Q&A: Sheronda Jeffries Talks ISO 9001 and How to Be a Champion for Quality
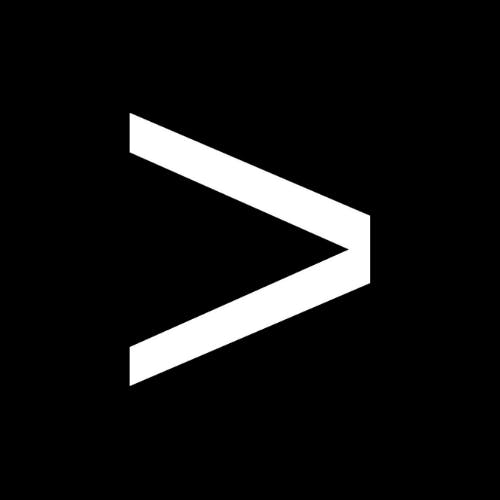
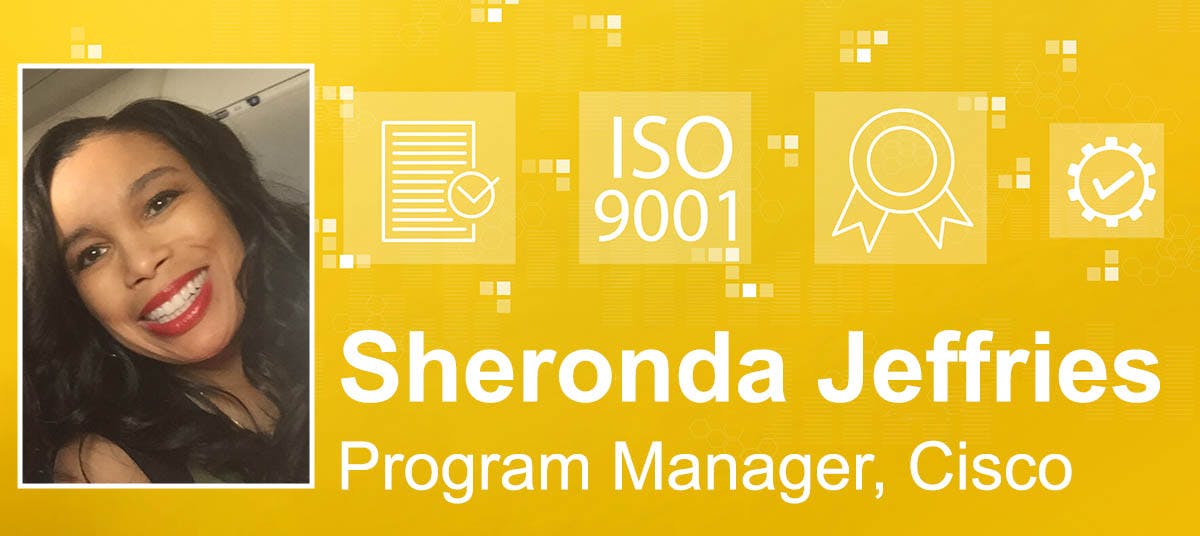
Today’s post is a Q&A featuring Sheronda Jeffries, program manager at Cisco Systems and one of our previous Champions for Quality award winners.
An ISO 9001 expert, Jeffries represents industry at various standard development organizations, serving as a director representing the ICT and telecom industry at the International Accreditation Forum (IAF). She also convenes the Sector Industry Forum made up of representatives from the automotive, aerospace, railway and information and communication technology (ICT) telecom industries.
At Cisco, Jeffries primarily trains auditors, bringing decades of experience as a quality auditor and expert in quality management system (QMS) implementation for manufacturing.
We talked to Sheronda about the role ISO 9001 should play in organizations, how to attract the next generation of quality professionals and creating a culture of quality.
Q: How are companies using ICT for audits and assessments within the context of COVID-19?
