Layered Process Audits: Start with Paper or Go Straight to Digital?
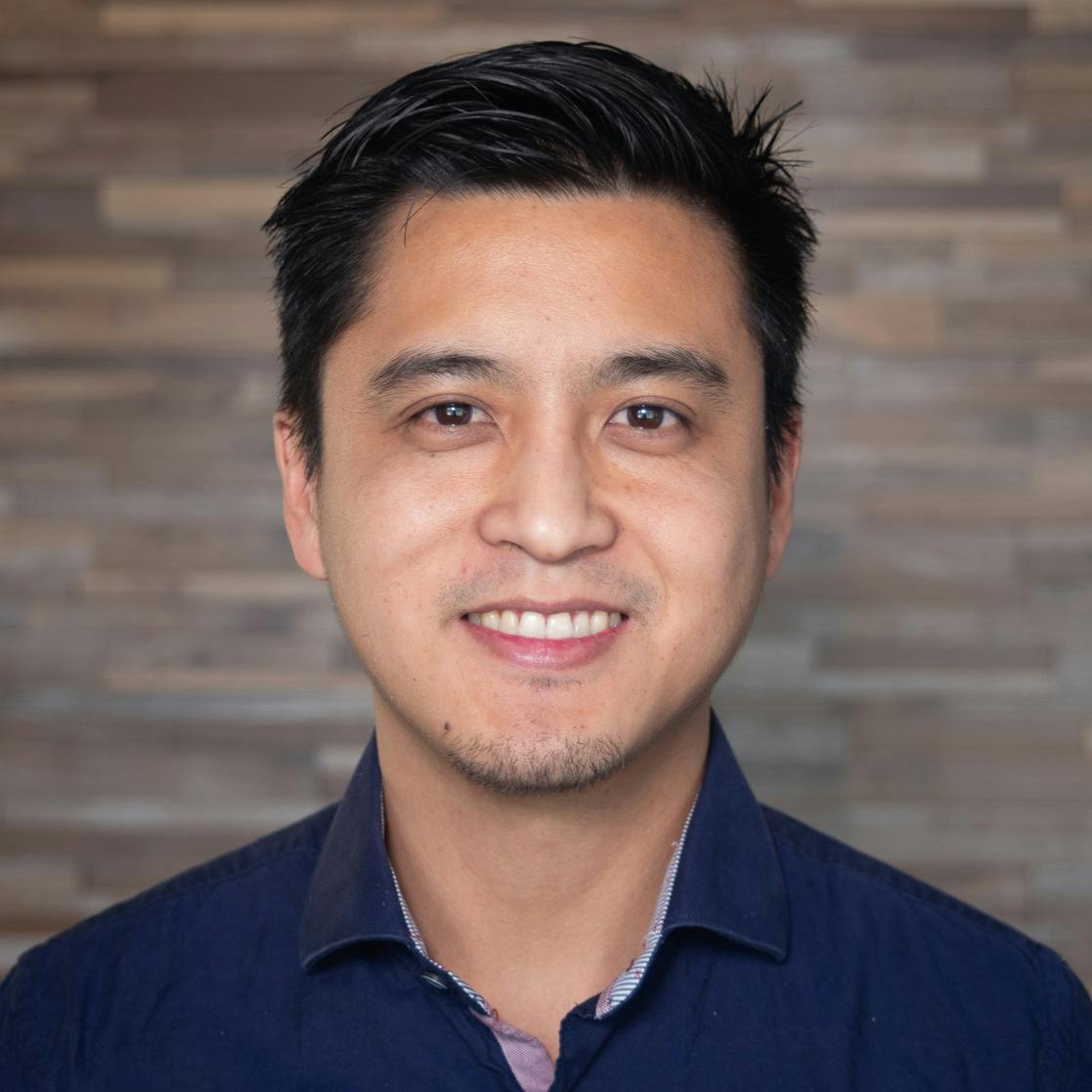
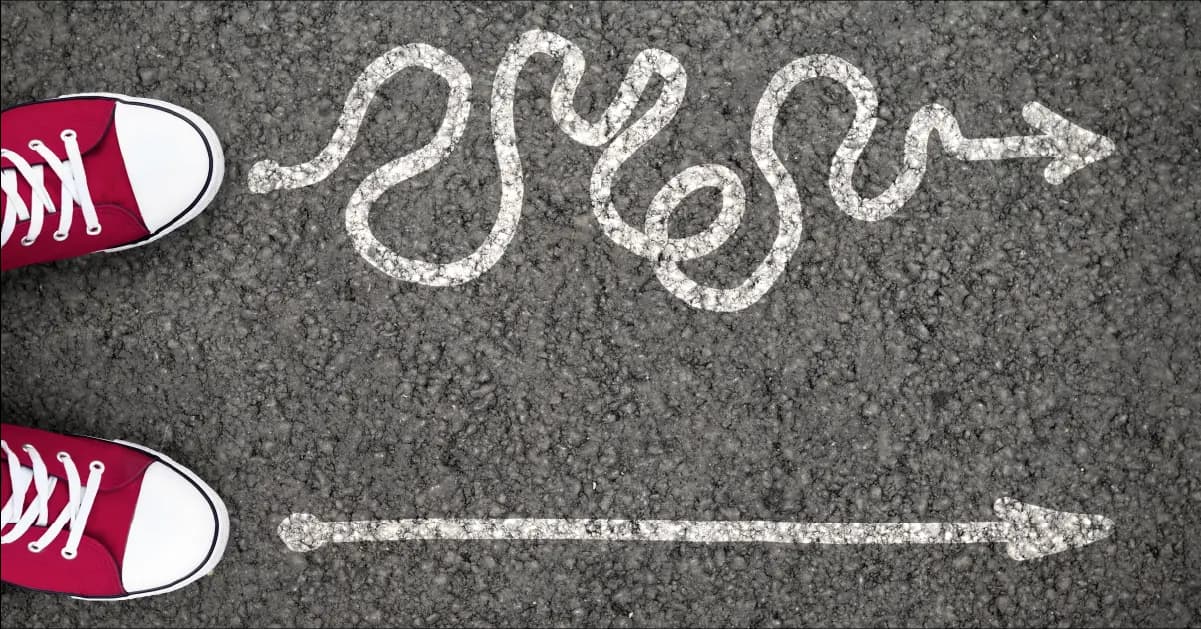
Implementing layered process audits (LPAs) can be a challenge due to a variety of factors. For starters, there’s the complexity involved in scheduling a high volume of audits across different levels of management. Then there’s writing effective LPA questions, conducting the audits and entering findings. Finally, LPAs won’t work without robust processes for reporting on, reviewing and following up on findings.
One important question as plants embark on their LPA journey is whether to pilot the audits with paper checklists and Excel spreadsheets, or to launch LPAs with a digital-only strategy.
In today’s post, we explore how starting with digital LPAs can help plants achieve quicker wins, improve employee buy-in and maximize efficiency. We also look at the elements of a digital LPA platform that can help you set the stage for success.
Get our free Ultimate Guide to Layered Process Audits for top tips, strategies and best practices to get the most from your LPA program
Getting LPAs Right the First Time
Many companies transitioning from a paper-based to digital LPA program do so because their manual process simply wasn’t effective. Common problems with using paper and spreadsheets include:
- The complexity of scheduling hundreds (or thousands!) of audits a year
- Getting people to actually complete those audits at all, let alone on time
- Keeping checklists fresh so that questions reflect current risks and quality issues
- Entering findings in a timely manner
- Lack of or inadequate reaction plan for failed audit questions
- Tracking issue mitigation to minimize risk and reduce the backlog of corrective actions
Starting with digital LPAs helps you get these processes right the first time, so you can focus on plant floor insights rather than time-consuming administrative tasks. This allows you to get to the heart of the matter faster: identifying and correcting problems before they become quality escapes.
Simplifying Change Management
Change management is an important consideration for any company looking to deploy LPAs in their plant. In addition to the new systems that must be set up, there’s the issue of getting your team on board. Without that, you’ll be looking at low audit completion rates, a lack of good data and ultimately, a loss of credibility due to LPAs not delivering value.
