People, Processes, and Systems: Rethinking Quality with Mechatronics
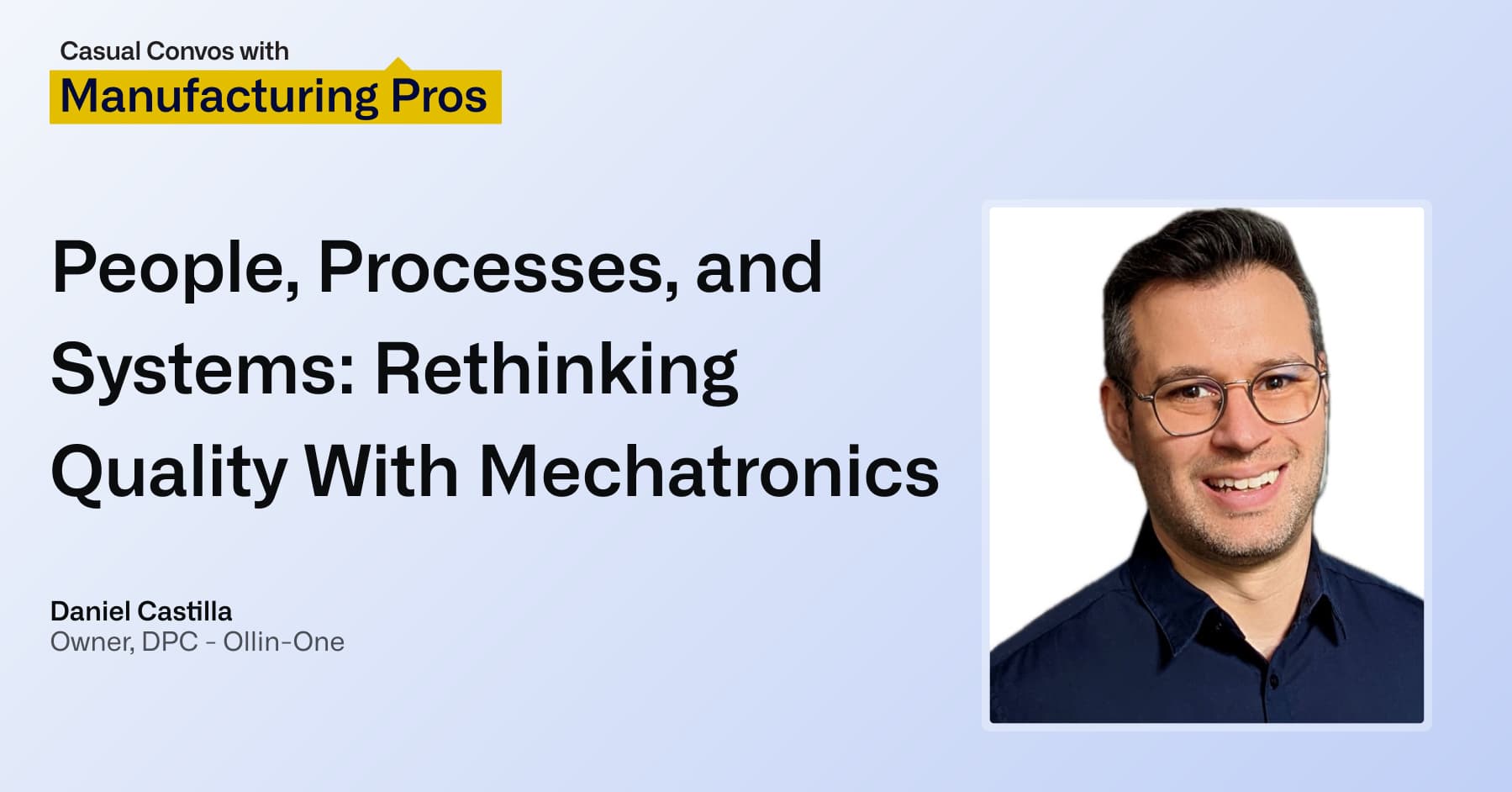
Episode overview
In this episode of Shop Floor, Top Floor Talk Show, host Josh Santo sits down with Daniel Castilla to discuss a mechatronics approach to quality management in manufacturing. Daniel, (Former) Director, Powertrain Quality & Customer Satisfaction, explains mechatronics as the intersection of multiple engineering disciplines, including mechanical, electrical, and software engineering, with a focus on systems thinking. He emphasizes the importance of considering the human element in these systems.
Daniel highlights how quality management can benefit from a mechatronics perspective, advocating for a systemic approach that embeds quality throughout the entire process. He challenges the traditional view of quality as a separate function, suggesting it should be an integral part of the input, not just an attribute of the output. This holistic view promotes collaboration between different teams and specializations, breaking down silos and fostering a more integrated approach to problem-solving.
The conversation also explores the common misperceptions about quality management and the role of technology in improving quality processes. Daniel touches on the importance of adapting communication to different stakeholders and overcoming the tendency to oversimplify complex challenges. He expresses excitement about the future of quality, particularly the advancements in Quality 4.0 and the potential of AI and digital twin technology.
Listen to the full episode here:
Transcript
[00:00:58] Josh Santo: Our next guest is a systems thinker, a digital problem solver, and a go-to expert on quality challenges seem too complex to untangle with deep roots in automotive, and a toolkit that blends lean thinking, data analysis, and global team leadership.
[00:01:13] Josh Santo: He’s helped some of the world’s most competitive manufacturers break down silos and build smarter, more sustainable operations. He doesn’t just fine tune existing processes either. He challenges outdated norms, architects, scalable solutions, and redefines how quality fits into the business. He. Whether leading quality transformation at a global Tier one supplier, or training the next generation of engineers in A PQP and FMEA, he brings clarity, structure, and measurable impact to every engagement.
[00:01:43] Josh Santo: Please welcome to the show, Daniel Castilla. Daniel, thanks for being here.
[00:01:48] Daniel Castilla: Hey Josh, thank you for having me.
[00:01:50] Josh Santo: Yeah, it’s great to have you always learn a lot. Looking forward to learning more and sharing those lessons with the folks that are listening today. Speaking of today, we’re talking today about a mechatronics engineers approach to quality and how you can operationalize quality through it.
[00:02:05] Josh Santo: So gonna start out with my first question. Now, I’m gonna be honest with you, Daniel, I had never heard the term mechatronics until we had the pre-interview, so I wanna level set because there may be people like me listening to the show who also don’t have a strong definition of it. I would love for you to define mechatronics and help us understand how that differs from more specialized engineering paths like industrial engineering.
[00:02:33] Daniel Castilla: Sure, yeah, sure. And that’s not an uncommon question. I had it myself when I selected my. My career path, right? Like, like what’s mechatronics? And then that’s how I got into it. So yeah,
[00:02:44] Josh Santo: gonna do that. Yeah,
[00:02:46] Daniel Castilla: exactly. Like some, some sketches, but why not? No. Well, mechatronics, even the name itself capture, capture, some of it is, you could say the intersection of mechanical, mechanical engineering, electronics, computer science, and, control systems, right?
[00:03:00] Daniel Castilla: So it’s kind of, if you blend, a lot of the, uh, different, specialized engineering, fields that you can have, you get that. So mechatronics is kind of, uh, response. To the need, coming from the industries in the, it’s around the early two thousands. Uh, when the industry says, yeah, we are getting a lot of, very specialized technical people, right?
[00:03:22] Daniel Castilla: But we need the, to combine them, right, so they can actually talk to each other. Uh, and that’s how Mecca drinks happens. So you have a, like a Venn diagram and put all of them together. Mechatronics is almost in the middle, um, and the technical side. And we also have a little connection to business, like the software, uh, uh, skills, stuff like that.
[00:03:42] Daniel Castilla: So in contrast with the industrial engineering, you could say that mechatronics is more about. The system level. Right? So creating like the holistic thing, right? we kind of interact with the, or have the ability to interact with the different disciplines and specialists, put things together, but always looking at the bigger picture.
[00:04:03] Daniel Castilla: And Industrial engineers, they actually are more in like the other way, right? They go deep into, making things more efficient, making things more productive. So extracting waste and stuff like that. But they work with the pre-established, um, systems, right? So it’s, it’s, they, they go into something that’s already running and they make it better, right?
[00:04:24] Daniel Castilla: on the mechatronic side is we say, okay, how could we build it? So, so it’s actually efficient since the beginning, taking in consideration all the pieces.
