Real-World Mistakes Companies Can Avoid with Mobile Audit Software
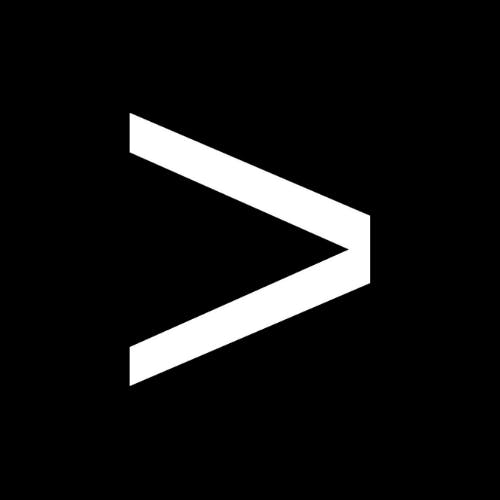
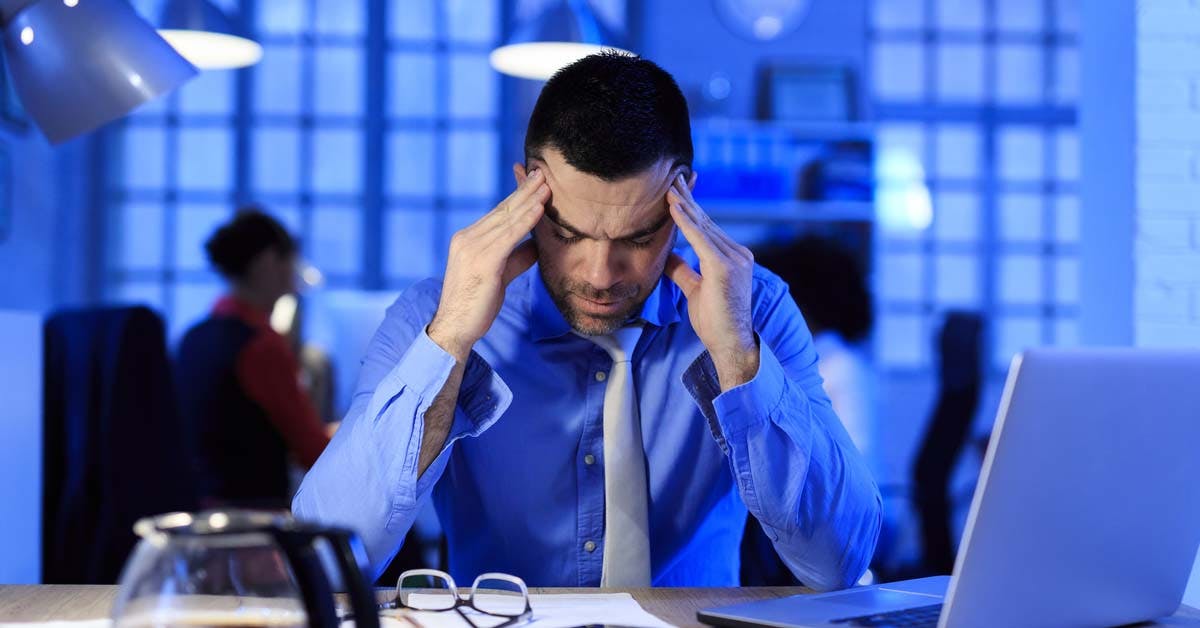
An operator uses a torque wrench incorrectly, leading to a loose nut on a Subaru Impreza transmission selector lever cable. Tesla Model Ys delivered with back seats not attached to the vehicle. Over 1,700 Ford Broncos recalled over both front and rear suspension issues. 15 million COVID-19 vaccines are discarded over an ingredient mix-up.
What do these real-world headlines have in common?
They all happened because of process errors—and they all could have been prevented by verifying process adherence on the plant floor.
Here we examine newsworthy quality escapes in the past year, and how manufacturers can avoid similar mistakes with mobile audit software.
