Rising to the Challenge: How Automotive Suppliers Are Addressing IATF 16949
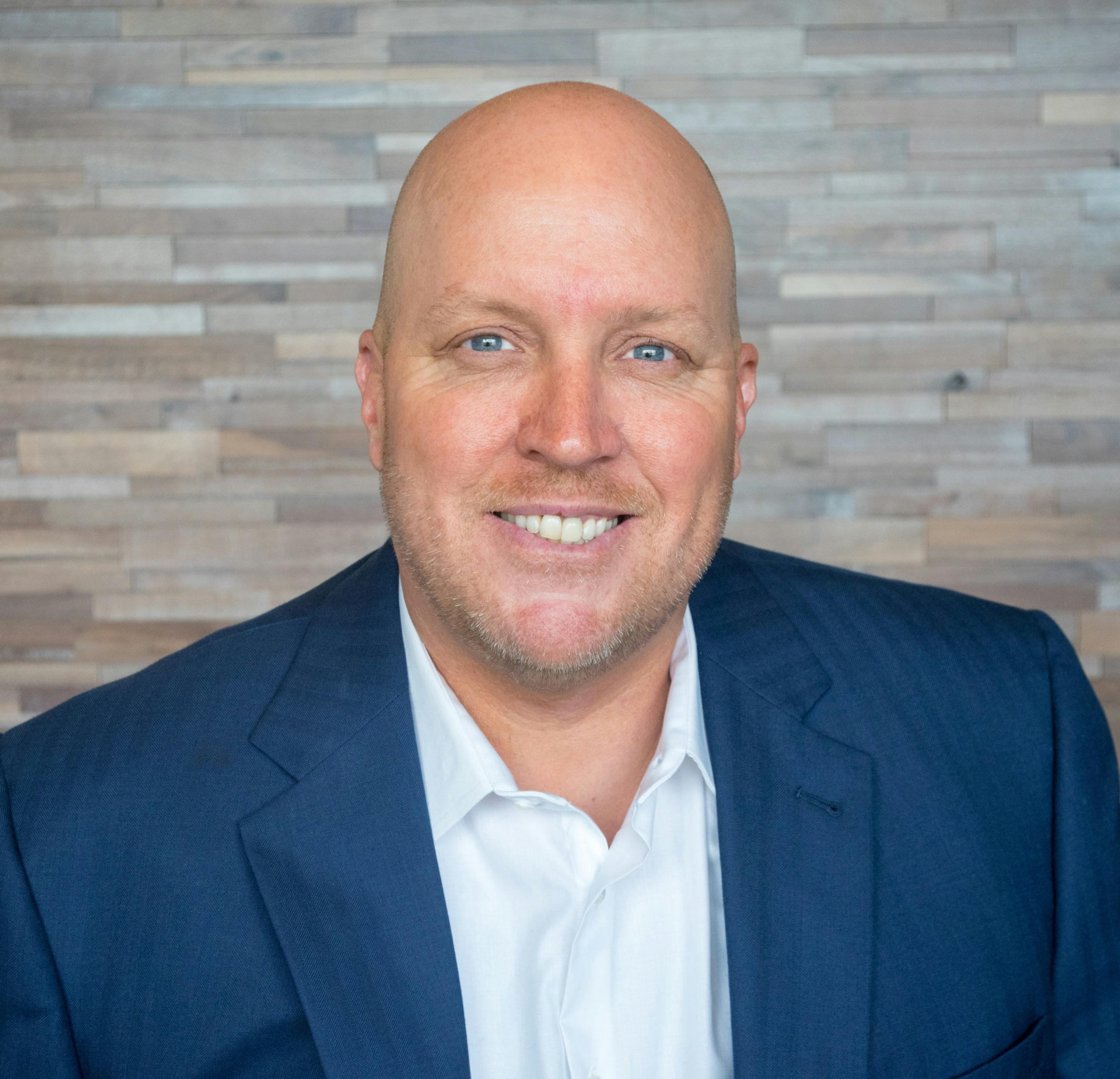
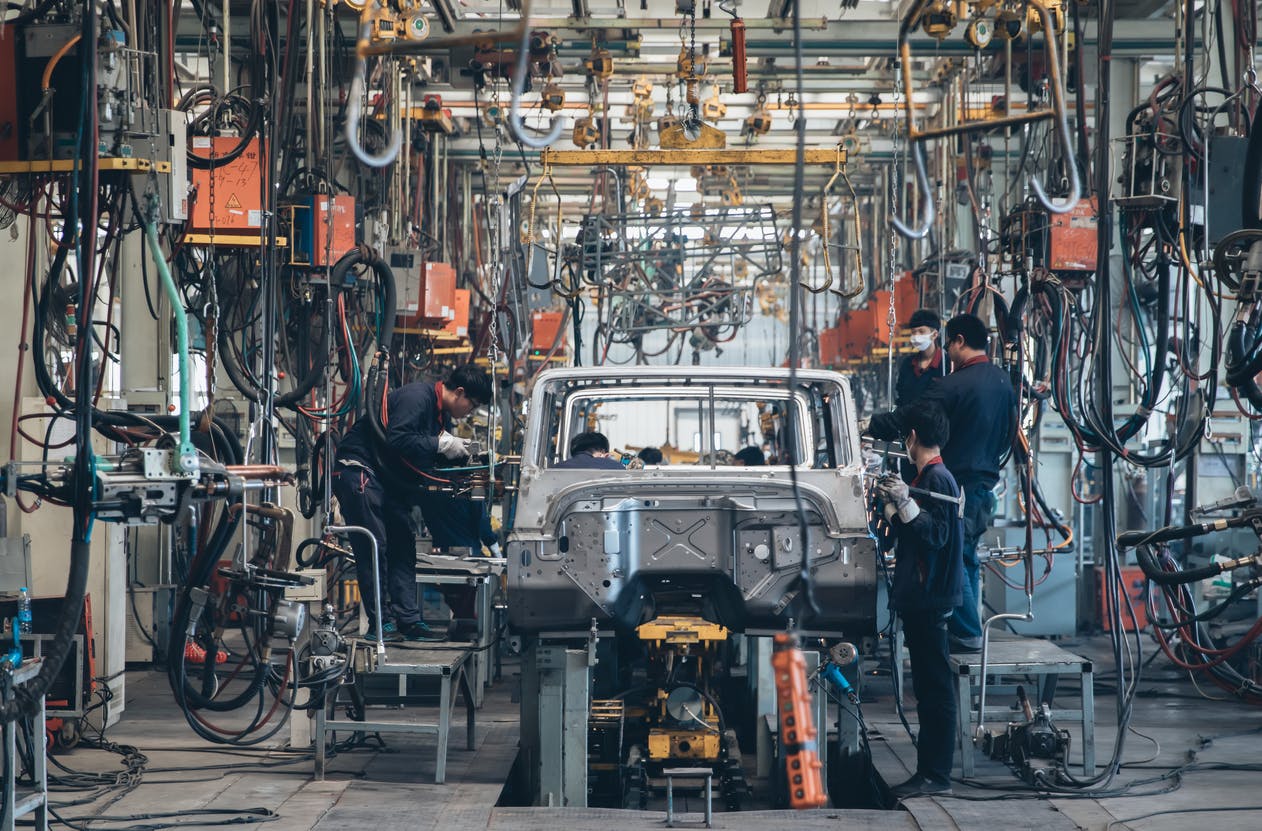
In accordance with the new standard, IATF 16949, Fiat Chrysler Automobiles (FCA) recently published a document updating its customer-specific requirements. This publication, along with similar documents from General Motors and other large automotive customers, lays out tighter requirements that are prompting automotive suppliers around the world to evaluate their existing processes and systems to ensure compliance.
Notably, the document requires suppliers to conduct an internal quality audit at least once per year, and also mandates they conduct Layered Process Audits (LPA) on all elements of manufacturing and assembly lines that produce parts for FCA. In this article, we’ll highlight some of FCA’s specific requirements, evaluate their significance and in some cases, discuss potential solutions that can help companies with compliance.
Requirement: Audit process shall involve multiple levels of site management, from line supervisor up to the highest level of senior management normally present at the organization site.
What it means: The need for active, ongoing management involvement is a key theme throughout many of FCA’s new requirements. For many companies who already engage multiple levels and areas of management in the audit process, this is a formalization of good management practices that have been promoted for years. The distinction here is the need to engage and rotate cross-functional layers of management to reduce the risks and challenges associated with operational areas that have previously been overlooked throughout the audit process. This periodic changing of the audit area responsibility for the more senior managers addresses a number of common gaps, including increased pressure by supervisors and managers to pass items that an independent reviewer might flag for additional attention. It also ensures that managers remain aware of changing processes and ideally brings new improvement ideas to the table.
—-
Requirement: A member of site senior management shall conduct process control audits at least once per week – and all members of site senior management shall conduct process control audits on a regular basis. Additionally, the delegation of this activity will not be accepted with the exception of extenuating circumstances.
What it means: Along with the above requirement, these obligations further specify the need for senior managers to stay actively involved in the audit process on an ongoing basis. Management will be expected to actively work together with their teams and take ownership of their processes at any given point in time. This increases the likelihood that their teams will catch issues as they occur, rather than reacting to them and risking a costly escape.