[00:04:34] Josh Santo: So there was a lot of components to that that really centered around how do we get different groups, different specialties working together. In fact, when you were describing it, you hear the term mechatronics, at least I hear the term mechatronics. I hear mech, I think machines, mechanical things of that nature. But I was struck by, in your description of it, there was very much a people focused element to your definition of bringing these different groups together to make
[00:04:59] Josh Santo: sure that they work together. From your perspective, is it a more technical specialty or is it more focused on the people side?
[00:05:09] Daniel Castilla: I would say it can be. Both because, uh, even, well, I say when I was studying it, you have the different paths you can actually go into being very, very technical. Then you devote your career probably to building robots and building like these systems that have software inside that have electronics. So now, I mean, we see a lot of, of these creations from kind of that idea.
[00:05:29] Daniel Castilla: the electric vehicles are kind of a MEChA system because it has all the different, uh, ways of creating, engineering solutions. Like, well, this, the, mechanical part, electronics, the software and so on. But you can also go into the more, uh, organization kind of systems, right? Where you have not just a hardware and software, you also have people, you also have these conceptual, uh, entities that are not tangible, right?
[00:05:56] Daniel Castilla: And then you start touching other areas that are not typically, what you would think, uh, about when you talk about engineering.
[00:06:03] Josh Santo: Okay. So really getting the different systems to work together, getting the different people to work together and
[00:06:10] Josh Santo: getting the different people and systems to work together.
[00:06:13] Daniel Castilla: exactly, exactly. Because system is the whole is everything, right? So you cannot, uh, remove people from systems.
[00:06:22] Josh Santo: Well, thinking about your experience in manufacturing, and I think you mentioned earlier that you’re not surprised when people aren’t as familiar with mechatronics engineering.
[00:06:31] Josh Santo: It doesn’t seem to be as common. Uh, I’m curious in your experience, how common is mechatronics engineering in manufacturing?
[00:06:39] Daniel Castilla: I’ll say that nowadays it’s becoming more, well, it, it’s already more common, right? But, uh, there are two things that come to mind. I see more people that actually study Medtronics or are actually, uh, they have the, uh, the education to be a mega engineers or a variation of, of that depending on their, on the region.
[00:06:57] Daniel Castilla: you’ll see that in. In industries where you have these complex, products that the by nature have that, like automotive, aerospace, those kind of things that, that you say, well, their product itself demands, uh, these skills to be, uh, front and center. but also, it’s starting to be, more obvious and less, uh, less traditional or, or, or, or say less edgy, uh, industries because now we see a lot of industry 4.0, we see a lot of integration of systems that are just becoming mainstream, right?
[00:07:28] Daniel Castilla: So the, the, the mechatronics, uh, engineers, uh, are, are more, uh, common nowadays. I will also say that, Maybe, or probably it is not common to hear the term, but we see more of these profiles, right? Even, even if people didn’t study by itself, or they define themselves as mechatronic engineers, they by experience or by a collection of different, uh, uh, education, uh, um, uh, paths, they end having that profile, right?
[00:07:55] Daniel Castilla: It could be that somebody started being a mechanical engineer, but by trade they, you start getting all the other skills and they end having that profile. Mm-hmm.
[00:08:04] Josh Santo: So the study’s becoming more and more common to see people actually pursuing that. Kind of like you did mechatronics engineering. That sounds cool.
[00:08:11] Josh Santo: Let me do that.
[00:08:12] Josh Santo: But also to your point, the necessity of what’s going on within the industry, the different types of requirements for the products that are being made has led to a need for someone to fill this role. Whether or not they have that official training in that background. So they may be performing the actions and the activities that are associated with mechatronics engineering like you’re describing. So it sounds like the popularity is ultimately rising, and if you don’t have a mechatronics engineer, with you today, it may behoove you to look into either developing that skillset or bringing
[00:08:44] Josh Santo: someone in with that skillset.
[00:08:47] Daniel Castilla: exactly, exactly that. Mm-hmm.
[00:08:50] Josh Santo: So you’ve got a pretty extensive background in quality, that was one of the things I was struck with when we were talking in the pre-interview, is that you studied mechatronics engineering. You’re looking at how these systems can come together, how you can get people to work effectively together and bring both of those things together in order to make sure you’re delivering the products that the customers need on time in full. curious with your experience in quality, what do you think that quality management can learn from mechatronics engineering?
[00:09:23] Daniel Castilla: Yeah. So for me it was also a surprise ending with the, so much experience in quality, right? But, after some time I realized that actually is well aligned with being a mechatronics engineer because quality management is nothing else, than another way of doing the same because a quality management, or when you do that is, is system thinking, right?
[00:09:44] Daniel Castilla: saying, well, the, the, A company is running, uh, as a whole and there are different elements and it’s a human element, the infrastructure element, the environment, the machines themselves, the product, the needs, all those things. But everything is a part of one thing. So, so systems, thinking and quality, actually, it’s a must.
[00:10:04] Daniel Castilla: Right. So, and I will, I’ll say, uh, with my, or would I make atronix, uh, background? Then it gives you that edge because immediately you are already thinking into, okay, how does this work? How do I extrapolate this into, into something that, in your mind is a machine, right? How do you, how do I conceptualize it?
[00:10:21] Daniel Castilla: So, so all the things. If I move one thing, and it could be that I move the policy, then how is that affecting. the end result of a, of a factory, right? Or if I have changes in, uh, external factors or I have changes in human, resources, availability, stuff like that, like how is that connected with my maintenance?
[00:10:39] Daniel Castilla: So all because everything has an interconnection. yeah, I’ll say that’s the one. The other one is, uh, well, as I explained when I was, well, when you asked me about the, the difference between other disciplines and mechatronics is that we are trying to create the,system or to see it like, well, we have to create it, so it works by itself, right?
[00:10:58] Daniel Castilla: So in quality. You are trying, or the best approach, the most, cost effective approach is to design for quality, right? Is to ensure that whenever you start producing your first piece, it’s good, and from there on it will be good for the rest of, of your manufacturing, project, whatever.
[00:11:15] Daniel Castilla: So, so, uh, I think that also helps. Right? And, and, and that’s, I see the benefit with my own experience is like, there is, there is a, a school of, uh, of thought and quality. That quality you have to take care of the output. Well, the school of thought that I prefer to follow is what you take care of quality, uh, from the input, right?
[00:11:33] Daniel Castilla: So from the beginning even, and the result happens by itself.
[00:11:37] Josh Santo: So taking that perspective of a mechatronics engineer, looking at the system as a whole, sounds like your perspective is that quality is something that needs to be embedded throughout that system. It needs to be a factor within the entire process so that you’re not addressing quality at the end. Quality is part of the input. And if anything a a governing aspect of that system.
[00:12:02] Daniel Castilla: Yes. Yeah. Quality is just the, it is a, it is an attribute of the output, right? So if, if your machine is well, oil and all the things are happening as they’re supposed to happen, the output should be good.
[00:12:13] Josh Santo: Now that sounds like a, a perfect perspective in my. More inexperienced opinion. How common would you say that mindset is viewing quality from a systemic perspective as opposed to quality as a separate function?
[00:12:31] Daniel Castilla: That’s a tough one because I want, I want to say that, uh, it’s becoming more common, but I see over the years I have seen like back and forth, back and forth, right? it’s one of those things that the, as, as, as industries or companies mature, they start seeing that, right? it’s kind of experience gives you that, understanding of like there is something else, right?
[00:12:51] Daniel Castilla: Like there is, there is a better way of doing this. And then you start, well, people start realizing, ah, maybe instead of trying to, uh, catch what is, uh, coming bad, out of my line or, or my factory, maybe I go back and I start thinking about, oh, what if we design the process better so it doesn’t create that product?
[00:13:10] Daniel Castilla: Or even better, what if we design the product itself? So it is more difficult or less likely to have, uh, products that are. not Are not working right? Even if the factory has a certain, certain situations or even you go back and they’re like, oh, wait a minute. what if I structure my company, my organization, so I have all the elements that whatever I put in place, if I’m designing a service, I’m designing a product, it will actually come with all these attributes, right?
[00:13:38] Daniel Castilla: So that will be be the, the perfect scenario. But, kind of off waves, right? Because as, as soon as you see progress, then it’s, given for granted, right? So it’s, it’s, it’s something that is assumed, oh, we are already doing it, and then companies stop doing it, and then you see a step back.