Learn about a powerful strategy for cutting production defects and scrap rates with our free Ultimate Guide to Layered Process Audits eBook
Subaru Recalls Hundreds of Cars Over Torquing Issue
According to Automotive News, a single operator not using a torque wrench correctly led to the recall of over 400 vehicles from Subaru’s Indiana plant. The error allowed for a loose nut on the transmission selector lever cable.
Subaru reports that the problem was found during assembly line sampling. It was the first week the operator was performing the task, and the company is quick to point out that they aren’t pointing fingers or assigning blame.
This error underscores the need to verify compliance with standards on the shop floor. It’s especially important in light of pandemic-related production changes, where operators may need to perform new roles due to absenteeism or reorganized production lines.
Customers Refusing Deliveries of Tesla Model Y Over Production Defects
Reuters reports that over 90% of Tesla Model S and Model X vehicles leave the manufacturing line defective, and defects are apparently also an issue with the Model Y.
Ars Technica recently revealed reports on forums like Reddit and YouTube where numerous customers have rejected Tesla Model Y deliveries over manufacturing defects. The problems reported include:
- Alignment issues
- Improperly closing rear hatches
- Charge port doors not closing
- Doors and trim that are misaligned
- Paint issues
- Underfloor panels or rear seats not completely attached
- Damaged or dirty interiors
- Broken seatbelts
And these aren’t just one-off problems. Editor-in-chief of the pro-Tesla Electrek suggests that the quality issues of the Model 3 pale in comparison to those with the Model Y, noting that they are “overwhelming Tesla’s quality control.” In some cases, the company has even delayed deliveries due to defects.
Elon Musk himself has noted the Model Ys need too many rectifications or fixes after leaving the manufacturing line. These problems aren’t hidden design flaws, but production defects that point to potential issues that process verification can prevent.
Suspension Issues Lead to Ford Bronco Sport Recalls
Ford recalled 1,666 of its 2021 Ford Bronco Sport SUVs due to workers incorrectly securing rear suspension modules to the vehicle subframe. This problem could increase stability problems and injury risks, although no crashes have been reported.
The Bronco Sport also had a second recall of 106 vehicles due to front suspension issues, in this case having the wrong front lower control arms. Ford traced the problem to a single supplier assembling front suspension modules with the wrong arms, an issue that process audits by the supplier may have helped prevent.
Ingredient Mix-Up Wastes 15M Johnson & Johnson Vaccines
One huge quality escape that garnered media attention recently was the loss of more than 15 million Johnson & Johnson vaccines. Employees at Emergent Biosolutions, a contract manufacturer for J&J, apparently mixed ingredients from two different coronavirus vaccines.
The mistake led to 15 million doses wasted and a delay in J&J’s delivery timeline. The facility in question was also shut down temporarily pending the results of an FDA inspection. The company has said that the vaccines had not advanced to the finishing stages of production, and that it’s an example of strong quality control measures in place. However, it’s clear that had process audits been in place, the mistake may have been caught before millions of doses were ruined.
How Mobile Audit Software Can Help Avoid These Problems
Mobile audit software can help manufacturers avoid mistakes like the ones discussed here, allowing them to identify process errors before they lead to defects. Mobile audit software like EASE, combined with process audits, allows manufacturers to:
- Quickly verify key inputs like materials, equipment use and processes
- Add extra layers of verification around high-risk and critical-to-quality processes
- Design questions based on known quality issues to prevent recurrence
For example, companies can create process audit questions based on the work standard dealing with how an operator performs a torque wrenching, the materials used at a station, or other assembly technique.
Layered process audits (LPAs) amplify this strategy, engaging people from different levels of the organization to get more eyes on key processes. LPAs only take about 10 minutes to complete on a tablet, providing instant visibility into process errors that can cause defects.
While LPAs have helped manufacturers significantly reduce complaints, scrap and rework, these results aren’t typical with paper checklists and manual data entry. Digitization is key, eliminating lag time between audits and reporting, randomizing questions for better coverage of standards and allowing plants to add new checks immediately when problems are detected.
Just one of the problems addressed here is enough to make an impression on buyers, cause massive financial headaches for manufacturers, and in the case of Emergent Biosolutions, impact the rollout of a life-saving vaccine. Mobile audit software combined with process audits, on the other hand, give companies a head start in preventing production defects at the source.