Ease Introduces New Corrective Action Tools in Beacon 1.22 Release
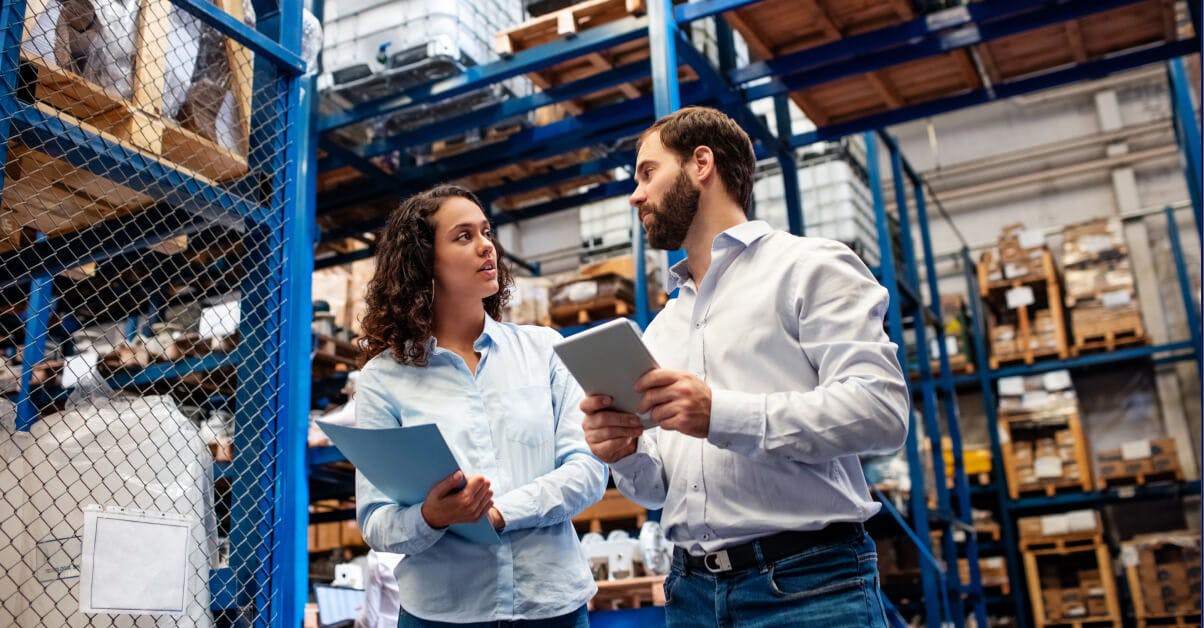
MISSION VIEJO, Calif., October 25, 2017—Ease, Inc. announced the addition of new corrective action tools as part of Beacon Release 1.22, the latest version of its automated audit management platform.
“The new tools make it easier to close the loop on audit non-conformances,” says Paul Foster, product manager for Ease. “Teams can now design customized corrective action plans that align with popular problem-solving methods like 8D, 5 Whys, SWOT analysis and turtle diagrams.”
Beacon users can also:
- Map corrective action templates to internal processes with custom fields that include tasks, due dates and responsible team members
- Automate routing via email notification to minimize delays and solve problems faster
- Assign action items, escalation and approval steps to ensure accountability
- Hold the gain by linking corrective actions to future audit questions
- Track corrective action metrics such as time to closure and overdue requests to evaluate quality system performance
“We’ve been working on these tools for several months based on conversations with clients about what they need to improve quality,” says Foster. “When they see the results Beacon can deliver, the next logical step is making their corrective action processes just as effective.”
Beacon is an automated platform that adapts to any audit type, including process audits, 5S audits and safety audits. Leading automotive and aerospace suppliers use Beacon for layered process audits (LPAs), a type of high-frequency process audit capable of reducing defects by 50% or more over several months.
Automotive manufacturers including General Motors (GM) and Fiat Chrysler now require suppliers to conduct LPAs as a condition of doing business with them. Beacon’s new corrective action capabilities help ensure appropriate audit follow-up, also representing a strategic tool for reducing the cost of quality.
“Every hour of delay in corrective action creates the opportunity for a multi-million-dollar quality escape,” says Foster. “Our goal is to streamline the process and eliminate bottlenecks, so manufacturers can find and fix problems before they leave the plant.”