[00:13:53] Daniel Castilla: So it’s a back and forth, back and forth, but I will say that, it’s slowly, slowly improving.
[00:14:01] Josh Santo: so people see the absence of quality issues and they think, well, why are we doing all this quality stuff?
[00:14:06] Josh Santo: We’ve got quality on lock
[00:14:09] Josh Santo: and
[00:14:09] Daniel Castilla: That’s always the irony. Mm-hmm.
[00:14:11] Josh Santo: and then you pull back and then all of a sudden, oh, why are we seeing quality issues? Well, we stopped investing into
[00:14:17] Josh Santo: quality
[00:14:19] Daniel Castilla: There is, there is a say, uh, among quality professionals that we actually work to lose our, our jobs, right? Because we are trying to, uh, make people realize that we get the things to work like smoothly and, get the standardization where it makes sense, then you don’t need a quality professional check in and helping you, like patching the work.
[00:14:39] Daniel Castilla: But it’s like if you actually get it, then as you said, like, well, why do we need you? Right? And then they’re like, well, that person is gone, or quality functions are reduced, or me into something else, minimize whatever. And suddenly all those things stop, happening and they’re like, oh, we need quality, right?
[00:14:56] Daniel Castilla: So, yeah. Mm-hmm.
[00:14:57] Josh Santo: it’s such an interesting point that in an ideal world, we wouldn’t need quality because quality would be a part of everything all the time.
[00:15:05] Josh Santo: Always top of everyone’s mind. Any process, any design is already factored quality in. But like we all know, we don’t live in that
[00:15:14] Josh Santo: ideal
[00:15:15] Daniel Castilla: right.
[00:15:16] Josh Santo: right? We live in the reality and we build towards that ideal situation. And then to your point, you gotta look at all the systems coming into play are leading to the impact that you’re having. So this perspective of really needing to take. And view quality from a systems perspective versus looking at quality as a separate function. In your experience, who do you think benefits more from viewing quality through this mechatronics perspective? Do you think this is something more beneficial for plant personnel and plant management, or do you think this is more beneficial for corporate leadership?
[00:15:50] Daniel Castilla: I will say that both get a benefit, but in different ways. Because, eh, plant personal benefit from the immediate gains, right? I mean, this way of, of seeing things, of saying, well. It’s input and output and it’s a, a, a system. And I fix the gears in the engine instead of trying to put something on top, gives immediate results if you go down to that level, right?
[00:16:13] Daniel Castilla: So, I mean, I had seen a, a cases where there is a mechatronics, project, right? Where, what I’m saying make aran project, I mean some, something more holistic in a plant, and then the results are right there. And then, plant people see the benefits, less scrap, less inefficiencies, stuff like that, right?
[00:16:30] Daniel Castilla: Or, uh,
[00:16:31] Daniel Castilla: uh, productivity, eh, is increased, stuff like that. But it’s also on the other side, when you see like even a bigger picture, you see a company itself where you can actually impact corporate, leadership because you are talking about making more, more efficient, uh, strategies, right? So long-term vision for quality, right?
[00:16:52] Daniel Castilla: When, when you start saying, well. what if, if from corporate, uh, we actually make the different functions or the different divisions or the different whatever departments or the different locations, be steady, be, have better, better elements to work smoothly, and then you impact everyone.
[00:17:12] Daniel Castilla: Right? Uh, my own experience was like that. When you actually go to corporate, you, it’s a little frustrating because you cannot jump into the machine and say, I will fix it. Right. Or I have a better way, or I will actually put these five things together and it will be, uh, beautiful. No, it’s more about thinking.
[00:17:27] Daniel Castilla: Okay. How can I make this machine that is, uh, is not about hardware, that is about the HR people.
[00:17:35] Daniel Castilla: hiring people, hiring employees and training them, and then the, people that are, finding infrastructure and buying machines, and then the, the ones that are running them and all those, how can I actually get them to work in better sync?
[00:17:50] Daniel Castilla: So the end result is better. Right? And what’s the end result is good business. It’s like, so corporate gets, or, or corporate leadership gets, uh, a smoother, operations.
[00:18:01] Josh Santo: So it sounds like there’s benefits to both. maybe it just manifests in different ways. I think to your point,
[00:18:07] Josh Santo: it, it sounds like you have to think through a little bit of what’s within your direct sphere of influence, as well as what are the actual activities within
[00:18:16] Josh Santo: your own control. But by applying that perspective of how does this work together, who do I have to work with?
[00:18:21] Josh Santo: What has to come together? What do they need to do? How are the things that we’re responsible for impact those things? What can we do better to help them do their thing better? What can they do to make our job a little bit
[00:18:35] Josh Santo: easier? Are we communicating with them, et cetera? There’s ways of understanding what you can own, what you can control, what’s within that sphere of influence, and if you were to put that in place with that perspective of all of us have to work together and accomplish these different things in order to deliver on whatever the goal is, that could be a helpful perspective to adopt and drive, change, progress, improvement, et cetera.
[00:19:01] Daniel Castilla: Yes. Yeah, and I, I, I will just add to that, that the, it is, it’s like if you, if you’re baking a cake, right? It doesn’t matter which ingredient is wrong. You just need one to be wrong, and then everything is wrong. Right. So it’s like you have to really, you cannot just say, oh, well I only care about the water, right.
[00:19:16] Daniel Castilla: Because that’s my responsibility. Well, if it’s not the water, it’s something else, then the end result is a bad cake. Right. Or, or you don’t get a cake, basically. Right. So it’s, it’s that, that way of thinking. It’s like, it’s the, the, the, the end result is the addition of the different elements and the interactions.
[00:19:33] Josh Santo: Mm-hmm.
[00:19:33] Josh Santo: Mm-hmm. So, you know, you as an individual or your team or your organization may be doing everything right, but we altogether are still failing in some regards.
[00:19:44] Josh Santo: So it is everyone’s problem and everyone needs to come together
[00:19:49] Josh Santo: to, to help do something about that. ’cause in your cake example, it could be very easy to be like, well, don’t look at me. I sourced the eggs. Like I did
[00:19:57] Josh Santo: what I was supposed to do. I did it per. ISO standard.
[00:20:02] Daniel Castilla: Exactly. And at the end it’s like there’s no cake to sell, to sell. Sorry. And then that’s the end, right?
[00:20:08] Josh Santo: right?
[00:20:08] Josh Santo: Yeah. Then
[00:20:09] Daniel Castilla: We don’t have a job.
[00:20:10] Josh Santo: Yep, exactly.
[00:20:11] Daniel Castilla: Not my fault.
[00:20:13] Josh Santo: Yeah. look at me,
[00:20:15] Josh Santo: the eggs were good, cake was bad. interesting because that’s something that has to you you do have to overcome is, is, you know, getting people to like accept that ownership and be a part of the team. It’s a tough thing to balance that individual responsibility or that specific team responsibility. ’cause you want people to stay within their scope, but you also want people to make sure that they’re working together effectively in order to accomplish that goal. How do you balance those two things?
[00:20:45] Daniel Castilla: yeah, and I, I’ll say that it’s not about, Getting everybody to do everything and to jump into, all the different aspects. It’s more about understanding, right? Like understanding that, well, that, that you, if you have to break that, siloed approach, right? That silo thinking where you say, well, this is my lane, and as long as my lane is fine, then I don’t care about what’s happening to the others.
[00:21:07] Daniel Castilla: Because if your lane is causing delays, to the next one in line, then it’s, it’s just a ripple effect, right? So it’s about understanding that, whatever you are doing there is, there is some process, I will say process, just to be very generic. There is some process before you that you depend on or a few processes you depend on, but there are also processes after you that depend on you, right?
[00:21:30] Daniel Castilla: So any inefficiency or any, anything that might not be, impacting. Your your own thing, right? Could be just, just a, a, creating chaos or creating, uh, delays, inefficiencies, and that starts creating this, snowballed approach.
[00:21:49] Josh Santo: Well, you said something just now that I think comes up pretty frequently. It’s that idea of silos and you said you have to break that siloed approach. That’s easier said than done. How do you break a siloed approach?
[00:22:01] Daniel Castilla: Yeah. And well, for me, but that’s a, that’s, that’s a tough one. We are humans. We like that. We want, we like going home, closing the door and saying, this is my kingdom. And it’s like, I don’t care about the neighbor. Right. So that’s, that’s kind of a, a universal, it’s like I control it. it’s really about ownership sometimes, right?
