Layered Process Audit Implementation Basics for Aerospace Companies
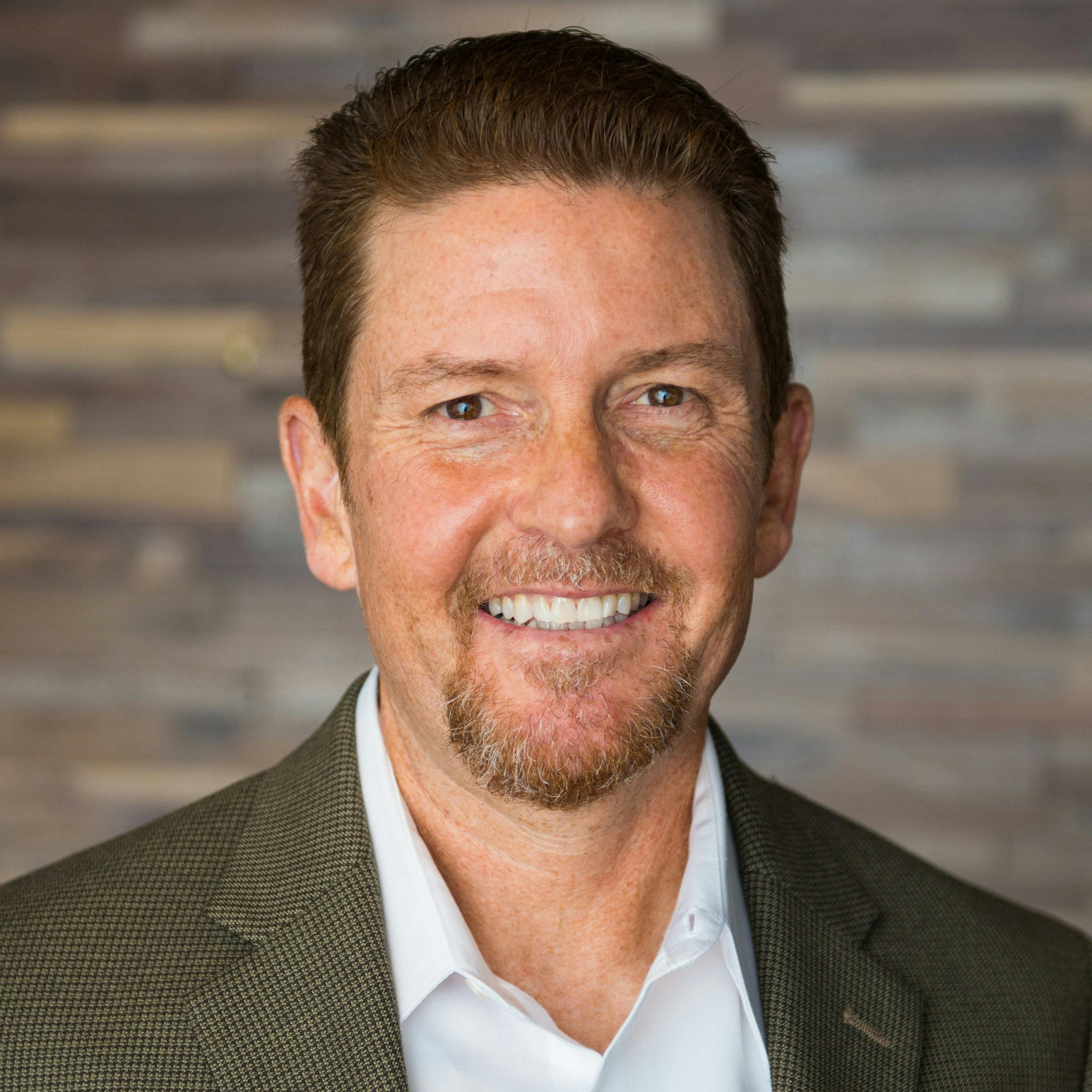
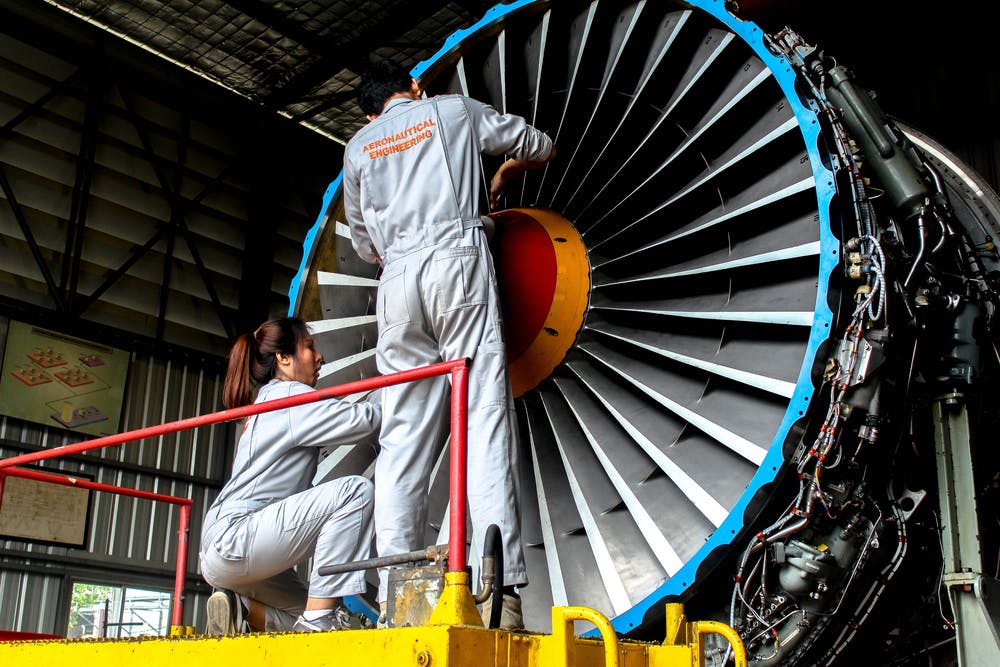
Ask any meeting of automotive quality professionals, and the majority could tell you what a layered process audit (LPA) is. In aerospace, that number is smaller but growing. Aerospace suppliers and OEMs are just starting to realize the kind of transformation they can achieve by implementing an LPA program.
