Close Compliance Gaps with Plant Floor Inspections
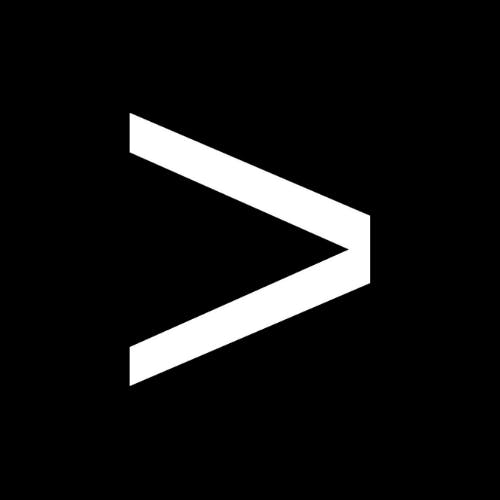
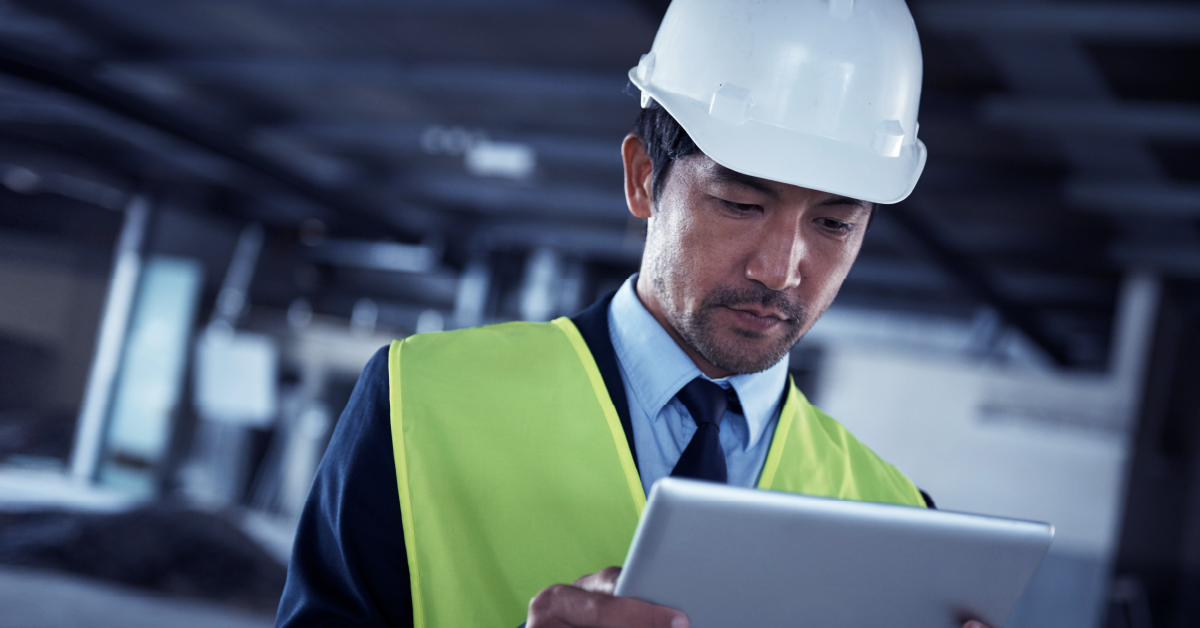
What’s the cost of a single compliance mistake?
For some companies, learning the answer is a tough lesson, especially given that the U.S. Occupational Safety and Health Administration (OSHA) raised its penalties in 2023.
The solution: find and fix your compliance gaps, before OSHA inspectors do, or worse—before an incident occurs.
Below we discuss practical strategies for using plant floor inspections to do it, and the tough questions you should be asking to make sure employees are truly safe.
Download your free guide on How Digital Safety Inspections Help Manufacturers Work Safer
The Compliance Assurance Approach
Compliance assurance refers to the process used to identify, track and demonstrate compliance with all of the requirements that your organization must meet. This process broadly aligns with the Plan-Do-Check-Act approach, based on the following steps:
- Identify all applicable requirements: Companies often do this in a regulatory register or a spreadsheet. This should include federal, state, and local regulations, as well as any applicable ISO requirements and internal policies.
- Link each requirement to an existing control: Controls may include physical controls such as personal protective equipment (PPE) as well as processes or policies designed to ensure compliance.
- Identify compliance gaps: Here the goal is to identify which requirements do not have an existing control.
- Add new controls to compliance gaps: If you’re looking at a long list of compliance gaps, assigning a risk level to each can help with prioritization.
- Verify controls: At this step, organizations must verify that controls are in place and sufficient to meet compliance.
Identifying Hidden Gaps with Plant Floor Inspections
Plant floor inspections help strengthen the compliance assurance process in terms of identifying compliance gaps and verifying controls.
At step two, one common mistake is simply assuming that just because a control exists, the company is in compliance. Take OSHA requirements around emergency action plans, for example. When creating their regulatory register, it’s easy enough to list an emergency response plan posted in the work area or stored in a binder as meeting those requirements.
But does that really mean the company is in compliance? More importantly, does it really mean your employees know what to do in an emergency?
It’s understandable why a company would take a piece of paper such as a policy or plan at face value when linking requirements to controls. After all, the Code of Federal Regulations contains thousands of shall requirements that organizations must comply with.
All the same, an occasional inspection question on what the operator should do in the event of an emergency can help ensure that people truly are prepared. It can also help identify where the plan needs review and updating, or where employees may need refresher training.
Verifying New Controls
For new controls added, it is imperative to verify they have been implemented correctly and are effective before considering the compliance gap closed. It’s especially important for high-risk compliance gaps, which could lead to serious injuries.
When adding questions based on new controls to inspection checklists, frequency is an important consideration. Where you might only include a periodic check for a control such as the emergency action plan mentioned above, new controls require more frequent checks.
That’s because whenever there’s a new process, people are more likely to fall into old habits. Upping the frequency of a question means more chances to identify, for instance, where an operator wasn’t trained on the new process, or where it might be unclear.
Getting More from Plant Floor Inspections
Plant floor inspection software can help with this process by making it easy to rotate questions within checklists and vary their frequency with custom tags. This is in contrast to using paper inspection checklists, which are difficult to update and are rarely changed as a result.
A plant floor inspection solution can also provide deeper insights into compliance gaps, so you can resolve them more effectively. For instance, let’s say you’re verifying lockout/tagout controls on equipment. During the inspection, you discover the instructions aren’t specific to the equipment, and the operator isn’t trained on lockout/tagout procedures—both of which are common violations.
Using a digital app, you can flag the question, include a photo of the generic instructions that need replacing and add an action item to update training. In the software, you can easily add the question to other workstations to ensure similar problems aren’t occurring elsewhere.
A single compliance gap can cost a manufacturer thousands of dollars or more should the problem lead to a serious accident. Finding and fixing compliance gaps requires a structured approach, supported by technology to make sure you’re checking frequently and getting the best insights from inspection data.