[00:22:17] Daniel Castilla: Like, it is like, well this is, this is my territory. I can eh, modify it. I can control it, I can decide on that one, and then I feel well here. Right. And then if I cannot control the other side of the fence, then I will just ignore it and I actually have a, a taller fence. Right? So it’s, about.
[00:22:35] Daniel Castilla: getting people to understand those fences are just artificial, right? It’s like those are just so you don’t have to take care about the complete city by yourself. Right. But at the end of the day, it’s like, there is only one way to be successful. it is, all of us need to work in syn, right?
[00:22:52] Daniel Castilla: It’s a lot of, of these soft skills, right? It’s a lot of, I mean even, even there is, it is said many times, but it comes back to leadership, right? Because leadership has to create the conditions when they, where they actually have, uh, or give the rest of the organization clarity on what’s a responsibility, but also clarity that that doesn’t mean that the, that, that the rest of the company is not relevant for them, If it’s is having that, that at the end it becomes a, in software terms, is the empower, the empowerment side of this is the, is is giving a lot of awareness of of, of how things work, eh, technical people. Probably trend more to trench themself into their, your, their matter expertise of expertise, right?
[00:23:37] Daniel Castilla: Like, if I am in the lab, I like the lab, I stay here, I feel comfortable here, I don’t care about business, but at the end of the day, it’s like, well, it’s part of the same, right? So it’s, it’s a bold directions like technical people. Yeah. We don’t have to forget about them. They need to understand how business is running, right.
[00:23:53] Daniel Castilla: To cap that, bigger picture, but also business people understand that there’s no business without these technical things happening. Right. So it’s, it’s crossing those, creating those breaches. Mm-hmm.
[00:24:02] Josh Santo: Hmm. And I can see even in your answer, you’re still bringing it to how things work together. A systems perspective, right? Here’s your role, here’s why it matters. Here’s the impact that it has. Here’s what you’re not thinking about that we need you thinking about. And on the flip side, for folks on, on the business side, you know, same thing except from the technical side. Here’s the things that you may not be thinking about that are important and really just. It sounds like breaking down the silos is just leveling with folks, meeting, meeting them where they are, helping them understand where the organization needs them to get to and how that actually happens is really gonna be on the leader, the culture, there’s a lot of variables that come in to getting people to buy into the idea and concept, and it’s
[00:24:46] Josh Santo: really up to those individuals to, to nurture that thought process.
[00:24:49] Josh Santo: And it takes time to change people’s perspective too.
[00:24:53] Daniel Castilla: That’s, that’s true. And I, well, and comes to mind that the, that’s probably why, I mean, you asked me before why, well, you said that I have a lot of quality experiences here and there in the, in my, in my cv. Uh, I think that’s, what is attractive to me, right? Because quality is the natural function that is doing that all the time.
[00:25:10] Daniel Castilla: Because as a quality professional, you interact with the, uh, manufacturing, you interact with the human resources, you interact with, purchasing, you interact with, and then you start kind of creating that in your mind like, oh, okay, everything is like, kind of connected that you see that, but also you become the ambassador of that or, uh, of that message you start conveying.
[00:25:28] Daniel Castilla: It’s like, well guys, actually, the only way this will be more efficient is like, well, we start aligning our horses, right? Like, there is, there is no other way. I actually even have, um, presentation that I use a lot to educate people of how you can describe a company, right? And there’s, there are different ways of describing a company.
[00:25:45] Daniel Castilla: You can say geography. Right? Like, yeah, you see these are the locations, these are the buildings, these are the areas. That’s one way of looking at a company. The other one, organizational chart, people skills, jobs, right? So that’s another way of, of describing a company. Third one, activities. What is a company doing?
[00:26:02] Daniel Castilla: What is a four one money flow? How money flows around the company, that financial world. That’s what they do, right? And the other one is from the customer perspective, right? Like, okay, how you are adding value, transforming into satisfaction, all those stuff. And then the question is, which one is right? Well, all of them, because all of them go together.
[00:26:22] Daniel Castilla: It’s just different dimensions of the same thing. So you cannot decide and say, well, I wanna only take the geography because I like it. No, that doesn’t mean that the others disappear, right? So it’s more about saying, well, by nature, depending on what the employee is doing, they will probably gravitate around one that is more relatable.
[00:26:40] Daniel Castilla: But as soon as they start seeing the others, they start saying, ah. So the business people. Are actually trying to do the same as me. They’re trying to create an output that is, for me, is a product for them is a revenue, and for others is customer satisfaction. Everything is the same.
[00:26:58] Josh Santo: It can be hard to build that perspective though, that ability to, to look at the same thing from multiple different angles, multiple different perspectives. how do you do that without requiring people to walk a mile in the other person’s shoe?
[00:27:14] Daniel Castilla: That’s a, that’s an interesting one, I’ll say. And that had been, a journey for me. I’ll say I started seeing that, uh, probably two decades ago. I’ll say, well, this is, this is multidimensional, right? Like, this is not just one thing. And, uh, for example, I take the traditional quality, fundamentals like iso, right?
[00:27:32] Daniel Castilla: You see iso, ISO tells you, well see, a company is basically telling you the, a company can be described by activities and processes and all that. It’s just one dimension, right? But then you go to a business, descriptions, it’s like, no, you see it by flows or you see it by the people, interactions and stuff like that.
[00:27:49] Daniel Castilla: HR is more probably about, well, you see the employees, you see how they have their skills and their abilities and all that. and it’s really about, it’s, it’s kind of creating that, equivalence like you, you start putting the two or the three next to each other, and then it’s how you start showing people.
[00:28:08] Daniel Castilla: IWI think technology is allowing us to have a easier ways, for example, nowadays, what before was, or, or still called, but uh, was traditional like quality systems. Now it’s more morphing into digital twins because that captures or, or technology allows to go and navigate those dimensions. Like say, okay, well I wanna see a model of my company, but not just in one, one single, uh, variation.
[00:28:32] Daniel Castilla: Right? It’s not, not just geography. Geography. You could say Google Maps is a digital twin for geography, right? But then you start adding these other elements and, and we are getting closer to that,
[00:28:42] Josh Santo: Hmm. Yeah. Digital twin is an interesting, uh, interesting concept. Would you mind just defining it for the audience here, how you think about a digital twins so we can make sure we’re all on the same page?
[00:28:53] Daniel Castilla: Sure. So yeah, a digital twin I mean, the, the term will explain, it, as, I’ve done, but it’s, it’s creating a model. It’s creating a, a virtual e equivalence of, of, of your company. Right. Or, or whatever you’re modeling, right? But in this case, a company, so you say, well, let’s first look around.
[00:29:12] Daniel Castilla: Yeah, let’s start exploring and, and seeing what they’re doing. Like map, map the, the organization in these dimensions and you create, a model. It could, it doesn’t mean that it’s a, 3D model or anything, right? It’s, it’s more of representation. It could be the traditional ways, a collection of documents, or it could be with, with better technology.
[00:29:30] Daniel Castilla: It could be a, a collection of websites that describe and lets you navigate. Or it could be the addition of your, your job, job descriptions in a way that you actually can see the, the relationships. So you kind of, describe, in a fake or a or electronic version, uh, your organization, uh, one-to-one or close as close as you can go one-to-one.
[00:29:50] Daniel Castilla: And the idea with digital twins is once you have that and you say, yeah, this is valid. this is actually looks like my company. Then you have the ability to play with the, the digital twin for almost for free, right? And you can say, well, if this, if this company. Where to become excellent and, uh, efficient and perfect.
[00:30:09] Daniel Castilla: it’ll look like this and you start modifying it because you don’t have a budget restriction, right? You can just imagine whatever you want. The output would be perfect and all that. So now you have a digital twin that is no longer a twin reality, but it’s kind of the best of the best, right.
[00:30:23] Daniel Castilla: That you can get. And that helps you compare your company and say, well, let’s get as close as we can to that ideal state.
[00:30:32] Josh Santo: Well, I’m glad you broke it down. ’cause whenever I had thought of digital twin, I, I had never realized that I had focused purely just on the actual, like manufacturing side of it.
[00:30:42] Josh Santo: I never thought of it to, to bring it to like an entire company perspective. I’d always kind of thought about it as like the digital. Recreation of the assets that
[00:30:51] Josh Santo: you use to produce the products or convert raw materials into finished goods. And I always thought, you know, you gotta have the right assets represented digitally so that you can run the modeling to say like, okay, well if we were to try to increase production by this much, you know, what would that look like?
