Process Audit: Driving the Change Towards a Quality Culture
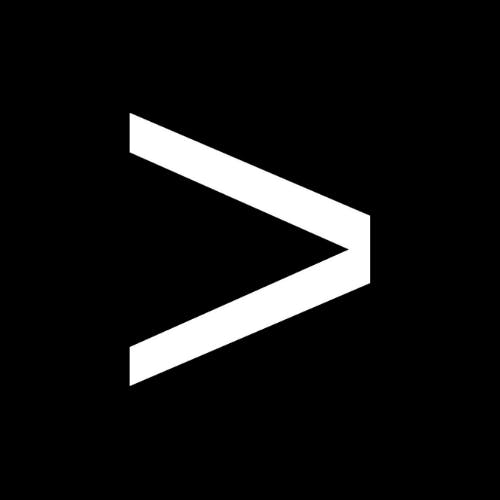
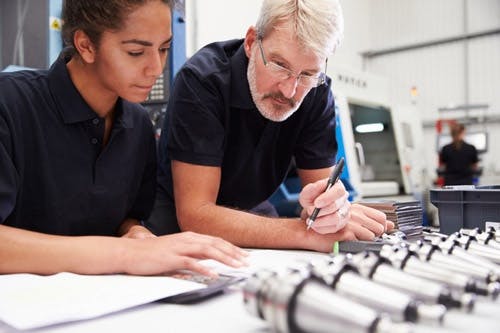
When implemented correctly, layered process audits (LPAs) go beyond satisfying customer requirements by transforming an organization’s culture into one that embraces continuous improvement. This powerful audit approach pays dividends by improving safety and quality, and delivers cost savings by greatly enhancing traditional assurance systems and making continuous improvement nearly routine.
The additional layers in LPAs ensure additional eyes are looking for issues, and the rotation of participants involved provides a powerful deterrent against those eyes “looking the other way” if even marginal concerns are identified. LPAs should include a wide spectrum of employees—from shop-floor operators to executives—conducting audits in order to verify that standardized procedures are followed consistently in the continuous pursuit of quality.
At Least 30-50% of the Workforce Should Be Involved in a Layered Process Audit Program
Certainly, the nature and size of the business influences the discussion, but in general, the higher the rate of participation, the better. Larger companies that have sizable marketing and administrative teams may choose to generally exclude these employees from the LPA process—although periodic assignment ensures everyone is seen as participating on some level.
Some believe that all employees from the manager level and up should be involved in the process, but overall, a good rule of thumb is at least 30-50% of the workforce should participate. In manufacturing companies, all staff has a vital stake in the quality of the company’s products and processes, whether directly, such as operators or supervisors, or indirectly, such as plant managers, human resources, finance, engineering, and even marketing personnel. All of these employees should therefore participate in LPAs at some point.
Participation Versus Commitment
In order for results to be effective, process audits require a team’s commitment to conduct the audit in a timely manner. Participation in the auditing process can vary from team to team. So long as teams are conducting the same audits in the same area, an audit can be completed by anyone in the organization. Often, layered process audit participants are employees outside of the organization’s operations or quality departments. Turning to people unfamiliar with the operations processes to conduct layered audits can be effective because they bring a fresh perspective to the audit.
Top management must be explicitly and visibly committed to the LPA process to ensure maximum participation, and they should be personally involved in audits at least quarterly—preferably monthly—to maintain accountability of the LPA system.