For plants that start with paper LPAs and only transition to a digital platform later, these are serious problems. Instead of just one change management process involved with a straight-to-digital strategy, you’re saddled with having to execute two change management processes.
What’s more, the move from paper to digital is likely to face more resistance internally, since the previous process involved a lot of paperwork with minimal results. Team buy-in and participation is critical to LPA success, making this an important consideration.
Creating a Closed-Loop Process
Starting with paper-based LPAs can be time-consuming and inefficient, particularly when it comes to creating a process that doesn’t allow problems to slip through the cracks. Missed audits, entering findings, following up on failed questions—all these and more create opportunities for quality issues to persist, emphasizing the need for a closed-loop process.
LPA software provides a framework for this type of process, allowing you to:
- Schedule audits out for the entire year in just a few minutes rather than hours or days
- Set up audit notifications and escalation rules to improve audit completion—a top struggle with LPAs
- Rotate and randomize LPA questions so that audits provide adequate coverage of standards, requirements and known risks without becoming cumbersome
- Record and enter findings and on-the-spot mitigations, including with photo documentation
- Assign action items and notify relevant parties of pending and past-due tasks
- Review audit findings with one-click graphs, Pareto charts and custom dashboards
- Verify corrective actions with updated checklists
This type of closed-loop process is consistent with the Plan-Do-Check-Act approach, improving efficiency as well as compliance with regulations and standards.
An audit platform like EASE is the ideal starting point for manufacturers interested in deploying LPAs in their facility. With tools like simplified scheduling, real-time reporting and issue tracking, users can easily avoid many of the problems of traditional LPAs and start seeing results faster.
Starting with digital LPAs provides significant advantages over trying to create a paper process and then transitioning to software later. Not only does it help you get LPAs right the first time, it simplifies change management while providing a best-practice approach for continuous improvement. The results are fewer quality escapes, a culture of quality and a successful LPA process that your entire team is more likely to be on board with.
- Learn how our white-glove implementation and support services can help you hit the ground running with digital LPAs!