[00:31:07] Josh Santo: What impact would that have? What would we have to do, et cetera. Uh, is that gonna be feasible to, to run those different scenarios like you’re describing? But I think it’s interesting, the, the way that you defined it is kind of bringing it up and putting, you know, that the, how I define it into a broader context, kind of.
[00:31:25] Josh Santo: Once again, we’re seeing your systems perspective come into play, right? Bringing it up to the bigger picture, et
[00:31:32] Daniel Castilla: exactly. It’s just the level, right? I mean, because what you are describing is also perfectly valid to a digital twin, right? Could be just a product, it could be a screw, and they say, well, this is a deal of a screw. How do I make it better? And all that. So you are doing the same. It’s just your scope and how high you go.
[00:31:47] Josh Santo: Mm-hmm. Yep. That’s why I love doing these learning as we go.
[00:32:08] Mike Fank: Hey, I’m Mike Fank, quality Manager at Wisconsin Metal Parts, and here would be my quick advice, to help make your career more impactful, more successful. You work on the skill of leading up and down the chain. Uh, and I’m gonna steal from Jocko Willink book Extreme Ownership Here. When you’re leading down, make sure you’re helping your team prioritize their biggest efforts, making sure you understand what they’re working on.
[00:32:34] Mike Fank: The particularities of their job. And if you’re leading up, help your boss succeed. So you wanna understand what is important to them and how do you make them more successful in what they do. ’cause your boss is probably not actually trying to make your life more difficult. He just has his own priorities.
[00:32:50] Josh Santo: Well, we were talking about quality. We were talking about who benefits from viewing quality through a mechatronics perspective. I’m curious if you’ve encountered some misperceptions that may prevent manufacturers, maybe even leadership and manufacturing from viewing quality like a mechatronics engineer might.
[00:33:14] Daniel Castilla: Yeah, I’ll say one that I face, uh, very early in my, career was the, well, ignoring the human factor, right? Saying, oh yeah, this is great. We can do this. And then we are eliminating human factor or we are minimizing human factor, right? No. Now, uh, all this is truly about, uh, well, as I said, putting all the pieces together, right?
[00:33:34] Daniel Castilla: And the, and human factor is actually very important, right? So even that, uh, mechatronics engineer by, because it’s engineering at the end of the day, will look more like, oh, this is about the machines, this is about the hardware, this is about that. It’s like. It, it comes with culture, it comes with, uh, training.
[00:33:52] Daniel Castilla: It comes with the, all the, considering that a person has, uh, emotions, variation, it has a, aspirations, all that, right? So it’s is, uh, that’s a, a very common, uh, mistake. Second one that I can think about is the disconnection of, uh, quality in the business, right? I mean, that’s, that’s, I’ll say it from a mechatronics point of view, but probably you can reach that conclusion as soon as you get into quality, right?
[00:34:15] Daniel Castilla: Like it’s quality is doing one thing and it’s thinking about the eliminating complaints and, uh, passing audits and doing all that, but missing that at the end of the day, all of that is to have good business, right? So, so it’s, it’s missing that connection and saying, no, no, no, we only want customer satisfaction.
[00:34:34] Daniel Castilla: Well, we don’t really want customer satisfaction. You’re for the sake of customer satisfaction, right? Customer satisfactions. It is actually a good business because customers come back, customers are satisfied, they pay us for the services or the products that they, we deliver, right? So that’s really what is behind that.
[00:34:50] Daniel Castilla: So, uh, that’s the second one. I’ll say the third one, uh, which is, is a tough one, is underestimating or avoiding complexity, right? Saying, well, yeah, this scope is too large. If we wanna actually see the, the bigger picture or all the elements, then this is a multi-year, project. Let’s do less. Let’s do as much as we can with, within six months, 12 months, right?
[00:35:16] Daniel Castilla: So then we start compromising and we start mixing simplistic with simple, right? For me, simple, it means that we find a way to, uh, handle the complexity. Without pushing it to, to the people, right. Without pushing it to the users or to the workers or whatever. It’s like we find clever ways to handle that complexity.
[00:35:36] Daniel Castilla: Simplistic is ignoring it, right? Saying, well, I don’t like it. 1, 1, analogy that I, that I use sometimes is saying, well, how many states do we have in, in the us? Well, 50, right? Okay. Uh, do you know all of them? Well, probably not, right? I mean, or maybe you do, I don’t know. But it’s like, well, what if we only say that there are three?
[00:35:57] Daniel Castilla: It’s easy, right? And you can name three very easily, right? Where you live, and maybe two that are where, where you had vacations, whatever. But does that change the fact that there are 50 states? It doesn’t. So if you start doing that in business or you start doing that in the operations, is you are just ignoring reality.
[00:36:15] Daniel Castilla: Right? And when, when you go down to, to, to real thing, to, well, to to face reality, like still there, there’s still 50 states, right? So it’s handling that complexity. Mm-hmm.
[00:36:24] Josh Santo: I think that was a good example. Simplistic being, ignoring it. Simple being, overcoming the complexity. I liked your example of simplistic. How many states in the United States are there? Well, three. Um, which is true. There are three, if not all
[00:36:39] Daniel Castilla: Yes,
[00:36:40] Josh Santo: right. And maybe may be a
[00:36:41] Josh Santo: more accurate way of putting it. Simplistically is, more than three. Right. How many states
[00:36:47] Daniel Castilla: yep,
[00:36:47] Josh Santo: there’s definitely more than three, right?
[00:36:49] Josh Santo: Everyone good? Everyone good with that answer? It’s
[00:36:51] Josh Santo: true.
[00:36:52] Daniel Castilla: Easy.
[00:36:53] Josh Santo: we’re going, but that doesn’t actually get to the heart of what is really trying to be answered, which was the exact number in that ex example. So you, you mentioned three misperceptions. You just talked about ignoring the human factor. You talked about a disconnection of quality in the business.
[00:37:07] Josh Santo: And then on that last one, underestimating or avoiding complexity, let’s talk about ignoring the human factor. Ignoring the human factor. Meaning the way that I took how you explained it is that there’s a big variable in your operation and that’s your people. Because
[00:37:23] Josh Santo: people themselves have a ton of different variables that influence how they are just period, right?
[00:37:32] Josh Santo: I’m sure we all
[00:37:32] Josh Santo: can think of examples of characters in our lives who are very different from us, and you either love them or hate them because of that. So they, the human factor, how. Should someone factor that in whenever taking a mechatronics approach to quality in manufacturing?
[00:37:52] Daniel Castilla: Yes. And I’ll, I’ll say human variation is sometimes, or many times mental misunderstood as noise or, or or variation that you don’t wanna have there. But in reality, that human variation many times is the success factor for your processes because it compensates for deficiencies in the design of our machines, our products, all that.
[00:38:15] Daniel Castilla: Typical cases when you have an operator that the just knows. He just knows that if he said something here, if he pushes that, if he doesn’t completely close the door, it’ll work. Right? So that’s variation, right? But this is the variation that we kind of turn a blind eye on, but it’s like, we like it, right?
[00:38:33] Daniel Castilla: Because it’s like, oh, we have no clue what’s the root cause we don’t know what’s happening. It’s like, call this guy he knows, like, don’t ask, he knows, right? That’s variation. So, uh, I’m not saying that we have to, to, to go and, and, uh, make that the solutions, right? But it’s taking that into account, right?
[00:38:52] Daniel Castilla: That we actually will need those kind of things, experiences, variation, experiences is good, right? So we will never, ever be able to design a system or a, or a line or whatever that truly works perfectly, right? Unless, unless we design something that is so constrained and so very well, very few. Pieces or very few elements that Yeah, yeah, it can, could run, right?
[00:39:15] Daniel Castilla: But, well, in engineering or in physics, it’s called entropy, right? It’s like any system will deteriorate by itself. If you don’t, if you don’t maintain a system, it will just start breaking, right? So, so you need people, you need people to actually, uh, well, as I say, compensate for those things that, uh, will happen.
[00:39:34] Daniel Castilla: And also the people that will actually make sure that if your process is changing, right, we can adapt to it. It does, even, even with the, I mean, I love automation. I really like it. I, those are toys, uh, that are great, right? Like, uh, who, who will not play with those things that are million dollars and you have access to for fun, even that they call it work.