—-
Requirement: Error-Proofing Validation (EPV) audits shall be conducted at least once per shift, preferably at the start of shift. Compliance charts shall be completed once per quarter and maintained for the life of the program. The following metrics shall be included:
- Audit completion by all auditing layers
- By-item percentage conformance by area
What it means: In short, these are additional, wide-ranging checks that FCA requires across every shift. This brings additional scheduling, reporting, and other administrative burdens, which in many cases will necessitate the implementation of software solutions that can ensure complete coverage as well as track, share and manage metrics in a timely and accurate manner.
—
Requirement: The organization shall show evidence of immediate corrective action, containment (as required), and root cause analysis (as required).
What it means: Corrective action/ preventive action (CAPA) activities are designed to eliminate non-conformities and bring about improvements to an organization’s processes. FCA’s new requirement seeks to ensure that CAPA procedures are in place, actively monitored, and that they’re fully and permanently closed out in a timely manner.
The new requirement, which also calls for suppliers to perform a root cause analysis (RCA), also reinforces existing good practices such as the Eight Disciplines (8Ds) approach that is used to identify, correct and eliminate more severe problems. A key input here is the Failure Mode Effects Assessment (FMEA) process, which is often a good starting point to assess a process during the design phase to identify appropriate preventative and corrective actions for significant failure risks. For many automotive manufacturers, this requirement will again require the use of software that can track and catch mistakes in real-time, note their severity, track their mitigation, report on overdue activities, and enable immediate updates to audit questionnaires to close the loop with permanent fixes.
Summing It Up
We continue to see elevation of customer requirements in the automotive industry. As they accelerate, there comes an increased opportunity for errors as management struggles to keep up with quality and compliance challenges, including changes in IATF 16949. To learn more about how the Beacon assessment platform has helped organizations keep pace with these rising challenges, feel free to reach out to one of our support experts at any time.