Lessons from World War II on Manufacturing and the COVID-19 Pandemic
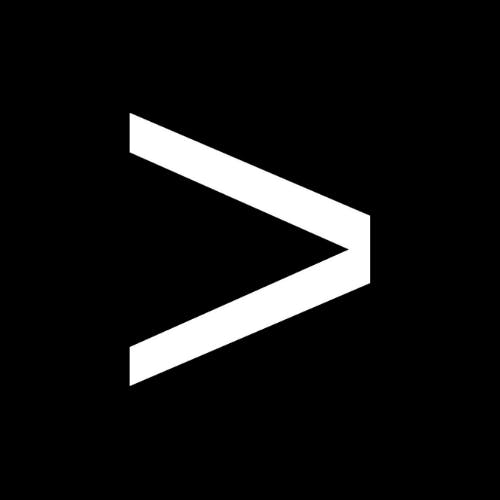
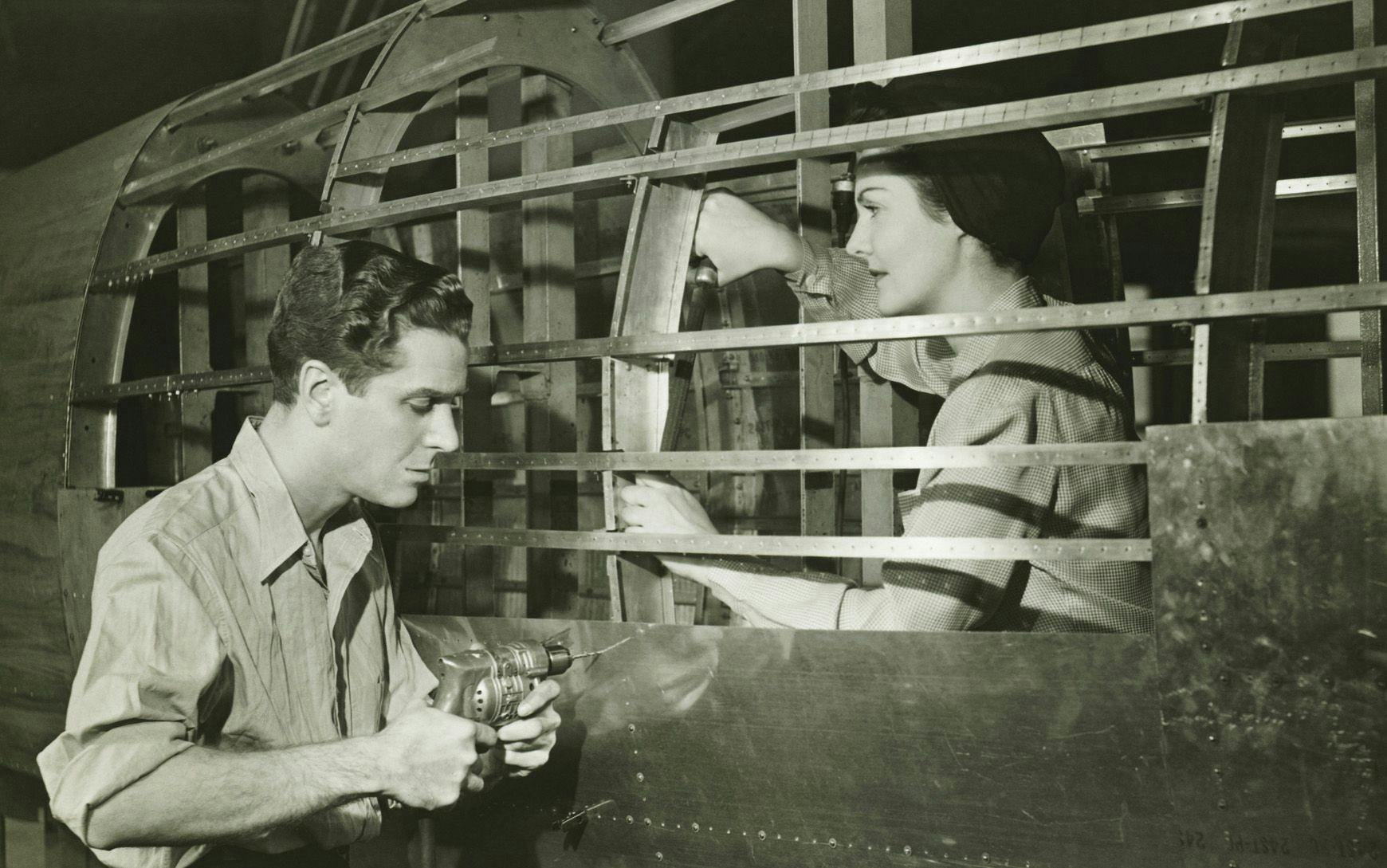
At a recent news briefing on the coronavirus health crisis, U.S. Surgeon General Jerome Adams referred to a particularly grim week of numbers “our Pearl Harbor moment.”