[00:39:53] Daniel Castilla: But,
[00:39:54] Daniel Castilla: at the same time, robots are not perfect, right? They might be repeat very well, right for certain time, but if you just let them run as maybe. Couple of years, whatever, one in gear will break, one gear will slide. I mean, the rubber will start leaking, stuff like that. Right? So, so they also come with that, so, yes.
[00:40:15] Josh Santo: I like how you put that where it’s really about not trying to eliminate or get rid of the, the variation that comes from just working with people, but instead finding ways to embrace it.
[00:40:24] Josh Santo: Because ultimately these different perspectives, these different background experiences and skill sets ultimately are gonna be the things that enable you to find how you can make improvements or how you can overcome situations that pop up, how you can capitalize on opportunities, et cetera. And so your point is, keep that in mind that there’s gonna be this variable, and then find out what those variables are, like, how they’re manifesting, and, and work with them, not necessarily try to eliminate them because we’re not working with robots here.
[00:40:55] Josh Santo: And then to your point, even robots are not to the point where they’re completely autonomous
[00:41:02] Daniel Castilla: Correct. Yeah.
[00:41:03] Josh Santo: Yeah.
[00:41:04] Daniel Castilla: I mean, and it’s, even, even that it sounds that we are getting closer. AI is artificial intelligence, but it’s not, smart. Intelligence is not, is not thinking. Right. It’s, it’s just a, a very, very fast processing of things.
[00:41:17] Josh Santo: Yes, yes. but it certainly outdoes me in a lot of ways, that’s for sure.
[00:41:23] Daniel Castilla: Just faster.
[00:41:24] Josh Santo: It’s just, yeah. say it’s that. We’ll say that it’s faster now. Uh, another misperception that you called out was the disconnection of quality within the business. Talk to us about how this, misperception, can be overcome.
[00:41:40] Daniel Castilla: Yeah. Well, I, I will have to give a little background of how, how I think we get, we got there, it’s probably the nineties or eighties nineties when the, all these, uh, ISO and the to Toyota Way and all those things started to happen where eh, quality was specialized. Right. And say, well, we actually have, we need to do better products.
[00:42:01] Daniel Castilla: Right? And then the industries, the companies said, well. Let’s create this, entity called quality that will be, uh, kind of, we outsource that, to a specific group. They, they will, they will take care of, uh, of making sure that, we protect the customer that we actually, are correcting, are having this, uh, this improvement cycles.
[00:42:21] Daniel Castilla: Right. Okay. That works well. Right? But what really truly happened is that quality started to create the, their own thing, right? And that’s what we see. I mean, a lot of, professionals are brilliant, right? But they are very ISO centric. They are talking about the requirements, they’re talking about the customers saying auditor is doing right?
[00:42:39] Daniel Castilla: Like, and that is, it seems even something that is imp happening in parallel to, to, to reality of the locations. it’s really about bringing those two worlds together, right? It’s, it’s, it’s, it’s on both sides. Um.
[00:42:52] Daniel Castilla: Quality professionals need to learn truly. And, I said this, to the, to an in, during an automated forum.
[00:42:59] Daniel Castilla: I think one of the missing core tools for quality professionals or core skills for quality professionals is business understanding. Is talking business, right? is being able to go and, talk to management in, to management, to leadership and say, well, this is what I want to do, but express it in business terms, ’cause right now it’s like a very well-rounded quality professional in their field will be able to express it, but not in terms that leadership will actually follow. Right? And, and expecting leadership to actually understand or learn all these quality kind of equivalences is, is it will not happen, right?
[00:43:37] Daniel Castilla: I mean, they, they are, they’re doing their own thing, right? So for me it’s about quality professionals, adding that business side to the profile, being able to express when, I mean, I wanna have capable processes. Why do you want capable processes? Oh. Because that will be more efficient and we will have, we will have a, a less downtime and we will have a reduced scrap and all that.
[00:43:58] Daniel Castilla: Like, that sounds like a nice to have when you start saying, well, because that increased productivity, product productivity means capacity. It means also reducing, reducing waste and waste means reducing, or limiting waste is, is money, right? Is money that we have. Capacity means that we can take more business.
[00:44:18] Daniel Castilla: Oh, now we’re talking. Right. So it’s that connection.
[00:44:21] Josh Santo: Mm-hmm. And that’s a tough skill set to develop, especially if you’re
[00:44:24] Josh Santo: not ever exposed to that idea or, or even exposed to What What the people that you’re trying to, to get bought in are interested in. ’cause the, the example that you gave my mind goes to leadership.
[00:44:36] Josh Santo: I’m thinking plant management and
[00:44:38] Josh Santo: that, that type of example that you gave. but let’s say you, you know, when you say you have to have that business understanding, there’s also that element of adapting the message. That’s your point. You have to adapt the
[00:44:50] Josh Santo: message. The, the message might resonate better with a, a plant manager, if you put it in terms of operational opportunity, you can, get more capacity.
[00:44:59] Josh Santo: That means we could essentially make more money at this plant
[00:45:03] Josh Santo: that’s gonna make you look good, right? Like, you know, to, to them. Probably don’t say that, but like, that’s kind of the under, under
[00:45:11] Daniel Castilla: Yeah. Because it, it, it tells them you understand what the game is, right. Or what the ultimate goal is. Right. Like this is a business. It started as a business. It’s still a business. Yeah. Mm-hmm.
[00:45:20] Josh Santo: But to the flip point, maybe you see, uh, a number of non-conformances that are happening.
[00:45:25] Josh Santo: You, you come to the conclusion that if, if you spend, I don’t know, let’s say a week longer training folks, that’s, that could reduce it. And maybe this time you have to get HR to buy in. You’re not gonna go to HR and be like, I know how we can get more capacity for our facility. At that point, you’re gonna have to adapt to the message
[00:45:43] Daniel Castilla: you have to talk hr. Exactly. Exactly.
[00:45:46] Josh Santo: so, you know, it’s not enough to just understand like what the
[00:45:49] Josh Santo: overall business needs, but kind of to your point, what does each level, each stakeholder or representative within the business, what’s going to make that message
[00:45:58] Daniel Castilla: Exactly.
[00:46:00] Josh Santo: Now la last thing you covered was that idea of underestimating or avoiding complexity.
[00:46:05] Josh Santo: You gave the example of how many states. Or in the United States, a simplistic approach, which you argue is not the right way, is to say, well, there’s three, more than three, which is technically correct, but it’s not getting to the root of the actual problem to be solved. and your argument is that, taking complexity, finding a way of making it simple, so you’re overcoming that complexity.
[00:46:28] Josh Santo: That’s the way the path to go down. Can, can you talk to us just a little bit about that idea of complexity in, in addressing complexity and overcoming complexity?
[00:46:40] Daniel Castilla: Yeah, so for, I, I, I’ll give a, a quality kind of example, right? The very, very typical when you are creating a man a process map, right? We are basically identifying what happens if in my company. and then you have to create a graphic, right? We say, well, I have a marketing, then I have design and development, then I have a design of my manufacturing set up.
[00:47:03] Daniel Castilla: Then I have purchasing, then I have a, a incoming inspection, then I have manufacturing, then I have logistics, delivery, transportation, all that. Suddenly you start realizing that you have around 50 boxes. It’s around 50 boxes that you have, right? so what happens many times is like, oh, too many boxes.
[00:47:21] Daniel Castilla: It’s too complex, What if we only. Take the core ones or what if we actually say, well, we only do this, let’s center about around manufacturing and remove the rest. You end with a very nice graphic, very simple, well, or very simplistic, I’ll say very simplistic graphic, right? But you’re ignoring a lot of things that are happening in your company, right?
[00:47:41] Daniel Castilla: So that will be a simplistic approach, right? Traditional ones that, well, whoever is working in a factory and is listening probably could relate to that, is like, well, what are the processes? Well, we only take care of what is happening inside these four walls. And my typical question when I go there to, to consult her to help us, like, so who’s designing?
[00:48:00] Daniel Castilla: No, we don’t do it. I didn’t, I didn’t ask. If you design, I’m asking who is designing, because I don’t, I don’t think this print came from nowhere. Somebody is designing and if they don’t design right, you face the consequences. So if you are just ignoring that there is a complete design world out there, then you are just blindly accepting whatever they send you.
[00:48:21] Daniel Castilla: Maybe you are lucky and they have everything under their control, but if not, then that might be the source of, of a lot of the issues that you have here because you are building to print might be that the print is not even right, that you cannot,or sometimes it’s like, well if you actually build to print the product does not work because there are design issues.
