents the lowest probability of detecting a potential failure |
Connecting PFMEA with Layered Process Audits
When developing a plan for LPA, there are a few ways leaders can use their PFMEA and RPN as cues for where to start.
- Prioritize LPA development in the same order as other risk mitigation activities using RPN – Why change something that isn’t broken? If your team is short on manpower, the simplest way to get started with an LPA program is to follow the guide that’s already in place. Structure LPA questions to directly address operational areas with a high RPN to ensure that those areas are being audited by a team on a regular basis. Keep in mind that the areas with the highest RPN are difficult to detect by definition. Engineers may need to be creative in the types of questions they ask to dig to the root of problems and gain results. Depending on the type of LPA system being implemented, cloud-based solutions offer multiple question types that can aid in gathering more data on the specific risk area and how it performs over time.
- Prioritize LPA using calculations for Severity and Occurrence rates from PFMEA – You have the data in place and depending on how your team completed its PFMEA, it may be quite simple for you to create LPA questions looking at only the Severity and Occurrence rate of risks. This approach would make sense for teams who work in a highly automated operations environment where an increased dependence on machinery has led to a negative or positive skew for detection of risks. If your team feels that Detection of risks is highly subjective, the team should modify priorities and focus instead on Severity and Occurrence.
- Prioritize LPA using high Severity, Occurrence and order in reverse of Detection difficulty from PFMEA – ((S x O), D) = Process Audit Priority Number – Separating the calculations to (S x O, D) encourages engineers to think of RPN as a dynamic number relative to environment restraints. By prioritizing high severity, high occurrence, and low detection for LPA development, teams gain quick wins when starting a new program. This approach encourages long-term sustainability for LPA programs by allowing more opportunities for group buy-in gained from quick wins.
Starting a Layered Process Audit Program
When starting a new project, it’s easy to get overwhelmed by taking on too much in the beginning. Leaders who are receiving or initiating LPA programs need to take advantage of quick wins so teams gain momentum. One of the most challenging steps in developing a successful LPA program is writing effective questions and knowing where to start.
Do you have any questions based on our suggestion? What other practices have you followed to determine priority for risk mitigation?