LPAs are high-frequency process audits that are helping aerospace companies dramatically reduce defects, quality costs and customer complaints. Organizations thinking about starting LPAs first need to understand how these unique process audits work, and what to expect during the implementation process.
What Makes Layered Process Audits Unique
LPAs are broadly applicable to a variety of situations. While process audits look at inputs like fabrication steps and instrument calibration, LPAs add multiple layers of personnel to the verification process. These layers include:
- Layer 1: Floor supervisors and team leads conduct daily audits, every shift.
- Layer 2: Middle management performs audits each week.
- Layer 3: Site leaders and even executives engage in audits on a monthly or quarterly basis.
LPAs involve groups that include not just quality, but also operations, engineering, logistics and others. This has big implications for the quality of data you get from the audits and on the quality culture of the entire organization, which we’ll look at more closely below.
How Layered Process Audits Help Manufacturers
Evaluating upstream inputs identifies variation and nonconformities that cause defects. With quality costs totaling up to 40% of manufacturing revenues, even small changes can mean big financial gains. LPAs also help aerospace suppliers:
- Build a culture of quality: LPAs provide accountability and raise the visibility of quality across the organization. They also engage management on an ongoing basis, a common weak spot in many quality programs.
- Leverage limited resources: Aerospace companies often have smaller quality departments compared to other types of manufacturing. Distributing audits across areas like engineering and operations helps aerospace suppliers improve quality without hiring additional staff.
- Sustain the gain: Making improvements means nothing if you don’t have procedures to sustain those gains. LPAs help verify that corrective actions and other initiatives are fully implemented, and that people aren’t slipping back into old ways.
Unlike one-off quality initiatives that tend to be quickly forgotten, LPAs actually represent an opportunity to make a noticeable and sustainable impact on your biggest goals.
Layered Process Audit Implementation,
Step by Step
Implementing an LPA program is a significant undertaking that can take anywhere from two months to two years. It all depends on the conservatism of your company, and whether you’re building a paper-based system from scratch vs. a faster implementation with an automated LPA system.
The basic steps you’ll want to consider are:
- Learning about LPAs: The Automotive Industry Action Group’s CQI-8 Layered Process Audit Guideline provides an in-depth overview of LPAs.
- Building your team: Groups outside of quality need to be involved, and management needs to participate in planning, conducting and reviewing audits.
- Writing process audit checklists: LPAs should consist of 10 to 15 questions that are easy for non-experts to understand. Focus on being specific, objective and concise.
- Creating an audit plan: Once you’ve designed your layers and how frequently each will perform audits, you can start scheduling your audits. With a paper-based system, scheduling and follow-up typically requires up to two full-time employees. If you’re using an automated platform, these administrative tasks can be handled more quickly and without adding headcount.
- Piloting your LPA program: Because of the time and investment involved, companies often start by piloting LPAs in a single area or plant to iron out the wrinkles before deploying on a company-wide basis.
- Rolling out your program: Getting buy-in from your team will require communicating the value you expect to gain from the audits. This can be accomplished with a streamlined set of metrics and objectives. You’ll also need to be clear about expectations for team members, and follow up if people don’t meet those expectations.
- Monitoring and continuous improvement: Reporting and adjusting based on process audit data is crucial to success with LPAs. Proactively analyzing trends, addressing non-conformances and monitoring corrective action closure all lead to faster improvement.
Implementing LPAs can be a big decision, especially if it involves adding headcount to manage the administrative details. It’s important to consider how automation can accelerate your efforts, allowing you to focus on results instead of paperwork. In the end, it’s also a question of how fast you want to start seeing these benefits, and careful consideration of the opportunity costs of waiting.