[00:48:38] Daniel Castilla: Right? so the other approach is, okay, well it doesn’t mean that now we need to live with the 50 boxes and very complex, thing. Yeah. But you start playing, okay, what if we start grouping things right? We don’t do design well, don’t ignore it. Just group maybe seven things there. And you say, well this is the design world.
[00:48:56] Daniel Castilla: I will not explore it. This is just like saying, well, I live in, in, in, in America. Then, well, Europe is there, but I will not go into every single country and every, and draw every single line in every single county. Right? It’s like, I, I just say, well, my, my word is here, but I am aware of the, of the rest of the things.
[00:49:14] Daniel Castilla: So for me, that’s,it’s creating a simpler approach, right? It’s like you start saying, well, yes, I have more resolution here, more detail here. Or if I am, I go a little down into the levels. If I am a maintenance guy, right? Well, yeah. Maintenance is, handling machines and production and all that.
[00:49:30] Daniel Castilla: Well, for them, they need all the detail in life into their maintenance process, right? Into what they are doing. And they probably go down into manuals and how to their maintenance routines and how they, change parts and all that. That’s what they need. The others for them. They just need to be aware.
[00:49:48] Daniel Castilla: Of their interactions, right? They don’t need to have the things that the logistics is doing or finances is doing. Right? So, so you are, you are, you start playing with that. It’s like you have to tailor it to the user, right? So it’s, and I’ll say that’s a, a huge task. And I’ll say if you, you try to do it with Excel, word, the PowerPoint, whatever, all those, it’s almost impossible.
[00:50:10] Daniel Castilla: But technology is helping us now because now you can actually play with that and create systems like that. Mm-hmm.
[00:50:17] Josh Santo: so one of the takeaways that I had from that is it’s really about. Things are gonna be complex and there may not really be a way to simplify it. There may not be a way around it. Things are going to be complex. It’s, it’s really, don’t ignore the complexity. Understand where these complexities exist, how you connect within to that system. Focus in on what’s within your sphere of influence, like we talked about earlier. Go deep in that, but understand there’s other parts that are happening before happening after. And you do have to have an awareness of how these minute details ultimately build up to that bigger picture. And that’s kind of where your perspective of that system, that
[00:50:59] Josh Santo: holistic system, that mechatronics engineering, uh, background kind of, kind of manifests. Now you mentioned one last thing. You talked about technology is helping. That’s got me curious about, um, you know, when you think about technology, when you think about just tools, skills, training in general. I’m curious on your perspective, what are the must have tools, the must have skills or books or well trainings that you would recommend people prioritize to continue driving the industry forward?
[00:51:33] Daniel Castilla: Yeah. well, I will repeat myself for the first one, but skills, I’ll say again, system thinking. I mean, because of all these that we are seeing, right? The ability to see the bigger picture going up, down in the labels, understanding where you are. So that’s for me one that at least for me have been, extremely useful.
[00:51:50] Daniel Castilla: Opened a lot of doors and understanding. Second one, I’ll say, uh, well, from skills is problem solving real, or I mean root cause analysis, that kind of thing. So, and not, not, not really any specific methodology, uh, that I will say that it’s because you wanna follow this approach of, no, no, no. It’s more about the, the way of, of analyzing things, right?
[00:52:11] Daniel Castilla: Always, always trying to go deeper, right? And to say, well. Uh, am I really seeing the problem? Am I really seeing the thing that failed? Or am I seeing an, a manifestation of, of that one? Am I seeing a, an effect, right? I’m seeing just a, just a superficial bubble that, uh, is coming from, from below, right?
[00:52:28] Daniel Castilla: And it’s, it’s thinking in that way. and as I say, it’s not about doing the, the ideas and all that. I mean, obviously that that comes with the, with the, with the exercising of, of this skill. But it’s more that whenever you have a conversation, whenever you are confronted with a problem, immediately your mind start going into, okay, let’s go deeper.
[00:52:46] Daniel Castilla: Let’s start thinking logically. Let’s start connecting the dots. Okay, what caused this? And if I truly want to get rid of this, forever and ever, where would I go? Right? Instead of just patching, patching, patching. third one that I will say continuous learning. I cannot, I can after those two, I cannot name one that just say, well, with this, this tree, you are good.
[00:53:06] Daniel Castilla: It’s more about. Eh, always trying to learn the new things. Right. Right. Now, I mean, if I am to, to say something, well, artificial intelligence for now, right now, it’s like learn that, but five years from now is, or maybe even two years from now, it’s like probably there’s something else to learn, right? It’s like always, always, always try to keep yourself, eh, fresh and understand the what’s, what’s coming or what’s already here.
[00:53:31] Josh Santo: on that last one.
[00:53:32] Josh Santo: Ai, there’s a lot of buzz around AI and I was just at a conference recently and there a lot of people there were, were attending some of the talks around AI kind of looking to answer, you know, what’s. What’s buzz versus what’s reality?
[00:53:46] Josh Santo: What are other people in manufacturing actually doing with ai? What’s notable?
[00:53:52] Josh Santo: I’m curious about your perspective with regards to AI and manufacturing. Where have you seen some of the fit in the use?
[00:54:01] Daniel Castilla: Yeah. First I’ll say AI is just a new term. Because it, before it was a artificial, net, neural networks. That was kind of, how I studied, when I studied, uh, how it was, uh, called then it was computer learning kind of thing. So it’s more an evolution of that. What I’ll say AI for me is, uh, it’s the manifestation that now is a mainstream technology right now.
[00:54:28] Daniel Castilla: It’s something that, almost every single person can access, has access to, right? You can just go into ChatGPT or whatever, and it’s free, right? Maybe you don’t get the, the Cadillac version, but, but it’s, it’s accessible. for me it not really changing fundamentally the problems that we have, but it’s giving us a very powerful tool to do things faster.
[00:54:51] Daniel Castilla: Right, because it’s about that the access to information is amazingly fast. it made me think like when we have this first access to the internet, like, or like suddenly we have access to who, like a library is in front of us, uh, in our houses. And then it was then Google said, well, what if we index all this?
[00:55:10] Daniel Castilla: And then it is not just that you have the library, now you have the index and you can actually jump into the page very fast. Right now it’s like, I don’t even have to open the book. It’s like I have the guy that tells me, okay, in that book, and in that book, if I take those two and three and then I, I put them together.
[00:55:25] Daniel Castilla: This is what you wanna see. Right? Whoa, I get it so fast. Right. Sothat’s creating enormous possibilities. Um, examples that I had seen is, uh, well, I’ll say everybody’s trying to, uh, crunch their, their, their metrics and their KPIs and all their information faster. Um, I’ll say that the, the potential is there.
[00:55:45] Daniel Castilla: Eh, the struggle is the same. It’s like, well, how structured is your information? Right? So it’s like we go back to it’s like, well, you wanna, you wanna process all this data? Okay, do you actually have the data so we can actually process it? Otherwise you will process it, uh, faster, but it will tell you the same as if you have done it in, in a month and a half and get nowhere.
[00:56:06] Daniel Castilla: other things are, uh, I’ll say one that I like is, uh, the automation of repetitive tasks, right? So getting, getting people out of those very repetitive tasks. And I’ll say that’s with caution that I say, because obviously that can be understood as a, well getting rid of jobs. But I see it more as saying, well, if we actually.
[00:56:31] Daniel Castilla: Eh, automate or AI can take this repetitive task, then we actually need people for something more valuable than their, their repetition is their, their, their, their mind, right? Or actually the decisions that they can take. And I think that decision making because of that will actually be, eh, will go down into lower levels or, or deeper, not, not down deeper into lower levels of the organization.
[00:56:58] Daniel Castilla: Because people with less years of experience or education or whatever that you need to, to, to put all those things together, will have technology that will give them the elements to take correct decisions in their correct moments. Right. you don’t need to be like a manager up, uh, to take decisions with.
[00:57:17] Daniel Castilla: What, what is kind of looking as ai, is creating
[00:57:21] Josh Santo: I like how you put that. It’s not. Fundamentally changing anything, it’s really just helping go faster because the access to the information you need is, has been greatly improved. the example you gave with, the data analysis side of the people looking to crunch numbers, so how can we get this, computer to help us just run that really quickly and then ideally extract some sort of insight behind it? The way that I’ve always thought about it is the act of analyzing, while fun for some people is not really a value added activity, right?
[00:57:53] Josh Santo: You’re analyzing so that you can understand or come to a conclusion of what you should do, and then you take that action and really it’s that action that becomes the value add.