Jeffries: The use of ICT in audits and assessments is what has allowed conformity assessment to continue to provide confidence for our global supply chains during this COVID-19 pandemic. Essentially, electronic or remote audits have allowed organizations to keep their ISO certifications current, including ISO 9001, ISO 14001 and even ISO 13485 for medical device quality management. During the COVID-19 pandemic this has been of primary importance.
Q: Tell me about the next update coming to Annex SL, the high-level structure that governs ISO management system standards.
Jeffries: There are still updates being made to the Appendices, and it’s going to be awhile before these work their way through the process.
The Sector Industry Forum was created because we recognized that any update to Annex SL would ultimately impact ISO 9001 and therefore all of our standards. So we got together to present a unified front and voice for all of our interests.
This update is intended to be a limited revision, and we fully support the limited revision concept. We are very much in favor of less churn and less change.
Q: When we think about certifications like ISO 9001, how should they be influencing operations as a whole, and not just quality?
Jeffries: When I worked as a third-party auditor, I once audited a small organization based in Georgia in the carpet industry. I was assessing the organization to ISO 9001, and leadership said to me, “When you walk in, we don’t want you to use the term ‘ISO 9001.’” “Why?” I asked, and they said, “We don’t want anyone thinking that we’re doing something because someone else is telling us to. We’re doing it because this is what we intend to do.”
That organization had one of the highest commitments to quality that I’ve seen. But it wasn’t about the certificate. They didn’t even promote that they had an ISO 9001 certification internally to employees. Internally they shared that they met their own quality requirements with no reference to ISO 9001.
Q: With ISO 9001 so important to manufacturers today, do you think companies should be looking closer at supply chain partners and evaluating their certifications?
Jeffries: Yes, I definitely do. I hosted a webinar recently that talks about how to look at certificates. So many organizations are focused on getting the certificate and then asking their supply chain to get certified, but they don’t really know how to verify the validity of it.
What do you think are the biggest trends in digital transformation today?
Jeffries: One concern is that as we become more reliant on technology, we’ve got to become more knowledgeable about security. And it’s not just our organization—it’s also our supply chain. Who are we partnering with? Do they take the same precautions that we do?
Q: What do you think industry needs to do to attract the next generation of leaders?
Jeffries: I know a couple of organizations banded together and started an apprenticeship program for auditors. It’s still in its initial stages, but I think it’s a great concept.
I think the key is we’ve got to be open to try new things. We’ve got to provide opportunities for ongoing education, training and internships. We’ve also got to recognize that what we used to do may not always work. Even in my training courses, I’m always trying new tools and figuring out what’s out there.
Q: What do you think the big opportunities are going to be for quality people as we look toward the future?
Jeffries: One thing is that those opportunities are going to look different, so it’s important to have a commitment to lifelong learning and thinking outside the box.
For example, I don’t know long much longer you’re going to be able to say, “I’m just a consultant in ISO 9001.” I think you’re going to have to talk about the fact that you’re knowledgeable on how a lot of different things play together.
I like to tell folks, yes, I know ISO 9001. But I also know TL 9000, I’m reading about ISO 45001 and I’ve got a copy of the railway standard over here.
The metal worker, for example, has an opportunity to impact both the safety and the quality of that job. There are also lots of opportunities to learn and do more in terms of efficiency and other improvements. It’s all about working, learning and continuing to grow.
Q: What’s most important to being a champion for quality and an advocate for positive change in your organization?
Jeffries: You’ve got to be willing to do what’s right. If you see something that’s not right, you’ve got to be able to say, “Hey, why are we doing this?” You’ve got to be willing to ask that question.
When you try to be different, people may or may not be in support of that. You’re going to have naysayers, so you’ve got to develop thick skin. Some people will question your motives. But as long as you try to do the right thing and are committed to change, ultimately you want to believe it’s going to work out. Even if it means falling down seven times and getting up eight.