A look at manufacturing and the COVID-19 pandemic shows the comparison to World War II is an apt one. From victory gardens to discussions of shared sacrifice to ramping up production of critical supplies, the parallels between the health crisis and WWII are hard to ignore.
And while that generation was asked to leave their homes to fight or join the war effort, people today are being asked to stay at home to prevent the spread of the virus.
What lessons can manufacturers learn from WWII, and what do they need to do to survive the coming changes? In this post, we’re looking back through the lens of history to examine the answers to these questions and help companies chart a strategic path forward.
Pivoting Production Can Mean Faster Recovery
Many manufacturing heroes have already pivoted production to needed supplies such as ventilators, personal protective equipment (PPE) and hand sanitizer. While drivers include practical considerations like filling gaps in revenue, it’s also about the common good.
First and foremost, these changes in production are undoubtedly saving lives by helping overcome critical hospital shortages. They’re also keeping workers employed who might otherwise be furloughed due to a drop in demand or supply chain disruptions.
What’s also true, however, is that making these bold changes can help us all recover more quickly from the crisis and become better equipped to tackle future threats. Because the faster companies can manufacture supplies, treatments and even vaccines, the faster we can overcome this invisible enemy—and be better prepared for any second wave.
Employees Will Need to Fill New Roles
The second world war saw a massive influx of new workers in manufacturing as the country quickly shifted into high gear to produce airplanes, carriers and other equipment. In today’s environment, it’s similarly clear that employees will have to pivot to new roles they may be unfamiliar with.
In addition to changes in production, there’s also the fact that manufacturers will likely be dealing with lower staff density due to social distancing as well as potential spikes in absenteeism.
What can manufacturers do to prepare for this reality?
- Start preparing now for where you need to cross-train employees and how to deliver that information quickly and effectively
- Implement verification processes to prevent and detect quality issues that arise from lack of experience with a given production process
- Make succession planning a priority to ensure continuity when key individuals aren’t at work
This last point is especially important in the context of what comes after the crisis has abated. While millions are unemployed now, a rebound in hiring could eventually increase poaching for top talent. However, companies can’t afford to be caught with key positions unfilled when trying to regain productivity levels.
If You Fail to Plan, You Plan to Fail
Before the onset of WWII, the U.S. was far from ready for the conflict. In 1939, the US military didn’t even rank in the top ten globally, with a cavalry force of 50,000 that relied on horses to pull artillery.
All of that changed after the bombing of Pearl Harbor, a disaster many historians have ascribed, at least in part, to unpreparedness on the part of the U.S. military. Not willing to make the same mistake twice, the president quickly called on the manufacturing industry to produce hundreds of thousands of aircraft, tanks and guns by 1943.
In the context of the COVID-19 crisis, the parallel is unmistakable: failure to plan is the same as planning to fail. The writing is on the wall, both in health and economic terms. Manufacturers must plan now for a potential second wave of the virus, with many U.S. companies already preparing pandemic plans for just such an occurrence. Reducing operational costs with tools such as layered process audits to combat waste and improve process efficiency will be key to surviving economic changes.
Things Are Going to Look Different
WWII changed everything, driving economic recovery from the Great Depression while putting the U.S. on a trajectory for massive social change (not least of all by giving women a chance to be part of manufacturing).
While we don’t yet know what awaits after the crisis is over, experts agree that things won’t be the same once the widespread lockdowns have ended. Handshaking may be out permanently. Remote work and tele-health are in.
For manufacturers, reliance on globalized supply chains and just-in-time manufacturing will be called into question. The case for digital transformation has never been stronger, allowing manufacturers to achieve greater levels of efficiency with fewer resources.
Experts at McKinsey have deemed it the next normal, saying leaders must “reassess their entire business system and plan for contingent actions in order to return their business to effective production at pace and at scale.”
Versatility will be key to survival, just as quality will be integral to the ultimate success or failure of any new manufacturing initiative.
The story of WWII is one of not just heroism, but also industrial power. Just as the manufacturing boom helped lead the U.S. out of the Great Depression, manufacturers today are similarly poised to help move the country forward after the crisis.