[00:58:03] Josh Santo: So the more you can shorten the time between the data point is captured and the action that you take, that’s that’s gonna be a huge gain in efficiency. That brings up to one of the points you made with regard to data analysis. Though you’re gonna run into problems if you don’t have a structured approach for data collection.
[00:58:20] Josh Santo: Data storage. If you have poor data going in, that’s gonna affect the results that you’re getting. And so there’s some things that have to happen upstream in order to get the best impact from ai. In that example, then you called out the idea of, kind of offloading repetitive tasks from people to, you know, these, these, I believe it’s referred to as a tic ai, you know, AI that can actually take some sort of action with some regard.
[00:58:48] Josh Santo: And to your point, it’s not necessarily to get rid of people, it’s to free up their time and their mental capacity to focus on those more. more things that require that human variable to come in, which goes back to what you talked about with the systems thinking, the skills being to problem solving and the continuous learning. Well, that’s great. Well, uh, one last question for you. It sounds like you’re a little excited about ai, at least it seems like you are. a little. I I could feel you getting a little passionate there. What’s happening in the world of manufacturing or in the world of quality that’s got you excited?
[00:59:23] Daniel Castilla: yeah, I’ll say that, uh, for me, and I, I touched some of those already. For me, the quality 4.0 that is a subset of industry 4.0 is really exciting because, it’s nothing, it’s nothing else than trying to solve issues or problems that had been there for, well, as long as, as, as, as we have been, uh, uh, producing, uh, in, or serially producing is probably a hundred plus years, right?
[00:59:50] Daniel Castilla: Uh, same issues, but now. We are getting technology that actually is, uh, is, is showing us the path, right? Or is, is getting us to places where we say, ah, actually yeah, yeah. Now we can actually make a, make that thing, we can create the solution, right? So for me, that’s an amazing thing that is happening and it’s happening so fast.
[01:00:08] Daniel Castilla: second one that I, I already mentioned digital twins, because for me, uh, that was always a topic of interest. I was like, okay, well how could, how could we actually,
[01:00:17] Daniel Castilla: create a virtual world, right? and use that for not just for the fun of it. And, uh, seeing that industries are moving in that direction is, uh, is, is, is very interesting.
[01:00:27] Daniel Castilla: the last one, I mean, I will touch back to AI and the vision systems is, is, is one of the topics that I, that I, I think, I didn’t mention that before when you asked me about ai, but uh, that’s also one that is becoming quite interesting. That, that now, we will be able to have a. Well, eyes everywhere, right?
[01:00:45] Daniel Castilla: and being able to process things, faster. So it’s, it, it also opens a, a world of possibilities.
[01:00:52] Josh Santo: yeah. And then I imagine taking your mechatronics perspective, it’s how do all these things work together to accomplish that
[01:00:59] Daniel Castilla: Yeah.
[01:01:00] Josh Santo: goal? Right. How does
[01:01:02] Josh Santo: the AI and vision systems, the digital twin capabilities, enable that idea of quality 4.0?
[01:01:07] Josh Santo: How does Quality 4.0 ultimately enable an organization to accomplish its own goals of delivering more value to the customer? Introducing new opportunities to, to, uh, you know, either not just be efficient, but we’ll open up new opportunities for revenue as well, make
[01:01:26] Josh Santo: more money, become more profitable, et cetera.
[01:01:29] Josh Santo: So tell us about a time in which the importance of your mechatronics background really clicked and I mean ultimately led to us having this conversation today.
[01:01:39] Daniel Castilla: Sure. So, yeah, when I, well, I’ll say it is really my story, my professional, career story because, uh, when I, left college, I, by coincidence because there was a program in a company, I ended in quality. And the reason why I ended in quality is because they gave me two options.
[01:01:58] Daniel Castilla: I say, you want to go to production, you want to go to quality? And I said, the last one, right? Like, I don’t know, like, I didn’t know any, any, any of those. and then I ended there, had some experience in the plant. Then actually I, I moved to, to Europe and I work in, uh, well first in a headquarters for electronics, also doing quality.
[01:02:19] Daniel Castilla: And then I moved to an another city, in Europe, uh, to a tech center while working, uh, at the tech center. And then I questioned myself as like, why am I doing this if I’m a mechatronics engineer? Right? And then I, I’m saying, well, I’m actually, I mean, I should come back to, to what I’m doing.
[01:02:35] Daniel Castilla: ’cause I am, I myself like designing robots and stuff like that. And I was always kind of around with this case, quality function. but it’s, it’s, when it click, it’s like, wait a minute. But the real me mechatronic thing, the constant through my experiences is that no matter if it was company A, company B, company C is the same thing.
[01:02:58] Daniel Castilla: The comp companies are only, only a different, uh, iteration or a different version of organizations that are trying to produce, uh, a solution, right? that’s what they do, right? So that’s when I say, wow. So if I see it as a, a company, as a system. Hmm. And I could actually, create something that has more value than just solving like, I don’t know, wind turbines, being more efficient or whatever.
[01:03:23] Daniel Castilla: Right. I mean, that would be great, and I did it for a while, but, but it’s like if I actually
[01:03:28] Daniel Castilla: dedicate myself into that, then I’m actually doing make electronics engineering in a non-traditional way. And at the same time, I’m doing quality in a non-traditional way. And 20 years later it’s proven that actually works.
[01:03:43] Daniel Castilla: Yeah.
[01:03:45] Josh Santo: So you had this kind of realization. It took a little bit of time, but you had this moment where it clicked where? You know, you’re, you’re in these different roles for these different companies that make different products, but you’re starting to see a lot of the same patterns repeat themselves and it kind of clicks for you. Oh, that’s because, you know, strip away some of the details. They’re all trying to do the same thing.
[01:04:04] Josh Santo: And when you stop looking at it as being so different and start looking at what are the consistencies behind that, that ultimately set you up to be able to have that adaptable perspective. not just from role to role in company to company, but like in between the different departments.
[01:04:19] Josh Santo: We’re all kind of trying to do the same thing
[01:04:21] Josh Santo: here. We just have different ways of doing it, different ways of describing it, different details that come about it. And that ultimately set you up to have this career in which you applied that, time and time again. Probably learned to develop that further and iterated.
[01:04:36] Josh Santo: ’cause like you said, continuous learning is part
[01:04:39] Josh Santo: of something that you believe in. That’s right.
[01:04:42] Daniel Castilla: it is. The only, the only thing that I want to change that I, I think I will not be able to do is to change the name of a quality function to something like operational excellence, because quality is misunderstood by, by that term. That term is what creates a lot of confusion.
[01:04:58] Josh Santo: the term quality
[01:04:59] Josh Santo: is what, or operational. So you think quality is operational excellence, or is, operational
[01:05:04] Daniel Castilla: it, yeah, it should be. I mean, the good quality or creating quality is creating operational excellence, right? This create is, is making a company being, be operations, being excellent, being, being better. Right? And then the output is quality. Right? But by calling it quality’s like, you have to be at the end taking care of the output without everything that happens inside the operations.
[01:05:27] Daniel Castilla: So that’s, that’s for me, very, very small change. But through my experience is when, when you have people that are not deep into quality or, or are because of their job, their nature, or hiring in the organization, and they think about quality, it’s like, oh, so they check things, right? They make sure of the, like the product at the end.
[01:05:48] Daniel Castilla: It’s like the, the ones that are checking, checking, checking. It’s like, it shouldn’t be like that. Mm-hmm.
[01:05:53] Josh Santo: Got it. So you heard it here first. If you are in quality, know that you are actually part of operational excellence and if you are, uh, a leader focused on operational excellence. Make sure your quality team is actively involved in the participation because those quality
[01:06:09] Josh Santo: professionals are operational excellence professionals. Daniel, I’ve certainly learned a lot from our time here today. I definitely have a better understanding of mechatronics engineering in comparison to where we started, and I appreciate you taking the time to share your perspective on how taking that holistic approach of how things work together, being able to go deep, but being able to bring it back to the bigger picture and being able to communicate with all the folks in between making it happen, uh, and the importance of that, not only in your career, but as a set of lessons that others can learn and improve their own experiences with.
[01:06:45] Josh Santo: So thanks for stopping by today.
[01:06:48] Daniel Castilla: Thank you Josh. Thank you for having me. I enjoy this time.
Forget the headaches. Digitize with EASE.
Join top manufacturers using EASE to drive quality, safety and productivity.